- Obszary automatyki i IT były przez długie lata odrębne od siebie i dopiero w epoce Przemysłu 4.0 zaczęły się realnie łączyć – szczególnie jeżeli chodzi o organizacje i pracowników. Jak postrzegacie te zagadnienia w Siemensie i jak ważna jest dla Was tematyka cyfryzacji?
Rzeczywiście w przemyśle przez długi czas istniał podział na dwa odrębne światy – IT oraz OT. Jednocześnie bardzo jasno były określone role informatyków i automatyków. Dzisiaj nadal potrzebna jest ich specjalizacja, bowiem rozwój technologii przyspiesza i rośnie zapotrzebowanie na kompetencje zarządzania zautomatyzowanymi procesami w przedsiębiorstwie. Z drugiej jednak strony wiele się zmienia. Przykładem jest podejście do programowania. W procesie kodowania nie wchodzi się już w poszczególne bajty, nie tworzy programów niskopoziomowych – programuje się obiektowo lub wręcz korzystając z gotowych modułów.
Specjalizacja musi łączyć się z umiejętnością dużo szerszego spojrzenia niż kiedyś. W Siemensie zwracamy szczególną uwagę na to, aby budować zdywersyfikowane zespoły i ekosystemy. Chodzi o to, że w grupach pracowniczych wymagane jest szerokie know-how, a to można uzyskać jedynie, gdy współpracują ze sobą różne osoby z różnorodnymi kompetencjami.
Również u nas, w moim zespole, widzę i doceniam taką różnorodność. Przykładowo osoby zajmujące się tematyką cyfrowego bliźniaka to mechatronicy z wiedzą informatyków lub, w drugą stronę, informatycy i programiści z kompetencjami mechatronicznymi. Takie połączenie jest konieczne, żeby rozumieć zagadnienia związane np. z wytrzymałością materiałów czy techniką napędową, ale też by symulować działanie maszyny, napisać kod, a finalnie stworzyć wirtualny model systemu.
- Jak te zmiany przejawiają się w kontekście Waszej oferty kierowanej do rynku?
W Siemensie powstały firmowe rozwiązania poszerzające ofertę klasycznych systemów SIMATIC – sterowników swobodnie programowalnych PLC. Dzisiaj oferujemy rozwiązania brzegowe, IoT Cloud, mamy też aplikacje chmurowe. W efekcie wiedza wykorzystywana w działach IT przenosi się powoli do automatyki. Do tego należy dodać tematykę ochrony danych, która bezpośrednio wiążę się z cyfryzacją.
Można stwierdzić, że Siemens odchodzi od patrzenia komponentocentrycznego. Sprawdzało się to 10‒15 lat temu – dzisiaj kluczowe jest szerokie spojrzenie na całe portfolio. Prezentujemy podejście holistyczne, zarówno w kwestii cyberbezpieczeństwa, które jest jednym z filarów cyfryzacji, jak i w obszarze innowacyjności. Dotyczy to całej firmy, także działu Digital Industries wraz z częścią Factory Automation, którą reprezentuję.
- Jak wpływa to na działalność Siemensa jako dostawcy komponentów typu sterowniki, panele czy napędy elektryczne?
Produkty te są i nadal będą dostępne w naszej ofercie, ale one same też ewoluują. Przykładowo TIA Portal służy już nie tylko do programowania sterowników, ale też do zarządzania panelami z zapewnieniem cyberbezpieczeństwa. Osobiście jestem przekonany, że w perspektywie dekady sterowniki jako idea pozostaną, ale będą coraz częściej wirtualizowane. Dawniej przewaga PLC związana była z ich hardware'em i niezawodnością – teraz dostępne są m.in. komputery przemysłowe, które spełniają te wymogi, a dodatkowo zapewniają dostęp do różnorodnych protokołów i otwartego software'u. Do tego dochodzą możliwości szybkiego tworzenia i pozyskiwania oprogramowania.
- Czyli komponenty pozostają dla Was bazą, natomiast klientom pokazujecie się jako kompleksowy dostawca rozwiązań i know-how?
