- W tym roku mija osiem lat od momentu połączenia firm Danfoss i Vacon – fińskiego producenta napędów elektrycznych. Jakie są efekty tej zmiany i jak rozszerzyliście ofertę rozwiązań napędowych?
W Danfoss Poland zarządzam działem napędowym, aczkolwiek z firmą Vacon łączą mnie historyczne więzy, bowiem osobiście otwierałem jej polski oddział. Po roku działalności miało miejsce połączenie z Danfossem, w efekcie czego tamtejszy dziesięcioosobowy zespół dołączył do kilkunastoosobowej grupy napędowej w Danfossie, swoją drogą świetnie się z nią zgrywając. Sądzę, że było to wyjątkowo dobrze przygotowane i płynnie wprowadzone połączenie biznesów.
Wcześniej obydwie firmy specjalizowały się w nieco innych obszarach. Danfoss miał kompetencje pozwalające na masową produkcję przetwornic niewielkich mocy. Wprawdzie mieliśmy również urządzenia dużych mocy, ale raczej standardowe, a więc inaczej niż w przypadku Vacona. Ten z kolei był bardzo silny w obszarze dużych napędów przeznaczonych do konkretnych zastosowań. Przykładowo miał modele chłodzone cieczą do zastosowań głównie w przemyśle morskim. Te dwa portfolio bardzo dobrze się uzupełniły, tworząc spójną całość.
Powyższe zmiany przyniosły również zwiększenie naszego know-how i skutkowały wprowadzeniem szeregu nowości. W szczególności dotyczyły one software’u, zagadnień condition based monitoring oraz możliwości nadzoru pracy i analizy całego układu napędowego. Wprowadziliśmy też rozwiązania z obszaru zdalnego monitorowania i kontroli, co pozwala wdrażać zaawansowane usługi serwisowe. Obecnie przygotowujemy nową, wspólną platformę łączącą wymienione technologie, która zostanie zaprezentowana publicznie jesienią.
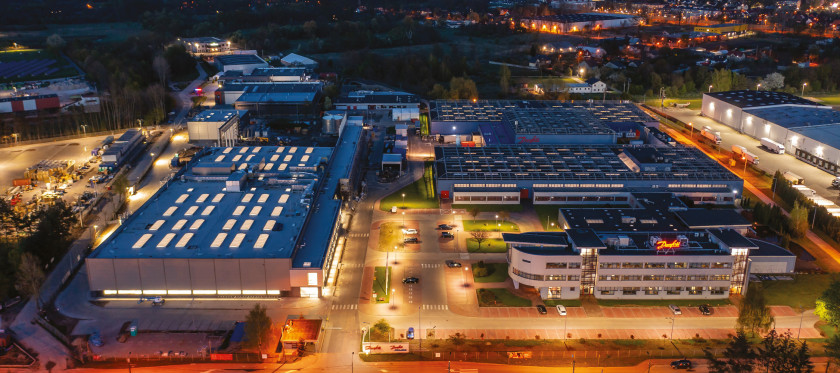
- W jaki sposób działacie w różnych sektorach rynku?
Przede wszystkim pracujemy z polskimi firmami, głównie inżynierskimi, specjalizującymi się w konkretnych sektorach – np. wodnym, spożywczym czy budowy maszyn. Są to przedsiębiorstwa mające bardzo dobrze rozwinięte kompetencje inżynieryjne, aplikacyjne i jednocześnie firmy będące blisko klientów. Dzięki temu mogą one dobrze analizować ich potrzeby i wspierać serwisowo. Tego typu firmy z powodzeniem integrują nasze produkty w większych systemach.
Dodam, że również w kontekście posiadanych partnerów akwizycja Vacona była bezproblemowa. Udało nam się połączyć te grupy pod względem kompetencji, do tego wyłoniliśmy partnerów „Drive Pro”, którzy zapewniają najbardziej zaawansowane usługi inżynierskie i serwisowe.
Naszą rolą, oprócz dostarczania produktów, jest przede wszystkim wspieranie techniczne i kompetencyjne współpracujących z nami firm. W zespole Danfossa istnieje kilkuosobowa grupa specjalizująca się w aplikacjach i pomagająca partnerom we wdrożeniach. Współpracujemy również z centrum aplikacyjnym w Holandii, dodatkowo firma rozważa budowę kolejnego takiego centrum w Europie Centralnej. Kooperujemy także z innymi dostawcami – przykładowo z jednym z największych producentów silników w Polsce automatyzujemy centrum testowania silników. Nie wchodzimy natomiast w projekty jako wykonawca. W wyjątkowych sytuacjach robimy od tego odstępstwa, ale dotyczy to klientów OEM (producentów maszyn), a nie odbiorców końcowych.
