WYRÓWNANIE BŁĘDU KARETKI ŁADUNKOWEJ
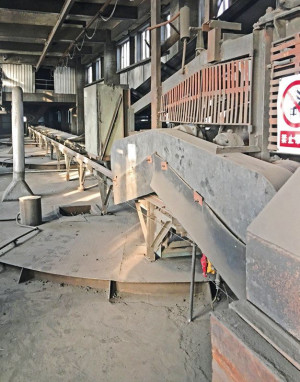
Fot. 1. Gorąca lokalizacja: Prawidłowe położenie wózka jest niezawodnie wykrywane za pomocą RFID, co eliminuje problem poślizgu
Producent węglika musiał pilnie zoptymalizować proces produkcji. Wózek szynowy do podawania surowca w piecu węglikowym musiał być prawidłowo wyrównany z drzwiami ładunkowymi. W poprzednim rozwiązaniu mierzono położenie wózka za pomocą enkodera.
Częste przyspieszanie, hamowanie i zatrzymywanie wózka powodowało czasem jego niewielkie przesunięcie. Odległość poślizgu nie była mierzona przez enkoder, więc dane pozycji enkodera nie były poprawne. Z tego powodu występowała rozbieżność pozycji wózka względem drzwi ładujących.
W momencie wystąpienia takiej rozbieżności wymagało się od personelu ręcznej interwencji. Obszar otaczający drzwi ładunkowe jest bardzo gorący, ponieważ piec znajduje się bezpośrednio pod nim. Ponadto jest to środowisko zapylone, wysoce łatwopalne i wybuchowe.
Trudne warunki występujące w tym obszarze oznaczają, że personel musi nosić specjalistyczny sprzęt ochronny i jest narażony na znaczne niebezpieczeństwo. Z racji tego nie jest to środowisko, w którym pracownicy chcieliby często przebywać.
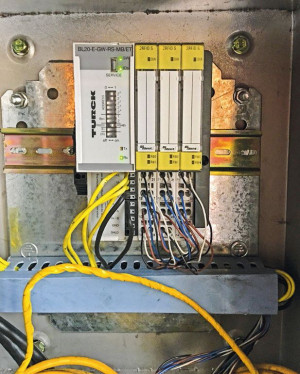
Fot. 2. Urządzenie BL20 z połączeniem RS-485 zapewnia komunikację z kontrolerem, a moduł RFID-S umożliwia łatwe sterowanie bez konieczności programowania
Właściciel zakładu wybrał więc rozwiązanie RFID do pozycjonowania wózka do ładowania. Rozwiązanie składa się z trzech nośników RFID zamontowanych na wózku ładującym: jeden przy otworze wózka i po jednym w określonej odległości przed i za otworem w celu wskazania pozycji. Głowica odczytująco-zapisująca jest umieszczona na szynie w miejscach występowania wszystkich drzwi do ładowania.
Jeśli wózek porusza się po szynach, nośniki po obu stronach otworu wózka przesuwają się nad głowicą odczytująco-zapisującą przy drzwiach do ładowania. Głowica odczytuje informacje z nośników i wysyła sygnał zwrotny do kontrolera, który następnie spowalnia wózek ładowania.
Jeżeli znacznik na otworze karetki znajduje się naprzeciwko głowicy odczytująco-zapisującej przy drzwiach do ładowania, głowica czytająca wyprowadza informację z nośnika. Po otrzymaniu informacji przez kontroler wózek jest zatrzymywany, a materiał podawany.
Wykonuje się to w ułamkach sekundy, a prawidłowe położenie wózka jest gwarantowane niezawodnym systemem pozycjonowania RFID. Wszelkie ręczne korekty i związane z tym niedogodności są w ten sposób znacznie ograniczone.
W skróciePozycja wózka do ładowania w zakładzie produkcyjnym była wcześniej określana przez enkoder na kole wózka. Jednak odbierane informacje stawały się coraz bardziej niepoprawne z powodu poślizgu podczas przyspieszania i hamowania, powodując konieczność ręcznego korygowania pozycji. Obecnie producent mierzy pozycję za pomocą znaczników RFID na wózku i głowicy odczytująco-zapisującej zamontowanej na szynach transportowych. Umożliwia to niezawodne umieszczenie wózka przed drzwiami ładującymi. Ani głowica odczytująco-zapisująca IP67, ani wytrzymałe nośniki RFID nie są uszkadzane przez kurz i ciepło w procesie produkcyjnym. Obecnie zakład działa z większą wydajnością energetyczną, podczas gdy pracownicy pracują w bezpieczniejszym środowisku. |
KONCEPCJA ROZWIĄZANIA Z BLIDENT
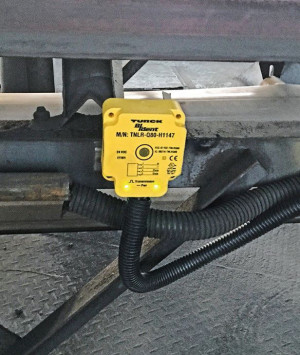
Fot. 3. Ze stopniem ochrony IP67, rozszerzonym zakresem temperatur i dużymi zakresami odczytu/zapisu, głowice TNLR-Q80 są optymalnie zaprojektowane do użycia na gorącej linii ładowania
Ponieważ klient korzysta z systemu kontroli procesu Supcon, interfejs RS-485 jest już dostarczony na miejsce instalacji. Firma Turck dostarczyła zatem bramkę sieciową BL20, która obsługuje RS-232/RS-485. Ponieważ znaczniki są używane tylko do wskazania pozycji, wymagania dotyczące danych są bardzo małe.
Moduł RFID-S, który można łatwo zintegrować, jest całkowicie wystarczający. Klient nie wymaga programowania w PLC dla S-Interface (S oznacza Simple - łatwe). Interfejsy RFID mogą być używane jako standardowe wejścia. Ponieważ miejsce instalacji narażone jest na znaczne zapylenie, użytkownik musiał zainstalować moduł komunikacyjny i moduły I/O w szafie ognioodpornej.
Głowice do odczytu i zapisu o stopniu ochrony IP67 są odpowiednie do stosowania w temperaturach od -25 do +70°C i można je montować bezpośrednio w miejscu instalacji. Etykiety wykonane są z żywicy epoksydowej i są wyjątkowo wytrzymałe. Nawet jeśli powierzchnia jest porysowana lub brudna, jej funkcja nie jest osłabiona.
WNIOSEK
Dzięki zastosowaniu systemu identyfikacji RFID firmy Turck, operator może zwiększyć moce produkcyjne zakładu i dokonać znacznej poprawy w zakresie oszczędności energii i bezpieczeństwa oraz zmniejszenia zużycia w tym samym czasie.
W związku z jeszcze bardziej rygorystycznymi wymaganiami dotyczącymi dokładnego pozycjonowania, klient zamierza również korzystać z rozwiązania RFID w innych częściach zakładu produkcyjnego. Rozwiązanie RFID oferuje szerokie możliwości rozwoju w tej dziedzinie.
Turck
Więcej na www.turck.pl