INNE USZKODZENIA
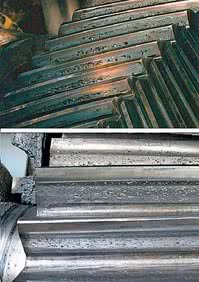
Fot. 2. Przykład występowania wżerek
Jeżeli smar zostanie zanieczyszczony na przykład wodą morską lub chemikaliami, rozwinąć się może korozja metalu zębów przekładni. Aby tego uniknąć, olej należy często zmieniać. W trudnych warunkach otoczenia jedynym rozwiązaniem może się okazać hermetyzacja przekładni.
Na powierzchni zębów występować też mogą charakterystyczne dziurki, z czasem zmieniające się we wżerki (pitting) (fot. 2). Powstają one, gdy wytrzymałość zmęczeniowa materiału zostanie przekroczona, zwykle w wyniku nierównomiernego rozłożenia obciążenia. Podobne objawy występują w wyniku łuszczenia się powierzchni kół zębatych (spalling). Ubytki są jednak wówczas płytsze i mają większą średnicę niż wżery. Postęp uszkodzeń obu typów spowolnić może szlifowanie powierzchni metalu lub jej utwardzenie. Najczęściej konieczne jest jednak całkowite przeprojektowanie przekładni. Zarówno złuszczenia, jak i wgłębienia są bowiem oznaką, że koła zębate nie zostały dobrane odpowiednio do wymagań danej aplikacji.
Innym problemem jest zacieranie się zębów (scoring) (fot. 3). W wyniku kontaktu na powierzchni współpracujących kół powstają wówczas specyficzne pionowe ślady w kierunku ześlizgu zębów. Ich główną przyczyną jest przegrzewanie się przekładni, które może wystąpić na przykład przy niedostatecznej ilości oleju, nadmiernym obciążeniu lub zbyt dużej prędkości obrotów.
W skrajnych przypadkach zmęczenie materiału skutkować może pęknięciem u podstawy zęba. Z czasem prowadzi to do odłamania się go w całości lub tylko jego fragmentu. Aby temu zapobiec, oprócz dopasowania wytrzymałości materiału zębatki do jej spodziewanych obciążeń, należy polerować oraz utwardzać zaokrąglone przejścia między zębami koła.
Pod wpływem zbyt dużego obciążenia zachodzi też zjawisko płynięcia plastycznego (plastic flow), w wyniku którego zęby przekładni ulegają deformacji. Można mu zapobiec, m.in. zmniejszając luzy międzyzębne lub zastępując koło elementem wykonanym z twardszego materiału.
Wieloetapowa diagnostyka pompy odśrodkowej
Kolejne kroki jakie podjęto to: inspekcja wału i wirnika pompy. Na tym pierwszym nie było żadnych niepokojących śladów, natomiast na wirniku odkryto żłobienia oraz zadrapania. Okazało się również, że jest on niewyważony. Najpierw zdecydowano się na rozwiązanie tego drugiego problemu. Po wyważeniu wirnika pompę złożono w całość i uruchomiono. Niestety podobnie jak wcześniej hałas i wibracje nie ustąpiły. Wówczas w miejsce wirnika noszącego już ślady korozji zamontowano nowy. To jednak również nie rozwiązało problemu. Wobec tego zdecydowano się wezwać na pomoc przedstawiciela producenta pompy. Ten ponownie rozmontował to urządzenie i jeszcze raz sprawdził wirnik, wał, łożyska oraz dodatkowo spiralną osłonę pompy. Okazało się, że na tej ostatniej, na powierzchni wokół wlotu pompy występuje korozja, która już bardzo głęboko wniknęła w materiał. Z jej powodu znacznie (ponad 30-krotnie) zwiększył się odstęp między wirnikiem i obudową. Po odkryciu tego faktu natychmiast zamontowano nową, zapasową osłonę pompy. Po ponownym uruchomieniu urządzenia wszyscy zaangażowani w jego naprawę mogli wreszcie odetchnąć z ulgą. Pompa pracowała bowiem prawie bezgłośnie oraz równo, a poziom wibracji zmniejszył się o 90%. Takie drgania w czasie pracy maszyny były praktycznie niewyczuwalne. Przyczyną uszkodzenia osłony okazały się drobne cząstki zanieczyszczeń występujące w pompowanej substancji. Aby zapobiec ponownej erozji wlotu urządzenia tę ostatnią filtruje się. Ponadto okresowo sprawdzany jest poziom wibracji pompy. |
UKŁADY HYDRAULICZNE
W układach hydraulicznych większość problemów objawia się nadmiernym hałasem, podwyższeniem temperatury płynu roboczego lub spadkiem wydajności. Głośna praca jest zwykle spowodowana jednym z dwóch zjawisk: napowietrzeniem czynnika roboczego lub kawitacją.
