Asortyment tytułowej branży jest szeroki. Generalnie można go podzielić na dwie grupy: napoje alkoholowe i bezalkoholowe. Do pierwszej zaliczane są m.in.: piwa, wina i wódki, a do drugiej m.in.: soki owocowe, soki warzywne, wody mineralne, napoje gazowane i produkty mleczne (kefiry, jogurty pitne). Produkcja napojów jest złożona i wieloetapowa. Przedstawiamy to na przykładzie: piwa, wódki, soków oraz bezalkoholowych napojów gazowanych.
CZĘŚĆ 1. PRZYGOTOWANIE NAPOJÓW
Do produkcji piwa potrzebne są wysuszone skiełkowane ziarna jęczmienia (słód). Mieli się je do otrzymania śrutu słodowego. Po zmieszaniu go z wodą i ogrzaniu powstaje zacier. Filtruje się go, aby oddzielić części stałe nierozpuszczone w procesie zacierania, jak łuski i zarodki, od roztworu rozpuszczalnych składników. Tak powstaje brzeczka.
Gotuje się ją w kotle warzelnym z chmielem, w celu rozpuszczenia i przemiany substancji chmielu, odparowania wody, sterylizacji, zakwaszenia i zniszczenia enzymów. Następnie brzeczka trafia do kadzi wirowej. Dochodzi w niej do wytrącenia się osadu. Po usunięciu go brzeczka zostaje schłodzona.
Kolejny etap to fermentacja, podczas której drożdże przetwarzają cukry zawarte w brzeczce w etanol i dwutlenek węgla. Gotowe piwo leżakuje. Potem trafia do zbiorników, gdzie jest przechowywane przed rozlaniem do kegów, butelek, puszek. Wcześniej poddawane jest jeszcze filtracji i pasteryzowane.
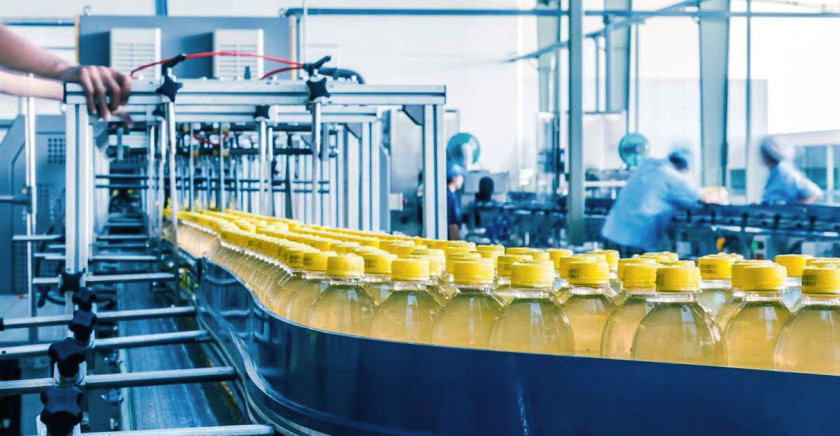
Wódkę produkuje się m.in. z: ziemniaków, żyta, pszenicy, pszenżyta, jęczmienia, owsa. Pierwszym etapem jest przygotowanie tych składników, podobnie jak w produkcji piwa, przez podgrzanie ich w wodzie. Do powstałego zacieru dodaje się drożdże. Zachodzi wówczas fermentacja. Kolejnymi krokami są: destylacja oraz rektyfikacja odfermentowanego zacieru w celu oddzielenia alkoholu etylowego od zanieczyszczeń.
Następnie miesza się go z wodą. Ten rozcieńczalnik alkoholu ma duży wpływ na jakość produktu finalnego, dlatego używana jest woda o najwyższej czystości i demineralizowana. W ten sposób powstaje wódka. Ostatnim etapem przed rozlaniem do butelek jest jej filtracja.
JAK SIĘ PRODUKUJE SOKI OWOCOWE I NAPOJE GAZOWANE?
Sok owocowy jest uzyskiwany z koncentratu. Pierwszym etapem jego produkcji jest przebranie, umycie i obranie owoców, które później rozdrabnia się i zgniata. Powstała w ten sposób miazga poddawana jest depektynizacji w celu rozłożenia związków pektynowych. Ułatwia to tłoczenie i poprawia jego wydajność. Z miazgi wyciska się sok.
Potem dearomatyzuje się go, żeby uzyskać kondensat substancji zapachowych. Operację tę przeprowadza się w podgrzewaczu, w którym sok jest równocześnie pasteryzowany. Następnie znowu poddaje się go depektynizacji. Potem sok jest klarowany, filtrowany i zagęszczany przez odparowanie wody. Przed magazynowaniem koncentrat schładza się. Aby wyprodukować z niego sok, dodaje się wodę i kondensat zapachowy.
Napoje bezalkoholowe gazowane produkuje się z wody z różnymi dodatkami w zależności od tego, jakie walory smakowe, zapachowe i estetyczne (kolor) chce się uzyskać w produkcie finalnym. W związku z tym w ich składzie można znaleźć m.in.: syrop fruktozowo-glukozowy, soki owocowe, cukier, regulatory kwasowości, jak cytrynian sodu lub kwas cytrynowy, substancje konserwujące, przykładowo sorbinian potasu albo benzoesan sodu, przeciwutleniacze, jak kwas askorbinowy, aromaty, barwniki (na przykład karoteny) i dwutlenek węgla. Dodatki zwykle najpierw rozcieńcza się wodą. Następnie ich roztwory miesza się ze sobą. Powstały w ten sposób syrop pasteryzuje się, a potem schładza. Dalej zostaje on nasycony dwutlenkiem węgla i rozlany do butelek.
NA CZYM POLEGA PRODUKCJA WSADOWA?
Kolejne etapy produkcji napojów są zwykle realizowane jako procesy wsadowe, czyli przebiegające przez określony czas i zazwyczaj w jednym urządzeniu, według receptury, która stanowi ustaloną sekwencję kroków. Obejmuje ona załadowanie składników do zbiornika, na przykład kotła albo mieszalnika, i ich przetwarzanie w kontrolowanych warunkach (podgrzewanie, schładzanie lub podtrzymywanie stałej temperatury, obniżanie / podwyższanie ciśnienia, dodawanie / usuwanie substancji, mieszanie). Na koniec produkt finalny jest odprowadzany ze zbiornika. Przykładem procesu, który może być przeprowadzany jako wsadowy, jest fermentacja.
