Jak dobrać serwowzmacniacz?
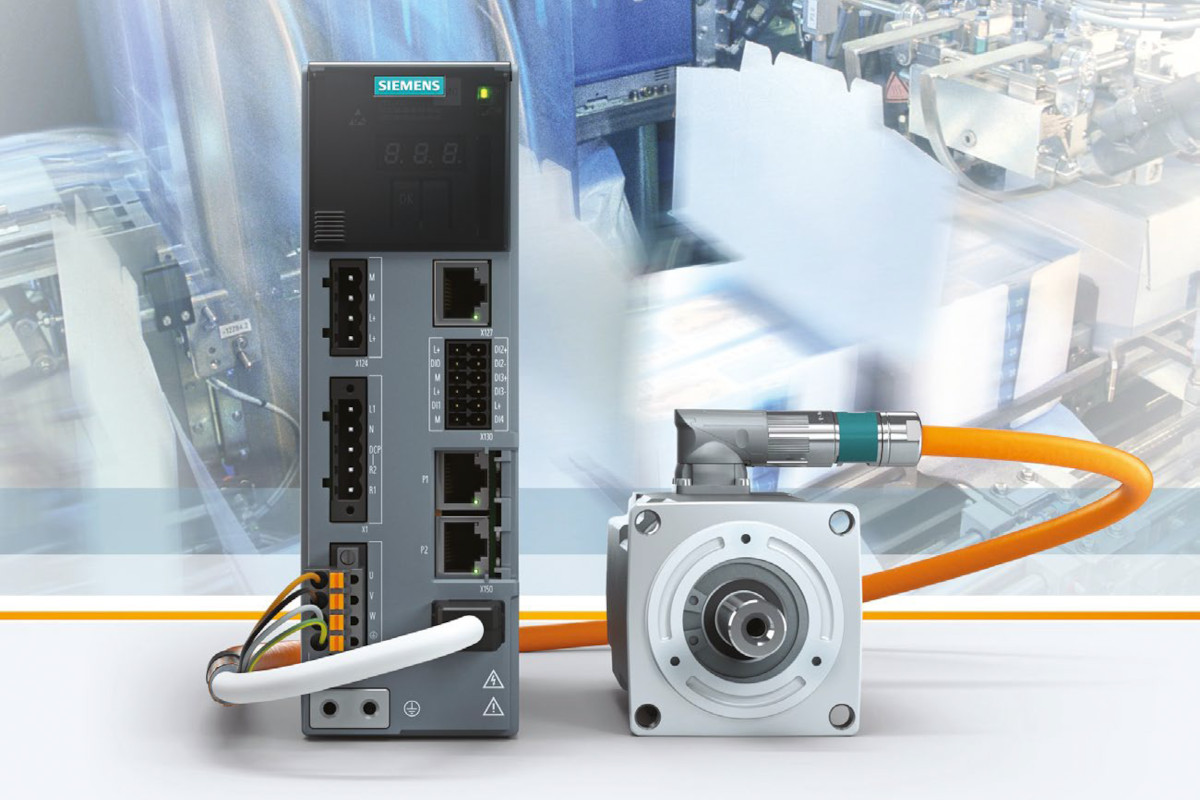
Serwowzmacniacz odpowiada za wysterowanie silnika na podstawie sygnału ze sterownika. Z pozoru może się wydawać, że jego wybór polega tylko na dopasowaniu prądu i napięcia wyjściowego do wymogów silnika – moc serwowzmacniacza (maksymalne napięcie, prąd ciągły oraz prąd szczytowy) powinna być wystarczająca do wytworzenia potrzebnej mocy mechanicznej (momentu obrotowego, prędkości). Nie jest to prawdą, gdyż żeby wybrany serwowzmacniacz spełnił swoją funkcję, trzeba dodatkowo przeanalizować kilka kwestii. Niektóre zastosowania mogą wymagać specjalnych opcji, zasadniczo jednak pod uwagę powinno się wziąć poniższe cechy.
Taką jest rodzaj komutacji – na jej wybór ma wpływ typ silnika oraz dopuszczalne w danym zastosowaniu tętnienia momentu. W bezszczotkowych silnikach prądu stałego jest to jedna z dwóch technik: sześciostopniowa albo sinusoidalna, a w silnikach synchronicznych AC sinusoidalna. W pierwszej klucze tranzystorowe przełączające prąd do uzwojeń silnika są sterowane przebiegami prostokątnymi, a w drugiej sinusoidalnym. Zaleta komutacji sześciostopniowej to łatwość realizacji, zaś wady to: mniejsza dokładność sterowania i większe pulsacje momentu obrotowego, szczególnie przy małej prędkości. Komutacja sinusoidalna z kolei praktycznie eliminuje tętnienia momentu obrotowego i zapewnia dokładniejszą kontrolę. Jest jednak bardziej skomplikowana w realizacji.