- Jak wygląda model współpracy z firmami OEM?
Z większością takich przedsiębiorstw współpracujemy bezpośrednio. Dysponują one kompetencjami inżynierskimi i chcą od nas zaadaptowany do ich potrzeb produkt. Są to zresztą firmy coraz bardziej zaawansowane kompetencyjnie. Dawniej przenosiły one produkcję z zagranicy do Polski, potem pojawiała się u nas coraz większa wartość dodana w postaci projektowania, a dzisiaj ze swoimi produktami i usługami przedsiębiorstwa takie wychodzą poza nasz kraj.
Przykładem może być nasz partner produkujący wciągarki morskie. Dawniej jego polski oddział tylko je montował, zaś cały inżyniering odbywał się w centrali w Norwegii. W tej chwili zatrudnia on wielu inżynierów w Gdańsku, a efekty ich pracy – gotowe produkty – idą na eksport do stoczni w Wietnamie, Korei Południowej czy innych miejsc na świecie. Dodam, że podobny schemat widzę też w przypadku dużych firm integratorskich. Współpracujemy przykładowo z polskimi integratorami, którzy realizują projekty w spalarniach odpadów w Szwecji czy Wielkiej Brytanii. Są to firmy cenione za granicą.
Jakub Czapliński: Niestety uderzyły w nas dosyć mocno, zresztą chyba podobnie jak w wielu innych producentów na rynku. Jako że zachowanie ciągłości dostaw stanowiło dla nas priorytet, firma bardzo szybko podjęła decyzje odnośnie redesignu części wyrobów. Zostały one na nowo zaprojektowane z wykorzystaniem komponentów dostępnych na rynku. Drugim z powiązanych obszarów było zapewnienie ciągłości serwisu, a więc też dostępności części zamiennych z naszych trzech globalnych magazynów. Było to niezbędne z punktu widzenia dotychczasowych klientów, bowiem pozwalało na utrzymanie ciągłości produkcji. Finalnie ostatnie lata przyniosły zmianę optyki, jeżeli chodzi o utrzymanie ruchu. Naszych klientów namawiamy na wdrożenie serwisu prewencyjnego, którego celem jest takie monitorowanie urządzeń oraz systemów, aby nie dopuszczać do sytuacji nagłych uszkodzeń i konieczności natychmiastowego sprowadzania nowych komponentów. |
- Jak wygląda popyt na zaawansowane produkty w przypadku rynku w Polsce i za granicą?
To ciekawe pytanie. Sądzę, że na każdym rynku dominują nieco inne produkty. Pozostając przy polskich OEM-ach, można zauważyć, że firmy te były silne w produkcji maszyn kastomizowanych, wytwarzanych na zamówienie, a więc produkowały ich krótkie serie, ewentualnie wyroby jednostkowe. W Polsce budowano też maszyny w większych seriach, ale raczej najprostsze. Z kolei w zakresie wyrobów zaawansowanych, seryjnych zdecydowanie dominowali Niemcy, Włosi, a nawet Czesi.
Powyższy stan zmienia się. Obserwuję, że coraz więcej firm, które zaczynały od nieskomplikowanych maszyn, przechodzi na wyroby bardziej złożone, zaś ci, którzy produkowali wersje kastomizowane, coraz częściej stawiają na seryjność i produkcję w większych wolumenach. Powoduje to, że rynek maszynowy rozszerza się, w efekcie zmienia się też zapotrzebowanie na komponenty napędowe. Dodatkowo sektor ten rozwijają też firmy zachodnie, które lokalizują u nas swoją produkcję.
- Danfoss Drives to nie tylko przetwornice – dostarczacie produkty o różnych mocach zarówno do systemów tradycyjnych, jak i zdecentralizowanych, a do tego dużą grupę innych urządzeń napędowych.
