Zdjęcie tytułowe: Pracownicy firmy (od lewej): Rainerem Rösselem, Karolem Kozłowskim i Michałem Krzysztofiakiem |
Niemiecki igus to producent prowadników kabli i przewodów do aplikacji ruchomych, a także polimerowych łożysk ślizgowych oraz liniowych systemów prowadzenia. Są one wytwarzane z odpornych na ścieranie tworzyw sztucznych, które firma określa mianem "trybopolimerów". W tym roku igus obchodzi 25-lecie marki Chainflex, która obejmuje kable do aplikacji w ruchu i zastosowań w prowadnikach kablowych.
Z tej okazji, a także ze względu na premierę nowych kabli z wbudowanymi modułami pomiarowymi, spotkaliśmy się z przedstawicielami firmy w zakładzie produkcyjnym w Kolonii. Jest to największa jednostka produkcyjna igusa, gdzie prowadzone są też m.in. prace R&D i znajduje się duże laboratorium testowe. O tym ostatnim oraz o budowie i zastosowaniach kabli do aplikacji w ruchu rozmawialiśmy z Rainerem Rösselem, który odpowiada w firmie za dział biznesowy Chainflex.
- Czym kable do aplikacji w ruchu różnią się od wersji standardowych przeznaczonych do zastosowań w instalacjach stałych - np. w okablowaniu strukturalnym?
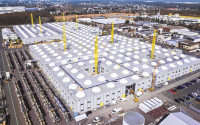
Zakład igusa w Kolonii, gdzie rozmawialiśmy z pracownikami firmy
Kable to produkty, które na pierwszy rzut oka wydają się bardzo podobne do siebie. Zgodnie z definicją kablem elektrycznym nazywamy rodzaj izolowanego przewodu jedno- lub wielożyłowego, który może być otoczony wspólną powłoką. Końce przewodów są podłączane do urządzenia lub innego podzespołu - i tyle definicji słownikowej.
Większość kabli stosowanych jest w instalacjach stałych, takich jak te podziemne czy jako okablowanie strukturalne. W tym przypadku ich cechy są ściśle określone w normach branżowych i takimi wyrobami praktycznie się nie zajmujemy. Tym, co nas żywo interesuje, są natomiast kable specjalistyczne.
Stosowane są one do różnych celów i występują w wielu wykonaniach pod względem przekrojów i typów żył, stosowanej izolacji, odporności środowiskowej i mechanicznej. Ich aplikacje obejmują pracę w maszynach, zasilanie urządzeń będących w ruchu, wykorzystanie w robotach, bębnach kablowych, systemach elektryczno-pneumatycznych i innych. W tym asortymencie istnieje dużo produktów, ale też nie ma standaryzacji takiej, jak w zakresie kabli standardowych.
Najważniejszą dla nas grupą są kable specjalistyczne do pracy w ruchu w prowadnikach kablowych e-chain. Ich kluczowymi cechami są przede wszystkim: wytrzymałość na zginanie, liczona liczba ruchów w prowadniku kablowym, minimalny promień gięcia oraz odporność środowiskowa. Wiele takich przewodów wykonujemy na zamówienie klientów, tj. bezpośrednio do ich aplikacji, przez co czas produkcji wydłuża m.in. proces dodatkowego testowania.
Do tego ostatniego przykładamy bardzo dużą wagę, bowiem uszkodzenia kabla w maszynach mogą być bardzo kosztowne. Znamy przypadek, gdy na skutek degradacji standardowego, taniego kabla wystąpił pożar w maszynie produkcyjnej, a straty z tym związane wielokrotnie przewyższały skalę pierwotnych oszczędności.
- Jaki jest asortyment kabli specjalnych oferowanych przez igusa?
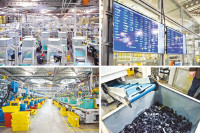
Znaczącą część zakładu produkcyjnego zajmują wtryskarki - firma korzysta z ponad 350 tego typu maszyn
Dostarczamy kable do aplikacji w ruchu praktycznie do wszystkich zastosowań maszynowych i innych. Obejmuje to połączenia silnoprądowe, sterownicze, komunikacyjne, silnikowe i serwosilnikowe, pomiarowe oraz światłowodowe. Nasze kable stosowane mogą być w aplikacjach obejmujących od prostych systemów ruchu liniowego - np. w zakurzonych obrabiarkach drewna, do złożonych aplikacji 3D w robotach w pomieszczeniach cleanroom, gdzie używane są kable do ruchów skrętnych.