Można też wybierać między serwowzmacniaczami analogowymi i cyfrowymi. Zaleta pierwszych to łatwiejsza instalacja, ale niestety wymagają ręcznego dostrajania. Za modelami cyfrowymi z kolei przemawia większa funkcjonalność (dostrajanie programowe, diagnostyka wewnętrzna, sterowanie nie tylko momentem obrotowym i prędkością, jak w wersjach analogowych, ale i położeniem). Ważne kwestie to ponadto też: kompatybilność serwowzmacniacza z sygnałem pętli sprzężenia zwrotnego, interfejsy komunikacyjne, zintegrowane funkcje bezpieczeństwa.
Serwonapędy w praktyce: rozwiązywanie problemówoJednym z najczęstszych problemów w sterowaniu ruchem jest głośna praca jednej z osi. Jest to uciążliwe, ale może też skutkować skróceniem żywotności komponentów serwonapędu. Hałas może mieć kilka przyczyn. Taką w regulatorach PID jest za duża wartość wzmocnienia członu różniczkującego, która powoduje głośne drgania silnika. Pomóc może jego zmniejszenie, o ile nie pogorszy to skuteczności pętli sterowania. Powodem bywa również przestrojona pętla prądowa i zbyt duża częstotliwość próbkowania. Hałasować mogą także bezszczotkowe silniki prądu stałego z komutacją sześciostopniową – ciszej pracują przy komutacji sinusoidalnej. Powodem uciążliwych dźwięków bywają poza tym niedobrane komponenty mechaniczne. Jeśli z kolei serwowzmacniacz albo/i silnik się przegrzewają, warto rozważyć doinstalowanie dodatkowych cewek indukcyjnych, które zmniejszą tętnienia prądu, podobnie jak zwiększenie częstotliwości przełączania i obniżenie napięcia zasilania silnika. Trzeba też zdiagnozować problemy z komutacją. Nadmierne wibracje z kolei mogą być skutkiem niedobranego profilu ruchu – na przykład można rozważyć zmianę na profil, w którym przyspieszanie i hamowanie będą realizowane płynniej. W razie problemów z enkoderami można: skorzystać z interfejsów komunikacyjnych z różnicową transmisją danych, zastosować filtr sygnałowy, sprawdzić ekranowanie przewodów i odseparować kable z silnika do serwowzmacniacza od tych z enkodera, sprawdzić, czy napięcie zasilania enkodera nie jest za niskie. Jeżeli dane zastosowanie wymaga płynniejszego ruchu także przy małej prędkości, można: wymienić enkoder na model o większej rozdzielczości, zmniejszyć częstotliwość próbkowania, rozważyć zastosowanie kontrolera z pętlą fazową. |
Resolwer czy enkoder?
Serwonapędy pracują w zamkniętej pętli sterowania ze sprzężeniem zwrotnym. Wymagany jest w związku z tym element pomiarowy mierzący wartość danej wielkości, która będzie porównywana z wartością zadaną w celu obliczenia błędu i wyznaczenia na jego podstawie sygnału sterującego. Najpopularniejsze są przetworniki kąta obrotu, resolwery i enkodery. Oba typy mierzą położenie kątowe wału silnika, przekształcając jego ruch w sygnał elektryczny.
Resolwery mają dłuższą historię – początkowo używane w wojsku, w przemyśle upowszechniły się dzięki wytrzymałej konstrukcji. Są zbudowane z wirnika z uzwojeniem pierwotnym i stojana z uzwojeniami wtórnymi, ustawionymi względem siebie pod kątem 90°. Po zasileniu uzwojeń wirnika w tym stojana można zmierzyć napięcia o wartościach równych iloczynowi napięcia odniesienia przez, odpowiednio, sinus albo kosinus kąta odchylenia wału silnika od położenia referencyjnego. Stosunek tych napięć odpowiada bezwzględnemu położeniu wału.