Rzeczywiście mamy ofertę, która oprócz przetwornic obejmuje serwonapędy, softstarty, układy zintegrowane, filtrujące i wiele innych produktów. Dodatkowo w ubiegłym roku bardzo silnie rozwinęliśmy nasze portfolio przetwornic średniego napięcia. W tym przypadku oferujemy dwie nowe serie – przemienników tradycyjnych V1000 oraz przeznaczonych m.in. do przemysłu morskiego o nazwie Vacon 3000. Są to nowatorskie przetwornice chłodzone cieczą, które są bardzo kompaktowe, złożone ze zintegrowanych, łatwo wymienialnych modułów, zabezpieczonych przed wpływem warunków atmosferycznych i drgań.
Obecnie również przygotowujemy nowe serie produktów niskiego napięcia, o których będziemy szeroko informowali jesienią tego troku. Będą to wersje zarówno podstawowe, jak też zaawansowane funkcjonalnie, przy czym w ich projektowaniu korzystaliśmy z doświadczeń zebranych przy produktach VLT oraz Vacon. Promujemy na rynku rozwiązania takie jak zdalny oraz prewencyjny monitoring. Do tego dochodzą technologie stosowane w magazynach energii, energetyce OZE, a także produkcji zielonego wodoru oraz zielonego amoniaku w przemyśle chemicznym.
- A co z napędami do konkretnych aplikacji – np. do systemów HVAC czy zastosowań wod-kan? W tych obszarach zawsze mieliście produkty specjalizowane…
Tak, dostarczaliśmy i dostarczamy wyroby, które są funkcjonalnie dopasowane do takich aplikacji. Dotyczy to systemów HVAC, wod-kan, ale też branży spożywczej czy morskiej. Ostatni z rynków jest bardzo ciekawy i rozwija się w Polsce dynamicznie, w tym dzięki mniejszym i średniej wielkości firmom. Mamy napędy specjalizowane, które wykorzystywane są m.in. w certyfikowanych systemach oddymiania pożarowego. Mają opcje pracy w trybie fire mode, przy czym w odróżnieniu od innych tego typu wyrobów, również w tym trybie możliwa jest kontrola pracy urządzenia. Pozwala to na kontrolę różnicy ciśnień pomiędzy pomieszczeniami w przypadku wystąpienia pożaru, co jest unikalną funkcjonalnością na rynku.
Ostatnio weszły w życie przepisy, zresztą dla mnie bardzo logiczne, zgodnie z którymi certyfikowane muszą być też systemy hydrantowe wodne, które zapewniają dostępność wody do gaszenia pożarów. I tutaj również współpracujemy z wieloma producentami, dostarczając im przetwornice pozwalające na taką certyfikację. Mamy też ciekawe doświadczenia w przemyśle dźwigowym – proponujemy tu przetwornice z systemami anti-sway. Dzięki nim, gdy dźwig się przesuwa, przetwornica automatycznie kompensuje wahania ewentualnego ciężaru.
- Czy tego typu wbudowane funkcje zmniejszają ilość koniecznej pracy inżynieryjnej i ułatwiają uruchomienia?
Zdecydowanie tak! Natomiast ważne są też dodatkowe korzyści, które związane są z późniejszą pracą takich systemów. Przetwornice zapewniają informacje analityczne, mogą też generować ostrzeżenia, pozwalając na szerszą autodiagnostykę siebie, silnika i systemu. Jest to bardzo pomocne dla służb utrzymania ruchu i serwisantów.
W Polsce mamy wielu bardzo dobrych inżynierów, ale niestety bywa tak, że niektóre zakłady nie mają odpowiednio dużych zespołów utrzymania ruchu. W takich sytuacjach doceniana jest możliwość wykorzystania urządzeń, które zdejmują z inżyniera część zadań, dostarczając mu przetworzonych informacji analitycznych.
Chciałbym tu wspomnieć jeszcze o jednym składniku naszej oferty produktowej, w mojej opinii bardzo ważnym. Od kilku lat coraz większą część obrotów tworzy sprzedaż przetwornic dla OZE, a dokładniej do systemów przetwarzania na potrzeby magazynów energii. Ta część rynku szybko rośnie, bowiem też zwiększa się udział instalacji prądu stałego w całości sieci energetycznych. Sądzę, że już niedługo może to spowodować, że przetwornice do takich zastosowań będą równie popularne, jak te do pracy z silnikami prądu przemiennego.
- Co stanowi dzisiaj rdzeń Waszej działalności, jeżeli chodzi o napędy? Jak konkurujecie w obszarach rynku, gdzie liczą się głównie produkty ekonomiczne?
