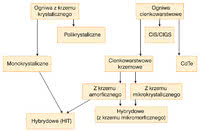
Rys. 1. Ogniwa PV są produkowane w różnych odmianach - dostępne są np. ogniwa cienkowarstwowe z tellurku kadmu (CdTe), selenku indowo-miedziowego (CIS), produkowane z połączenia miedzi, indu, galu i selenu (CIGS) oraz hybrydowe HIT (heterojunction with intristic thin layer)
Na rynku systemów fotowoltaicznych dominują obecnie dwa typy ogniw słonecznych: krystaliczne, wykonane na podłożu w postaci krzemowej płytki, oraz cienkowarstwowe, które budowane są na podłożu szklanym, metalowym lub z tworzyw sztucznych.
W obrębie każdej z grup w zależności od użytych materiałów wprowadza się dalszą klasyfikację (rys. 1), wyróżniając np. ogniwa z krzemu polikrystalicznego lub monokrystalicznego oraz w przypadku krzemowych cienkowarstwowych: ogniwa z krzemu amorficznego lub mikrokrystalicznego.
Każdy z rodzajów ma zalety, ale też wady. Przykładowo ogniwa krystaliczne charakteryzuje wyższa sprawność konwersji energii słonecznej w energię elektryczną (około 20%) w porównaniu do sprawności ogniw cienkowarstwowych (około 10%). Produkcja w technologii cienkowarstwowej jest z kolei tańsza i prostsza, podczas gdy wytwarzanie ogniw krystalicznych jest skomplikowane i wieloetapowe, a przez to droższe.
JAK POWSTAJĄ OGNIWA KRYSTALICZNE
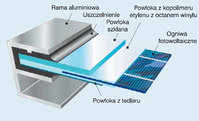
Rys. 2. Moduł z ogniw krystalicznych
Proces produkcji rozpoczyna się od stopienia w tyglu krzemu, do którego dodawany jest bor niezbędny do uzyskania półprzewodnika typu p. Z surowca tego formuje się pręty, cięte następnie na płytki o grubości kilkuset mikrometrów i średnicy około kilkunastu cm. Cienkie krążki narażone są na różne uszkodzenia (zarysowania, pęknięcia, zniekształcenia, odpryski), czasem noszą też ślady po cięciu lub są trwale zabrudzone.
Dlatego kolejnym etapem jest inspekcja wizyjna. Płytki, które przejdą ją pomyślnie, poddawane są obróbce chemicznej w ramach czyszczenia, teksturyzacji oraz domieszkowania. Po oczyszczeniu powierzchni krążków przeprowadza się teksturyzację, która np. w przypadku płytek z krzemu monokrystalicznego polega na zanurzeniu w gorącym roztworze wodorotlenku sodu i izopropanolu. W wyniku reakcji roztworu z krzemem na powierzchni formują się wypukłości, które zmniejszają refleksyjność płytki i tym samym zwiększają absorpcję promieniowania słonecznego.
Następnie krążki są domieszkowane fosforem w procesie dyfuzji. W ten sposób powstają złącza p-n. Realizuje się to w piecach nagrzewanych do bardzo wysokiej temperatury, a efektywność domieszkowania w największym stopniu zależy od precyzyjnej kontroli tego parametru. Fosfor osadza się też na brzegach płytek i aby usunąć te niepożądane warstwy tworzące pasożytnicze złącza na krawędziach, krążki układa się w stosy i umieszcza w komorze chemicznego trawienia. Skuteczność tej operacji sprawdzana jest w czasie kolejnej kontroli jakości.
Następnie płytki pokrywa się antyrefleksyjną warstwą z azotku krzemu lub tlenku tytanu. Powłokę nanosi się w procesie PECVD, czyli chemicznego osadzania z fazy lotnej wspomaganego plazmą. Ostatnim z etapów jest utworzenie kontaktów elektrycznych - zazwyczaj w formie pasków z dobrego przewodnika. Najczęściej wykorzystuje się srebro, głównie ze względu na plastyczność tego materiału.
