Jakie są zalety kabli podziemnych?
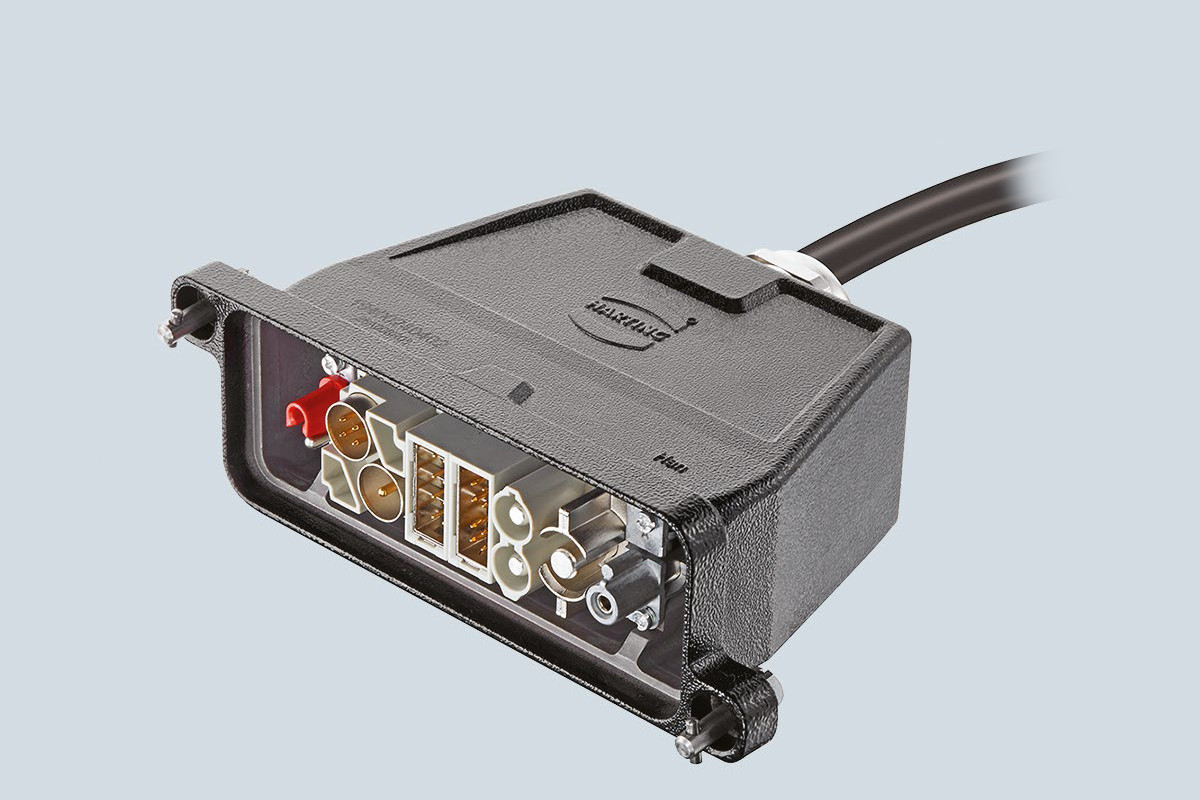
Pierwsze kable poprowadzono pod ziemią pod koniec XIX wieku. Od tamtej pory sukcesywnie zyskują na popularności jako alternatywa dla napowietrznych linii kablowych. Wynika to z ich licznych zalet. Prowadzi się je przeważnie tam, gdzie linie napowietrzne nie sprawdzają się ze względu na bezpieczeństwo (linie podziemne nie stwarzają zagrożenia pożarowego ani ryzyka kolizji drogowych, powietrznych, zerwania przewodów pod napięciem), ograniczenia przestrzenne (podziemne pozwalają na zabudowę terenu) albo estetykę (podziemne są niewidoczne, więc nie zmieniają krajobrazu). Poza tym grunt chroni zarówno kable przed uszkodzeniem, jak i ludzi i zwierzęta przed porażeniem prądem. Linie podziemne są także niewrażliwe na ekstremalne warunki atmosferyczne (burze, silny wiatr, oblodzenie, ośnieżenie) i wandalizm. Dzięki temu są rzadziej i taniej konserwowane, a ich żywotność jest liczona w dziesiątkach lat (nawet 50).
Nie są jednak oczywiście niezniszczalne – zagrażać im mogą na przykład wykopy prowadzone w niewłaściwym miejscu, jak również klęski żywiołowe, zwłaszcza powodzie czy rozległe pożary. Dlatego również wymagają specjalnych rozwiązań konstrukcyjnych, zabezpieczających je przed uciążliwymi czynnikami.
