Gdzie korzysta się z serwonapędów?
Na linii transportu wyrobów płaskich o sporym rozmiarze, jak płyty drewniane albo blachy, serwonapędy mogą znaleźć zastosowanie w korygowaniu ich skrzywienia na taśmociągu. W przykładowej realizacji płyty są przenoszone na dwóch taśmach z oddzielnymi napędami. Jeden z nich pełni funkcję nadrzędną względem drugiego. Położenie krawędzi płyt mierzą dwa ustawione naprzeciwlegle czujniki. Na podstawie ich odczytów obliczany jest błąd, charakteryzujący skrzywienie płyty względem położenia prawidłowego, czyli prostopadłego do kierunku biegu taśmociągu. W zależności od wartości odchyłki regulowana jest prędkość napędu podrzędnego, a w rezultacie szybkość przesuwania się taśmy, którą napędza. To sprawia, że skrzywiony bok płyty zostaje wyrównany.
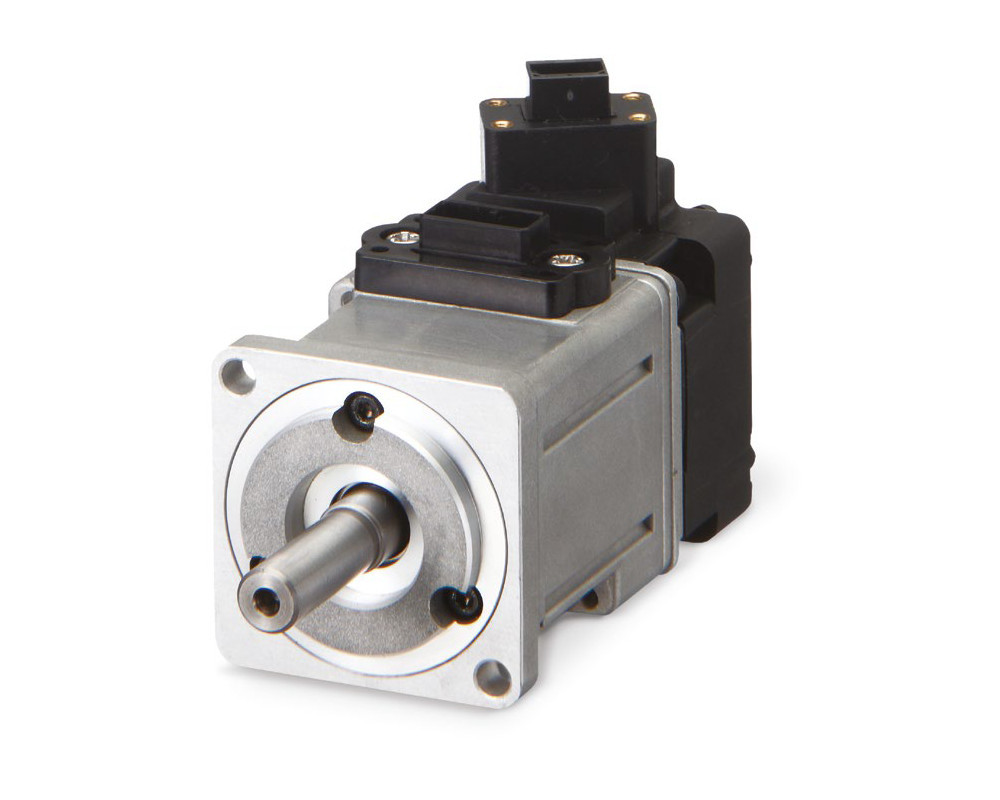
Serwonapędy wykorzystuje się także do korygowania odstępów między produktami, jak pudełka, dostarczanymi na taśmociąg w przypadkowych odległościach od siebie. Przenośnik jest w takim przypadku zwykle podzielony na segmenty: podajnika, regulacyjny i odbiorczy. Czujnik, który jest zainstalowany przy taśmociągu, wykrywając krawędzie pudełek mierzy odległość między nimi. Jeżeli jest inna niż wymagana, sterownik serwonapędu odpowiednio zmienia prędkość przesuwania się segmentu regulacyjnego przenośnika, odsuwając lub przysuwając do siebie kolejne pudełka.