BIOREAKTORY - POMIARY I...
Zachodzi ona w specjalnych zbiornikach - fermentatorach, inaczej fermentorach lub bioreaktorach. Są to złożone urządzenia. Specyfika ich zastosowania wymaga, by były sterylne oraz umożliwiały pomiar i regulację wielkości kluczowych dla właściwego przebiegu zachodzących w nich reakcji. Monitorowane są wielkości fizyczne i chemiczne.
Przykładami pierwszych są: temperatura, natężenie przepływu powietrza, natężenie przepływu cieczy, ciśnienie, poziom cieczy i poziom piany, szybkość obrotów mieszadła, lepkość płynu. W związku z tym fermentory wyposaża się m.in. w: czujniki rezystancyjne, termistory, termopary, przepływomierze łopatkowe, rotametry, kryzy pomiarowe, przetworniki membranowe do pomiaru ciśnienia, pojemnościowe i oporowe czujniki poziomu i reometry do pomiaru lepkości.
Jeśli z kolei chodzi o wielkości chemiczne, w bioreaktorach monitorowane są na przykład: stężenie tlenu rozpuszczonego, pH, potencjał redoks, stężenie tlenu i dwutlenku węgla, czyli gazów, których ilość charakteryzuje aktywność znajdujących się w zbiorniku mikroorganizmów. Do pomiaru stężenia tlenu rozpuszczonego używa się m.in. sond polarograficznych. Stężenie dwutlenku węgla może być oznaczane przez sensory podczerwieni, zaś stężenie tlenu za pomocą analizatorów paramagnetycznych.
Krzywo nałożone nakrętkiW pewnym zakładzie produkującym soki owocowe oraz napoje gazowane operatorów linii rozlewniczej na odcinku napełniania butelek PET oranżadą zaczęły niepokoić powtarzające się coraz częściej alarmy systemu kontroli jakości wykrywającego krzywo założone nakrętki. W końcu liczba opakowań, które z tego powodu w związku z obawą o brak szczelności zamknięcia uznano za wybrakowane, przekroczyła straty dopuszczalne dla tego etapu produkcji. Zdecydowano się wtedy zatrzymać maszyny i przekierować butelkowanie oranżady na sprawne stanowisko zapasowe, wcześniej czasowo wyłączone z eksploatacji ze względu na mniejszą wydajność. Z powodu dużej liczby zamówień tylko tymczasowo rozwiązywało to problem, dlatego sprawność linii głównej trzeba było przywrócić jak najszybciej. W tym celu osoby oddelegowane do tego zadania zweryfikowały najczęstsze przyczyny nieprawidłowości w pracy maszyn tego typu. Generalnie, bez względu na szczegóły konstrukcyjne zakręcarki, powodów krzywego zakładania nakrętek może być kilka. Potencjalnym źródłem problemu jest system ich podawania. Zazwyczaj składa się z misy albo palety wibrującej i prowadnicy, którą zakrętki trafiają do głowicy. Jeśli nie działa prawidłowo, poza krzywym zamocowaniem możliwe jest m.in. uszkodzenie nagwintowania albo pominięcie niektórych butelek. Szukając przyczyny problemu, w podajniku trzeba sprawdzić na przykład, czy nie przesunął się względem przenośnika. Z większymi modyfikacjami lepiej się jednak wstrzymać, wykluczając najpierw inne możliwe nieprawidłowości, ingerencja bez konsultacji z producentem zakręcarki może się bowiem negatywnie odbić na jej wydajności. W opisywanym przypadku, ponieważ pobieżna inspekcja nie wykazała, że podajnik jest wadliwy, inżynierowie skupili się na kolejnym ewentualnym powodzie. Takim bywa niesprawny układ unieruchamiania butelki i pozycjonowania nakrętki w momencie jej zakręcania. W tym celu wykorzystuje się na przykład różnego typu elementy dociskowe, jak pasy i pręty. Jeśli stwierdzi się ich rozluzowanie lub nadmierne ściśnięcie, zwykle wystarczy odpowiednio je wyregulować. W tym przypadku jednak również i tę przyczynę udało się wykluczyć. Kolejnym powodem bywa zdarcie powierzchni albo odkształcenie się długo eksploatowanych elementów mających bezpośredni kontakt z butelkami i zakrętkami. Jak się ostatecznie okazało, właśnie to było przyczyną. Inżynierowie odkryli bowiem, że do wstrzymania pracy głównej linii rozlewu oranżady doszło z powodu nadmiernego, widocznego już gołym okiem, zużycia się rolek dociskowych w głowicy zakręcającej. Stwierdzono to podczas inspekcji tego elementu zakręcarki. Po ich wymianie i wznowieniu produkcji częstość alarmów systemu kontroli jakości zmalała do marginalnej wartości. |
...STEROWANIE
Do regulacji powyższych wielkości fizycznych i chemicznych służą elementy wykonawcze. Podstawowym wyposażeniem są mieszadła, których zadaniem jest zapewnienie jednorodności zawartości bioreaktorów. Mogą być napędzane mechaniczne albo, dla zapewnienia sterylności, magnetycznie. Do regulacji temperatury bioreaktorów oraz ich sterylizacji wykorzystywane są płaszcze grzewczo-chłodzące (wodne, parowe).
Stężenie tlenu rozpuszczonego kontroluje się przez regulację natężenia przepływu w instalacji nasycania zawartości bioreaktora pęcherzykami powietrza oraz zwiększanie lub zmniejszanie szybkości obrotów mieszadła. Zwykle realizuje się to w układzie regulatora kaskadowego.
Problemem w bioreaktorach bywa silne pienienie się. Obniża ono ich pojemność użytkową, utrudnia pomiary, prowadzi do nagromadzania się osadów na ściankach i może spowodować skażenie materiału w zbiorniku w przypadku wniknięcia piany do układu wentylacji. Dlatego fermentory wyposaża się w mechaniczne rozbijacze piany lub stosuje się środki zmniejszające pienienie się. Czujniki piany, pH i zapełnienia zbiornika współpracują z pompami dozującymi środki antypienne, substancje regulujące pH i medium procesowe. Bioreaktory wyposaża się również w zawory do pobierania próbek ich zawartości do badań.
