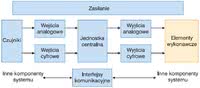
Rys. 1. Główne części składowe PLC
Już taka pobieżna charakterystyka funkcjonalności PLC pozwala na wyróżnienie jego zasadniczych części składowych. Są to: wejścia (analogowe, cyfrowe), jednostka centralna, pamięć, wyjścia (analogowe, cyfrowe), interfejsy komunikacyjne oraz zasilacz (rys. 1). W kompaktowych PLC, o sztywnej architekturze i mniejszych rozmiarach, podzespoły te są zintegrowane w jednej obudowie.
Więcej swobody zapewniają PLC modułowe, gdzie komponenty można dokładać i odinstalowywać w zależności od potrzeb w obrębie specjalnych szyn lub kaset. W artykule "zaglądamy" do środka sterowników programowalnych, w tym tych w wykonaniu niestandardowym, jak Safety PLC, kolejno charakteryzując wymienione części. Przedstawiamy również cykl pracy sterownika.
ROLA I PODZIAŁ WEJŚĆ ANALOGOWYCH
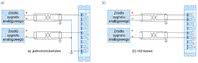
Rys. 2. Wejścia analogowe mogą być: (a) jednokońcówkowe lub (b) różnicowe
Zadaniem wejść analogowych PLC jest przekształcenie sygnałów ciągłych na cyfrowe, których wartości mogą być dalej zapisywane w pamięci i przetwarzane przez procesor. Te pierwsze to sygnały napięciowe, zwykle o wartościach -10 V... +10 V, 0...+10 V lub 1...+5 V albo prądowe, zazwyczaj w przedziale 0...20 mA lub 4...20 mA. Odzwierciedlają one zmiany wielkości fizycznych - na przykład temperatury, ciśnienia, poziomu lub przepływu, mierzonych przez czujniki monitorujące przebieg sterowanego procesu.
Wejścia analogowe napięciowe to układy o dużej impedancji wejściowej, rzędu MΩ. W wypadku prądowych wartość tego parametru nie przekracza 500Ω. Mogą być one różnicowe (Differential) albo jednokońcówkowe (Single-Ended) - w tych pierwszych przetwarzana jest różnica napięć między dwoma wejściami, natomiast w drugich napięciem odniesienia jest masa wspólna dla wszystkich wejść (rys. 2). Zaletą wejść różnicowych jest większa odporność na zaburzenia z zewnątrz. Jednokońcówkowe charakteryzuje za to większa gęstość upakowania wejść w pojedynczym module. Przewody łączące je ze źródłem sygnału należy jednak ekranować. Warto pamiętać, że w razie potrzeby, gdy źródło sygnału jest oddalone od PLC, możemy skorzystać z rozproszonych modułów I/O.
WEJŚCIA ANALOGOWE OD ŚRODKA
Za konwersję analogowo-cyfrową odpowiada przetwornik A/C. Sygnał jest do niego doprowadzany za pośrednictwem filtru aktywnego. Filtry montowane w PLC to zwykle układy dolnoprzepustowe lub pasmowoprzepustowe, klasyczne lub z przełączanymi pojemnościami.
W zależności od sposobu realizacji toru przetwarzania, sygnał do filtru dociera ze wspólnego wzmacniacza, którego wejście połączone jest z wyjściem multipleksera analogowego albo z wyjścia zespołu przełączników analogowych, do których wejść dołączone są wzmacniacze, oddzielne dla każdego z kanałów.
Wymagania stawiane multiplekserom to głównie: mała rezystancja w stanie załączenia i mały prąd upływu. W stopniu wzmacniającym najczęściej używane są układy PGA (Programmable Gain Amplifiers) lub dyskretne, bipolarne wzmacniacze operacyjne i precyzyjne dzielniki rezystancyjne. Powinno je charakteryzować m.in. małe napięcie offsetu i jego minimalny dryft temperaturowy. Określone wymogi musi też spełniać sam przetwornik A/C. Na przykład maksymalna częstotliwość próbkowania zależy od częstotliwości sygnału, a rozdzielczość przetwornika od jego budowy.
Cykl pracy PLC
Ważne! Jakakolwiek zmiana stanu wejść sterownika w czasie, gdy trwa etap wykonywania programu albo przekazywania nowych wartości na wyjścia PLC, nie będzie uwzględniana do czasu rozpoczęcia kolejnego cyklu oraz ponownego zeskanowania wejść sterownika. Analogicznie - stan wyjść PLC nie jest aktualizowany ani wtedy, gdy skanowane są wejścia sterownika, ani w trakcie wykonywania programu użytkownika. Dzieje się to dopiero w fazie nr 4. Szybkość wykonania cyklu zależy od: szybkości procesora, ilości dostępnej pamięci, liczby zmiennych (wejść i wyjść) oraz długości i stopnia skomplikowania programu użytkownika. |
WEJŚCIA CYFROWE SĄ IZOLOWANE GALWANICZNIE

Rys. 3. Wejście cyfrowe
Częścią PLC najczęściej są przetworniki 16-bitowe, chociaż na przykład do konwersji wyników zmierzonych przy użyciu termopar wymagana jest wyższa rozdzielczość, do 24 bitów. Przykładem wielkości, które z reguły zmieniają się na tyle wolno, że niepotrzebna jest duża częstotliwość próbkowania (do kilku tys. próbek/s), są: temperatura, ciśnienie, poziom i przepływ. W wypadku dużej liczby kanałów parametr ten powinien sięgać już jednak kilkuset tys. próbek/s. Dobrze w tym zastosowaniu sprawdzają się m.in. przetworniki z sukcesywną aproksymacją (SAR).