O obecności pęcherzyków powietrza w płynie hydraulicznym świadczy przede wszystkim charakterystyczne stukanie podczas jego sprężania i rozprężania. Inne oznaki to pienienie się czynnika roboczego oraz nieregularne ruchy siłowników. Powietrze, które zmniejsza wydajność układów hydraulicznych, przenika do nich zwykle wlotem pompy. Z tego powodu ta część systemu wymaga większej uwagi. Sprawdzić na przykład trzeba szczelność połączeń. Pamiętać należy też, że elastyczne przewody wlotowe z czasem stają się porowate, dlatego warto je regularnie wymieniać. Ponadto, jeżeli poziom płynu hydraulicznego w zbiorniku jest zbyt niski, powstać może wir, który ułatwi wniknięcie powietrza do pompy. Czasem przenika ono do systemu również przez nieszczelne połączenie wału.
Kawitacja występuje, gdy na skutek niedopasowania zapotrzebowania na czynnik roboczy do wydajności układu hydraulicznego spada ciśnienie płynu. Powoduje to gwałtowną jego przemianę z fazy ciekłej w gazową. Powstają w nim wówczas pęcherzyki, które sprężane implodują. Towarzyszy temu charakterystyczny hałas, wytwarza się również fala uderzeniowa. Ta ostatnia może uszkadzać elementy systemu. Drobiny uwalniane z nich w wyniku erozji zanieczyszczają płyn hydrauliczny. Prawdopodobieństwo wystąpienia kawitacji można zmniejszyć, m.in. dbając o to, aby filtry wejściowe pomp i przewody doprowadzające płyn nie były zapchane.
W czasie sprężania powietrza wydziela się ciepło. Dlatego napowietrzenie płynu hydraulicznego oraz kawitacja powodują wzrost jego temperatury. Ciepło czynnika roboczego rozpraszane jest głównie w jego zbiorniku. Aby zwiększyć efektywność oddawania ciepła do otoczenia, należy zadbać o swobodny przepływ powietrza wokół zasobnika płynu hydraulicznego. Ważne też, by nie dopuścić do nagromadzenia się na jego ścianach osadów, które będą go termicznie izolować. Przegrzewanie się czynnika roboczego skraca czas jego użytkowania. Jego wysoka temperatura negatywnie wpływa też na komponenty systemu, na przykład uszczelnienia. Spadek wydajności układu hydraulicznego jest z kolei jednym z głównych symptomów wycieku czynnika roboczego.
|
SIŁOWNIKI PNEUMATYCZNE
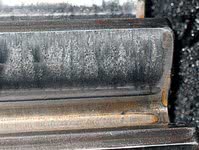
Fot. 3. Przykład zacierania się zębów
W siłownikach pneumatycznych energia czynnika roboczego, czyli sprężonego powietrza, jest zamieniana na energię mechaniczną. Ta ostatnia jest przekazywana dalej elementom maszyn wprawianym w ruch przez siłownik. Urządzenie to składa się z niewielu komponentów, a jego konstrukcja nie jest specjalnie skomplikowana. Na przykład główne elementy siłownika tłokowego to: tuleja, w której umieszczony jest tłok z tłoczyskiem, oraz pierścienie uszczelniające. Mimo prostoty budowy przyczyny problemów w funkcjonowaniu tego urządzenia mogą być złożone.
Częstą przyczyną awarii są zanieczyszczenia, które przenikają do wnętrza siłownika. Dostają się one tam wraz z czynnikiem roboczym albo wnikają z otoczenia. Są to głównie różnego typu okruchy i odłamki oraz piach, jak również woda i oleje. Powodują one korozję metalowych powierzchni siłownika, ich ścieranie oraz przedwczesne zużycie się uszczelnień. Aby temu zapobiec, należy filtrować powietrze zasilające siłownik oraz stosować osłony lub pierścienie zbierające. Filtry trzeba regularnie oczyszczać, podobnie jak przewody rurowe połączone z siłownikiem. Te ostatnie dla ochrony przed korozją wykonuje się ze stali nierdzewnej lub pokrywa powłokami ochronnymi.
Jeżeli siłownik pracować będzie w skrajnych temperaturach otoczenia, konieczne jest osuszanie sprężonego powietrza oraz kontrola jego wilgotności. Chodzi o to, aby punkt rosy czynnika roboczego miał temperaturę niższą niż temperatura otoczenia. W przeciwnym wypadku zawarta w nim para wodna ulegnie kondensacji. W niskiej temperaturze skropliny mogą zamarznąć wewnątrz siłownika, co z kolei spowoduje uszkodzenie jego uszczelnień. Ulegają one zniszczeniu również w wyniku nieprawidłowego zamontowania siłownika (tzw. wyboczenia) lub przekroczenia maksymalnych parametrów pracy (ciśnienia, obciążenia). W skrajnych przypadkach to ostatnie może nawet skutkować złamaniem tłoczyska.
Przykłady przedstawione w tekście oraz w ramkach obok nie wyczerpują tytułowego zagadnienia. Do każdego parku maszynowego należy bowiem podejść indywidualnie. Ważny jest również wybór odpowiednich narzędzi pomiarowych oraz strategii utrzymania ruchu.