Weźmy dla przykładu gamę kabli ethernetowych do zastosowań w naszych prowadnikach. Obejmuje ona 30 rodzajów przewodów miedzianych oraz wersje światłowodowe, które doskonale nadają się do pracy z niewielkimi promieniami gięcia. Oferujemy do tego kilkaset typów wstępnie zmontowanych kabli ethernetowych - przykładowo serię nowych e-prowadników triflex do robotów przemysłowych oraz wydajne transmisyjne kable optyczne z systemem micro flizz.
Oprócz tysiąca kabli katalogowych rokrocznie wprowadzamy drugie tyle wersji specjalizowanych. Wiele z nich powstaje na bazie zapytań od naszych klientów. Jeżeli zaś chodzi o te katalogowe, to występują one w kilkunastu - dokładniej w 13 typach pod względem budowy i żywotności. Jeżeli weźmiemy dla przykładu kable do aplikacji ruchomych z czterema żyłami po 0,5 mm², to najtańszą wersją jest przewód z PVC nieodporny na oleje, z promieniem gięcia wynoszącym 15-krotność średnicy i gwarantowaną niezawodnością pięciu milionów cykli gięć. Tego typu kabel kosztuje 2,10 zł za metr.
Z kolei na drugim biegunie jest analogiczny do powyższego produkt wykonany z TPE, o odporności na wszystkie typowe substancje zewnętrzne i cechujący się minimalnym promieniem gięcia wynoszącym czterokrotność średnicy. Nie ma on miedzi - zamiast niej stosujemy wytrzymały mechanicznie stop, zaś kabel ten osiągnął podczas testów żywotność wynoszącą ponad 140 mln zgięć w prowadniku. Choć jego cena wynosi 117,25 zł za metr, również znajduje on zastosowania w aplikacjach specjalnych.
Szerokie portfolio jest konieczne, bowiem zapewnia klientom możliwość doboru kabli precyzyjnie do ich potrzeb. Jednocześnie, gdy w przemyśle coraz częstsza jest miniaturyzacja maszyn, a promienie gięcia połączeń są coraz mniejsze, zwiększają się też wymagania stawiane producentom maszyn. Również rosną szybkości pracy urządzeń - na wszystkie te zmiany staramy się odpowiadać, oferując nowe rodzaje wyrobów. W procesie tym szukamy jak najlepszej równowagi pomiędzy parametrami i żywotnością kabli a ich kosztami.
- Podczas spotkania mieliśmy możliwość praktycznego porównania kilku rodzajów kabli do pracy w ruchu. Jakie są cechy charakterystyczne i budowa tych wytwarzanych przez igusa?
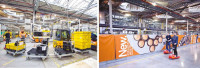
Ze względu na dużą powierzchnię zakładu do transportu wewnętrznego stosowane są różne rodzaje wózków
Różnice w obrębie asortymentu naszych przewodów, a także między produktami igusa a konkurencyjnymi są znaczne. Oprócz materiałów stosowanych do samych przewodników i izolacji - bazujących głównie na różnych mieszankach PCV, poliuretanu oraz TPE, wiele z nich dotyczy budowy kabli. Rozwiązania przez nas stosowane mają na celu zapobieganie uszkodzeniom przewodów i zagwarantowanie, że maszyny nie będą zatrzymywane podczas ich pracy.
Przykładowo kable wielożyłowe do maszyn mają budowę bazującą na kilku pękach (warkoczach) przewodów w jednym kablu. W przeciwieństwie do standardowych kabli, gdzie wszystkie żyły są skręcone w jeden pęk, zastosowanie kilku mniejszych grup zmniejsza siły ściskające i rozciągające na poszczególne żyły przy ruchu kabla, a w efekcie minimalizuje występowanie tzw. efektu korkociągu. Ten ostatni powoduje zwijanie się całego kabla, co występuje na skutek zmian długości żył wewnętrznych.
Wewnątrz płaszcza naszych kabli występuje struktura chropowata przypominającą skórę węża, która powstaje na skutek wytłaczania płaszcza pod wysokim ciśnieniem. W standardowych przewodach ze skrętem warstwowym płaszcze są gładkie, natomiast użycie wersji chropowatej blokuje możliwości ruchu żył w izolacji, zapobiegając ich degradacji. Ponieważ jednak tego typu produkt jest trudniejszy w przypadku ściągania izolacji, nasze kable wyposażamy w wewnętrzny sznurek - CFRIP, który pozwala na ich rozbieranie bez użycia specjalistycznych narzędzi.