Szkło w szkle - czemu trudno je wykryć?
Poza tym w szkle naturalnie powstają różnego typu skazy, jak na przykład pęcherzyki gazów, wtrącenia, plamy. Może także zawierać nieszkodliwe dla konsumentów wtopione zanieczyszczenia, na przykład drobiny metalowe, szkła innego gatunku, plastiku. Nie są one powtarzalne. Poza tym opakowania od różnych producentów, chociaż pozornie takie same, mogą się różnić składem chemicznym szkła i jego gęstością. To także wpływa na skuteczność inspekcji rentgenowskiej. Zależy ona oprócz tego w ogromnym stopniu od kształtu opakowania - im wymyślniejszy, tym jest mniejsza. Kontrola RTG najefektywniejsza jest w przypadku okrągłych butelek, bez ostrych kantów, w których w butelkach kwadratowych i prostokątnych od środka mogą się zbierać niewykrywalne zabrudzenia. Ponadto orientacja okrągłych butelek jest bez znaczenia. Utrudnienie stanowią wszelkie tłoczenia. Trudności w interpretacji obrazu rentgenowskiego może również sprawić wieczko ze względu na zgrubienia szkła na gwincie i metalową albo wykonaną z tworzywa sztucznego zakrętkę. Nie bez znaczenia są właściwości płynu, przede wszystkim jego lepkość, od niej bowiem zależy to, na jakiej głębokości będą się utrzymywać zanieczyszczenia. Zazwyczaj w przypadku napojów opadają one na dno, ale jeśli są one półpłynne, mogą podczas nalewania unieść zabrudzenia z dna i ścianek opakowania wyżej. Wówczas wymagana jest inspekcja całego pojemnika, a nie tylko jego dolnej części. |
JAK DZIAŁA SATURATOR?
Ważnym elementem linii produkcyjnych napojów bezalkoholowych i z alkoholem (piwa, wina) jest saturator, czyli urządzenie służące do nasycania ich dwutlenkiem węgla. Dzięki niemu musują, zapewniając charakterystyczne orzeźwienie. CO2 jako gaz nietoksyczny, obojętny i w zasadzie bezsmakowy, jest jednym z nielicznych, które nadają się do tego celu. Dwutlenek węgla hamuje oprócz tego rozwój bakterii i pleśni oraz ma właściwości konserwujące, dzięki czemu uzupełnia działanie innych środków dodawanych w tych celach do napojów.
Stopień nasycenia napojów CO2 jest różny w zależności od ich typu - na przykład bezalkoholowe zwykle wymagają dawki około 6÷8 g tego gazu na litr. Dwutlenek węgla przeważnie jest do zakładu dostarczany w stanie płynnym. Musi spełniać normy jakościowe, na przykład na zawartość tlenku węgla, która nie powinna przekraczać 0,1% i musi być neutralny zapachowo.
Saturator składa się typowo z ciągu rur, czujnika zawartości dwutlenku węgla, zaworu regulującego jego dopływ i jednostki sterującej. Gaz jest wprowadzany do cieczy za pomocą specjalnej dyszy (zwężki) zapewniającej jego równomierne rozprowadzenie i dokładne wymieszanie z napojem. Zawartość CO2 mierzona na wylocie saturatora zostaje porównana w regulatorze z wartością docelową. Na podstawie wyznaczonej w ten sposób różnicy steruje on zaworem regulującym dopływ dwutlenku węgla.
Praktykowane są dwie metody saturacji: gotowego napoju albo wody, do której dopiero zostaną dodane pozostałe składniki. W drugim przypadku urządzenia miksująco-saturacyjne mogą działać dwufazowo albo jednofazowo, jednocześnie mieszając składniki napoju i nasycając go CO2. Przed poddaniem cieczy saturacji tym gazem konieczne jest jej odpowietrzenie, obecność tlenu wpływa bowiem na skrócenie trwałości gotowego wyrobu. Gazowany napój trafia do zbiornika, w którym następuje jego ustabilizowanie się konieczne przed rozlewem.
Higiena produkcji w branży napojowej
Przykładowe stosowane w tym celu rozwiązania konstrukcyjne to: gładkie wykończenia powierzchni zewnętrznych i pokrywanie ich powłokami antyadhezyjnymi utrudniającymi przywieranie brudu, brak wentylatorów (chłodzenie przez konwekcję), dzięki czemu zanieczyszczenia z zewnątrz nie są zasysane do urządzenia i nie występują zawirowania powietrza, które rozprzestrzeniałyby zarazki w otoczeniu, wypełnianie wgłębień w obudowach (na przykład gumą), wyprofilowanie ułatwiające odpływ cieczy (bez stref martwych, w których nie ma przepływu, konstrukcje samościekowe), odpowiedni stopień ochrony zapewniający szczelność, korpusy z jednego odlewu (konstrukcje bezspawowe), brak nitów i śrub w komorze z produktem, wzmocnienia uszczelek metalowymi pierścieniami. Elementy wyposażenia linii produkcyjnych, które będą miały kontakt z żywnością, powinny być wykonane z materiałów dopuszczonych do użytku w produkcji spożywczej. Takimi są m.in. stal nierdzewna oraz tytan. Stal nierdzewną wyróżnia odporność na korozję, zaś tytan wytrzymałość mechaniczna oraz odporność na korozję, zwłaszcza w środowisku kwasowym. Wykonuje się z niego elementy stykające się z produktami o dużej zawartości kwasów i soli, na przykład sokami cytrusowymi czy pomidorowymi. Mycie i odkażanie muszą być przeprowadzane regularnie. Zadania te automatyzuje się w ramach systemów CIP (Cleaning in Place) oraz SIP (Sterilization in Place), czyli mycia i sterylizacji na miejscu. Polegają one na spłukiwaniu wnętrza wyposażenia linii produkcyjnych w przerwach między kolejnymi jej uruchomieniami, bez konieczności rozmontowywania elementów, wprowadzania do ich wnętrza urządzeń czyszczących lub wchodzenia do środka. Ważnym zadanie jest również dezynfekcja. Poddaje się jej opakowania, jak również surowiec, jakim jest woda. Metodą, która zyskuje w tym zakresie coraz większą popularność, jest odkażanie przez naświetlanie promieniowaniem ultrafioletowym. Technika ta ma kilka zalet. Najważniejszą jest duża skuteczność (niszczy nawet mikroorganizmy odporne na działanie chloru). Oprócz tego nie jest to proces chemiczny, nie powstają po nim produkty uboczne ani nie jest tak energochłonny, jak na przykład ozonowanie. |
KONTROLA JAKOŚCI OFFLINE
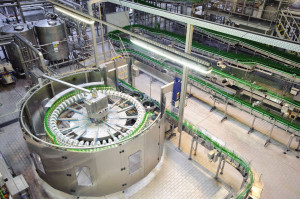
Kontrola jakości w tytułowej branży ma na celu sprawdzenie cech organoleptycznych napojów, ich właściwości fizykochemicznych i składu. Bada się również to, czy spełniają wymogi higieniczne oraz w zakresie zawartości zanieczyszczeń środowiskowych.
