Produkcja tabletek musujących
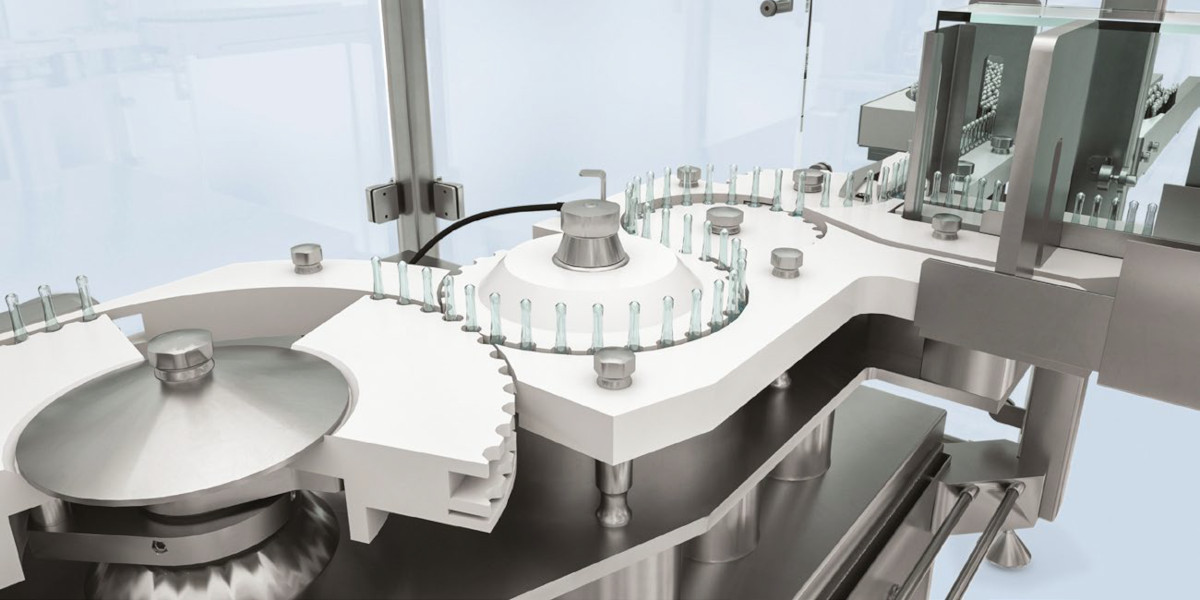
Tabelki musujące to rozwiązanie pośrednie między tymi do łykania a lekami w płynie, pozwalające ominąć ograniczenia tabletek (wolne wchłanianie składnika aktywnego) i płynów (ograniczona stabilność składnika aktywnego). Ich zalety to także: możliwość poprawy smaku przez dodatki i łagodniejsze działanie na żołądek. Są także odbierane jako atrakcyjniejsze przez konsumentów. Wymagają jednak dostosowania technik i urządzeń w produkcji do ich specyfiki.
Pierwsze wyzwanie to transport surowców – te używane w produkcji tabletek musujących są higroskopijne, czyli pochłaniają wilgoć z otoczenia. To jest niepożądane, ponieważ wywołuje reakcję musowania. Trzeba je więc izolować od otoczenia. Rozwiązanie to zamknięty system transportu i przechowywania. Jego część to specjalne pojemniki i zawory gwarantujące wysoki stopień hermetyczności. W przykładowej realizacji te drugie w wersji dzielonej obejmują dwa półzawory niezależnie uszczelniające dwa pojemniki. Są dołączane i otwierane przez siłownik. Kiedy oba półzawory są odłączone i zamknięte, nie dopuszczają do wydostawania się zawartości z pojemników. Gdy są podłączone, ale wciąż zamknięte, są połączone, nadal jednak zapewniając szczelność zbiorników. Po otwarciu półzawory działają jak jeden zawór motylkowy. To pozwala na załadunek i rozładunek produktu w sposób hermetyczny. Trzeba też dopilnować, by powietrze na stanowisku przeładunku surowców do produkcji tabletek musujących nie było zawilgocone.