POMIARY
Aby zdiagnozować przyczynę awarii danego urządzenia lub komponentu czasem wystarczy po prostu do niego "zajrzeć". Częściej w tym celu skorzystać trzeba jednak ze specjalistycznego sprzętu pomiarowego. Do pomiaru temperatury zwykle używane są przyrządy bezkontaktowe, na przykład kamery termowizyjne oraz pirometry. Wycieki płynów można wykryć, mierząc ich natężenie przepływu lub ciśnienie. Do pomiaru wibracji używa się analizatorów drgań. Do wykrywania wad materiałów często wykorzystuje się natomiast mierniki ultradźwiękowe.
W tych ostatnich w kierunku badanego obiektu nadajnik przyrządu (defektoskopu) wysyła fale ultra dźwiękowe. Te po odbiciu od nieregularności wewnątrz materiału są rejestrowane w odbiorniku przyrządu. Od rodzaju, kształtu oraz rozmiaru skaz w strukturze obiektu zależy amplituda fali odbitej. Mierzy się również czas jej powrotu oraz wiele innych charakterystyk. To pierwsze pozwala na przykład określić, na jakiej głębokości znajduje się wada.
Pomiary ultradźwiękowe mają wiele zalet. Wykrywają one m.in. zarówno defekty na powierzchni, jak i wewnątrz obiektu, mierzą skazy na głębokościach większych, niż wynosi zasięg konkurencyjnych metod pomiarowych oraz nie wymagają specjalnego przygotowywania badanej powierzchni. Oprócz detekcji wad mierzą również grubość materiału. Dzięki temu zakres ich zastosowań jest szeroki. Używa się ich przykładowo w detekcji szczelności i stanu: systemów próżniowych, parowych (kotłów, wymienników ciepła, odwadniaczy skroplin), pneumatycznych i hydraulicznych, zbiorników, rurociągów, włazów, elementów przekładni, pomp, silników, zaworów oraz łożysk. Tę metodę zaleca się szczególnie w inspekcji tych ostatnich. Pozwala ona bowiem wykryć najczęstsze problemy, czyli zużycie, zniekształcenie powierzchni, nadmierne lub zbyt skąpe smarowanie łożysk na bardzo wczesnym etapie, tzn. zanim jeszcze problem ten pogłębi się na tyle, że spowoduje wzrost temperatury oraz nadmierne wibracje.
Demontaż sprężarki ujawnia problem z izolacją
Aby określić przyczynę problemów w działaniu sprężarek jedną z nich zastąpiono tą wynajmowaną. Następnie przeprowadzono inspekcję urządzenia wyłączonego z eksploatacji. Okazało się wówczas, że przyczyną problemów jest izolacja akustyczna sprężarki. Z powodu wilgoci oraz środków chemicznych używanych w tym zakładzie uległa ona zniszczeniu. Obsługa oczyściła sprężarkę z okruchów izolacji. Tę ostatnią wymieniono ponadto na nową, innego typu. Tym razem zamiast piankowej wybrano izolację wykonaną z kauczuku, odporniejszą na warunki w jakich pracuje to urządzenie. Czynności te powtórzono w pozostałych sprężarkach. Od tej pory awarie były o wiele rzadsze. |
UTRZYMANIE RUCHU
Najczęściej w zakładach przemysłowych wdrażane jest utrzymanie ruchu: korygujące (corrective), prewencyjne (preventive) lub predykcyjne (predictive). To pierwsze polega na podejmowaniu działania dopiero w momencie wystąpienia awarii (lub tuż przed). Zadaniem personelu jest jak najszybsze jej wykrycie oraz usunięcie. Koszty z tym związane obejmują: wydatki na części zapasowe, koszty pracy oraz straty produkcji (i sprzedaży). W razie poważnej awarii zwykle te ostatnie są dla firmy najdotkliwsze. Aby je zmniejszyć, trzeba przyspieszyć naprawę. Można to osiągnąć m.in.: zwiększając liczbę osób w dziale utrzymania ruchu, inwestując w urządzenia i systemy zapasowe, które zapewnią ciągłość produkcji w razie awarii oraz ciągle udoskonalać procedury alarmowe. Z tym jednak również wiążą się koszty.
W predykcyjnym utrzymaniu ruchu inspekcja jest przeprowadzana stosownie do potrzeb, na przykład jeżeli odnotowana zostanie jakaś znacząca zmiana w charakterystyce urządzenia. Rejestracja oraz analiza tego ostatniego ułatwia wykrywanie często powtarzających się problemów oraz identyfikację maszyn najbardziej awaryjnych.
W prewencyjnym utrzymaniu ruchu sprzęt kontroluje się okresowo, według planu. Od tego ostatniego zależy efektywność oraz koszty inspekcji. Wydatki można znacznie zmniejszyć, przeprowadzając przeglądy, zwłaszcza te wymagające wyłączenia maszyn, w czasie innych planowanych przestojów. Takie okazje zdarzają się przykładowo w czasie wprowadzania zmian w konfiguracji sprzętu lub modernizacji parku maszynowego.
Poszczególne strategie utrzymania ruchu zwykle stosowane są jako wzajemne uzupełnienia. Celem jest zawsze kompromis między ich efektywnością a kosztami.
Monika Jaworowska