Złącza i kable a zagrożenie wybuchem
W wielu gałęziach przemysłu, szczególnie w branży chemicznej, petrochemicznej, papierniczej, spożywczej, górnictwie i poza nimi na różnych stanowiskach pracy, na przykład w lakierniach i malarniach w fabrykach motoryzacyjnych, może wytworzyć się atmosfera wybuchowa. Jest to mieszanina palnych gazów, par albo pyłów z powietrzem, w której po zainicjowaniu źródłem zapłonu spalanie rozprzestrzenia się samorzutnie. Aby doszło do wybuchu, muszą być zatem jednocześnie obecne trzy czynniki: substancja łatwopalna, tlen oraz źródło zapłonu. Na dwa pierwsze konstruktor wyposażenia do użytku w strefach występowania zagrożenia eksplozją nie ma wpływu, w związku z czym jego zadaniem jest wyeliminowanie trzeciego składnika, przez niedopuszczenie do powstania iskry i otwartego płomienia.
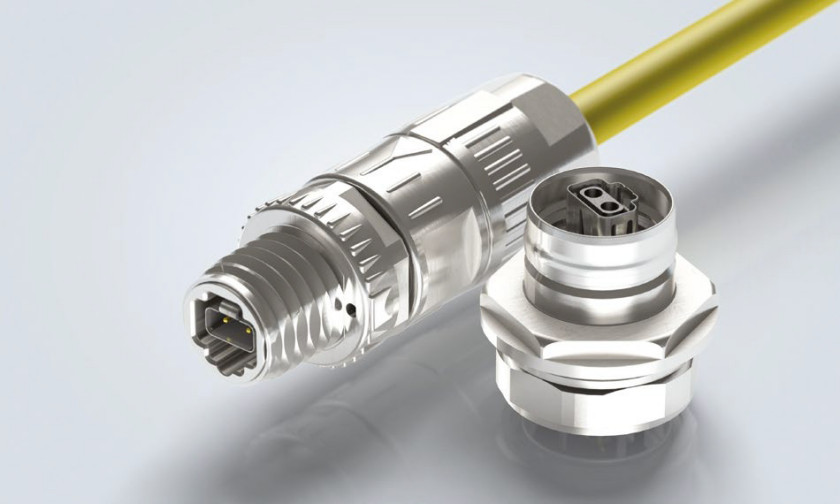
W przypadku złączy przykładowym rozwiązaniem jest ich umieszczenie w ognioszczelnej osłonie. Obejmuje ona wszystkie komponenty znajdujące się między dławicą kablową a obudową gniazda. Projektuje się ją tak, aby styki wkładek zostały rozłączone, zanim zostanie zdjęta. Oprócz tego, na wypadek eksplozji wewnątrz osłony gniazdo wykonuje się w taki sposób, by wytrzymało ciśnienie wybuchu.
Jeśli z kolei chodzi o kable, to w takich warunkach wykorzystuje się te z izolacją mineralną. Są zbudowane z powłoki metalowej, wypełnionej sprasowanym sproszkowanym tlenkiem metalu, przeważnie tlenkiem magnezu. Zapewnia on izolację między żyłami i izolację przewodów od powłoki zewnętrznej. Kable z izolacją mineralną nie iskrzą, nie palą się ani nie podtrzymują płomienia. Nie wytwarzają też szkodliwych gazów. Wyróżnia je ponadto wysoka odporność termiczna – są w stanie wiele godzin wytrzymać temperaturę przekraczającą nawet +1000°C, o ile tylko materiał osłony został odpowiednio dobrany – przykładem jest stal nierdzewna. W połączeniu ze złączami w wersji przeciwwybuchowej kable w izolacji mineralnej mogą spełnić wymogi normy ATEX.
Kable w skrajnych temperaturach
W wielu zastosowaniach kable są też narażone na wysokie temperatury w normalnych warunkach – przykładowo kable z izolacją z tlenku magnezu używane są m.in. w pomiarach temperatury za pomocą czujników rezystancyjnych i termopar. Niektóre wysokotemperaturowe zastosowania wymagają wprowadzenia specjalnych rozwiązań. Takim jest chłodzenie kabli. Kable chłodzone wodą są używany na przykład jako wtórne w piecu łukowym do produkcji stali, gdzie narażone są na silne promieniowanie cieplne. Zasadniczo jednak podstawową gwarancję niezawodności kabli w wysokich, jak i w niskich temperaturach, stanowią odpowiednio dobrane materiały, z których je wykonano. W przeciwnym razie, jeżeli zostaną wystawione na działanie, nawet niekoniecznie długotrwałe, czasem wystarczy tylko chwilowe, skrajnych temperatur, ich elementy miękną lub stają się kruche. Należy się tego spodziewać już po przekroczeniu progu +60°C i przy temperaturach poniżej –20°C. W konsekwencji dochodzi na przykład do: pękania i kruszenia się izolacji żył lub osłony kabla, zwarć, przebić, sklejania żył kabla, nadtapiania izolacji albo jej odkształcania.
