Przegląd mechanizmów znakowania laserem
Stosuje się też technikę, w której materiał jest usuwany tak, by powstałe wgłębienie kontrastowało z otoczeniem ze względu na zmianę sposobu, w jaki odbija światło. Głębokość znaków zazwyczaj nie przekracza 0,01 mm. Jest to jedna z szybszych metod znakowania laserowego.
Parametry wiązki laserowej można także tak dobrać, aby częściowo albo całkowicie usunąć jedną lub większą liczbę warstw powłoki, odsłaniając materiał podłoża, który różni się od niej kolorem. Metoda ta pozwala na znakowanie dowolnego materiału.
W przypadku tworzyw sztucznych popularna jest z kolei technika, w której lokalnie podgrzewa się je do temperatury topnienia. Powoduje to pojawienie się pęcherzyków gazu spieniających materiał. Po zastygnięciu piana jest jaśniejsza lub ciemniejsza od otoczenia, w zależności od tego, czy takiej obróbce został poddany, odpowiednio, ciemny czy jasny plastik. Żeby zwiększyć kontrast, stosuje się specjalne dodatki. Oznaczenia wykonane tą metodą są trwałe, ale nieodporne na zarysowania. Są też wyczuwalne dotykowo.
Kontrola jakości i odczyt etykietParadoksalnie automatyzacja, dzięki której linie produkcyjnie pracują szybciej i efektywniej, co korzystnie wpływa na wydajność i koszt produkcji, sprawia, że łatwiej o błędy w oznaczeniach, przy dużej prędkości bowiem personel nie jest w stanie wzrokowo wychwycić błędów i może dochodzić do powielanie tych zawczasu niezauważonych. Błędom etykietowania sprzyja też różnorodność asortymentu wyrobów produkowanych w obrębie danej linii – raczej niewiele ciągów technologicznych jest już obecnie przeznaczonych wyłącznie do jednego typu produktu. Błędy i niska jakość etykiet to duży problem – tak oznakowane produkty trzeba bowiem etykietować na nowo, przerabiać albo przeznaczyć na straty. Jeszcze poważniejsze są skutki wprowadzenia ich na rynek. Ich późniejsze wycofanie z niego to bowiem nie tylko strata dla producenta w związku z koniecznością oddania pieniędzy klientom, ale także uszczerbek na wizerunku, którego realny koszt potem odczuwa on latami. Aby do tego nie dopuścić, na liniach produkcyjnych wdrażane są zautomatyzowane systemy kontroli jakości etykiet oparte na systemach wizyjnych, które współpracują z systemami odrzucania wybrakowanych wyrobów. Ich standardowa funkcjonalność obejmuje:
Systemy wizyjne są również wykorzystywane w odczycie etykiet. Projektując je pod kątem takiej aplikacji, na wstępie często można stanąć przed dylematem, czy zacząć od opracowania algorytmu, czy raczej od skompletowania systemu wizyjnego. Są one bowiem od siebie wzajemnie zależne – potrzeby pierwszego determinują wymagania stawiane drugiemu, zaś od jakości obrazu zależy skuteczność algorytmu. Dlatego najlepiej pracować nad nimi równolegle, co można osiągnąć w podejściu iteracyjnym. W takim przypadku trzeba odnosić do siebie i aktualizować parametry obu składowych, sprzętowej oraz programowej. Przykładem takiego jest rozdzielczość przestrzenna, określająca rozmiar najmniejszego szczegółu możliwego do rozróżnienia na obrazie. Wpływa na nią m.in. częstotliwość próbkowania. Ta zależy od powiększenia układu optycznego, dlatego zmienia się razem z odległością od obiektu. Niewystarczająca częstotliwość próbkowania utrudnia rozróżnianie detali na obrazie i powoduje zniekształcenia z powodu aliasingu. By ją odpowiednio dobrać, znać trzeba: rozmiar fizyczny szczegółów, które powinny być rozpoznawalne, maksymalną odległość od obiektu inspekcji, wymaganą liczbę pikseli. Często na wstępnym etapie projektowania nie wszystkie dane są dostępne, szczególnie jeżeli będą implementowane zaawansowane algorytmy, na przykład techniki AI. Dlatego na początku warto częstotliwość próbkowania zawyżyć, a potem eksperymentując z algorytmem przetwarzania obrazu, ustalić jej minimalną wymaganą wartość. Wracając do części sprzętowej systemu – minimalna częstotliwość próbkowania determinuje: liczbę pikseli przetwornika obrazu, rozmiar piksela przetwornika obrazu i ogniskową obiektywu. |
Laserowe znakowanie szkła, stali, aluminium
W przypadku szkła stosuje się metodę, w której miejscowo absorbowana wiązka promieniowania powoduje powstawanie pod powierzchnią mikropęknięć. Te, ze względu na liczne wewnętrzne odbicia światła, wydają się jaśniejsze. Technika ta pozwala na wykonywanie dwu- i trójwymiarowych, tworzonych kropka po kropce, symboli wewnątrz szkła.