Na przykład w przypadku soków cechy organoleptyczne to: smak, barwa, zapach oraz wygląd, inny w przypadku soków przecierowych, które stanowią zawiesinę miąższu i cząstek owoców i warzyw z dopuszczalnym rozwarstwieniem, soków mętnych czy soków klarownych, czyli bez zawiesin i zmętnień.
Właściwości fizykochemiczne oraz składniki to m.in.: zawartość ekstraktu, kwasowość, gęstość, witamina C, cukry i olejki eteryczne. W zakresie wymagań higienicznych i zanieczyszczeń środowiskowych normy określają dopuszczalne graniczne stężenia m.in.: kwasu octowego, kwasu mlekowego, alkoholu i patuliny, której duża ilość świadczy o tym, że surowiec do produkcji soku był spleśniały, arsenu oraz metali ciężkich (ołowiu, rtęci, kadmu).
Po pobraniu próbek z danej partii produkcyjnej są one poddawane analizie w laboratorium. W tym celu korzysta się z różnych urządzeń pomiarowych. Przykładami takich są spektrofotometry. Służą one do pomiaru stopnia absorpcji światła, który zależy od składu oraz właściwości próbki poddanej naświetlaniu. Spektrofotometry znajdują zastosowanie w laboratoryjnej analizie m.in. cech piwa, na przykład: jego barwy, stężenia goryczki, zawartości izo-α- i β-kwasów, wolnego azotu aminowego, polifenoli, diketonow wicynalnych oraz redukowalności.
CO MOŻNA ZMIERZYĆ SPEKTROFOTOMETREM?
Kolor piwa jest jego ważną cechą, gdyż ma wpływ na pierwsze wrażenie, jakie ten napój wywiera na spożywającym. Często też to barwa decyduje o jego przynależności do danego gatunku. Mierzy się ją badając stopień pochłaniania promieniowania o długości fali 430 nm. Po jego przemnożeniu przez współczynnik podany w normie uzyskuje się wartość przypisaną konkretnemu kolorowi na zestandaryzowanej skali.
Źródłem goryczki, która wpływa na smak piwa, są związki zawarte w chmielu. Aby zmierzyć jej zawartość, najpierw gorycz ekstrahuje się, a następnie mierzy się jej absorpcję promieniowania o długości fali 275 nm. Smak piwa zależy też od zawartości izo-α- i β-kwasów. Określa się je badając wyekstrahowaną gorycz pod kątem pochłaniania promieniowania o długości fali 255 nm i 360 nm.
Stężenie wolnego azotu aminowego charakteryzuje przebieg procesu fermentacji - za niskie wskazuje na zbyt powolną lub niepełną, za duże może pogorszyć smak lub doprowadzić do skażenia mikrobiologicznego piwa. Ocenia się je na podstawie stopnia absorpcji próbki z odczynnikiem naświetlonej promieniowaniem o długości fali 570 nm. Polifenole z kolei mają wpływ na barwę, mętność, smak, pienienie i stabilność fizyczno-chemiczną piwa.
Do badania stężenia tych związków wykorzystuje się promieniowanie o długości fali 600 nm. Smak piwa pogarsza też nadmierna zawartość diketonów wicynalnych będących produktem metabolizmu drożdży. Określa się ją, naświetlając próbkę promieniowaniem o długości fali 335 nm. Związki redukujące, które wytwarzają się w procesie produkcji, negatywnie wpływając na jakość piwa, wykrywa się, wykorzystując promieniowanie o długości fali 520 nm.
Przeciek w nalewarceW pewnej fabryce produkującej soki warzywne w ramach modernizacji linii butelkowania kupiono nową nalewarkę przelewową. Zastąpiła wyeksploatowaną maszynę, która została zakupiona kilka lat wcześniej i była dostrajana przez inżynierów już niepracujących w tym przedsiębiorstwie. W związku z tym, gdy okazało się, że po uruchomieniu nowego urządzenia napotkano problemy, nowi pracownicy, którzy wcześniej nie programowali nalewarek tego typu, musieli je rozwiązać metodą prób i błędów. Jednym z nich był wyciek napojów, który zaobserwowano w czasie ich nalewania do butelek. Oprócz tego, że wiązał się ze stratami produktu, był źródłem zanieczyszczeń linii produkcyjnej, niedopuszczalnych w związku z ostrymi wymogami higienicznymi ich dotyczącymi. W związku z tym, że nalewarka została dopiero co kupiona od razu można było wykluczyć jako powód przecieku uszkodzenie albo zużycie się uszczelnień głowicy napełniającej. W przypadku dłużej eksploatowanej maszyny należałoby ich stan skontrolować w pierwszej kolejności. Po konsultacji z producentem nalewarki postanowiono sprawdzić, czy głębokość zanurzenia głowicy napełniającej w opakowaniu jest optymalna. Do wycieku dochodzi zwykle, jeśli wnika zbyt płytko, nie uszczelniając butelki. Trzeba jednocześnie uważać, żeby nie przesadzić w drugą stronę - skutkiem zbyt głębokiego zanurzenia głowicy jest nie tylko wyciek, ale też, będące jego bezpośrednią przyczyną, uszkodzenie otworu butelki. Niestety, chociaż wreszcie udało się ustalić, jak się wydawało, optymalną głębokość zanurzenia dla płynu testowego, po uruchomieniu serii próbnej produkt docelowy, czyli sok warzywny, w dalszym ciągu wyciekał. Ostatecznie okazało się, że typ napoju oraz opakowania wymaga, żeby pod koniec napełniania pompa zwalniała obroty. W przeciwnym razie uszczelnienie nie wytrzymuje ciśnienia, które się wówczas wytwarza i zaczyna przeciekać. Po wprowadzaniu odpowiednich poprawek w programie sterującym nalewarką problem uznano za rozwiązany. |
KONTROLA JAKOŚCI W OPAKOWANIACH I INLINE
Jeśli próbki produktu nie spełniają wymagań jakościowych, partia, z której pochodzą, nie trafia do sprzedaży. W laboratorium sprawdzeniu poddaje się także już zapakowane produkty. Badania tego typu przeprowadza się w specjalnych analizatorach z przebijakami pozwalającymi na dokonywanie pomiaru bezpośrednio w napełnionym napojem opakowaniu. Ponieważ nie jest wymagane pobranie ani przygotowanie materiału do badań, analiza wykonana w butelce albo w puszcze z zachowaniem szczelności opakowania ma wiele zalet.