W środku naszych niektórych kabli w ich osi znajduje się wytrzymały sznur - w przypadku występowania naprężeń przenosi on te siły, dzięki czemu nie oddziałują one na żyły przewodzące. Inną z ciekawostek jest ta dotycząca kabli do ruchów skrętnych. Ich zastosowania są zupełnie inne niż w przypadku wersji do ruchów liniowych, gdzie kabel nadąża za ruchem prowadnika. Tego typu kable, szczególnie w przypadku wersji ekranowanych, źle się skręcają, stąd też wersje do ruchów 3D są konstrukcyjnie zupełnie inne.
- Jakie są normy dotyczące testowania kabli do pracy w ruchu?
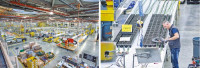
Procesy montażu gotowych systemów readychain i innych produktów na zamówienie
W przypadku kabli specjalnych istnieje kilka istotnych norm związanych z ich testowaniem, aczkolwiek aplikacje ruchome wymagają naszym zdaniem czegoś więcej, niż tylko testów w nich wskazanych. Dlatego oprócz standardowych testów zdefiniowanych w normach wykonujemy również inne badania i testy zmęczeniowe w naszym laboratorium testowym.
Weźmy dla przykładu test odpornościowy na ścieranie płaszcza. W normie wskazano, że należy go wykonać, stosując ostry element - np. jakieś narzędzie. Uważamy, że to zdecydowanie za mało, stąd też stawiamy na testy ścieralności w realnych aplikacjach - bezpośrednio w prowadnikach kablowych. Z kolei test na elastyczność i giętkość przewodu wykonywany jest wg normy poprzez przewijanie obciążonego kabla w bloczkach. Czy taki ruch ma coś wspólnego z pracą w warunkach w prowadniku?
Aby odpowiedzieć na powyższe pytanie, poddaliśmy testom jeden z kabli naszego konkurenta, który był przewidziany na 17 mln zgięć zgodnie z normą. Gdy przewód ten umieściliśmy w prowadniku kablowym, to po 73 tys. podwójnych cykli zgięć zaczął się w nim wytwarzać efekt korkociągu, natomiast po 157 tys. cykli uszkodzenia były bardzo duże i zakończyliśmy test!
Sądzimy, że jedynym miarodajnym parametrem dotyczącym żywotności jest liczba cykli pracy w prowadniku, a nie przewijania przez bloczki. Podobnie jest z testowaniem w warunkach obniżonej temperatury. To z kolei przeprowadza się zgodnie z EN 60811-504, a sam test polega na nawijaniu schłodzonego przewodu na tubę i sprawdzeniu, czy nie pękł płaszcz zewnętrzny. Oprócz tego sprawdzenia wolimy przeprowadzić realny test długoterminowy w komorze chłodniczej.
Dodam, że know-how w zakresie testowania jest krytyczne, jeżeli chodzi o opracowywanie nowych produktów. Przykładowo samo stworzenie nowego materiału może zająć nawet 5 lat, gdyż wymaga ono testów i wprowadzania zmian inkrementalnych. Proces ten jest tym dłuższy im niższe temperatury pracy przewodów i prowadników, mniejsze ich promienie gięcia czy większe prędkości przesuwu.
- Czy ze względu na Wasze doświadczenie w testowaniu nie chcieliście wprowadzić na bazie tego normy? Jaka jest, podsumowując, skala biznesu związanego z biznesem kablowym?
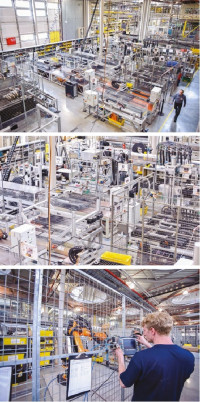
Laboratorium testowe - to tutaj wykonywanych jest rocznie około dwów miliardów cykli testowych prowadników i przewodów
O stworzeniu nowych norm rozmawialiśmy z odpowiednimi jednostkami, jednak głównym problemem jest to, że norma zawsze stanowi jakiś kompromis. Innymi słowy, opisywane w niej procedury testowania muszą być na tyle uogólnione, aby mogli z nich korzystać różni producenci. Taki kompromis oddalałby nas od naszego celu, którym jest zapewnianie nie tyle przewodów "teoretycznie zgodnych" ze standardami, ale przede wszystkim praktycznie sprawdzonych w aplikacjach, w ich rzeczywistym środowisku pracy.