Michał Podgórski
Cleanproject
Projektujemy i budujemy pomieszczenia typu clean room aż do klasy GMP A, natomiast w klasyfikacji ISO-14644 – do klasy ISO 4. Parametry te kojarzone są z wymagającymi procesami w farmacji, biotechnologii czy fotolitografii. Wysoka czystość, sterylność, kontrola wilgotności i temperatury w wąskich zakresach są bardziej wymagające i pojawiają się także w mniej oczywistych aplikacjach czy branżach – np. w branży spożywczej. Warto zwrócić uwagę, że najtrudniejsze do osiągnięcia jest nie tyle uzyskanie wymaganych parametrów środowiska wytwarzania, a ich utrzymanie w trakcie procesu. Ponieważ oczekiwane parametry muszą być utrzymywane nieustannie, to niezwykle ważne jest by zrozumieć proces, który zabezpieczamy, połączyć technologię z procedurami i szkoleniami, utrzymaniem strefy czystej oraz serwisem. Liczą się oczywiście wybory projektowe, wyposażanie sprzętowe, automatyzacja, jednak sukces daje koherentność i systematyczna przemyślana praca. To właśnie w mojej ocenie jest kluczowe w naszej pracy i pracy naszych klientów.
Cechą charakterystyczną są systemy szczelnych zabudów połączone z rozwiązaniami HVAC. Praktycznie każda strefa czysta łączy w jakiś sposób zabudowę/obudowę obszaru z oczyszczaniem, ogrzewaniem lub schładzaniem powietrza czy też utrzymaniem odpowiedniego poziomu wilgotności. Bardzo ważne jest także odpowiednie wyposażanie, tj. systemy utrzymania czystości, mierniki, odzież, meble, itp. W zależności od wymagań procesowych i parametrów środowiskowych dostępne są różne rozwiązania technologiczne – od komór laminarnych, poprzez pomieszczenia typu BOX po obiekty budowalne o powierzchniach tysięcy metrów kwadratowych z specjalistycznym sprzętem, takim jak centrale wentylacyjne, osuszacze, nawilżacze, itd. O wyborze konkretnych rozwiązań decyduje przede wszystkim proces jaki zamierzamy w strefie czystej prowadzić. Zrozumienie i umożliwienie skutecznego prowadzenia procesu jest najważniejsze. |
Jak się produkuje granulat?
Kolejne wyzwanie to etap granulacji. Jest wymagana, by zapewnić jednorodne surowce, co gwarantuje, że tabletki formowane w prasach tabletkarek będą miały jednakową zawartość substancji aktywnych. Ponieważ granulacja na mokro inicjuje reakcję musowania, stosowane są alternatywne metody suche: ugniatanie, bezpośrednie prasowanie i zagęszczanie walcami, które jednak wymagają drogich substancji pomocniczych. To zwiększa koszty, bo tabletki musujące są zwykle duże. Dlatego wprowadza się modyfikacje granulacji na mokro. Najważniejszą jest zastąpienie wody rozpuszczalnikami organicznymi niewywołującymi musowania. Dzięki temu uzyskuje się: niższe ciepło parowania, wysoką przepustowość i możliwość suszenia w niższych temperaturach. Wady wynikłe ze zmiany płynu granulacyjnego to z kolei: konieczność zmian w sprzęcie, złożony system oczyszczania spalin, zagrożenie wybuchem. Jeśli jednak używa się wody, dopuszczalne są tylko jej niewielkie ilości. Wtedy oczywiście zachodzi musowanie. Powstająca, oprócz dwutlenku węgla, woda podtrzymuje tę reakcję. Dlatego cykl trzeba przerwać rozpoczynając suszenie, które powinno usuwać wodę szybciej, niż będzie jej przybywać w efekcie musowania. Ta technika jest niestety problematyczna przy większych partiach produktu.
Maszyny specjalistyczne w produkcji tabletek musujących
Granulacje przeprowadza się w różnego typu granulatorach, na przykład w szybkotnącym. Urządzenie tego typu zbudowane jest z: misy mieszającej lub bębna, wirnika, rozdrabniaczy, napędu, wlotu do załadunku oraz wylotu wyładowczego. Misę wypełnia się sproszkowanym surowcem i szczelnie zamyka. Najpierw uruchamia się wirnik obracający się z dużą prędkością – typowo od 100 do 1500 obr./min, w osi pionowej lub poziomej, w zależności od konstrukcji. Jego zadaniem jest wymieszanie suchych składników. Następnie dodawana jest ciecz granulująca, którą wirnik, obracając się, rozprowadza w całej objętości granulatora. Do rozbijania powstałych w efekcie większych, mokrych brył surowca i zbijania mniejszych w większe w celu wytworzenia granulek służą szybko obracające się rozdrabniacze, które wirują z prędkością od 1000 do 3000 obr./min. Mieszanie kontynuuje się aż do uzyskania pożądanej wielkości granulek i ich gęstości. Dla efektywności granulacji kluczowe znaczenie ma konstrukcja wirnika i rozdrabniaczy oraz miejsce ich montażu – najlepsze efekty osiąga się zwykle, jeżeli wirnik jest zamontowany na spodzie, a rozdrabniacz z boku, ponieważ taka konfiguracja eliminuje martwe punkty i zapewnia jednorodność granulatu.
