Wprowadzenie robota na teren zakładu przemysłowego pociąga za sobą liczne konsekwencje. Są to zarówno zmiany na lepsze, jak i problemy, które dotąd były nieodczuwalne. Ponadto wiele z korzyści, ale i kłopotów związanych z pojawieniem się robota wychodzi na jaw dopiero po pewnym czasie od jego instalacji. Je także warto uwzględnić we wstępnych rachunkach opłacalności, które powinny zostać rozpoczęte od konfrontacji wydajności robota i człowieka.
Robot kontra człowiek
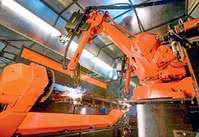
Dwa stanowiska spawalnicze z robotami ABB w Wytwórni Okuć Meblowych w Brodnicy
To co sprawia, że właściciel firmy zaczyna myśleć o zakupie robota przemysłowego, to pojawienie się w zakładzie dużej liczby powtarzających się czynności mechanicznych, które nie wymagają kreatywności. Świetnym przykładem jest paletyzacja, którą przeprowadza się w praktycznie każdym zakładzie produkującym towary. Polega ona na przenoszeniu gotowych produktów z miejsca na miejsce i układaniu ich w równych ilościach do kartonów czy na palety. Czynność ta wykonywana może być przez grupę ludzi, której liczebność zależeć będzie m.in. od wielkości bieżącej produkcji. Z racji swej szybkości i siły udźwigu roboty są w stanie znacznie sprawniej pakować produkty niż pojedynczy człowiek i często stosuje się przelicznik, według którego jeden robot wykonuje pracę trzech ludzi pracujących w tym samym czasie. W przypadku, gdy proces produkcyjny przebiega bez przerwy - tj. 24 godziny na dobę, łatwo wyliczyć, że wymaga to pracy w trybie trój- lub nawet czterozmianowym. Te trzy zmiany po trzy osoby przeliczają się na 9 etatów, za które płacić musi pracodawca. Biorąc pod uwagę koszt pensji tychże pracowników i porównując go z ceną robota, która waha się w granicach od 100 tys. do 500 tys. złotych, szybko okaże się, że inwestycja w robota zwróci się po mniej niż dwóch latach. Oczywiście, do kosztów obsługi maszyny dochodzi jeszcze pobór prądu i opłaty za serwis, a pensje pracowników zależne są od regionu, w którym mieści się zakład, i od wielu innych czynników, ale tak czy inaczej, przy wystarczająco dużym tempie produkcji, inwestycja w robota i tak będzie opłacalna.
Nie tylko koszty się liczą
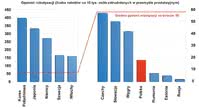
Liderzy robotyzacji przemysłowej - pięć najbardziej zrobotyzowanych państw (wykres po lewej) i państwa o dużym potencjale w zakresie robotyzacji (wybrane zostały kraje naszego regionu); źródło: IFR
Powyższe wyliczenia są tylko pierwszym etapem oceny sensu zakupu robota. Nawet jeżeli okaże się, że inwestycja nie rokuje szybkiego zwrotu poniesionych kosztów, warto rozważyć dalsze aspekty tej sprawy. Trzeba wziąć pod uwagę takie kwestie, jak urlopy wypoczynkowe i zwolnienia chorobowe pracowników, a także przypadki rezygnacji z wykonywanej pracy. Wiele z tych czynników pojawia się nagle, choć z pewną regularnością, ale mimo to je przewidzieć i skutecznie im przeciwdziałać. Jednakże niezależnie od podjętych kroków zawsze wiąże się to z dodatkowymi kosztami, które także powinny być oszacowane i uwzględnione w kalkulacji. Ich znaczenie rośnie coraz bardziej wraz z odpływem siły roboczej na zachód Europy i ze wzrostem praw przysługujących pracownikom. Częste powtarzanie tych samych czynności - szczególnie gdy w grę wchodzi dźwiganie dużych ciężarów, może być przyczyną trwałych chorób i uszkodzeń ciała. Pomimo nowoczesnych zabezpieczeń, jakie stosuje się w zakładach przemysłowych, prawdopodobieństwo wypadku nigdy nie zostało zredukowane do zera. O ile w Polsce konsekwencje takich sytuacji bywają różne, to w krajach Europy Zachodniej, a szczególnie w Stanach Zjednoczonych wiąże się to zazwyczaj z wytoczeniem procesu pracodawcy przez poszkodowanego pracownika. Należy liczyć się z faktem, że ta tendencja będzie narastała i w naszym kraju, a więc będą rosły i koszty związane z zatrudnianiem ludzi.