Metodą sitodruku nanosi się kontakty: przednie z pasty srebrowej oraz tylne z pasty aluminiowej. Pasty są następnie suszone i wypalane w piecu. Pojedyncze ogniwa przygotowane w ten sposób łączy się ze sobą, tworząc fotowoltaiczne moduły, które dodatkowo zabezpiecza się przed wpływem warunków atmosferycznych, tak by przez lata mogły spełniać swoją funkcję.
JAK TWORZYĆ MODUŁY FOTOWOLTAICZNE?
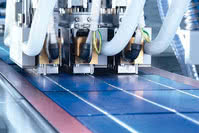
Fot. 1. Linia Rapid One do lutowania paneli PV w moduły oferowana przez firmę Somont
Drugim etapem produkcji jest lutowanie ogniw w łańcuchy. Jakość tego połączenia, na którą wpływa m.in. wybór stopu lutowniczego oraz temperatura lutowania, decyduje o mocy wyjściowej modułu. Złączone ogniwa są następnie w warunkach próżni pokrywane powłokami z kopolimeru etylenu z octanem winylu, a następnie zamyka się je w szklanych osłonach z obu stron. Górną osłonę pokrywa się powłoką przeciwodblaskową, natomiast tylną wykonuje się z materiału będącego połączeniem szkła z plastikiem - np. tedlarem (polifluorkiem winylu), który chroni moduł PV m.in. przed wilgocią.
Moduły krystaliczne są dalej zabezpieczane taśmą izolującą oraz umieszczane w aluminiowej, uszczelnianej ramie (rys. 2). Ostatnim etapem produkcji jest zamontowanie na module skrzynki przyłączowej. Oprócz tego, że umożliwia ona podłączenie do sieci elektrycznej, to zawiera też elementy zabezpieczające moduł, np. diody chroniące przed prądem wstecznym, który mógłby płynąć w nocy. Produkcja modułów krzemowych ogniw cienkowarstwowych rozpoczyna się od naniesienia kontaktu elektrycznego, czyli warstwy przezroczystego przewodzącego materiału, np. tlenku cynku, na szklane, metalowe lub plastikowe podłoże.
Realizuje się to w procesie napylania katodowego. Kolejnym etapem jest PECVD, w którym na podłożu tym osadza się warstwę krzemu o strukturze mikrokrystalicznej lub amorficznej. Poszczególne ogniwa są w strukturze modułu wyodrębniane laserowo. Następnie napyla się kolejną warstwę tlenku. Gotowe moduły laminuje się tworzywem sztucznym i umieszcza w szklanej osłonie. Na koniec usuwa się nierówności na krawędziach oraz umieszcza w ramie, o ile jest to wymagane. Dostępne są też cienkowarstwowe moduły bez ram.
ROBOTY W PRODUKCJI OGNIW I MODUŁÓW
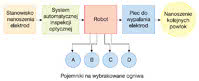
Rys. 3. System do badania jakości kontaktów elektrycznych ogniw przed ich wypaleniem w piecu zaprojektowany przez Adept Technology
Większość zadań na poszczególnych etapach produkcji ogniw i modułów PV można zautomatyzować, co nie uszło uwadze dostawców robotów przemysłowych. Odpowiadając na to zapotrzebowanie, systematycznie rozszerzają oni swoją ofertę o produkty dla branży solarnej. Na rynku dostępne są m.in. linie produkcyjne oraz zautomatyzowane stanowiska robocze czyszczenia płytek krzemowych, ich transportu i załadunku do pieców dyfuzyjnych lub maszyn nakładających powłoki antyodblaskowe, a także urządzenia do nanoszenia kontaktów elektrycznych, usuwania nadmiarowego materiału z krawędzi oraz obramowywania gotowych modułów.
Dostępne są też roboty przemysłowe z osprzętem specjalizowanym do sortowania płytek krzemowych, transportu kaset z ogniwami ułożonymi w stosy oraz montażu modułów i skrzynek przyłączowych i wreszcie do przenoszenia dużych lub nieporęcznych dla personelu modułów. Co więcej - potencjał robotów przemysłowych dzięki wyposażaniu ich w różne czujniki - np. siły oraz możliwość współpracy z systemami wizyjnymi - nieustannie rośnie.