Ochrona przed wodą
Takim jest woda, która powoduje korozję metalowych ekranów i przewodów. Narażone są na nią kable zakopane w strefie zalewowej albo w bardzo wilgotnym gruncie pod drogą wodną. Przed wodą zabezpiecza się je wielostopniowo. Przykładem jest ochrona trzystopniowa, składająca się z: taśmy półprzewodzącej, taśmy pęczniejącej pod wpływem wody oraz wodoodpornych włókien. Pierwsza stanowi podłoże z PET pokryte jedno- lub obustronnie półprzewodzącym polimerem. Oprócz tego, że zapobiega ona korozji elektrolitycznej metalowych części kabla, wyrównuje rozkład pola i zapewnia kontakt elektryczny z uziemieniem. Z kolei taśmy, które pęcznieją pod wpływem wody, mają za zadanie wchłonąć ją w miejscu przerwania izolacji i, dzięki szybkiemu wzrostowi swojej objętości, zablokować jej głębsze wnikanie. Ogranicza to rozwój uszkodzenia, zabezpiecza je i ułatwia jego zlokalizowanie oraz naprawę. Swoje właściwości tego typu taśmy zawdzięczają napyleniu proszków stanowiących mieszankę superchłonnych polimerów (Superabsorbent Polymers). Są to materiały, które są w stanie wchłonąć wodę w ilości od kilkuset do nawet tysiąca razy większej niż same ważą, a co ważniejsze nie uwalniają jej, nawet pod ciśnieniem. Mechanizm zatrzymywania wody jest następujący: SAP to polimery usieciowane, których łańcuchy są skurczone. W kontakcie z wodą struktury te rozszerzają się, wiążąc cząsteczki wody w swoich sieciach. Superchłonnymi polimerami impregnuje się też włókna wodoodporne.
Powyższe sposoby ochrony są zaliczane do kategorii suchych. Alternatywą jest uszczelnienie kabli nieprzepuszczalnym dla wody żelem, który wypełnia w nich wszystkie wolne przestrzenie. Jego ograniczenia to: "brudne" i wolniejsze łączenie przy instalacji i cięższy kabel.
Case study: Żel rozwiązał problem ze złączamiDostawca koparek, serwisując je w ramach gwarancji, coraz częściej w jednym z modeli spotykał się z problemem wnikania wody w złącza zamontowane w podwoziu, a w konsekwencji z korozją ich styków i przerwaniem połączeń. Kłopotliwe złącza miały stopień ochrony IP69, a woda wpływała do nich na skutek kapilarnego ruchu kropel, które spływały po dławicy kablowej i dalej po stykach. Sprzyjały temu trudne warunki pracy koparek, w których nawet złącza dobrze dopasowane są narażone na liczne niekorzystne czynniki (wilgoć, zapylenie, środki chemiczne). Problem był powodem kosztownych przestojów i konserwacji tych maszyn. Rozwiązaniem okazała się aplikacja specjalnego smaru do złączy. Środek ten powinien spełniać następujące warunki: musi mieć właściwości izolacyjne, by nie zwierał styków, nie może zwiększać rezystancji kontaktu na ich końcach, musi je uszczelniać, powinien być odporny na czynniki otoczenia i trwały, by chronić złącze jak najdłużej i najefektywniej między kolejnymi smarowaniami. W związku z tym wybrano smar na bazie oleju polialfaolefinowego. Charakteryzuje go stabilność termiczna i był kompatybilny z tworzywami sztucznymi, z których wykonano złącze. Zawiera oprócz tego dodatek w postaci zagęszczacza krzemionkowego nadającego mu właściwości hydrofobowe (zdolność odpychania cząsteczek wody). W skład smaru wchodzą też m.in. środki zapobiegające powstawaniu patyny i, ze względu na jego półprzezroczystość, barwnik, który reaguje na promieniowanie ultrafioletowe, ułatwiając jego wykrycie. Aplikując go, trzeba było przestrzegać kilku zasad. Przede wszystkim powinien być nakładany we wszystkich punktach wnikania wilgoci. Zalecono, by pokryć nim męską i żeńską stronę złącza. Należało także uważać, żeby go nie przepełnić, gdyż ze względu na wysoki stopień uszczelnienia (IP69) nadmiar smaru nie będzie mógł się wydostać przez tylną część złącza. |
Kable podmorskie
Kable podmorskie są użytkowane od ponad wieku, a na przestrzeni lat zakres ich zastosowań stale się poszerzał. Początkowo były używane do zasilania odizolowanych obiektów morskich, jak na przykład latarni morskich. Później głównym celem prowadzenia kabli pod powierzchnią morza było zasilanie wysp przybrzeżnych w zastępstwie pracujących lokalnie, zwykle nieefektywnych, agregatów prądotwórczych. W latach 60. ubiegłego wieku zaczęto je również wykorzystywać do łączenia niezależnych sieci elektroenergetycznych różnych krajów. Pozwala to na współdzielenie mocy wytwórczych w okresach większego zapotrzebowania, co zapewnia stabilność zasilania i efektywniejsze zarządzanie jednostkami wytwórczymi. Obecnie natomiast coraz ważniejszym zastosowaniem kabli podmorskich znów jest zasilanie obiektów morskich. Takimi są platformy wydobywcze ropy i gazu, będące odbiornikami energii zasilającej i farmy wiatrowe, zasilające za ich pośrednictwem sieci lądowe w zieloną energię. Oprócz kabli energetycznych pod powierzchnią morza prowadzone są również te telekomunikacyjne: telegraficzne, telefoniczne oraz internetowe.