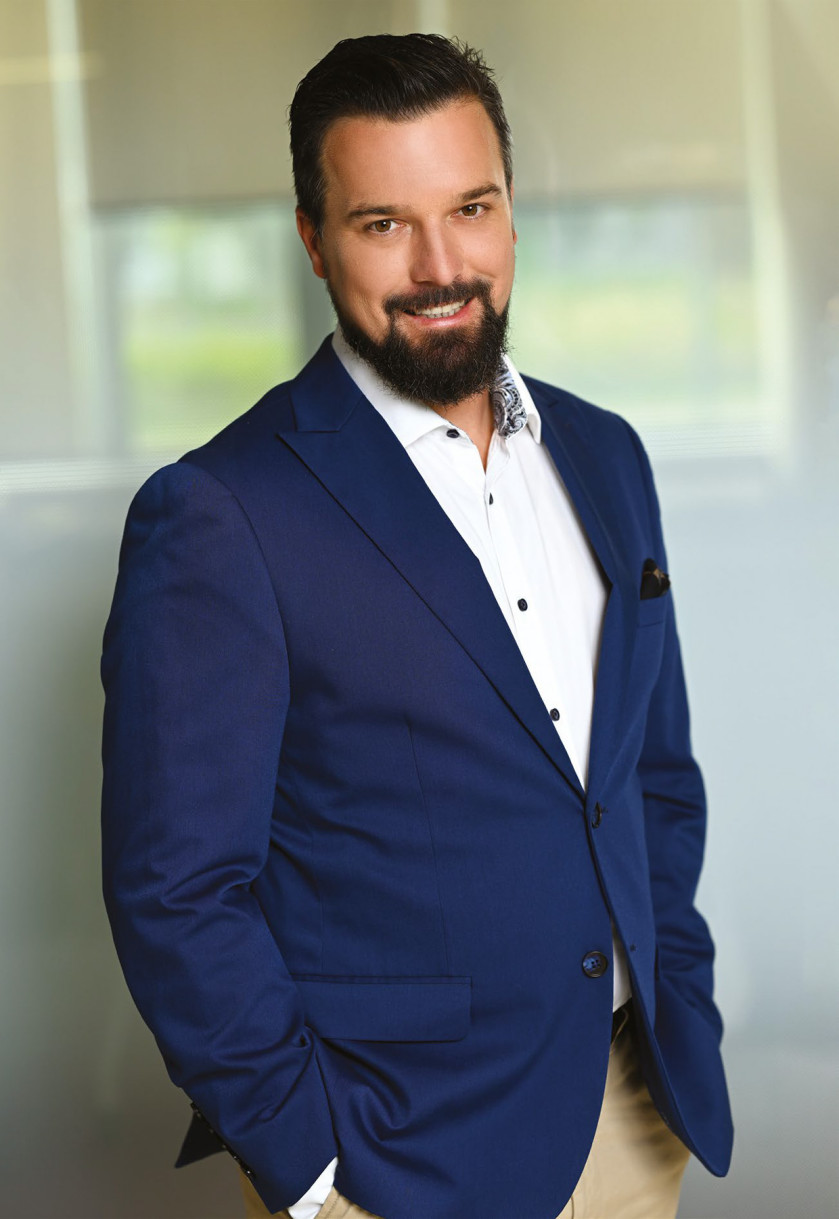
Tak, zdecydowanie. Zapewniamy klientom gotowe rozwiązania – od wysterowania konkretnej maszyny, sterowania systemem, przez ochronę danych, aż po przesyłanie informacji do chmury, gdzie mogą te dane analizować, a w efekcie optymalizować procesy i pracę linii produkcyjnych.
W moim przekonaniu cyfryzacja to rozwój software'u, ale oczywiście liczy się tu także hardware. W tym roku będziemy promować na polskim rynku naszą nową platformę Siemens Xcelerator, która wspiera transformację cyfrową w przedsiębiorstwach. Łączy ona w sobie rozwiązania hardware'owe, a więc portfolio sprzętowe oferowane dla wszystkich branż, z software'owymi, dotyczącymi różnorodnego oprogramowania. Wokół platformy chcemy też skupiać firmy partnerskie i klientów z branży IT, budując mechanizmy współdziałania pomiędzy różnymi podmiotami. Przykładowo programista z branży IT będzie mógł wykorzystać wiedzę obiektową, typową dla działów automatyki firm partnerskich, a także napisać fragment oprogramowania do rozwiązań bazujących na rozwiązaniach brzegowych – docelowo z wykorzystaniem sztucznej inteligencji czy też rozszerzonej rzeczywistości!
- W przemyśle, w tym w obszarze związanym z IT, właściwie nie ma firm mających u siebie 100% kompetencji. Czy takie kompetencje – w szczególności branżowe, aplikacyjne, chcecie budować wspólnie z partnerami z rynku?
Dokładnie tak! Kompetencje i siła działu Digital Industries są zbieżne z kompetencjami oraz działaniami naszych partnerów. Z tego połączenia staramy się wytworzyć synergie, oferując wspólnie gotową ofertę rozwiązań dla różnych branż. Jednocześnie my sami, zapewniając jakość, markę i rozpoznawalność, a także doświadczenia zdobywane przez 175 lat działalności Siemensa, gwarantujemy naszym klientom wizję realnego rozwoju.
Myślę, że w przyszłości filozofia dostarczania produktów na rynek będzie się zmieniała. Wiele rzeczy będzie tworzonych jako software-as-a-service lub jako innego rodzaju usługi. Ważne przy tym będą kwestie alternatyw finansowania – i tutaj mamy spółkę Siemens Finance, która zapewnia wiele modeli współpracy.
- A co z partnerami i ich specjalizacją?
