Złącza ogólnie dzieli się na: przesyłające energię (silnoprądowe) i dane (analogowe, cyfrowe). Dostępne są również w wersjach hybrydowych, w których do jednej obudowy podłączane są przewody zasilające i sygnałowe, elektryczne i optyczne, w różnych konfiguracjach. Główne komponenty złączy to, poza obudową wtyczki: dławnica kablowa, wkład męski i wkład żeński ze stykami i obudowa gniazda. Podobnie klasyfikuje się kable, na energetyczne i sygnałowe. Ich komponenty to: osłona zewnętrzna, osłony wewnętrzne izolujące żyły, ekran, przewody, a w kablach światłowodowych: rdzeń i płaszcz, tuba ochraniająca włókno światłowodowe, osłona zewnętrzna. Materiały oraz konstrukcje warunkują zastosowanie złączy i kabli – te przemysłowe muszą się wyróżniać odpowiednią wytrzymałością i dodatkowymi cechami, zależnymi od typu sygnałów i miejsca montażu. Przykład środowiska, gdzie wymagania stawiane złączom i kablom są wysokie, to pojazdy w transporcie drogowym i szynowym.
Na przykład od złączy montowanych na zewnątrz pociągów (między wagonami, pod nimi, na dachu, przy torach) oczekuje się odporności na: silne wibracje, osłabiające połączenia, uderzenia drobin piasku, kamieni i opady atmosferyczne (deszcz, śnieg), powodujące erozję i korozję, oblodzenie oraz nasłonecznienie, a więc skrajnie niskie i wysokie temperatury, skutkujące kurczeniem się i rozszerzaniem materiałów. Na wstrząsy i drgania i ekstremalne temperatury narażone są także złącza w autach dostawczych. Te oprócz tego trzeba zabezpieczyć przed: wnikaniem wilgoci, kontaktem z substancjami korozyjnymi (sól drogowa, chemikalia), wnikaniem pyłów, kurzu i innych zanieczyszczeń.
Jak zapewnić szczelność złączy?
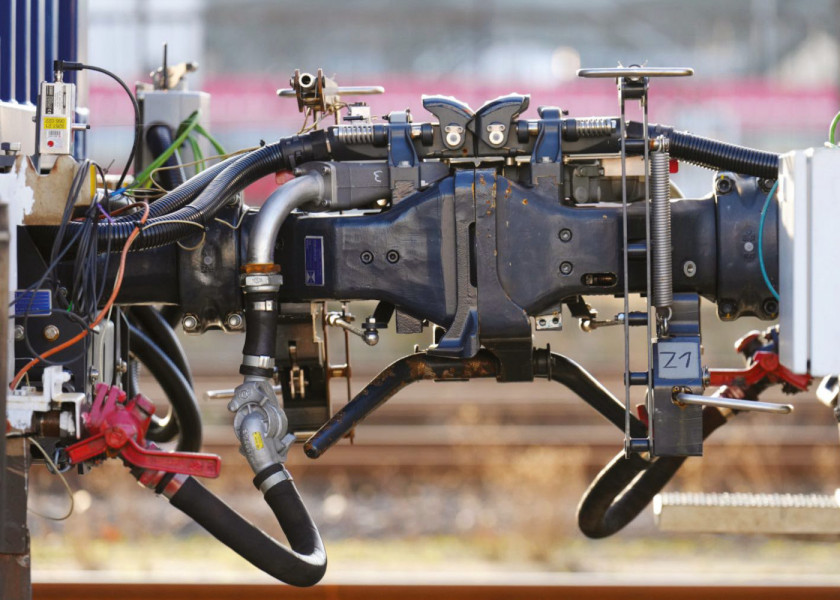
Złącza wodoodporne i pyłoszczelne są chronione uszczelnieniami z tworzyw sztucznych. Ich skuteczność charakteryzuje dwucyfrowy stopień ochrony IP. Pierwsza cyfra w jego zapisie, 5 albo 6, opisuje odpowiednio pyłoodporność i pyłoszczelność, z kolei druga, z przedziału 0‒9, wodoszczelność przy różnym nasileniu oddziaływania wody, od pojedynczych kropel, przez polewanie strugą wody, po pełne w niej zanurzenie. Na przykład złącza z gwarantowanymi stopniami ochrony IP67 i IP68 obydwa są pyłoszczelne, ale pierwsze jest odporne tylko na krótkotrwałe zanurzenie w wodzie, a drugie pozostanie wodoszczelne nawet przy ciągłym. Największą szczelność gwarantują złącza hermetyczne uszczelniane szkłem, ceramiką lub żywicą. Są również zaprojektowane tak, by wytrzymały wysokie ciśnienie.
Popularne są szczególnie złącza z uszczelnieniem ze szkła. Zalety tego materiału to: trwałość, wytrratura pracy. Proces uzyskiwania hermetyczności polega na topieniu szkła w piecu do czasu, aż wypełni ono przestrzeń pomiędzy kontaktami i obudową wkładki, a między szkłem i metalem powstaną trwałe wiązania. Wtedy temperatura jest obniżana, aż do schłodzenia wkładów. By uzyskać szeroki zakres temperatur pracy, szkło i metal powinny charakteryzować się zbliżonymi współczynnikami rozszerzalności cieplnej. Zapobiega to niekontrolowanym naprężeniom i przesunięciom komponentów wkładek złącz przy zmianach temperatury.