Przede wszystkim jest dokładniejsza, gdyż nie ma możliwości zanieczyszczenia próbek i mniej czasochłonna. Dzięki temu, że w przyrządach tego typu kluczowe zadania - przebijanie zakrętki, pobieranie napoju, a jeżeli wymaga tego jego specyfika, też potrząsanie nim, są zautomatyzowane, wpływ operatora na wyniki pomiarów jest znikomy. Są zatem wiarygodne i powtarzalne.
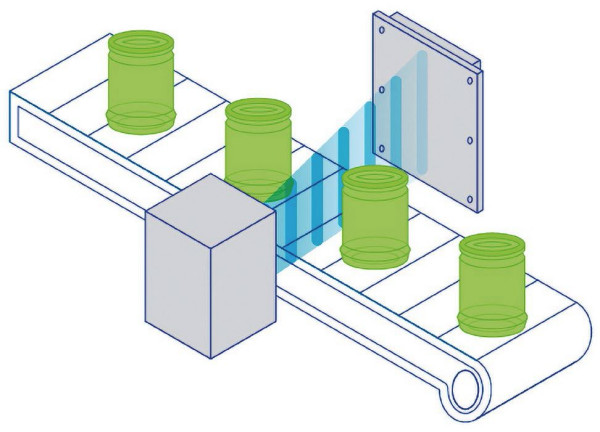
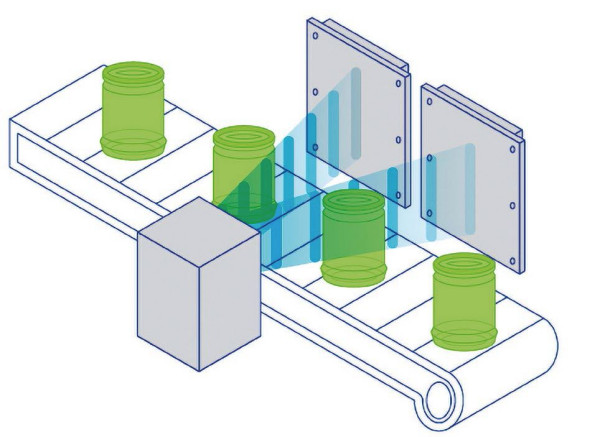
Wybierając taki sprzęt, należy sprawdzić, czy typ opakowań i ich zamknięć, do których nakłuwacze zostały przystosowane odpowiada tym, w które będą pakowane sprawdzane napoje. Warto również zwrócić uwagę na dodatkowe rozwiązania, które usprawniają korzystanie z urządzenia. Przydatne jest na przykład wskazanie miejsca do ustawienia opakowania za pomocą wyświetlanej laserowo siatki znaczników.
Oprócz kontroli jakości offline przeprowadza się też pomiary inline. Realizuje się je zazwyczaj w ramach zautomatyzowanych stanowisk analiz napojów, o które uzupełnia się linie ich rozlewania. Takie rozwiązanie ma ważną zaletę - pozwala uniknąć strat surowców, gdyż w razie wystąpienia odchyleń jakości produktów od przyjętego standardu można szybko zareagować, wprowadzając poprawki w ustawieniach maszyn albo usuwając inne przyczyny problemu.
CZĘŚĆ 2. PAKOWANIE NAPOJÓW
W branży napojowej korzysta się z opakowań różnego typu. Najpopularniejsze są: butelki szklane, opakowania PET, puszki aluminiowe i kartonowe pudełka. W przypadku pierwszych używa się nie tylko nowo wyprodukowanych, ale i pozyskanych ze zwrotów. W butelki PET producenci napojów zaopatrują się u zewnętrznych dostawców lub wytwarzają je na miejscu w zakładzie rozlewniczym, w ramach produkcji własnej.
Drugie rozwiązanie jest tym bardziej opłacalne, im większy jest popyt zakładu na takie opakowania, zwłaszcza jeżeli koszty ich transportu są duże. Oprócz tego pozwala uniezależnić się od ograniczeń wydajności zewnętrznych dostawców oraz zapewnia większą elastyczność w zakresie zmiany cech opakowań (kształtu, pojemności) odpowiednio do aktualnej wydajności produkcji, bieżących zamówień, trendów na rynku albo innych czynników.