Naturalnie, przeciwnicy robotyzacji powiedzą, że robot też może się zepsuć i spowodować przestój w produkcji. Oczywiście jest to prawda, ale jak wskazują statystyki, odpowiednio konserwowane urządzenie przy 8-godzinnym dziennym cyklu pracy psuje się średnio raz na 100 miesięcy, czyli co ponad 8 lat. Dla porównania, zakładając, że pracownik choruje raz na rok, wśród trzech robotników, których może zastąpić maszyna, obniżenie wydajności z powodu choroby pojawia się nawet 3 razy na rok, czyli 25 razy częściej. Co więcej, firmy zajmujące się wdrażaniem robotów często mają ściśle określone czasy reakcji na awarię i naprawę usterki, dzięki czemu szacowanie ewentualnych dodatkowych kosztów jest ułatwione.
Kwestia wyuczenia i bezpieczeństwa
Nie bez znaczenia jest także czas szkolenia pracowników, który jest często znacznie dłuższy niż czas programowania robota. Kwestia ta staje się tym bardziej istotna, gdy wziąć pod uwagę konieczność zatrudniania co jakiś czas nowych pracowników, w związku z odchodzeniem poprzednich. W przypadku stosowania robotów raz napisany program - o ile tylko został zakodowany w odpowiednim języku, może po niewielkich modyfikacjach zostać wykorzystany ponownie jako podstawa do optymalizacji procesu pracy nowo instalowanego robota.
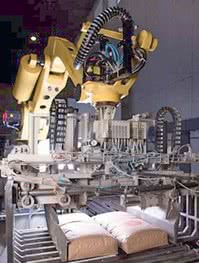
Robot FANUC Robotics pracujący w Cukrowni Strzyżów
Kolejną, często niedocenianą kwestią jest precyzja, z jaką maszyny mogą wykonywać swoje zadania. Ruchy powtarzane są przez nie z dokładnością do ułamków milimetra, co sprawia, że efektem ich pracy są produkty o znacznie wyższej jakości. W przypadku paletyzacji precyzyjne ułożenie towaru ma zazwyczaj marginalne znaczenie, choć istnieją czynniki, które od ułożenia zależą. Poprawnie ułożony towar jest korzystniej postrzegany przez kontrahentów i lepiej nadaje się do dalszej obróbki za pomocą wszelkiego rodzaju maszyn. Ponadto niedokładne rozłożenie towaru na paletach może być przyczyną rozpadnięcia się całej paczki, co powoduje konieczność ponownej paletyzacji, a także stanowi zagrożenie dla pracowników zakładu. W bardziej wymagających aplikacjach powtarzalność wykonania produktu sprawia, że będzie on spełniał różnego rodzaju normy, przy mniejszych nakładach związanych z wprowadzaniem marginesów błędów produkcyjnych. Dobrym przykładem może być spawalnictwo, w którym wykorzystanie robota nie tylko przyspiesza prace i zwiększa powtarzalność procesu produkcyjnego, ale także ogranicza zużycie drutu spawalniczego, co wpływa na zmniejszenie kosztów spawania.