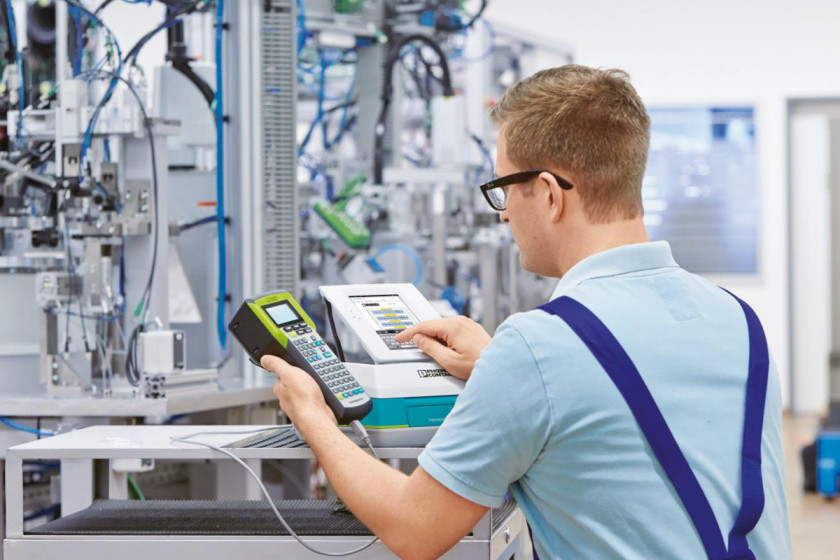
W przypadku takich materiałów jak stal nierdzewna czy tytan stosuje się także zmodyfikowaną metodę wyżarzania. Polega ona na zmienianiu parametrów znakowania w taki sposób, aby w wyniku utleniania w zagłębieniach symboli tworzyły się powłoki tlenkowe, które różnią się kolorami. W tym celu regulowane są: średnica wiązki, moc lasera, prędkość oraz kierunek znakowania, częstotliwość i czas trwania impulsów laserowych.
Podobnie w przypadku anodowanego aluminium, odpowiednio dobierając parametry pracy lasera, można selektywnie, do określonej głębokości, usuwać fragmenty powłoki tlenkowej. Technika ta jest popularna w znakowaniu urządzeń mobilnych w obudowach z tego materiału. Symbole w ten sposób wykonane charakteryzują się dużym kontrastem i wysoką jakością wizualną i dotykową.
Thomas Spranzel
Turck
W przemyśle przeważnie wykorzystywane są kody kreskowe i 2D oraz znaczniki RFID. Kody kreskowe są najbardziej rozpowszechnioną metodą znakowania, głównie ze względu na niski koszt wprowadzenia takiego rozwiązania. Rozwiązanie oparte o kody kreskowe i 2D niesie jednak ze sobą ograniczenia w postaci ilości danych jakie mogą być przekazywane, łatwość kopiowania, problem z odczytem w wyniku wystąpienia zabrudzenia. Systemy RFID umożliwiają przechowywanie większej ilości danych, są odporne na zabrudzenia, a nawet pozwalaj na zmianę danych zawartych w nośniku. Kolejną ważną zaletą systemów RFID jest zasięg, który dla odpowiednich systemów liczony może być w metrach, a dodatkowo ułożenie znakowanego elementu nie musi być ściśle określone jak w przypadku kodów kreskowych i 2D. Aplikacje, w których znakowane przedmioty nie są bardzo wartościowe i dodatkowo w procesie nie występują trudne warunki atmosferyczne sugerują zastosowanie kodów, jeżeli natomiast ważna jest możliwość pracy w trudnych warunkach, pewność odczytu na najwyższym poziomie oraz wymiana dużej ilości danych to systemy RFID nie mają sobie równych. Ważnym punktem pozwalającym na podjęcie odpowiedniej decyzji odnośnie metody znakowania ma także obieg znacznika. Jeżeli elementy nie wyjeżdżają poza jednostkę czyli znajdują się w obiegu zamkniętym to bardzo dobrym rozwiązaniem są nośniki danych zamknięte w plastikowych obudowach, jeżeli jednak znakowany towar wyjeżdża poza jednostkę i więcej do niej nie wraca, to kody kreskowe bardzo często okazują się najbardziej optymalnym rozwiązaniem. Dla nośników danych RFID podaje się praktycznie nieograniczoną liczbę operacji odczytu i około 100 tys. operacji zapisu. Czasy zapisu i odczytu mogą różnić się w zależności od rozwiązania oraz ilości wymienianych danych, jeżeli przyjmiemy za odnośnik kod kreskowy to sam odczyt podobnej ilości danych z RFID trwa milisekundy. Wybór odpowiedniej metody znakowania zależy zatem od wielu czynników, należy jednak pamiętać, że w ramach jednej aplikacji metody mogą być ze sobą mieszane. |
Czy warto wybrać znakowarkę laserową?
Znakowanie laserowe jest popularnym sposobem nanoszenia oznaczeń, w wielu przypadkach preferowanym ze względu na jego liczne zalety w porównaniu z metodami konkurencyjnymi. Przede wszystkim symbole wykonane tą techniką są trwałe i odporne na czynniki niszczące, na przykład: ścieranie, wodę, rozpuszczalniki, olej, temperaturę, promieniowanie UV. Dzięki temu trudno jest je zmodyfikować i usunąć, co stanowi samoistne zabezpieczenie przed fałszowaniem.
Trwałość oraz duży kontrast oznaczeń zapewniają też ich długotrwałą czytelność. Laserem można nanosić grafiki, logo i czcionki wysokiej rozdzielczości, jak również kody kreskowe 1D i 2D. Jest to metoda elastyczna – przestawienie znakowarki na inny rodzaj symbolu nie jest skomplikowane (polega zwykle na jego edycji w programie sterującym maszyną), szybka, bezkontaktowa (mało niszcząca) i uniwersalna – lasery znakują różne materiały. Ponieważ nie są stosowane płynne czynniki (farby, tusze, kwasy, rozpuszczalniki), nie trzeba czekać, aż znakowane przedmioty wyschną. Sam proces jest niebrudzący. Ze względu na brak chemikaliów jest przyjaźniejszy środowisku. Pozwala to także zaoszczędzić na materiałach eksploatacyjnych. Ponadto nie są wymagane dodatkowe czynności, jak czyszczenie, wymiana i ostrzenie narzędzi tnących.