Kolejnym etapem jest tabletkowanie przeprowadzane w... tabletkarkach. Są to maszyny, w których granulaty są sprasowywane oraz formowane do postaci krążka. Wyróżnia się dwa typy tabletkarek: z pojedynczym wykrojnikiem oraz prasy wielostanowiskowe (rotacyjne). Ich główne komponenty to: para stempli, górny i dolny, i matryca. W pierwszych dolny stempel jest zwykle nieruchomy, a górny wywiera siłę w celu uformowania tabletki, w rotacyjnych zaś poruszają się zarówno górny, jak i dolny stempel. Drugie charakteryzuje znacznie większa wydajność produkcji. Zależnie od wzoru stempla i kształtu matrycy tabletki mogą mieć różne kształty i wymiary. Oprócz stempli ściskających mieszankę tabletkową i matrycy, w obrębie której krążek jest formowany, częścią tabletarek z pojedynczym wykrojnikiem są: zbiornik z granulatem i jego dozownik. Maszyny rotacyjne wyposażone są dodatkowo w: mechanizm rozprowadzający masę tabletkową do poszczególnych wnęk matrycy, rolki dociskowe usuwające jej nadmiar, zbierak, który prowadzi tabletki wyrzucone z matrycy przez dolne stemple do rynny wyładowczej. Do pakowania tabletek musujących używa się tub z tworzywa sztucznego i blistrów aluminiowych.
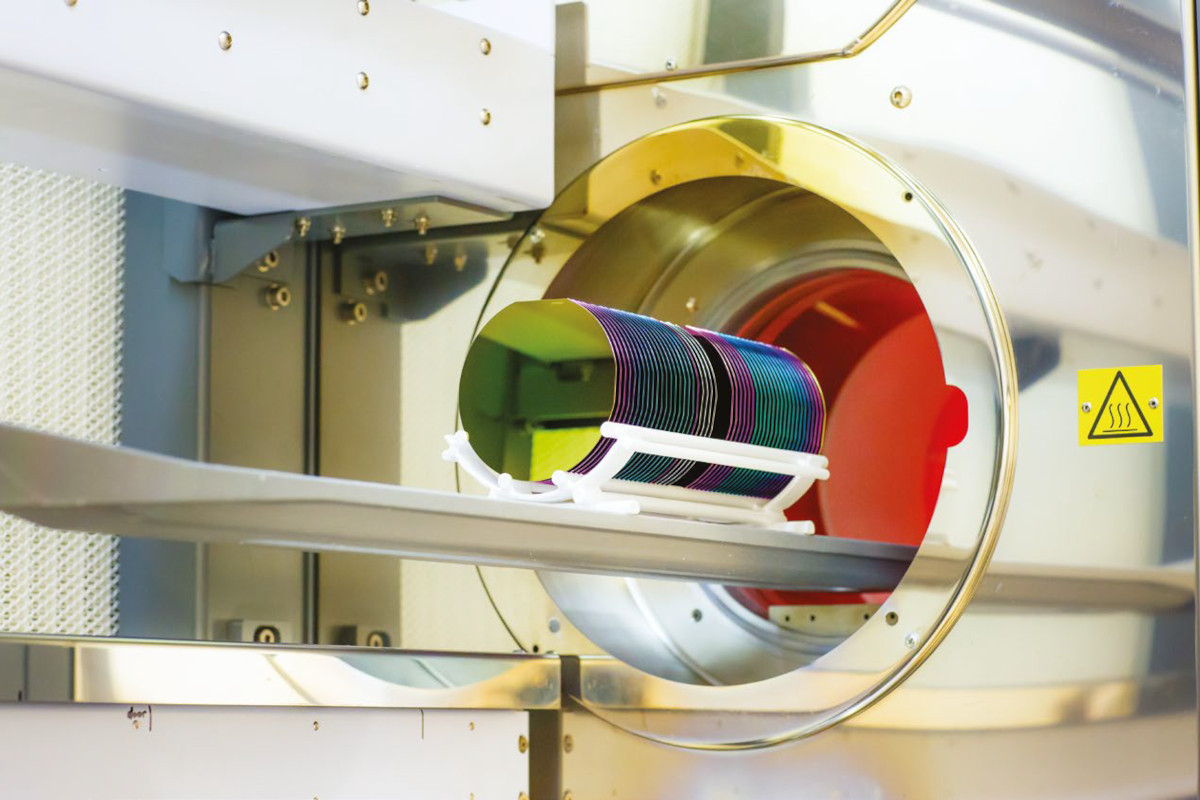
Monika Jaworowska