Wejścia cyfrowe PLC przekształcają w sygnały binarne, o poziomach napięć akceptowanych w obwodach sterownika, sygnały dwustanowe (tzn. włączony / wyłączony, zamknięty / otwarty, prawda / fałsz) z urządzeń takich jak przyciski, przełączniki i styki. Najczęściej spotykane napięcia tych sygnałów to: 0-5 VDC, 0-12 VDC, 0-24 VDC, 0-120 VAC i 0-240 VAC.
Na rysunku 3 przedstawiono uproszczony schemat wejścia cyfrowego AC. Składa się ono z: mostka diodowego, który odpowiada za konwersję AC/DC, filtru oraz komparatora. Kolejnym blokiem jest optoizolator, który zapewnia separację galwaniczną pomiędzy obwodami zewnętrznymi a tymi sterownika. Zasadniczą różnicą między wejściami AC i DC jest brak prostownika na wejściu tych drugich.
Safety PLC![]() W systemach sterowania wymagających ponadstandardowej niezawodności wykorzystywane są sterowniki typu Safety PLC. Chociaż są zbudowane z tych samych bloków funkcyjnych, co zwyczajne sterowniki, wprowadza się w nich specjalne rozwiązania konstrukcyjne. Na przykład nadmiarowość zapewnia się na poziomie procesorów, natomiast działanie systemu jest kontrolowane przez watch doga. Ponadto sterowniki w wykonaniu bezpiecznym wyposażane są w obwody testowania poprawności funkcjonowania ich wejść. Realizuje się to, przypisując im "wewnętrzne" wyjścia. Ich stan jest porównywany z wartościami oczekiwanymi każdorazowo w czasie uruchamiania PLC, gdy stan wejść sterownika przyjmuje testowe wartości. Redundancja i testowanie są również zapewnione dla wyjść sterownika. |
ROLA JEDNOSTKI CENTRALNEJ I PODZIAŁ PAMIĘCI
Do zadań procesora sterownika należy: zarządzanie pracą całego urządzenia, odczyt stanu jego wejść i aktualizacja stanu wyjść, wykonanie programu użytkownika oraz zarządzanie komunikacją z innymi elementami systemu sterowania. Jeżeli chodzi o pamięć, to PLC są wyposażane zarówno w te typu RAM, jak i ROM. Ich pojemności i sposób wykorzystania zależą od specyfiki konstrukcji danego sterownika, można jednak wyróżnić co najmniej pięć głównych obszarów zastosowań.
Pamięć systemu operacyjnego (wbudowanego) jest zapisywana przez producenta i rzadko później zmieniana. Aby system operacyjny mógł działać, część pamięci RAM jest zarezerwowana na jego potrzeby, na przykład przechowywanie danych tymczasowych. Są to m.in.: kody błędów, które wystąpiły podczas wykonywania programu użytkownika.
Część pamięci RAM jest również przydzielona do przechowywania aktualnego stanu wejść i wyjść PLC. Każdemu z nich przypisany zostaje konkretny adres. W czasie wykonywania programu użytkownika to właśnie z tego obszaru pamięci, a nie bezpośrednio z danego wejścia, odczytywane są wartości zmiennych wejściowych. Analogicznie, pod odpowiednim adresem, zapisywane są stany wyjść sterownika.
PLC kontra systemy wbudowaneW przeciwieństwie do PLC, w wypadku których sprzęt jest dostępny od ręki i wymaga tylko zaprogramowania oraz zorganizowania na poziomie systemu sterowania, systemy wbudowane wymagają więcej czasu i wysiłku na stworzenie (i przetestowanie) kompletnej platformy sprzętowo-programowo-systemowej. Ich funkcjonalność, sprzętowa i programowa, jest ponadto ograniczona do wymogów danej aplikacji, podczas gdy PLC charakteryzuje pod tym względem większa nadmiarowość. Dlatego pewnych funkcji nie da się w tych pierwszych później dodać, natomiast w wypadku sterowników programowalnych wystarczy, na przykład, dołączyć nowy moduł wejść i wyjść i dopisać kawałek kodu. Również utrzymanie systemu z PLC, ze względu na dostępność standardowych modułów, jest łatwiejsze. Z drugiej strony, gdy funkcje są ściśle określone i niezmienne, wybór PLC może być kosztowniejszy. |
KOMUNIKACJA ORAZ ZASILANIE STEROWNIKA
W pamięci RAM przechowywane są też różne dane (stan liczników, wyniki obliczeń, parametry procesu), które są używane przez funkcje programu użytkownika. Ten ostatni też zresztą jest w niej zapisywany. W niektórych PLC program użytkownika i pewne stałe dane można jednak, po wstępnym przetestowaniu ich w wersji z pamięci ulotnej, przekopiować do pamięci EEPROM.
Za pośrednictwem interfejsów komunikacyjnych, które wyposażone są zwykle w oddzielny kontroler nadzorujący przebieg transmisji, sterownik komunikuje się na przykład z: innymi PLC, panelami operatorskimi oraz nadrzędnymi systemami sterowania (
Rys. 4. Wyjście cyfrowe AC