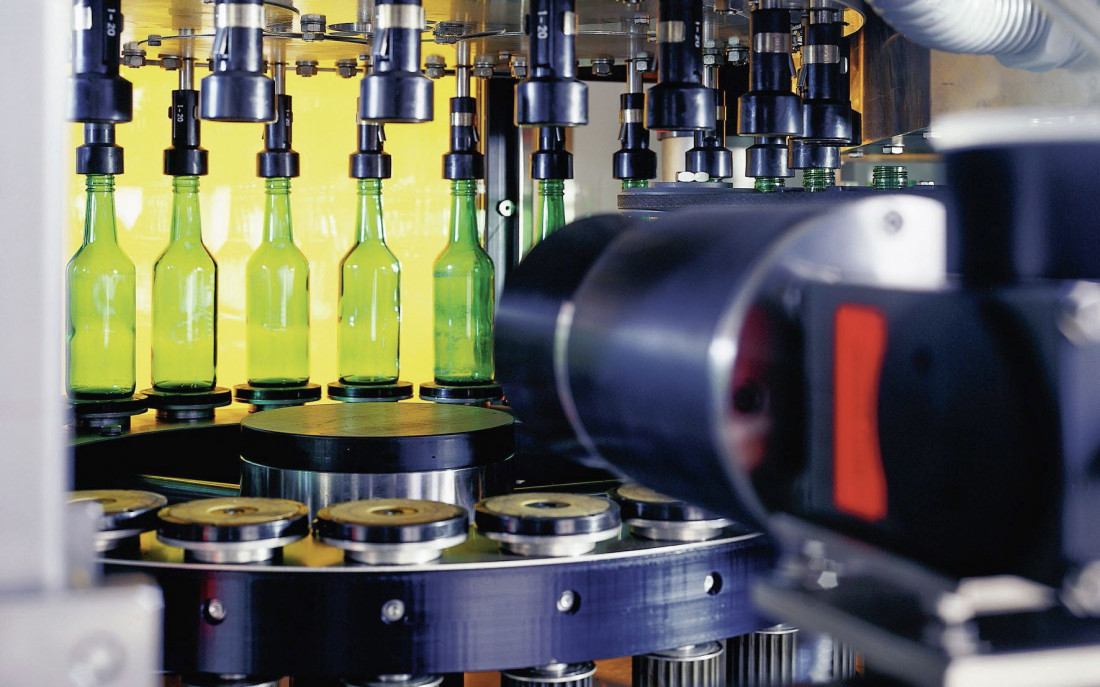
Butelki szklane i PET wymagają umycia i/albo przedmuchania powietrzem. Pudełka tekturowe natomiast trzeba złożyć i skleić. Przed napełnieniem opakowania poddawane są kontroli jakości. Następnie transportuje się je do maszyn napełniających. Po rozlaniu napojów opakowania należy zamknąć, nakładając koronkowe kapsle lub aluminiowe gwintowane pokrywki na butelki szklane, plastikowe nakrętki na butelki PET i zgrzewając pudełka tekturowe. Na opakowania nakleja się etykiety i/lub nadrukowuje oznaczenia. Szczelność zamknięć i czytelność opisów są kontrolowane. Następnie napoje zapakowane jednostkowo pakuje się zbiorczo, na przykład owijając po kilka sztuk folią termokurczliwą albo wkładając do skrzynek.
Linie pakowania napojów stanowią zatem nagromadzenie maszyn specjalistycznych, często w postaci bloków integrujących na przykład płuczkę, nalewarką i zakręcarkę, oraz systemów kontroli jakości. Dalej przedstawiamy wybrane z nich.
PŁUCZKI - PRZEGLĄD MEDIÓW CZYSZCZĄCYCH
W przemyśle napojowym mycie opakowań przed ich napełnieniem jest etapem obowiązkowym. Zapobiega się w ten sposób przeniknięciu do produktu zanieczyszczeń, które mogłyby zagrozić zdrowiu osób go spożywających, a nawet jeżeli okazałyby się dla nich nieszkodliwe, ale byłyby widoczne wprost albo miały wpływ na wygląd, smak, zapach napoju - na przykład odbarwiając albo rozcieńczając go, zniechęcałyby do zakupu i wpływały negatywnie na reputację producenta. Kurz, okruchy, zarazki osadzają się i gromadzą w opakowaniach w czasie ich produkcji, transportu oraz magazynowania.
Projektując ten segment linii rozlewniczej, trzeba zdecydować o rodzaju płuczki i formie czynnika czyszczącego, gazowej lub płynnej. Drugim może być woda, woda z dodatkiem środka myjącego / odkażającego albo sam produkt, o ile korzyści z tego wynikające (pewność, że wyrób końcowy nie zostanie zanieczyszczony) przewyższają wady tego rozwiązania (strata produktu). Gazowe medium to powietrze.
Przedmuchiwanie powietrzem w porównaniu z płukaniem cieczą generuje mniej odpadów, które trzeba usunąć. W obu metodach są to zanieczyszczenia nagromadzone w opakowaniach, lecz w drugim przypadku dodatkowo wraz z nimi trzeba się pozbyć płynnego czynnika myjącego, gdy płuczka pracuje w obiegu otwartym, albo, jeżeli jest zamknięty, oczyścić go przed ponownym użyciem.
Oprócz tego powietrze wydmuchując zabrudzenia, nie pozostawia śladów. W razie niedokładnego opłukania na ściankach opakowania może natomiast zgromadzić się osad z mieszaniny brudu z czynnikiem czyszczącym albo jego płynne resztki wymieszają się z właściwą zawartością butelki.
Realizowane projekty coraz częściej bazują na wykorzystaniu chmur obliczeniowych i możliwości analityki predykcyjnej
|
JAK SIĘ CZYŚCI NIETYPOWE OPAKOWANIA?
Czasem jednak przedmuchanie nie wystarczy i płukanie jest konieczne, na przykład w przypadku opakowań ze zwrotów, które muszą być dokładne umyte i odkażone. Płukanie może być również wymagane, jeśli w procesie produkcyjnym butelki na ściankach osadzają się zabrudzenia, których sam przedmuch nie usunie. Biorąc pod uwagę zalety oraz ograniczenia obu metod, w trudniejszych przypadkach warto rozważyć ich połączenie, czyli przedmuch resztek po płukaniu.
Jeżeli chodzi o rodzaj płuczki, popularne są maszyny, których częścią jest chwytak podnoszący butelkę i odwracający ją do góry dnem. Jej wnętrze jest wtedy opłukiwane lub przedmuchiwane. Metoda ta nie sprawdza się w przypadku opakowań dużych, ciężkich lub o nietypowym kształcie, które trudno jest podnieść lub którymi manipulowanie grozi ich uszkodzeniem.
