CZĘŚĆ III: UTRZYMANIE RUCHU
JAK DBAĆ O PRZENOŚNIK?
Wybór odpowiedniego typu urządzenia i jego napędu to dopiero połowa sukcesu. Przenośniki wymagają odpowiedniej uwagi od momentu instalacji przez cały czas użytkowania. Przedstawiamy to na przykładzie transporterów taśmowych.
Częstą przyczyną ich awarii jest nieodpowiednio naciągnięta taśma. Gdy jest założona zbyt luźno, zwisa i ześlizguje się z bębna. Łatwiej wtedy o jej uszkodzenie i trudno wycentrować jej bieg. Zbyt mocne napięcie również skraca czas użytkowania tego komponentu przenośnika.
Najlepiej, jeżeli naciąg taśmy mieści się w przedziale od 0,2% do 0,7% jej długości. Im cięższy ładunek, tym napięcie powinno być bliższe górnej granicy tego zakresu. Naciąg taśmy można łatwo sprawdzić. Przed regulacją na obu jej stronach trzeba narysować linię, a po - uruchomić przenośnik na chwilę, zatrzymać go i zmierzyć wydłużenie kreski.
Gdy bieg taśmy nie jest wycentrowany, może się ona trwale rozciągnąć lub skręcić, niszczą się jej brzegi i konstrukcja nośna przenośnika. Podczas załadunku i rozładunku towar może z niej łatwo spaść.
CO ZROBIĆ, ŻEBY TAŚMA SIĘ NIE PRZESUWAŁA?
Warto zamontować barierki, dzięki którym produkty będą układane na jej środku. Ponadto trzeba sprawdzić rolki - jeżeli nie obracają się lub obracają wolniej, na przykład z powodu uszkodzenia łożysk, dodatkowy opór, jaki przy tym stawiają, wypaczy bieg taśmy. Jeśli bębny i rolki nie są ustawione prostopadle do ramy przenośnika (płaszczyzny taśmy), pas też przesunie się w kierunku ich odchylenia. Aby go wycentrować, należy postępować według instrukcji producenta urządzenia.
Nie zawsze także da się uniknąć rozerwania taśmy - w ramce wyjaśniamy, co należy wówczas zrobić. Konserwacja przenośników taśmowych obejmuje ponadto czyszczenie pasów. Dobierając metodę i środki pielęgnacji taśmy, należy uwzględnić specyfikę materiału, z jakiego ją wykonano.
Newralgicznym elementem przenośników i ich napędu są łożyska. W ramce przedstawiamy główne rodzaje uszkodzeń tych elementów. Jedną z ich przyczyn jest nieodpowiednie smarowanie. Powoduje ono przegrzewanie się łożysk, ich nadmierne, zbyt szybkie zużywanie się i sprzyja rozwojowi korozji. Powodów tego może być kilka. Wśród nich najczęstsze to: niedostateczne albo przesadne smarowanie oraz zastosowanie niewłaściwego środka smarnego.
|
CZYM SMAROWAĆ?
Typowo korzysta się z oleju lub smaru, czyli oleju, do którego dodano zagęszczacz. Ten ostatni to zwykle mydło metaliczne, czyli substancja, dzięki której olej bazowy uzyskuje konsystencję półstałą. Oleje zaleca się stosować przy większych prędkościach ruchu. Łatwiej rozprowadzają się one po powierzchni łożysk oraz szybciej rozpraszają ciepło. Smarowanie przy użyciu oleju jest również łatwiejsze i można je zrealizować na wiele sposobów (m.in. metodą kąpieli olejowej, rozbryzgową, z wymuszonym obiegiem oleju). Można także dokładnie kontrolować ilość tego środka.
Z kolei smary lepiej przylegają do powierzchni łożysk. Dzięki temu nie wyciekają z komory łożyskowej. Mniejsze straty środka smarnego pozwalają na rzadszą jego aplikację. Ponadto smary uszczelniają komorę łożyskową przed wnikaniem zanieczyszczeń oraz wilgoci z zewnątrz.
NAJWAŻNIEJSZE WŁAŚCIWOŚCI ŚRODKA SMARNEGO
Wybierając konkretny środek smarny, należy porównać kilka najważniejszych właściwości substancji. Są to m.in.: zakres temperatur roboczych, lepkość, współczynnik lepkości, odporność na utlenianie i zdolność przenoszenia obciążeń.
W przypadku smarów dolna temperatura graniczna to najniższa temperatura, przy której możliwy jest jeszcze rozruch łożyska. Ma na nią wpływ głównie lepkość oleju bazowego. Górna temperatura graniczna to z kolei temperatura, przy której smar zmienia swoją konsystencję na płynną - zależy ona przede wszystkim od właściwości zagęszczacza.
Lepkość jest miarą oporu cieczy przy płynięciu. Aby pomiędzy współpracującymi powierzchniami łożyska wytworzyła się powłoka środka smarnego, musi on, w danej temperaturze roboczej, mieć określoną minimalną wartość tej wielkości. Wskaźnik lepkości jest miarą względnej zmiany lepkości cieczy w danym zakresie temperatur - im większą ma wartość, tym jest ona mniejsza. Środki smarne ulegają też utlenianiu. W jego wyniku tworzą się różne związki chemiczne, które pogarszają właściwości smaru.
Odporność na utlenianie to jedna z właściwości środków smarnych, które poprawia się, stosując specjalne dodatki (anti-oxidants) spowalniające tę reakcję. Kolejną jest zdolność do przenoszenia obciążeń. Oleje EP (Extreme Pressure) zawierają substancje, które przywierając do metalowych powierzchni, uniemożliwiają ich stykanie się, nawet w razie wywierania na nie bardzo silnego nacisku.
Do środków smarnych dodaje się oprócz tego inhibitory korozji oraz detergenty, które rozpuszczają zanieczyszczenia pływające w oleju. Ich składnikiem są też modyfikatory zmniejszające tarcie, którymi przeważnie są cząstki stałe, m.in. grafit, dwusiarczek molibdenu, dwusiarczek wolframu. Ponadto stosowane są substancje zapobiegające spienianiu się oleju oraz te, które poprawiają jego wskaźnik lepkości. To drugie uzyskuje się przez zwiększenie jego oporu przy płynięciu w wyższych temperaturach oraz zwiększenie płynności w niższych temperaturach.
CO ZA DUŻO TO NIEZDROWO
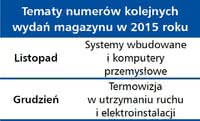
Tematy numerów kolejnych wydań magazynu w 2015 roku
Ważne jest też dostosowanie ilości środka smarnego do warunków pracy łożysk, głównie ich prędkości granicznej. Jeżeli będzie go zbyt mało, nadmierne tarcie szybko zniszczy te elementy. Przepełnienie nim z kolei wywołuje dodatkowe opory ruchu, powoduje wzrost temperatury i pogarsza właściwości smaru.
W związku z tym dobrze jest przestrzegać pewnych ogólnych ograniczeń. W przypadku smarów przyjmuje się na przykład, że jeżeli prędkość obrotowa jest mniejsza niż 50% prędkości granicznej, ilość przestrzeni wewnątrz łożyska wypełnionej smarem powinna wynosić od 1/2 do 2/3 dostępnej przestrzeni. W przeciwnym wypadku zalecana objętość to od 1/3 do 1/2 wolnego miejsca.
Monika Jaworowska
W artykule wykorzystano materiały firm Redor, SKF oraz NSK
Źródła zdjęć: QC Industries, ContiTech, WEG, Siemens, Bosch Rexroth, Schaeffler.