Narażenia mechaniczne
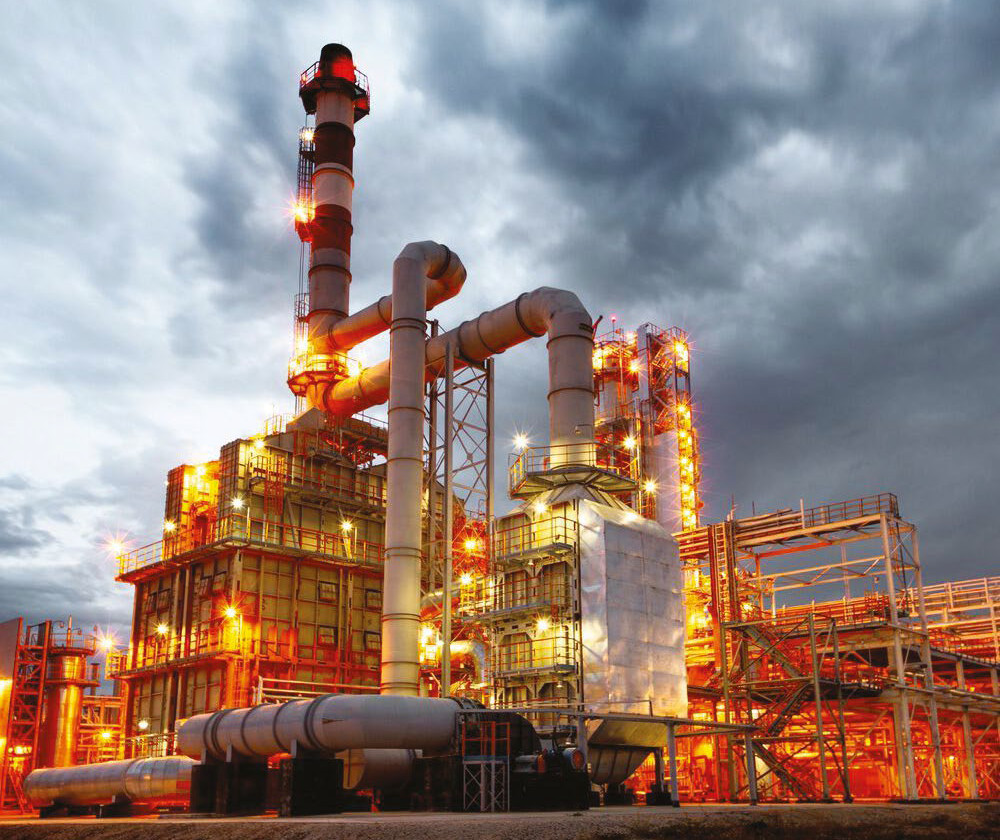
Jak chronić sprzęt przed wibracjami i uderzeniami?
Wyposażenie maszyn i pojazdów specjalnych używanych m.in. w rolnictwie, budownictwie, górnictwie oraz transporcie, na przykład w pociągach, powinno być również odporne na silne uderzenia oraz wibracje. Są one zwykle przenoszone z układu napędowego lub są następstwem kontaktu z przeszkodami terenowymi, w normalnych warunkach pracy tego rodzaju maszyn oraz pojazdów nie można ich zatem uniknąć.
Odporność na wibracje oraz udary mechaniczne uzyskuje się przez zabezpieczenie elementów na nie narażonych z wykorzystaniem izolatorów i tłumików drgań. Są to komponenty mechaniczne. Przykładem są konstrukcje sprężynowe. Zwykle są zbudowane z dwóch płytek, między którymi zamocowana jest sprężyna. Wykonuje się je z różnych materiałów, najczęściej ze stali węglowej, stali nierdzewnej i aluminium. Poza tym w konstrukcji maszyn i pojazdów narażonych na silne drgania i udary dąży się do wyeliminowania podzespołów najbardziej na nie wrażliwych, na przykład zastępując wentylatory radiatorami. Takie podejście stosuje się też m.in. w enkoderach optycznych w wykonaniu heavy duty, w których w zastępstwie szklanej tarczy z podziałką umieszcza się dysk metalowy albo wykonany z tworzywa sztucznego.
Monika Jaworowska