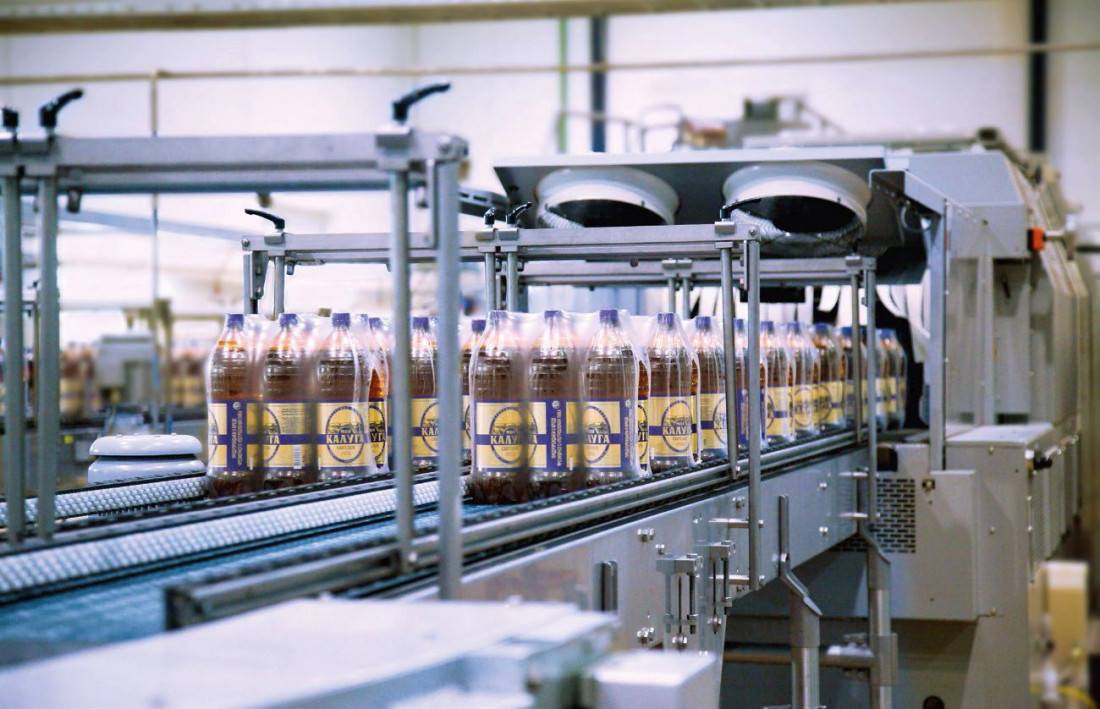
Rozwiązaniem są maszyny, których częścią jest specjalna dysza. Bez odwracania butelek zostaje ona wprowadzona do ich wnętrza. Dysza jest rozmiarem dopasowana do otworu wlotowego, tak aby go uszczelniała. Do środka butelki jest przez nią wdmuchiwane powietrze w celu oderwania zabrudzeń przyklejonych do ścianek, które następnie są zasysane do zbiornika zintegrowanego z dyszą.
Ze względów estetycznych konieczne bywa też usunięcie resztek produktu oraz innych zabrudzeń, które osadzają się na ściankach opakowań od zewnątrz w czasie ich napełnienia. W tym celu mogą być opłukiwane albo przedmuchiwane po zamknięciu.
NAPEŁNIARKI
Centralnym punktem linii pakowania jest maszyna napełniająca butelki. Rodzaj nalewarki zależy od specyfiki rozlewanego płynu, głównie jego lepkości. W nalewaniu piwa, win oraz soków popularne są nalewarki ciśnieniowo-przelewowe, sprawdzające się w dozowaniu głównie płynów o małej lepkości. Ich zaletą jest poza tym duża szybkość napełniania. Ten typ nalewarki nie nadaje się natomiast do dozowaniu gęstych płynów, na przykład miodu. W takim przypadku lepiej użyć napełniarki tłokowej.
Ważne jest również to, czy dozowany napój jest gazowany. Jeżeli tak, linię butelkowania powinno się wyposażyć w nalewarkę przeciwciśnieniową. Maszyna ta przed napełnieniem butelki usuwa z niej powietrze. Dzięki temu w czasie butelkowania nie zmienia się stopień nagazowania napoju.
Oprócz specyfiki produktu na wybór nalewarki wpływa to, czy wszystkie opakowania mają być zapełniane do jednakowego poziomu, czy taką samą ilością napoju. Wbrew pozorom nie jest to jednoznaczne.
NALEWARKI OBJĘTOŚCIOWE
Kilka typów maszyn można wykorzystać do napełniania objętościowego. Przykładem są nalewarki grawitacyjne. W maszynach tego rodzaju napój jest przechowywany w zbiorniku nad dyszami, a do jego nalewania do butelek wykorzystywana jest siła grawitacji. Urządzenia grawitacyjne nadają się do rozlewu cieczy swobodnie płynących, o stałej lepkości, bez cząstek, które mogłyby hamować jej przepływ. Kolejnymi przykładami nalewarek objętościowych są wymienione wcześniej napełniarki tłokowe i z pompą. W obu przypadkach przepływ cieczy jest wymuszony, dzięki czemu sprawdzają się w dozowaniu płynów o większej lepkości.
Mimo że w napełnianiu objętościowym każdy pojemnik jest wypełniony taką samą ilością napoju, jego poziom bywa w nich inny. Wynika to stąd, że chociaż nie jest to widoczne, poszczególne opakowania mogą się minimalnie różnić pojemnością. Powodują to tolerancje ich wymiarów i niedokładności wykonania. Jeśli butelki są przezroczyste, różne poziomy ich zapełnienia mogą wpływać na wybór konsumenta, dla niektórych może to bowiem oznaczać, że producent chce ich oszukać.
JAK DZIAŁA NALEWARKA PRZELEWOWA?
Nalewarki przelewowe zaliczane są do kategorii maszyn napełniających wszystkie opakowania do jednakowego poziomu. Urządzenia tego typu są wyposażone w specjalną dyszą, przez którą płyn wpływa do butelki, a gdy przekroczy zadany poziom jego nadmiar jest zwracany do zbiornika.
Zapewnienie takiego samego poziomu napoju jest z jednej strony wizerunkowo opłacalne, ponieważ klient, nie musząc przebierać między butelkami na półce, nie będzie podejrzewał producenta o oszustwo. Z drugiej jednak strony utrzymanie jednakowego poziomu, jeżeli opakowania znacząco różnią się pojemnościami, może się wiązać ze stratami produktu na „dolewki”, których nie sposób wliczyć w cenę podawaną dla ilości zadeklarowanej na etykiecie, a nie rzeczywistej.