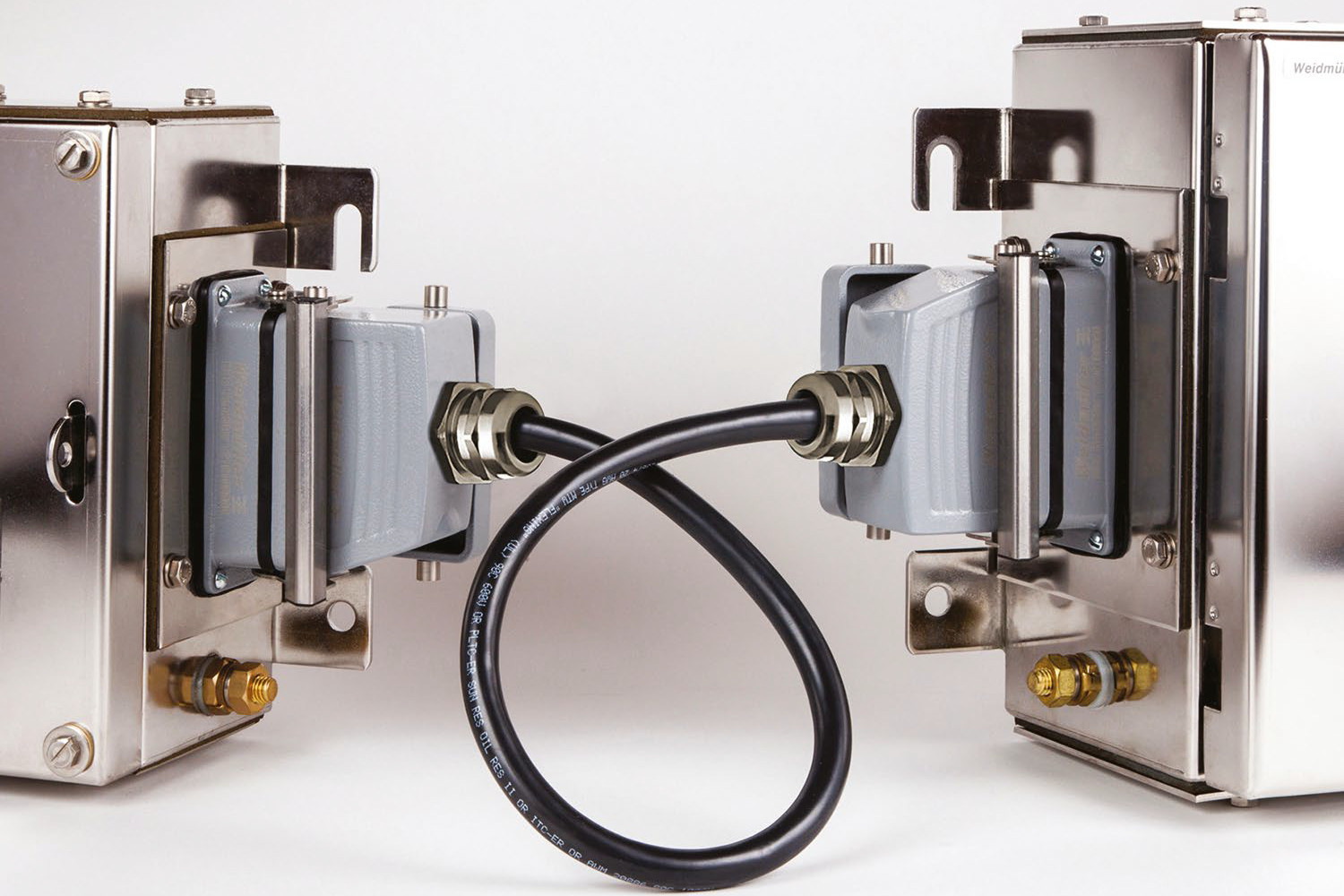
Kable podmorskie mają kilka ograniczeń. Przede wszystkim ich instalacja jest kosztowna, pracochłonna i wolna, podobnie jak ich naprawa. Z drugiej strony wyróżnia je niezawodność transmisji i jej bezpieczeństwo, ponieważ nie są łatwo dostępne, co z kolei utrudnia fizyczną ingerencję, jak podsłuchanie transmisji czy celowe zniszczenie. Są także bardziej opłacalne niż satelity.