Wpływa to na poprawę jakości produktów, co w przypadku ogniw słonecznych przekłada się na wyższą sprawność. Maleje też liczba wybrakowanych egzemplarzy, co oznacza większy uzysk produkcyjny. Oszacowano nawet, że inwestycja w robotyzację produkcji ogniw i modułów PV zwraca się średnio po około 1,5 roku od uruchomienia.
ROZWIĄZANIA WEDŁUG FIRMY KUKA
Rozwiązania dla branży PV ma w ofercie wielu dostawców automatyki, w tym np. ABB, Fanuc Robotics, Adept Technology i Kuka. Ta ostatnia propozycję dla producentów fotowoltaiki podzieliła na trzy grupy rozwiązań: stanowiska do obróbki bloków krzemu i produkcji płytek krzemowych, roboty przemysłowe z chwytakami do manipulowania ogniwami oraz zautomatyzowane stanowiska do montażu modułów PV. W pierwszej dostępne są m.in. AWSM 3800 - maszyna do cięcia krzemowych bloków na płytki oraz ASQM 2800.3 - urządzenie do produkcji kwadratowych bloków z okrągłych krzemowych prętów.
Przykładem zautomatyzowanego stanowiska jest natomiast stacja do rozładowywania szklanych płyt oraz nanoszenia powłok z kopolimeru etylenu z octanem winylu (Robo Load), którą dodatkowo można uzupełnić o urządzenia do mycia szkła. Kuka oferuje też stanowisko do trymowania gotowych modułów (Robo Trim), na którym robot podnosi moduły i przesuwa je bokiem po okrawarce usuwającej skrawki powłoki wystające poza krawędzie panelu.
Dostępne są też stanowiska do uszczelniania modułów specjalną taśmą (Robo Tape), ich obramowywania (Robo Frame) oraz linia do pakowania (Robo Stack), w której roboty zdejmują z taśmy moduły PV, wcześniej posortowane według sprawności. Parametr ten określa się na podstawie charakterystyk prądowo-napięciowych poszczególnych modułów wyznaczanych na stanowisku, na którym odtwarza się rzeczywiste warunki, wykorzystując sztuczne oświetlenie.
ŁĄCZENIE PANELI PV - PRZYKŁADY
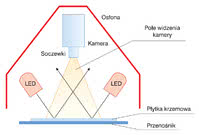
Rys. 4. System AOI składa się z kamery, oświetlacza LED oraz osłony, która ogranicza dopływ światła z zewnątrz; diody montowane są tak, by światło odbite od płytki było absorbowane w osłonie i nie trafiało w oko kamery
Jednym z częściej automatyzowanych zadań jest też proces lutowania ogniw w moduły. Przykładowo Kuka oferuje w tym zakresie linię technologiczną do lutowania z wykorzystaniem promieniowania podczerwonego ACS 600 (Advanced Cell Stringer), w skład której wchodzi m.in. robot SCARA KR4 oraz system wizyjny. Podobne rozwiązanie - linię Rapid One - dostarcza też firma Somont (fot. 1). Jej częścią jest sterowany wizyjnie robot, który układa ogniwa na przenośniku.
Następnie na zmianę są one ogrzewane i schładzane zgodnie z określonym profilem temperaturowym. W ten sposób zmniejsza się naprężenia termiczne powstające w czasie zgrzewania, które pogarszają jakość spoiwa. Równocześnie na innym stanowisku taśma lutownicza jest odwijana, podgrzewana oraz ucinana. Następnie robot układa ją na ogniwach, które są dalej transportowane do maszyny lutowniczej. Po złączeniu łańcuchy przechodzą kontrolę z wykorzystaniem systemu wizyjnego, gdzie bada się m.in. jakość wykonanych połączeń (np. pod kątem ewentualnych pęknięć spoiwa).
W ramach linii Rapid One realizowane są też kolejne etapy obróbki modułów, jak laminowanie i łączenie ze szklaną powłoką. Inne rozwiązanie u jednego ze swoich klientów, w firmie Scheuten Solar, wdrożył Fanuc Robotics. Stanowisko składało się z sześciu robotów sterowanych na podstawie informacji z dwóch kamer i systemu wizyjnego iRVision. Pięć maszyn zamontowano nad stanowiskiem, a jeden na podłodze.