Na wysokie temperatury odporne są szczególnie tworzywa termoutwardzalne. Przykładami są: silikon (od –80°C do +200°C), EPR (kauczuk etylenowo-propylenowy) o zakresie temperatur pracy –60°C...+150°C, XLPE (polietylen usieciowany) o dużej wytrzymałości mechanicznej w przedziale temperatur od –40°C do +100°C i neopren (+121°C praca ciągła, wyższa z przerwami), teflon (–190°C...+300°C). W przypadku kabli narażonych na niskie temperatury spowodowane wyłącznie oddziaływaniem czynników atmosferycznych zwykle powinna wystarczyć izolacja z tworzywa poliuretanowego (PUR). Jeżeli natomiast chodzi o materiały żył w wysokich temperaturach, w zakresie +150°C... +200°C mogą być używane przewody miedziane platerowane srebrem, a +200°C... +450°C przewody z miedzi, które pokryto powłoką niklową.
Złącza w kosmosieKosmos to wyjątkowe nieprzyjazne środowisko. Projektowanie wyposażenia do użytku w warunkach panujących w przestrzeni kosmicznej dodatkowo utrudnia fakt, że możliwości w zakresie napraw i zmian są bardzo ograniczone – od urządzeń pokładowych pojazdów kosmicznych wymaga się więc niezawodności i żywotności nieporównywalnych z tymi w nawet najbardziej zaawansowanych gałęziach przemysłu. Zadanie jest tym trudniejsze, że poza ekstremalnymi temperaturami, wstrząsami i wibracjami złącza i kable w kosmosie są narażone na dodatkowe niekorzystne czynniki, unikalne dla tego środowiska: promieniowanie kosmiczne, tlen atomowy, odgazowywanie. Ochrona przed promieniowaniem opiera się zwykle na dwóch mechanizmach: odbicia i pochłaniania, dlatego unika się takich metali, jak: czysta cyna, kadm i cynk, zastępując je złotem oraz stalą nierdzewną. Jeśli chodzi o tworzywa sztuczne, to na przykład polisiarczek fenylenu jest wysoce odporny na promieniowanie gamma. Jako materiał izolacyjny sprawdzą się również żywica poliimidowa i polieteroeteroketon. Poza narażeniem na promieniowanie złącza, zwłaszcza te zamontowane na zewnątrz statku kosmicznego, są podatne na uszkodzenia i zniszczenia spowodowane tlenem atomowym (z jednym atomem tlenu). Jest on wysoce reaktywny i powoduje erozję wielu materiałów, w tym większości polimerów, a nawet niektórych metali, w tym srebra. Ochronę kabli i złączy przed tym czynnikiem są w stanie zapewnić specjalne materiały, na przykład radatox. Został on opatentowany przez firmę Axon Cable i według jej zapewnień jest 10 razy odporniejszy na tlen atomowy i do 40% lżejszy niż typowe perfluoropolimery, takie jak FEP, PFA i PTFE i 100 razy odporniejszy niż poliimidy. Odgazowanie to z kolei uwalnianie lotnych związków organicznych uwięzionych w tworzywie sztucznym zachodzące w próżni przy braku ciśnienia atmosferycznego. Ich cząstki osadzają się na powierzchni złączy i kabli, zanieczyszczając je. By temu zapobiegać na etapie produkcji materiały te wypala się w piecu próżniowym, co uwalnia lotne związki organiczne w kontrolowanym środowisku. |
Jak ważna jest elastyczność?
Kolejną grupą zastosowań stawiających wysokie wymagania okablowaniu są aplikacje sterowania ruchem. W ich przypadku wymaga się małych promieni gięcia, które ułatwiają instalację oraz odporności na wielokrotnie powtarzające się cykle zginania. Ze względu na elastyczność kable klasyfikuje się na: stacjonarne, elastyczne, do ciągłego zginania i ciągłego skręcania. Pierwsze są sztywne i nie są zalecane do użytku w ruchu ani nawet, wtedy gdy okablowanie trzeba poprowadzić po rogach lub po łuku, co wymaga pewnej elastyczności. Dlatego nawet jeżeli nie będą przemieszczane, ale zostaną ułożone w maszynie lub korytkach kablowych z narożnikami, lepiej wybrać model droższy, ale przystosowany do zginania.