Dla naszego działu rdzeniem jest szeroko rozumiany przemysł. Kolejne dwa istotne to: budynki, gdzie stosowane są układy HVAC i pompowe, oraz infrastruktura, czyli przede wszystkim systemy dystrybucji i oczyszczania wody. Do tego dochodzą aplikacje windowe i dźwigowe.
Co do segmentu rynku związanego z produktami najtańszymi – w nim praktycznie nie uczestniczymy. Tutaj odbiorcami są przykładowo wytwórcy ekonomicznych układów klimatyzacyjnych, którzy stosują możliwie najtańsze napędy i silniki, które można kupić na rynku. Uznaliśmy, że ten obszar jest nie dla nas. Aczkolwiek jednak, co jest trendem pozytywnym, coraz więcej takich producentów powoli zmienia optykę. Dzieje się tak dlatego, że ich klienci zwracają coraz większą uwagę na niezawodność systemów klimatyzacyjnych i przede wszystkim zużycie energii.
Na powyższe potrzeby jesteśmy w stanie odpowiedzieć, proponując urządzenia o wysokiej wydajności i energooszczędności. Obecnie rozwijamy koncepcję EC+, w ramach której z producentem silników i wentylatorów tworzymy rozwiązania przeznaczone dla układów klimatyzacyjnych o superwysokiej sprawności. Sądzę, że rynek na takie produkty będzie rósł. O ile bowiem dawniej budowało się biurowce bez większego dbania o koszty ich funkcjonowania, gdyż za te ostatnie i tak miał płacić najemca, o tyle teraz okazuje się, że wynajmujący coraz częściej opuszczają budynki, które są drogie w eksploatacji.
- Co oferujecie w zakresie energooszczędnością poza napędami i innymi omawianymi wcześniej produktami?
Jesteśmy jednym z większych wytwórców modułów przetwarzania energii do samochodów elektrycznych. Zajmuje się tym nasz Silicon Power, który sprzedaje te układy do firm takich jak np. ZF, którzy są dopiero wytwórcami właściwych modułów silników czy baterii samochodowych. Oferujemy też serie dużych przetwornic do magazynów energii i współpracy z sieciami. Wymieniony dział również rozwija inne projekty – przykładowo uruchomiliśmy dwa duże promy zasilane z baterii, współpracujemy z producentami ładowarek oraz przemysłowych magazynów energii. Dzieje się to również w Polsce, gdzie działamy wspólnie z dwoma producentami takich magazynów. Dostarczamy do nich m.in. przetwornice zapewniające współpracę z siecią i sprawne ładowanie baterii.
- Czy dla uzyskania energooszczędności silników wystarczy zadbać o funkcjonalność związaną z monitorowaniem podstawowych parametrów ich pracy?
Monitorując tylko prądy i napięcia, można określić przestrzeń, w której silnik powinien prawidłowo pracować, przy czym oczywiście bierze się tu pod uwagę różne prędkości i obciążenia. Później, w trakcie pracy, kontrolowane jest zachowywanie tych parametrów. Jeżeli układ wychodzi poza kopertę pracy, można na bieżąco informować o tym obsługę. Daje to możliwość interwencji, zanim jeszcze silnik zacznie się przegrzewać lub ulegnie uszkodzeniu.
Dodam, że przetwornica rejestruje bardzo dużo danych – przykładowo może co ułamek sekundy mierzyć prądy, napięcia, itd. Dane te są przetwarzane i analizowane już w samej przetwornicy, przez co nie trzeba ich przesyłać w sieci. Do systemów nadrzędnych trafiają zaś zagregowane informacje, które pozwalają na podejmowanie decyzji. Pamiętajmy oczywiście, że dla osiągnięcia energooszczędności ważna jest przede wszystkim konstrukcja samego silnika i przetwornicy – same parametry pracy nie wystarczą. Tutaj jest core naszego biznesu.
- Czy wśród klientów widzicie zainteresowanie tego rodzaju rozwiązaniami, choćby w kontekście zmian cen energii?
Biorąc pod uwagę rynkowe braki inżynierów i innych specjalistów, w przyszłości właśnie taki trend powinien być dominujący. Urządzenia powinny być coraz bardziej inteligentne, zaś inżynierowie – podejmować tylko kluczowe decyzje.