Pierwszy z robotów wstępnie scalał panele specjalnymi łącznikami, a następnie drugim chwytakiem odwijał taśmę lutowniczą i układał ją w miejscu złączenia. Taśmę odcinał drugi robot, a wtedy trzeci lutował ją do paneli. Pozostałe dwa roboty wykonywały analogiczne czynności z drugiej strony modułów.
AUTOMATYCZNA INSPEKCJA WIZYJNA
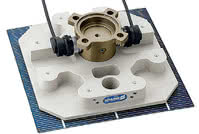
Fot. 2. Chwytak Bernoulliego firmy Schunk
Przedstawione przykłady pokazują, że jednym z kluczowych elementów zrobotyzowanych stanowisk są systemy automatycznej inspekcji optycznej (Automated Optical Inspection - AOI). Kontrolują one stan powierzchni oraz geometrię krzemowych płytek, a potem ogniw na różnych etapach procesu produkcyjnego. AOI to najczęściej źródło światła, np. oświetlacz LED, i kamera obrazowa lub linijkowa. Dobór konkretnych układów zależy od aplikacji.
Przykładowo do celu inspekcji stanu powłok antyodblaskowych zaleca się korzystanie z kamery kolorowej. W białym świetle ogniwa pokryte antyrefleksyjną powłoką są niebieskie, ponieważ promieniowanie o dłuższej długości fali dzięki tej warstwie w większym stopniu przenika do ogniwa. Odcień oraz nasycenie odbitego światła są z kolei zależne od grubości powłoki. Wykorzystując niebieski kanał kamery, można wykryć jej defekty.
Innym przykładem jest detekcja tzw. mikropęknięć płytek krzemowych, które niezauważone mogą na dalszych etapach produkcji prowadzić do pęknięcia płytki. Skutkuje to nie tylko stratami materiału, ale często zatrzymaniem całej linii produkcyjnej na czas usunięcia okruchów. Jednocześnie wykrycie mikropęknięć, o rozmiarze często poniżej kilku mikrometrów, jest bardzo trudne. Aby zwiększyć skuteczność AOI, najczęściej wykorzystuje się podświetlanie podczerwienią.
Ponieważ krążki są bardzo cienkie, a dodatkowo krzem w podczerwieni jest przezroczysty, płytki podświetla się diodą LED o długości fali emitowanego światła od 850 do 950nm. Wówczas pęknięcia są widoczne jako ciemne linie na jasnym tle. Pod kątem mikropęknięć oraz innych defektów testuje się również gotowe moduły słoneczne.
Zamiast AOI czasem wdraża się jednak inne rozwiązanie, zasilając moduły prądem o gęstości kilkudziesięciu mA/cm2. Wówczas ogniwa emitują światło, a uszkodzenia ich struktury sprawiają, że oświetlenie to jest nierównomierne. Można w ten sposób połączyć kontrolę jakości z badaniem sprawności modułu.
WIZYJNE STEROWANIE ROBOTEM
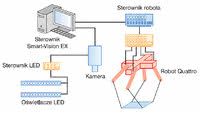
Rys. 5. Częścią systemu firmy Adept Technology jest sterowany wizyjnie robot z serii Quattro, który zainstalowany jest między stanowiskiem nanoszenia kontaktów i piecem; zdejmuje on z taśmy uszkodzone ogniwa
Na rysunku 3 przedstawiono schemat blokowy zaprojektowanego przez Adept Technology systemu badania jakości kontaktów elektrycznych ogniw przed ich wypaleniem w piecu. Dzięki niemu w razie wykrycia uszkodzeń lub zniekształceń elektrod pastę można zmyć, a kontakty nanieść ponownie.
W przypadku utrwalenia w piecu wybrakowane płytki trzeba niestety wyłączyć z dalszej produkcji. Częścią systemu jest układ AOI, który zrealizowano, montując nad przenośnikiem osłonę (rys. 4), pod którą zainstalowano kamerę firmy Basler piA2400-12gm z interfejsem Gigabit Ethernet oraz oświetlacze LED po obu stronach taśmy. Kamera komunikuje się ze sterownikiem Smart-Vision EX firmy Adept Technology wykorzystującym oprogramowanie AdeptSight. Zadaniem AOI jest inspekcja nadruku elektrod, kontrola geometrii płytki oraz stanu jej powierzchni.