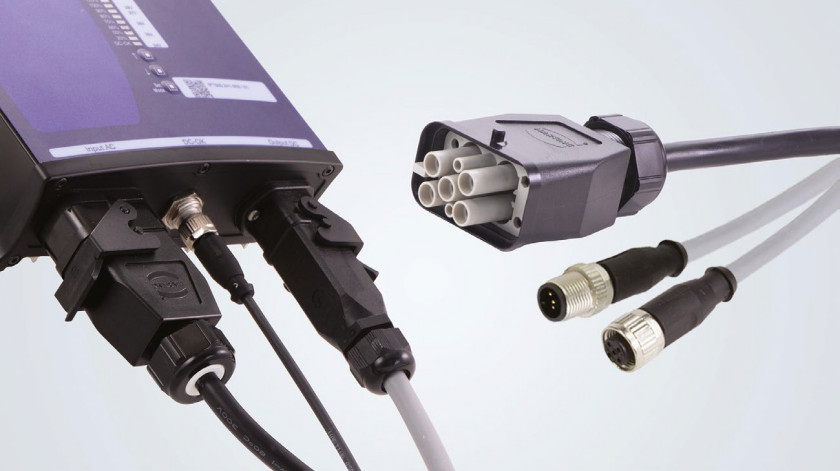
Kable elastyczne mają typowo wytrzymałość na kilka do kilkunastu milionów cykli gięcia, zaś w przypadku tych przeznaczonych do zastosowań, w których narażone będą na ciągłe zginanie, producenci deklarują wytrzymałość nawet kilkudziesięciu milionów cykli gięcia. Kable o najwyższej trwałości to natomiast te, które oprócz częstego zginania będą również stale skręcone. Są wymagane, jeżeli kabel obraca się dookoła własnej osi i m.in. w robotach w zadaniach pick and place.
Kolejnym wyzwaniem są maszyny, które gwałtownie hamują i bardzo szybko się rozpędzają. W ich przypadku problemem są duże przyspieszenia, które nadmiernie obciążają kable, powodując skrócenie ich żywotności. W związku z tym powinny się one cechować większą sztywnością, żeby mogły wytrzymać towarzyszące zatrzymywaniu oraz rozpędzaniu naprężenia. W tym celu na przykład izolację z TPE lub PVC zastępuje się nieco mniej elastyczną z polipropylenu. Kable z tego materiału są ponadto lżejsze, co jest w takich zastosowaniach dodatkową zaletą.
Karol Lenkiewiczigus
W przypadku zastosowań przemysłowych klienci zwracają uwagę na mechaniczne aspekty budowy złączy, muszą one być odporne na wszelkiego rodzaju uszkodzenia, wibracje. Również sposób mocowanie złącza do gniazda musi być niezawodny i odporny na wiele cykli odłączania i podłączania. Dużym ułatwieniem dla obsługi jest możliwość kodowania złączy, aby uniknąć pomyłki przy podłączaniu. W kablach przemysłowych liczy się zdecydowanie odporność mechaniczna i środowiskowa. Jeśli przewody poruszają się w sposób zautomatyzowany, to muszą mieć odpowiednią żywotność, liczoną często w milionach cykli. Ważny jest odpowiedni minimalny promień zagięcia, przystosowanie do odpowiedniego zakresu temperatur oraz odporność na substancje chemiczne, na przykład oleje i chłodziwa.
W ostatnim czasie widać szybki rozwój w zakresie funkcjonalności złączy. Dużym ułatwieniem dla użytkowników jest modułowość, dzięki temu można w szybki sposób integrować wiele przewodów w jednym miejscu połączeniowym i w łatwy sposób podłączać i odłączać tylko niektóre z nich. Producenci serwonapędów wprowadzają złącza i przewody hybrydowe, łączące zasilanie, sterowanie oraz funkcje przesyłu sygnałów np. z enkodera. Zmniejsza to ilość okablowania, a co za tym idzie, ilość potencjalnych awarii. Jedno gniazdo na silniku zamiast dwóch umożliwia miniaturyzację i oszczędność na masie własnej. Nowoczesne systemy hybrydowe umożliwiają również pomiar własnego zużycia i przesyłanie tej informacji do użytkownika. |