Warto na koniec wspomnieć o ważnej zalecie nalewarek przelewowych wynikającej z ich konstrukcji, dzięki której rozwiązanie pewnego problemu nie wymaga stosowania środków dodatkowych. Chodzi o pienienie się produktu. Jeśli w czasie nalewania piana zgromadzi się w nadmiernej ilości, po jej opadnięciu widoczny poziom zapełnienia opakowania się obniży. W przypadku nalewarek przelewowych wystarczy trochę przedłużyć czas nalewania płynu, żeby sam wyparł on pianę z butelki.
KONTROLA JAKOŚCI SZKLANYCH OPAKOWAŃ
Kontroli jakości poddawane są również opakowania z napojami. Monitorowane są na przykład: szczelność zamknięcia oraz poziom napełnienia. Oprócz tego muszą być sprawdzane pod kątem obecności zanieczyszczeń. Jednym z trudniejszych zadań w tym zakresie jest wykrycie szklanych drobin w szklanych opakowaniach. Na ciała obce tego typu konsumenci są szczególnie wyczuleni z powodu poważnego zagrożenia dla zdrowia, jakie szkło stanowi w razie jego połknięcia.
W przypadku przeoczenia, jeżeli już po wprowadzeniu napoju do sprzedaży ktoś znajdzie w nim szklane drobiny albo ucierpi z powodu ich spożycia, producent powinien się liczyć z poważnymi konsekwencjami, w tym stratami w wyniku wycofania feralnej partii ze sprzedaży, wypłatami odszkodowań poszkodowanym oraz utratą dobrej reputacji.
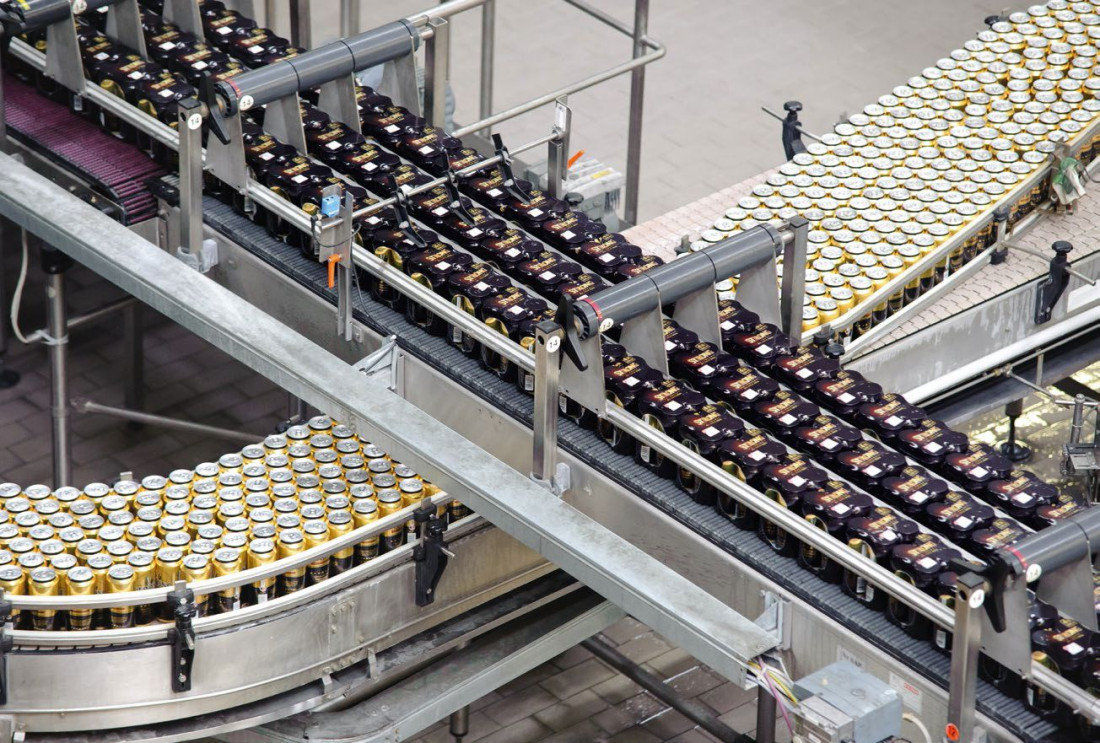
Zanieczyszczenia napoju szkłem niestety nie można wykluczyć nawet w obrębie najnowocześniejszych linii rozlewniczych z powodu specyfiki tego materiału, który łatwo pęka, odpryskuje i kruszy się na przykład pod wpływem wibracji przenośnika, uderzenia głowicy napełniającej w szyjkę butelki albo zbyt mocnego zakręcenia nakrętki.
W kontroli jakości pod kątem obecności tego typu zanieczyszczeń spopularyzowały się systemy inspekcji rentgenowskiej. Wykrycie szkła tą metodą nie jest niestety łatwym zadaniem z kilku powodów, co wyjaśniamy w ramce. Dalej przedstawiamy przykładowe konfiguracje systemów kontroli jakości RTG.
KONFIGURACJE SYSTEMÓW INSPEKCJI
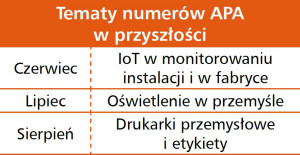
W inspekcji rentgenowskiej butelek ze szkła pod kątem występowania szklanych zanieczyszczeń dobrze sprawdza się układ jak na rysunku 1, ze źródłem i detektorem promieniowania umieszczonymi po przeciwnych stronach przenośnika, którym transportowane są opakowania. Zwykle lepsze efekty uzyskuje się w przypadku butelek wyższych, niż szerszych. W tego typu konfiguracji niezauważone mogą jednak pozostać drobiny przy dnie i te pod wieczkiem.
Większą dokładność zapewnia układ jak na rysunku 2, składający się z jednego źródła emitującego dwa promienie pod kątem i dwóch detektorów je odbierających. W rezultacie każde opakowania zostaje prześwietlone dwukrotnie. Uzyskane w taki sposób obrazy rentgenowskie ukazują daną butelkę z różnych stron, dzięki czemu prawdopodobieństwo wykrycia niepożądanych szklanych drobin jest większe. Jeszcze lepsze wyniki można uzyskać, korzystając z kombinacji układów z rysunku 1 i 2.
Monika Jaworowska