Jaki materiał na obudowę złączy?
Przed uderzeniami i czynnikami środowiskowymi wchodzącymi w reakcje złącza chronią obudowy. Kluczowe znaczenie ma w tym przypadku ich materiał – metal albo tworzywo sztuczne. Złącza w obudowach z metali są cięższe niż z tworzyw sztucznych. Pierwsze sprawdzają się w razie narażenia złączy na duże siły ciągnące i ekstremalne temperatury i pełnią funkcję ekranu. Popularnym materiałem jest aluminium poddane dodatkowej obróbce poprawiającej jego właściwości, na przykład anodowane, malowane proszkowo, pokryte różnymi powłokami (na przykład: niklową, tytanową, niklowo- -teflonową). Obudowy złączy wykonuje się także ze stali nierdzewnej, a jeżeli koszt złącza ma mniejsze znaczenie niż jego waga, jak m.in. w wyposażeniu samolotów, z tytanu. Obudowy z tworzyw sztucznych, wzmacniane na przykład włóknem szklanym, są tańsze. Ich zastosowanie ogranicza jednak temperatura pracy oraz brak ekranowania.
W zakresie zabezpieczenia przed wibracjami stosuje się mechanizmy blokujące. Standardowy pojedynczy ma dźwignię (rygiel) z przodu lub z boku obudowy. Ruch dźwigni powoduje zamknięcie obudowy i osłony. Podwójne systemy blokowania mają dwie dźwignie.
Bezpieczeństwo kabli w razie pożaru
Jeżeli natomiast chodzi o złącza i kable montowane wewnątrz lokomotywy, w wagonach, szczególnie w przedziałach pasażerskich, i kabinach pojazdów, wymaga się m.in., by były wykonane z materiałów niepalnych, nierozprzestrzeniających ognia i niewydzielających w czasie spalania szkodliwych substancji. Zwiększa to poziom bezpieczeństwa, ogień, dym i toksyczne produkty spalania w zamkniętych pomieszczeniach stanowią bowiem śmiertelne zagrożenie dla osób w nich przebywających.
W związku z tym w instalacjach spełniających normy przeciwpożarowe trzeba korzystać z kabli wykonanych z materiałów bez halogenów, dodatków, które stosuje się, żeby uzyskać określone właściwości tworzyw sztucznych, na przykład dużą wytrzymałość termiczną i, paradoksalnie, mniejszą palność. Ograniczenie to wynika stąd, że spalając się, wydzielają trujące i korozyjne gazy, które w połączeniu z wodą tworzą żrące ciecze. Mechanizm tego jest następujący: pod wpływem bardzo wysokiej temperatury z izolacji kabli wydzielają się halogenki wodoru, a te łącząc się z wodą używaną do gaszenia pożaru albo wilgocią z błon śluzowych, tworzą kwasy, na przykład kwas solny. Powstają też silnie toksyczne dioksyny. W efekcie nawet jeżeli ktoś przeżyje pożar, jego zdrowie może zostać trwale uszkodzone. Szerzej o halogenach piszemy w ramce.
Dlaczego wycofano halogeny?Do grupy halogenów zaliczanych jest pięć pierwiastków, niemetali, z 17. grupy układu okresowego: fluor, chlor, brom, jod i astat. Tworzywa sztuczne zawierające je łatwo można rozpoznać, ponieważ w swojej nazwie zawierają nazwy tych pierwiastków, jak na przykład: polichlorek winylu, kauczuk chloroprenowy, propylen fluoroetylenowy, fluoropolimery. Do stopniowego wycofywania z użytku kabli z elementami z materiałów zawierających halogeny przyczyniło się kilka wypadków. Jednym z tragiczniejszych był pożar na stacji metra Kings Cross w Londynie, który wybuchł w 1987 roku. Zginęło w nim 31 osób, a 100 zostało rannych. Jak wykazało późniejsze śledztwo, zapoczątkowała go upuszczona na ruchomych schodach zapałka, a liczne niekorzystne czynniki przyczyniły się do jego rozprzestrzenienia się i tak dużej liczby ofiar. Jednym z nich były kable z osłoną z PVC, które paląc się, wydzielały ogromne ilości czarnego dymu i toksycznych gazów, utrudniając ludziom ucieczkę i ich zatruwając. Kolejnym zdarzeniem był pożar, który wybuchł w 1988 roku w Bell Telephone Company w Illinois. W jego wyniku firma poniosła ogromne straty w sprzęcie zniszczonym przez korozyjne gazy wydzielające się w czasie spalania kabli. W efekcie zaczęto rezygnować z osłon z wymienionych materiałów, zastępując je m.in.: polipropylenem, gumą silikonową, poliuretanem, polietylenem, poliamidem, elastomerami termoplastycznymi, gumą etylenowo-propylenowo-dienową. Kable bez halogenowe zaczęto również specjalnie znakować – obecnie można się spotkać z m.in. następującymi etykietami: LS0H (Low Smoke, Zero Halogen), LSHF (Low Smoke, Halogen Free), LSNH (Low Smoke, Non-Halogen). |