Ostatnią kwestią do rozważenia jest bezpieczeństwo produkcji, które zagrożone jest głównie przez wprowadzenie do procesów czynnika ludzkiego. Problem ten jest szczególnie istotny w fabrykach produktów spożywczych oraz farmaceutyków. Procesy produkcyjne w takich zakładach wymagają zachowania wysokich standardów czystości, a głównym problemem są zanieczyszczenia wprowadzane na teren zakładu przez pracowników. Zastąpienie ludzi robotami stale znajdującymi się w hali produkcyjnej znacznie ogranicza liczbę wejść i wyjść ludzi na teren produkcji, redukując tym samym ilość wprowadzanych przez nich zabrudzeń. Nie bez znaczenia jest także bezpieczeństwo dotyczące potencjalnych sabotaży oraz kradzieży produkowanych dóbr. Dobrym przykładem walki z tym procederem jest instalacja robotów na liniach butelkowania i pakowania alkoholi.
Mikro- i makroekonomia
Robotyzacja zakładów produkcyjnych pociąga za sobą także inne konsekwencje ekonomiczne, często znacznie trudniejsze do oszacowania. Pierwszą z nich będzie wzrost prestiżu, jaki wiąże się z wprowadzeniem nowoczesnych maszyn do procesów wytwarzania. Niekiedy wrażenie, jakie robi dobrze zorganizowana i zautomatyzowana fabryka, jest silną kartą przetargową w negocjacjach biznesowych i może stanowić atut decydujący o realizacji kontraktów. Istotny jest także wzrost jakości finalnych produktów, jaki zawsze się wiąże z robotyzacją zakładu. Kwestia ta w obecnej sytuacji gospodarczej Polski jest bardzo istotna. Wyrobienie sobie zawczasu dobrej renomy opartej na wysokiej jakości produktów sprawi, że istniejące w Polsce zakłady będą w przyszłości lepiej postrzegane. Jako przykład państwa o negatywnej opinii na temat jakości można podać Chiny. Państwo to jest co prawda potęgą, jeżeli chodzi o ilość produkowanych tam towarów, ale jednocześnie synonimem różnej jakości wyrobów. Nierzadko można bowiem spotkać się z deklaracjami producentów, którzy zapewniają, że ich sprzęt nie jest produkowany w Chinach, ale np. w Japonii czy choćby Korei.
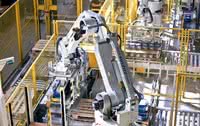
Roboty marki Kawasaki w Fabryce Farb i Lakierów Śnieżka
Mówiąc o kwestiach ekonomicznych, warto zwrócić uwagę na temat funduszy europejskich, które są dla przedsiębiorców coraz trudniejsze do zdobycia. W 2013 roku skończył się poprzedni okres budżetowy UE, zaś do 2020 dotacji ma być znacznie mniej i mają one być stopniowo zastępowane pożyczkami. Oczywiście nie jest to na rękę przedsiębiorcom, bo będzie to wymagało od nich wykazania zdolności kredytowej, podobnie jak przy kredytach komercyjnych, i oddania z czasem udzielonego wsparcia. Szefowie firm, starając się o fundusze, będą musieli również udowodnić, że taka pomoc jest im rzeczywiście potrzebna. To wymyślony przez Brukselę tzw. efekt zachęty. Teraz tylko więksi przedsiębiorcy muszą udowadniać, że bez unijnego wsparcia nie mogą prowadzić inwestycji - w niedługim czasie będą to robiły też małe i średnie firmy.
Przedsiębiorstwa nie dostaną już pieniędzy na każdy projekt, ale tylko na wybrane działania. Na przykład większość z wartego blisko 10 mld euro programu operacyjnego "Inteligentny rozwój" trafi tylko do tych przedsiębiorców, którzy chcą prowadzić badania, dopracowywać kupione technologie albo wypuszczać na rynek nowe produkty. Niektóre instrumenty, np. kredyt technologiczny, mają być dostępne tylko dla mniejszych firm.
Zmienią się także zasady dotyczące
Linia technologiczna z robotami Comau w Fiat Auto Poland