O ile firmy przekonują się do omawianych rozwiązań dosyć wolno, o tyle, gdy już raz je zastosują, to zazwyczaj nabierają do nich pełnego przekonania. Dodam, że nasze przetwornice dają możliwość wdrożenia niedrogiego, zdalnego monitorowania nawet jednego silnika, który określimy w jakimś układzie jako krytyczny. Dzięki temu mogą z nich korzystać nawet niewielkie firmy.
Ostatnio wyraźnie rośnie popyt na usługi, w tym różnego rodzaju audyty. Wykonują je również nasi partnerzy, którzy sprawdzają zainstalowane w danym obiekcie przetwornice i wyniki analizy wraz z potencjalnymi zagrożeniami przedstawiają klientowi. Prowadzimy również prewencyjne przeglądy serwisowe oraz oferujemy wspominane wcześniej rozwiązania condition based monitoring.
![]()
Szczegóły techniczne związane z wdrożeniem przedstawia Andrzej Sokołowski z działu Danfoss Drives. Budowa nowej hali w fabryce Danfoss w Grodzisku Mazowieckim była dla działu napędów elektrycznych okazją do wdrożenia projektu pilotażowego z przetwornicami częstotliwości VLT HVAC Drive FC102. Urządzenia te mają nowe funkcje, takie jak condition based monitoring oraz remote monitoring. Pierwsza z nich zapewnia ciągłe monitorowanie stanu układu napędowego, w szczególności uzwojeń stojana silnika, profilu obciążenia, dając również możliwość monitorowania drgań silnika. Druga z usług ma charakter serwisowy. Dzięki niej oraz wykorzystaniu protokołu Profinet dane z przetwornic, takie jak parametry pracy, alarmy, trendy, zużycie energii, profil obciążenia i inne, są przekazywane do chmury. Użytkownik może zdefiniować parametry, które chce monitorować i analizować w zdalnej diagnostyce oraz otrzymać pomoc techniczną z lokalnego serwisu. Dane w chmurze są dostępne niezależnie od działania BMS. Połączenie obu funkcji zwiększa niezawodność i bezpieczeństwo eksploatacji całego systemu wentylacji nowej hali, zapewniając dodatkowe wymierne korzyści finansowe. Omawiany system został wykonany przez firmę Inster, integratora automatyki HVAC oraz BMS. Zastosowała ona 16 przetwornic do regulacji wydatku wentylatorów central nawiewno-wywiewnych produkcji Klimor. Konfiguracja napędów FC102 uwzględnia wysoki stopień ochrony obudowy IP55 ze względów na ich montaż na dachu hali, a z uwagi na współpracę z systemem BMS firmy Beckhoff urządzenia mają wbudowane filtry przeciwzakłóceniowe RFI kl A1/B, ograniczające wpływ zaburzeń elektromagnetycznych na komunikację Modbus RTU z tym systemem. |
- Jak wyglądają przepisy związane z klasami sprawności napędów? Z tego co wiem zapowiadano kolejne zmiany dotyczące przemienników częstotliwości i całościowo systemów napędowych, a nie tylko silników AC.
W połowie ubiegłego roku w życie weszła zmiana przepisów odnośnie do klas sprawności jednostek napędowych i obecnie analizowana jest sprawność całości układu, w tym przetwornicy oraz silnika. Nasze urządzenia pozwalają na zapewnienie wysokiego poziomu sprawności wynoszącego IES2.
Uważam, że objęcie klasyfikacją przemienników częstotliwości było bardzo dobrym krokiem rozwojowym. Teraz producenci muszą podawać straty energii nie tylko przy prędkości nominalnej, ale też przy pracy z obciążeniami rzędu 75 i 50%. I ma to sens – przecież w praktyce nie stosujemy przetwornicy w miejscach, gdzie silnik ma pracować cały czas z prędkością maksymalną, ale właśnie tam, gdzie jest ona regulowana. Wtedy bardzo istotne staje się to, ile realnie energii jest traconej właśnie w przypadku ułamkowych części obciążenia. Dodam, że z omawianymi klasyfikacjami można iść jeszcze dalej, włączając kolejne elementy mechaniki układów napędowych. W wielu aplikacjach znacząco wpływają one na efektywność pracy maszyn i urządzeń, stąd też dobrze jest poszerzać spektrum patrzenia na te zagadnienie.
- Zagadnienia dotyczące energooszczędności dotyczą również rozbudowy kampusu produkcyjnego firmy w Grodzisku Mazowieckim. Jakie są szczegóły tej inwestycji?