Aby spełnały swoją funkcję przez zakładany okres żywotności ich konstrukcja musi być dostosowana do specyfiki środowiska, w którym zostaną zainstalowane. W związku z tym od kabli układanych na dnie morskim wymaga się, by były wytrzymałe na kontakt ze skałami i nierównomiernościami podłoża. Ponadto mogą być narażone na uszkodzenie przez zwierzęta morskie oraz statki i łodzie rybackie (kotwice, sprzęt rybacki). Muszą także wytrzymywać ekstremalne warunki, jak sztormy, tsunami i aktywność wulkaniczna. Wymagana jest oprócz tego wodoszczelność – woda może się przedostać do ich wnętrza nie tylko w wyniku uszkodzenia osłony, ale również przez nieszczelne złącza.
Konstrukcje pancerzy
W zakresie ochrony przed wnikaniem wody stosuje się rozwiązania analogicznie do tych w kablach podziemnych. Przed uszkodzeniem mechanicznym z kolei kable podmorskie chronią pancerze.
Wykonuje się je z metalowych drutów owiniętych wokół kabla z określoną długością skrętu (skokiem), czyli długością kabla, na której drut go jednokrotnie oplata. Typowo jest ona od 10 do 30 razy większa niż średnica kabla, a średnica drutów wynosi od kilku milimetrów do nawet centymetra. Konstrukcja opancerzenia ma duży wpływ na właściwości kabla, takie jak sztywność zginania czy wytrzymałość na rozciąganie. Przykładowo pancerze o dużym skoku, w którym druty biegną prawie równolegle do osi kabla, charakteryzuje duża wytrzymałość na rozciąganie, bez nadmiernej sztywności skrętnej. Można je łatwo zwinąć. Z drugiej strony duży skok zwiększa sztywność zginania kabla, co jest niepożądane. Ważny jest też sposób nawijania: pancerze z nawinięciem jednokierunkowym mogą amortyzować skręcanie tylko w jedną stronę, spiralne natomiast mają tendencję skręcania kabla. Podwójna warstwa drutów zapewnia większa ochronę, zwłaszcza gdy są nawinięte w przeciwnym kierunku, dzięki czemu trudniej o ich przebicie ostrymi krawędziami. Wykonywane są również pancerze z drutami nawiniętymi z odstępami, które wypełnia się tworzywem sztucznych lub pozostawia niewypełnione. Taka konstrukcja zmniejsza wagę kabla i redukuje straty na prądy wirowe, zapewniając jednak mniejszą ochronę niż pancerz zamknięty. Pancerze wykonuje się zwykle ze stali miękkiej, a jeżeli ten materiał nie sprawdza się ze względu na straty i nagrzewanie, mogą go zastąpić m.in. miedź i aluminium. Pierwszy materiał charakteryzuje wysoka cena, mała wytrzymałość mechaniczna, ale dobra odporność na korozję w wodzie morskiej, co jest słabym punktem aluminium. Drogie są też pancerze ze stali nierdzewnej.
Podsumowanie
W artykule przedstawiliśmy przykłady różnych zastosowań, w których złącza i kable są użytkowane w wymagających warunkach, w niektórych bardziej niż w innych. Na podstawie opisanych rozwiązań konstrukcyjnych wyraźnie widać, że producenci tych komponentów są w stanie sprostać nawet najbardziej ekstremalnym potrzebom. Dlatego w praktyce to od tych, którzy mają zdecydować o ich wyborze, zależy, czy złącza i kable staną się najsłabszym ogniwem.
Monika Jaworowska