Testując nasze przewody w prowadnikach kablowych, jesteśmy pewni co do ich jakości i długoterminowej wytrzymałości. Jesteśmy też jedynym producentem, który w przypadku omawianych przewodów daje trzy leta gwarancji oraz gwarancję żywotności wynoszącą do 10 milionów podwójnych cykli ruchu.
Jeżeli chodzi o obroty związane ze sprzedażą przewodów do aplikacji ruchomych, to w zeszłym roku wyniosła ona w przypadku igusa około 100 mln euro. Jest to dla nas biznes coraz istotniejszy, który stanowi obecnie 20% całych naszych obrotów globalnie.
- Porozmawiajmy o odwiedzanym przez nas zakładzie produkcyjnym. Co jest w nim wytwarzane i jakie operacje wykonujecie? Skąd pomysł na nietypowy wygląd budynku?
Zakład igusa w Kolonii, gdzie mieści się siedziba firmy, to nasza największa jednostka produkcyjna. Na powierzchni ponad 36 tys. m² prowadzimy produkcję oraz testy i badania. Fabryka była od czasu jej budowy dwie dekady temu rozbudowywana i przenoszone tu były kolejne działy - m.in. R&D, marketing, produkcja form oraz dział szkoleń technicznych.
Znajduje się tu również duże centrum logistyczne. Zakład charakteryzuje się nietypowym projektem architektonicznym. Budowa modułowa zapewnia możliwość łatwego przemieszczania się i komunikowania pracowników oraz rozbudowy fabryki.
Jeżeli chodzi o samą produkcję, to wytwarzane są różnorodne elementy z tworzyw sztucznych, w których się specjalizujemy. Posiadamy ponad 350 maszyn do wtrysku tworzyw sztucznych, które pracują w trybie ciągłym, korzystamy również z około 40 tys. form wtryskowych. W większości produkowane są elementy modułowe, dzięki czemu nie ma konieczności utrzymywania dużych stanów magazynowych. Produkcja odbywa się na bieżąco, co pozwala nam pracować zgodnie z zasadami Lean, a ponad 90% naszych wyrobów jest wysyłanych do klientów w terminie 24-48 godzin od zamówienia.
O ile dział wtryskarek jest wysoce zautomatyzowany, o tyle dalsze procesy montażu produktów są zazwyczaj manualne. Tak jest szczególnie w przypadku produktów readychain, gdzie klient ma możliwość zamówienia prowadnika na wymiar, z zamontowanymi przewodami. Oferujemy też gamę wyrobów readycable, a więc kabli ze złączami. Aby móc je szybko dostarczać, utrzymujemy stany magazynowe obejmujące ponad 3 tysiące różnych komponentów złączy! Po wyprodukowaniu zamówionego produktu przechodzi on kilkuetapowy proces kontroli jakości oraz testowania.
- Ważną częścią zakładu jest laboratorium testowe prowadników i przewodów...
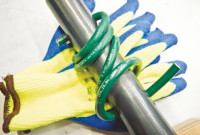
Praktyczne sprawdzanie kabli jest w igusie traktowane bardzo poważnie - odwiedzając firmę, otrzymaliśmy zestaw kabli i narzędzi do własnoręcznego wykonania testów
Zdecydowanie tak jest! Testy produktów odbywają się na wielu etapach ich wytwarzania, aczkolwiek z punktu widzenia jakości produkcji i rozwoju nowych wyrobów najważniejsze jest dla nas właśnie laboratorium testowe. Stworzyliśmy największą tego typu jednostkę w branży - ma ono ponad 2700 m² i korzystamy w nim z blisko 60 maszyn testujących. Żartobliwie mówimy, że wszystkie one służą do niszczenia kabli, jednak cel przeprowadzania testów jest jak najbardziej poważny - pozwalają nam one rozwijać nowe technologie, sprawdzać materiały i rozwiązania oraz testować gotowe produkty.