W zeszłym roku otworzyliśmy w Grodzisku Mazowieckim dużą halę produkcyjną, do której przeniesiono produkcję z zakładu w Danii. Jest to pierwszy całkowicie zeroemisyjny obiekt tego typu. Planujemy też doprowadzenie w ciągu dwóch lat do poziomu zerowej emisji pozostałych dwóch użytkowanych przez nas hal. W nowej hali wykorzystujemy ciepło odpadowe z produkcji, a także zoptymalizowaliśmy obieg ciepła i chłodu. Ważną rolę ogrywają tutaj nasze przetwornice częstotliwości w układach klimatyzacyjnych, notabene zrealizowanych w dużej części wraz z polskimi producentami tych systemów.
Omawiany projekt był dla nas bardzo istotny również dlatego, że połączył on nasze różne kompetencje – od napędowych, poprzez te związane z wentylacją oraz chłodnictwem, do tego ogrzewnictwem. W jego tworzeniu współpracowali również inżynierowie zajmujący się technologiami produkcji ze specjalistami od wentylacji. Dawniej były to zupełnie dwa światy, zupełnie inne grupy osób, które prawie nie kontaktowały się ze sobą. Budowany był zakład, później instalowano i uruchamiano w nim maszyny. Jednak jeżeli zawczasu inwestor zastanowi się, ile ciepła będą generowały maszyny, jakie temperatury w hali będą zimą, latem, itd., to tym lepiej można zaplanować budowę i przede wszystkim w przyszłym użytkowaniu osiągnąć większe korzyści.
Dodam, że w Grodzisku Mazowieckim zastosowaliśmy też rozwiązania z obszaru condition based monitoring oraz remote monitoring. Pozwalają nam znacznie lepiej kontrolować nasze systemy klimatyzacyjne i zasadniczo już po roku widzimy, że ich niezawodność jest wyższa niż systemów standardowych wykorzystywanych w pozostałych halach produkcyjnych.
- Czy doświadczenia pozyskane dzięki omawianemu projektowi planujecie wykorzystywać w przyszłych projektach komercyjnych? Jakie działy firmy brały udział we wdrożeniu?
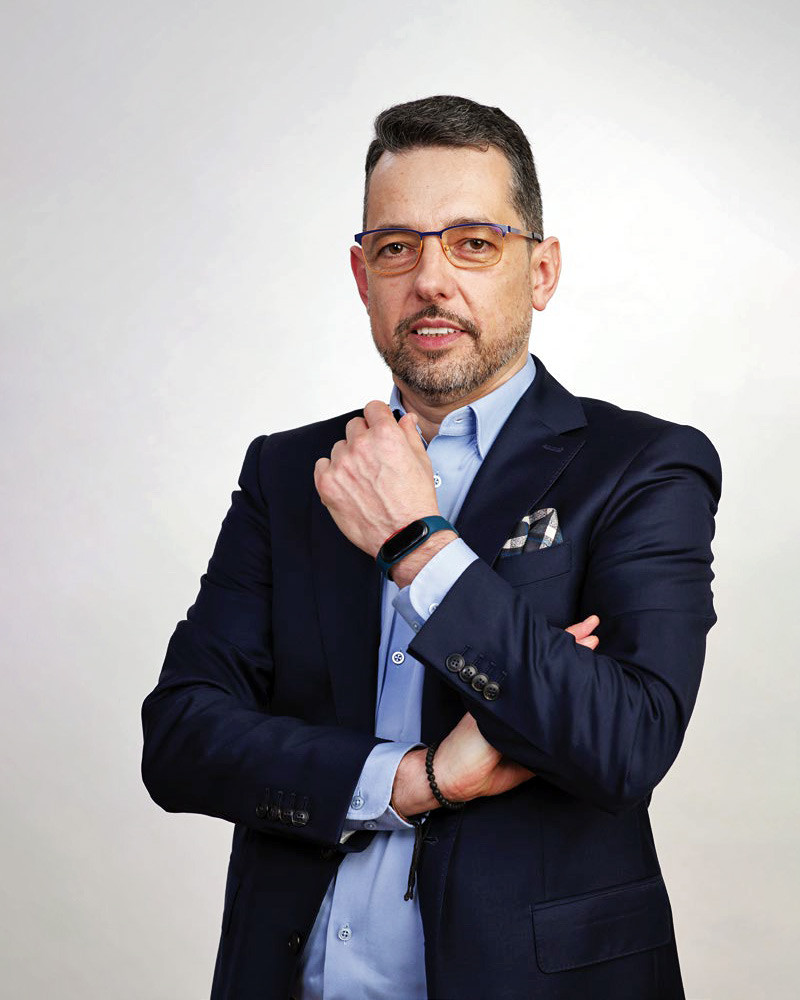
Projekt angażował kilka działów firmy, przede wszystkim Danfoss Climate Solutions, który zajmuje się chłodnictwem i ogrzewnictwem, a także partnerów biznesowych. Koledzy zgromadzili bardzo dużo wiedzy na temat stosowania wymienników ciepła i układów odzysku ciepła, my zaś byliśmy w tym projekcie dostawcą m.in. przetwornic częstotliwości. W przypadku projektów komercyjnych również współpracujemy z wyspecjalizowanymi firmami, które zajmują się układami wentylacyjnymi, chłodnictwem przemysłowym i budynkowym. Zapewniamy partnerom produkty, know-how i szeroko rozumiane wsparcie. I taką współpracę będziemy rozwijali w przyszłości.