Ważnym zastosowaniem serwonapędów są linie cięcia różnych materiałów. W przykładowej realizacji podajnik wykonuje określoną liczbę obrotów odpowiadającą konkretnej długości materiału i zatrzymuje się. Napęd sterujący gilotyną opuszcza ją. Wówczas podajnik jest uruchamiany ponownie.
Kolejne przykłady to latająca piła i wirujący nóż. Oba rozwiązania umożliwiają cięcie bez konieczności zatrzymywania przenośnika (cięcie w locie). Prędkość pracy ostrza piły musi być w takim przypadku zsynchronizowana z prędkością przemieszczania się taśmociągu. W tym celu ta ostatnia jest mierzona, a wynik pomiaru jest przetwarzany w kontrolerze napędu piły. Po odcięciu fragmentu materiału ostrze jest zatrzymywane i przemieszczane z powrotem do pozycji wyjściowej. Głównym komponentem wirującego noża jest obracający się cylinder, wzdłuż którego zamontowane jest ostrze. Od prędkości, z jaką obraca się nóż, zależy długość odciętego materiału. Im większa jest ta pierwsza, tym krótszy kawałek zostanie ucięty.
Serwonapędy znajdują również zastosowanie w maszynach włókienniczych, drukarskich, do formowania i obrabiania metali, drewna, tworzyw sztucznych, pakowarkach, drukarkach 3D.
Tomasz Szewczyk![]() Sitaniec
Technologia serwonapędów ewoluuje podobnie jak cała automatyka. Możemy zaobserwować przede wszystkim zwiększanie ich wydajności, efektywności, energooszczędność oraz rozwój systemów sterowania. Najnowsze rozwiązania pozwalają na programowanie i obsługę układów wieloosiowych z poziomu PLC, korzystając ze wspólnego środowiska. Znacząco ułatwia to i skraca czas potrzebny na uruchomienie. Zastosowań serwonapędów jest tak wiele, jak wdrożonych aplikacji. Są one z powodzeniem stosowane w nowo produkowanych maszynach, jak również zastępują inne napędy w przypadku maszyn remontowanych. O wyborze rozwiązania prawie zawsze decyduje producent maszyny lub integrator dobierający urządzenia pod daną aplikację.
Serwonapędy z powodzeniem zastępują dotychczas stosowane silniki klatkowe lub synchroniczne, jak również napędy pneumatyczne. Mnogość dostępnych rozwiązań oraz łatwość aplikowania sprawia, że możemy spotkać je dziś nie tylko w miejscach tradycyjnie stosowanych, takich jak pozycjonowanie CNC, ale również na transporterach, sorterach czy w napędach liniowych. Dotychczasowi producenci pneumatyki zachęcają do zastąpienia siłowników znormalizowanymi napędami opartymi na silnikach serwo.
Tak jak niemal we wszystkich dziedzinach, również tu możemy znaleźć dostawców prezentujących określony poziom jakości, możliwości, a co za tym idzie – ceny. Obok producentów europejskich, amerykańskich czy japońskich, oferujących rozbudowane układy Motion, można znaleźć tańsze, alternatywne rozwiązania z Azji. Innym interesującym obszarem są napędy dostarczane przez niezależnych producentów z Europy, których możliwości wystarczają do typowych aplikacji, a mają korzystną cenę. Warto również poszukać wyspecjalizowanych producentów gotowych rozwiązań z wykorzystaniem silników serwo, np. chwytaków, układów kinematycznych, przegubów czy przekładni.
W ostatnich latach zaburzone zostały łańcuchy dostaw elektroniki i nie ominęło to także producentów serwonapędów i systemów Motion Control. W skrajnych przypadkach zawieszona została produkcja niektórych grup produktowych, w innych wydłużyły się terminy. Możemy mieć nadzieję że w 2023 roku terminy zaczną wracać do normalności, chociaż na pewno nie będzie to obserwowalne w najbliższych miesiącach. |
Monika Jaworowska
źródła zdjęć: Siemens