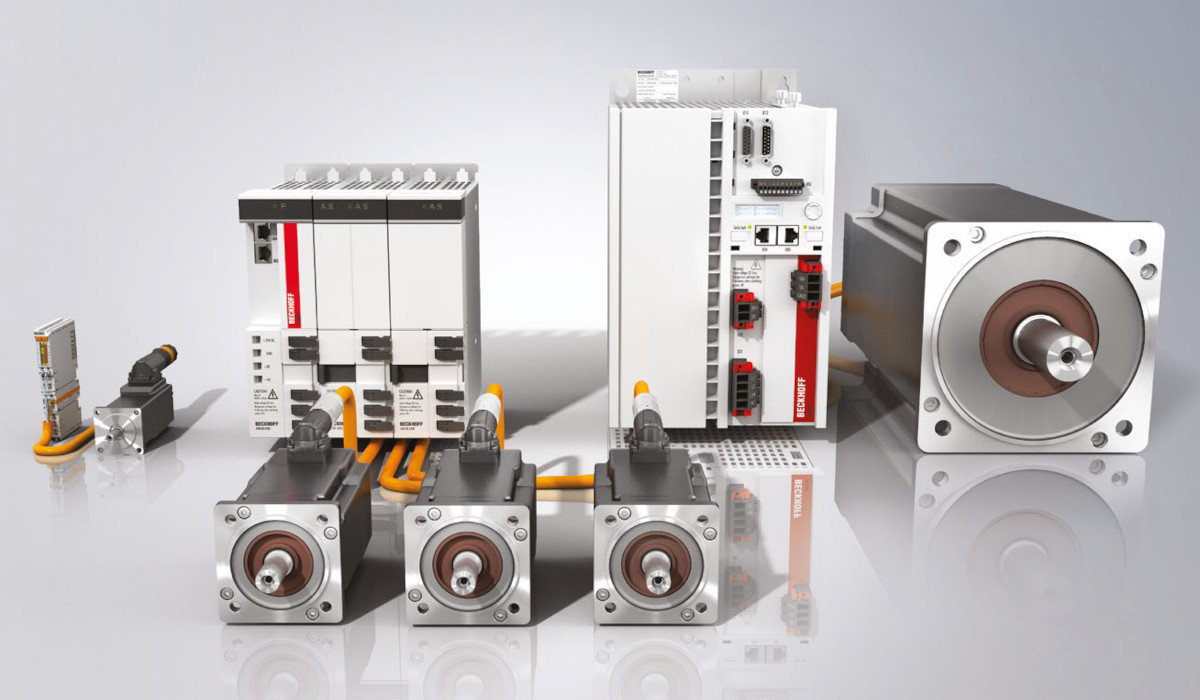
Brak części optycznych i elektronicznych sprawia, że resolwery w porównaniu do enkoderów są odporniejsze na drgania, udary, zaburzenia elektromagnetyczne i wysokie temperatury. Trudność może jednak sprawiać ich integracja z systemem. Nie jest też tania. Pod tym względem enkodery, jako przetworniki cyfrowe, wypadają korzystniej. Ponadto mają mniejszą masę i bezwładność, co sprawia, że lepiej nadają się do zastosowań z dużymi przyspieszeniami.
Wyróżnia je także większa dokładność pomiaru, która w przypadku resolwerów spada przy szybkiej zmianie prędkości. Ponadto przewaga tych ostatnich nad enkoderami pod względem odporności konstrukcji na czynniki otoczenia traci na znaczeniu, ponieważ rośnie dostępność przyrządów optycznych w wersjach heavy-duty.
Bartłomiej Kiełczewski![]() Induprogress
odpW obecnie projektowanych systemach Motion Control możemy zaobserwować całkowite przejście w kierunku układów sieciowych opartych o szybkie sieci komunikacyjne, najczęściej na bazie Ethernetu. Aktualnie kontrolery są w stanie obsługiwać bez większych problemów kilkanaście-kilkadziesiąt napędów serwo w czasie 1 ms. Dąży się więc zatem do całkowitego przesunięcie inteligencji maszyny do sterownika motion, a same napędy traktowane są jako "końcówki ruchu". Oczywiście po stronie serwonapędów muszą pozostać pewne funkcjonalności, jak choćby zaawansowane filtry rezonansowe, autonomiczny autotuning nastaw regulatorów, funkcje safety. Trzeba też pamiętać, że dynamiczny rozwój sieci komunikacyjnych wymusił też rozwój mechanizmów serwo w kierunku wyższych rozdzielczości enkoderów stosowanych w silnikach oraz wyższej częstotliwości taktowania pętli regulacji – znacznie szybszej odpowiedzi układu napędowego (np. 3,1kHz dla napędów ASDA-B3 od Delta Electronics). Same silniki serwo obecnie projektowane mogą uzyskiwać wyższe przeciążalności oraz prędkości obrotowe niż kilka lat temu przy jednoczesnym zmniejszeniu ich wymiarów.
Przy doborze silnika do układu serwonapędowego ważnym parametrem jest stosunek bezwładności obciążenia sprowadzony do bezwładności własnej samego motoru. Jest on kluczowym parametrem w maszynach wymagających dużej precyzji i bardzo dokładnego nadążania za pozycją zadaną. Tu algorytmy sterowania jakie implementowane są do samych kontrolerów również przeszły rewolucje i ten sam układ mechaniczny może obecnie pracować znacznie precyzyjniej i sztywniej nawet z mniejszym silnikiem (o mniejszej mocy i bezwładności własnej niż poprzednio). Z kolei rozwiązania sieciowe pozwalają też na bardzo prostą konfigurację i monitoring zdalny całości maszyny i zamontowanych osi napędowych. Możemy też budować naszą aplikację modułowo stosując funkcje osi opcjonalnych co jest teraz częstą praktyką wśród dużych producentów maszyn. |