Warto zaznaczyć, że niezależnie od tego, czy projekt jest realizowany z producentami systemów klimatyzacyjnych, z integratorami czy klientami końcowymi, wymaga on zawsze działań na wczesnym etapie tworzenia założeń. Specyfikacja projektu, za którą właściwie odpowiedzialny jest inwestor, czyli zwykle też późniejszy właściciel obiektu, musi być tak wykonana, aby oczekiwaną efektywność energetyczną od razu zaplanować. Oczywiście możliwe są też późniejsze modernizacje, jednak najbardziej optymalne jest wdrożenie tego w samych początkach tworzonego projektu.
- Jak wygląda czas zwrotu z inwestycji w przypadku modernizacji obiektów? Czy otrzymujecie zapytania w tym zakresie?
Tak, otrzymujemy je coraz częściej. Gdy koszty energii i innych mediów poszybowały w górę, pojawiło się coraz więcej zapytań o projekty modernizacyjne. Zwracają się do nas różne osoby – i zarządzające obiektami, i też przykładowo inżynierowie utrzymania ruchu, którzy otrzymali od swoich przełożonych zadanie opracowania sposobu oszczędzania energii. Czas zwrotu z inwestycji zależy wprost od kosztów energii. Gdy były one niskie, to wynosił on 5‒7 lat, natomiast obecnie wszystko skraca się do 2‒3 lat. Inwestycje tego typu stają się coraz bardziej opłacalne i merytorycznie uzasadnione.
- Z rozmowy wyłania się obraz przedsiębiorstwa działającego bardzo szeroko. Co łączy te różne dziedziny aktywności rynkowej?
Danfoss jest firmą rodzinną, która inwestuje większość zysków w rozwój – i to ukierunkowany na to, aby polepszać jakość życia ludzi. W wymiarze praktycznym oznacza to, że nasze produkty powinny być energooszczędne, pozwalać oszczędzać wodę, powietrze, żywność, zapewniając do tego wysoką niezawodność użytkowania. I właśnie ta idea spaja nasze trzy pozornie odmienne od siebie biznesy: napędy, climate solutions oraz power solutions.
- Czy działając w Polsce, korzystacie z doświadczeń globalnych?
W Polsce zlokalizowany jest drugi co do wielkości kampus produkcyjny Danfossa w Europie, który rozwija się bardzo dynamicznie. Oprócz produkcji w Grodzisku mamy też zakłady w Gdańsku produkujące węzły cieplne. I o ile opieramy się na kompetencjach lokalnych, o tyle korzystamy też z licznych doświadczeń globalnych. W szczególności słuchamy naszych klientów oraz tego, czego potrzebuje rynek, a następnie odpowiadamy na to innowacjami. Stosujemy tu program MLA, czyli „Meet, Listen, Act”, w ramach którego spotykamy się z kluczowymi klientami, rozmawiamy ich z pracownikami zajmującymi się rozwojem i projektowaniem produktów, zaś pozyskane uwagi finalnie uwzględniamy w kolejnych wersjach produktów. Dzisiaj rynek kupuje pakiety funkcjonalne, szuka rozwiązań. Dlatego też staramy się współpracować z ekspertami w odpowiednich branżach, tak aby w efekcie nasze produkty były jak najlepiej dopasowane do ich przyszłych aplikacji.
- Dziękujemy za rozmowę.