W pierwszym etapie system sprawdza, czy elektrody zostały równo naniesione w odpowiednich miejscach. Następnie analizowany jest kształt i rozmiary płytki. Bada się też jej ścięte rogi, które obcina się, by uniknąć obłamywania ostrych końców ogniwa. Ostatni etap, w którym wykorzystuje się algorytm rozpoznawania wzorca, polega na wyszukaniu w obrazie płytki zarysowań, kropli pasy, itp. Częścią omawianego systemu jest również sterowany wizyjnie robot Adept z serii Quattro (rys. 5).
|
Jest on instalowany nad przenośnikiem łączącym stanowisko nanoszenia kontaktów i piec. Jego zadaniem jest zdejmowanie z taśmy uszkodzonych ogniw. Kierowanie robotem polega na przesłaniu do sterownika ruchu informacji o współrzędnych środka płytki, wyznaczanych na podstawie współrzędnych jej końców oraz danych o orientacji płytki na taśmie. Określa się ją na podstawie kątów, jakie boki płytki tworzą z krawędziami obrazu. Dane te są w sterowniku wykorzystywane do transformacji współrzędnych ogniwa między układem odniesienia przenośnika i robota.
TRANSPORT OGNIW
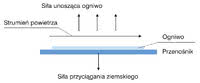
Rys. 6. Chwytaki Bernoulliego wykorzystują zjawisko, w którym przepływ strumienia powietrza o dużej prędkości nad obiektem powoduje powstanie siły, która go unosi
Kolejnym wyzwaniem w produkcji komponentów PV jest ich transport. Problem pojawia się już na etapie cięcia bloków krzemowych, gdzie otrzymuje się stosy cienkich płytek, które najczęściej są ze sobą posklejane płynami obróbkowymi (cieczą chłodząco-smarującą). W czasie rozdzielania łatwo jest je uszkodzić lub połamać. Aby tego uniknąć, wykorzystuje się np. bezdotykową metodę separacji płytek strumieniami powietrza. Rozwiązanie tego typu jakiś czas temu na zamówienie BP Solar zaprojektowali inżynierowie z NREL (National Renewable Energy Lab).
Opracowali oni system, który nie tylko rozdzielał, ale też transportował płytki krzemowe wzdłuż liniowego toru w dwóch kierunkach. W instalacji tej wykorzystano regulację ciśnienia dwóch przeciwnie skierowanych strumieni sprężonego powietrza zmienianego w taki sposób, aby płytki przemieszczały się w kierunku poziomym. Regulacją ciśnienia w dyszach sterował komputer za pośrednictwem dwóch serwozaworów.
Na podobnej zasadzie działają tzw. chwytaki Bernoullego. Ich nazwa pochodzi od fizyka, który opisał prawo, zgodnie z którym nad obiektem, nad którym przepływa strumień powietrza o dużej prędkości, występuje lokalny spadek ciśnienia. Różnica ciśnień nad i pod obiektem powoduje powstanie siły skierowanej od strony o wyższym do strony o niższym ciśnieniu. Jeżeli przewyższy ona siłę przyciągania działającą na obiekt, to przesunie się on w kierunku strony o niższym ciśnieniu (rys. 6).
Chwytaki tego typu oferuje wielu dostawców - np. Schunk (fot. 2) oraz Bosch Rexroth, który w asortymencie ma chwytaki serii NTC (Non-contact Transport System). Chwytaki Bernoullego wykorzystano też np. w przedstawionej na fotografii 3 automatycznej linii do manipulowania ogniwami słonecznymi z robotem kartezjańskim, którą oferuje Festo.