W laboratorium korzystamy z wielu rodzajów prowadników o długościach od dziesiątek centymetrów do kilkuset metrów oraz o różnych promieniach gięcia. Urządzenia te wykonują ruchy w trybie ciągłym, do tego korzystamy z dwóch robotów pozwalających na testowanie przewodów do pracy 3D. Elementem laboratorium jest komora chłodnicza o powierzchni 20 m², gdzie w temperaturach od -40 do 60°C testujemy prowadniki z przewodami. Odwzorowujemy w ten sposób możliwe warunki ich pracy, dodatkowo też testujemy odporność na oleje i inne substancje.
W ciągu roku w laboratorium wykonujemy sumarycznie dwa miliardy cykli testowych. Oprócz sprawdzania nowych konstrukcji i materiałów wykonujemy testy partii produkcyjnych przewodów. W tym przypadku wykonujemy minimum 200 tys. cykli testowych, a następnie przewody są rozbierane i badane pod kątem jakości.
Z uzyskiwanych wyników korzystamy na bieżąco w naszych narzędziach do projektowania i doboru kabli. Obliczenia okresu eksploatacji wykonywane na bazie danych testowych pozwalają nam też dawać klientom wspomnianą długą gwarancję.
- Skąd pozyskujecie materiały do produkcji tworzyw sztucznych?
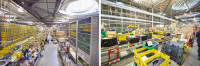
Magazyn i ostateczne procesy sprawdzania towarów przed wysyłką do klientów
W przypadku tworzyw sztucznych surowce pozyskujemy od wielu firm - zwykle przedsiębiorstw średniej wielkości, które wytwarzają dla nas mieszanki na zamówienie. Igus jest firmą rodzinną i stawiamy na długoterminowe relacje z kooperantami. Jest to tym ważniejsze, że na działalność R&D w zakresie nowych materiałów wydajemy rokrocznie duże kwoty i zależy nam, aby nasze know-how było bezpieczne.
Cała produkcja materiałów i gotowych produktów odbywa się u nas, zaś o jej skali świadczy fakt, że igus jest największym w Niemczech odbiorcą poliamidu zaraz za jednym z producentów z branży motoryzacyjnej.
- Mówiąc o przewodach i kablach, dochodzimy do Przemysłu 4.0 oraz "inteligentnego kabla", który zaprezentowaliście w tym roku na targach w Hanowerze. Czym on jest i co stało za jego stworzeniem?
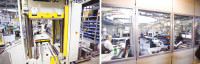
W obrębie zakładu produkcyjnego zintegrowano też m.in. narzędziownię do form wtryskowych i liczne biura, które znajdują się w bezpośrednim sąsiedztwie maszyn produkcyjnych
Naszą motywacją było dostarczenie automatykom dodatkowych narzędzi w zakresie prewencyjnego, a nawet predykcyjnego utrzymania ruchu. Dzisiaj, gdy dużo uwagi poświęca się Przemysłowi 4.0, nie należy zapominać o przewodach i innych elementach stanowiących część infrastruktury przesyłowej!
Chociaż można wyprodukować wysoce jakościowy kabel, to i tak zawsze będzie on charakteryzował się określonym czasem życia i kiedyś ulegnie uszkodzeniu. Stąd też postanowiliśmy stworzyć inteligentny kabel, który zaprezentowaliśmy jako jedną z nowości w ramach gamy produktów "smart plastics" podczas Hannover Messe 2016.
Inteligentne kable zawierają elementy pomiarowe monitorujące ich stan, co pozwala na poinformowanie obsługi o konieczności wymiany, gdy stan kabla wskazuje na możliwość wystąpienia awarii. Aby to umożliwić, rozwinęliśmy system "isense" obejmujący zarówno nowe produkty, jak też moduły komunikacyjne odpowiedzialne za przesyłanie informacji. Może on służyć do monitorowania stanu prowadników e-chain, przewodów oraz liniowych układów prowadzenia.
System isense może być podłączony do centrum danych firmy igus, co zapewnia klientom dodatkowe możliwości zarządzania posiadanymi urządzeniami i optymalizacji procesów produkcyjnych. Pracujemy również nad modułem "icom", który zapewni możliwość dostępu do danych przez Internet oraz integracji systemu z rozwiązaniami IT klientów. Sądzę, że w dobie Przemysłu 4.0 tego typu rozwiązania będą coraz szerzej stosowane w automatyzacji przedsiębiorstw produkcyjnych.
- Dziękujemy za rozmowę.