ROBOTY
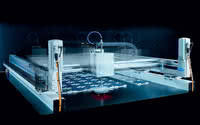
Fot. 3. Linia do manipulowania ogniwami słonecznymi z robotem kartezjańskim Festo
Oprócz peryferii o wydajności stanowiska, a tym samym całej produkcji decyduje szybkość i powtarzalność konkretnego robota. Ważny jest też wybór odpowiedniego typu tej maszyny. Przykładowo na etapie obróbki krzemowych bloków pracują najczęściej roboty kartezjańskie oraz przegubowe. Te pierwsze często wykorzystuje się później w operacjach typu "podnieś-połóż" - np. w sortowaniu i układaniu ogniw w stosy oraz przykładowo w dozowaniu uszczelniaczy na kołnierzu skrzynki przyłączowej montowanej na modułach.
Z kolei roboty przegubowe najczęściej realizują zadania odbiegające od standardowej operacji "podnieś-połóż". Angażuje się je do operacji wymagających od robota większej "zręczności" - np. przenoszenia ciężkich bloków krzemu oraz kaset z krzemowymi płytkami. Innym przykładem jest transport oraz manipulowanie szklanymi płytami dostarczanymi na stanowisko w różnych orientacjach. Czasem są one ustawiane pionowo pod ścianą, aby zwiększyć powierzchnię roboczą, a potem, w celu dalszej obróbki, należy je ułożyć poziomo.
Roboty przegubowe czasem są też używane do przycinania krawędzi oraz montażu modułów. W porównaniu do wspomnianych roboty SCARA i równoległe są szybsze oraz wydajniejsze, zwłaszcza w zadaniach typu "podnieś-połóż". Ponadto sprawdzają się tam, gdzie przestrzeń robocza jest ograniczona. Przykładowo roboty równoległe zazwyczaj montowane są nad stanowiskiem, dzięki czemu mają lepszy dostęp do obrabianych detali i nie zajmują dużo miejsca.
Z drugiej strony są w stanie operować jedynie lekkimi obiektami. Stąd roboty SCARA i równoległe w produkcji ogniw PV są wykorzystywane najczęściej w obróbce ogniw lub już pociętych płytek. Przykładem są maszyny, w których krążki krzemowe poddawane są chemicznemu czyszczeniu lub maszyny do nanoszenia powłok przeciwodblaskowych.
ROBOTY DO POMIESZCZEŃ CLEAN ROOM
W części przypadków "zwykły" robot nie wystarczy. Niektóre etapy produkcji - np. w technologii cienkowarstwowej, gdzie materiał fotoczuły jest nanoszony bezpośrednio na podłoże, wymagają zachowania dużej sterylności. Przykładem robota, który można wykorzystać w takich warunkach, jest specjalnie zmodyfikowana wersja IRB 6640 firmy ABB. Aby przystosować go do wymagań stawianych urządzeniom pracującym w urządzeniach o podwyższonej czystości, pokryto kilkoma powłokami, w tym warstwą gruntującą, białą farbą, lakierem bezbarwnym i powłoką wykończeniową.
W celu zapobieżenia późniejszemu złuszczaniu się farby wszelkie śruby oraz drzwiczki kontrolne zabezpieczono przed malowaniem osłonami z tworzyw sztucznych, które po wyschnięciu farby usunięto. Dodatkowo okablowanie umieszczono w prowadnicach, tak aby zapobiec jego ścieraniu się. Przed wysłaniem do klienta IRB 6640 jest czyszczony, a następnie pakowany w dwie powłoki z tworzywa sztucznego. Pierwsza jest zdejmowana u klienta, przed wstawieniem robota do pomieszczenia clean room, druga usuwana dopiero w pomieszczeniu sterylnym, w którym robot będzie pracował.
PODSUMOWANIE
Minione lata, w których nastąpił bardzo szybki rozwój branży fotowoltaicznej, pokazały, że dla producentów automatyki ta gałąź energetyki odnawialnej jest coraz bardziej interesująca. Dowodzą tego również statystyki - przykładowo według IMS Research światowy rynek maszyn do produkcji ogniw PV przekroczy w 2013 roku 9 mld dolarów, co oznacza wzrost o 80% w porównaniu do wartości z 2008 roku (5 mld dol.). Wzrosną też wydatki na inwestycje w automatyzację produkcji do ponad 1,2 mld dol. w 2013 z 450 mln dolarów dwa lata temu.
Monika Jaworowska