Są oni specjalistami zazwyczaj w pewnych procesach i obszarach – i to właśnie stanowi ich unikalne know-how i przewagę konkurencyjną na rynku. W Siemensie pracuję od 2004 roku i obserwuję rozwój tych przedsiębiorstw. Wiele odnoszących sukcesy firm indywidualnie rozbudowało swoje kompetencje, np. w zakresie IT, obróbki danych czy też wdrażania rozwiązań bazujących na nowoczesnej komunikacji. Sądzę, że kolejnym impulsem będzie dla nich rozwój w ramach Siemens Xcelerator, który jest platformą z założenia mającą skupiać wokół siebie partnerów i pozwalać im na współpracę.
- Czy z takich możliwości korzystają też mniejsze firmy? Jak wygląda to w przypadku producentów maszyn?
Nawyki klientów się zmieniają. Dobrym przykładem jest historia przedsiębiorstwa specjalizującego się w rozwiązaniach systemów palnikowych, grzewczych itp. Aby wykonywać testy, konieczne jest grzanie, a gaz kosztuje. Kiedyś zaproponowaliśmy im zasymulowanie pracy układu w celu optymalizacji, ale nie byli tym zainteresowani. Gdy jednak okazało się, że godzina palenia gazem na testach zaczęła kosztować tysiące euro, to zainwestowanie 5‒6 tys. w Digital Twin stało się tak atrakcyjne, że momentalnie przeszli na korzystanie z takiego rozwiązania.
Pandemia i lockdown doprowadziły również do tego, że przyzwyczailiśmy się do nowego modelu pracy. Dzisiaj oczekiwania względem powszechnej możliwości zdalnego dostępu do sprzętu i procesów są czymś powszechnym. Firmy też zupełnie inaczej patrzą na koszty – np. związane z wysyłaniem personelu w odległe miejsca. To ostatnie dotyczy m.in. producentów maszyn i kwestii serwisu.
- Czy Wasza oferta dotyczy tylko przemysłu, czy też innych branż – np. infrastrukturalnej, ochrony środowiska, itd.?
W ramach działu Factory Automation obsługujemy dwa obszary – branżę procesową (woda, woda-ścieki, chemia) i produkcji dyskretnej (motoryzacja, przemysł maszynowy, spożywczy i wiele innych branż). Ale w Siemensie mamy też inne obszary biznesowe, w tym Smart Infrastructure, który obsługuje projekty z obszaru energetyki, infrastruktury i inne. Obejmuje to różnorodne działania pod wspólnym szyldem zrównoważonego rozwoju. Dzisiejsza sytuacja na rynku surowcowym wymusza bardzo oszczędne i efektywne podejście do zarządzania nimi – i wszystko, co oferuje Siemens, dokładnie się w to wpisuje. Niezależnie, czy chodzi o część przemysłową, czy infrastrukturalną – wszędzie sustainability jest naszym hasłem parasolowym, zaś głównym celem, do którego dążymy, pozostaje jak największa efektywność. Ta obrana przez Siemensa zrównoważona strategia opiera się na procesie dekarbonizacji, co finalnie przekłada się na bezpieczeństwo i dobro człowieka oraz środowiska.
- Pandemia, nowa sytuacja geopolityczna, wojna – wszystko to miało również duży wpływ na zmiany w kierunku cyfryzacji.
Zgadza się. Niedobory komponentów, przerwane łańcuchy dostaw – wszystko to zmieniało w ostatnich latach sytuację w przemyśle. Wcześniej przez wiele lat Industry 4.0 wskazywany był jako trend związany z kastomizacją i produkcją zindywidualizowaną, do tego firmy często korzystały z rozwiązań just-in-time. I to ostatnie, przez międzynarodową sytuację kryzysową, okazało się ogromnym problemem. Wtedy też zauważono, że możliwości oprogramowania czy wdrożonych technologii cyfrowych pozwoliły wielu firmom kontynuować działalność na rynku mimo globalnych zakłóceń. Przedsiębiorstwom w zachowaniu ciągłości biznesu pomagały też możliwości zdalnego dostępu do danych oraz wirtualizacja procesów. Zresztą z naszych badań (raport Digi Index Siemensa) wynika, że firmy, które postawiły na cyfryzację, łagodniej przeszły pandemię.
- A co z danymi? Przecież to one są podstawą wszystkich procesów cyfryzacji…
Na tym właśnie polega sztuka! Danych produkujemy mnóstwo – jak je gromadzić? Jak przetwarzać, aby były użyteczne? Dane pozwalają optymalizować procesy produkcyjne, tworzyć cyfrowego bliźniaka. Dzisiaj ich przetwarzanie i zaawansowana analityka stają się niezbędne – bez nich nie ma efektywności.
Jednocześnie pojawia się pytanie – jak te dane chronić, jak zapewnić cyberbezpieczeństwo? I tu znowu wracamy tu do ujęcia holistycznego, jakie praktykuje Siemens. Obejmuje ono różnorodne audyty. Nawet jeśli niektóre z nich wydają się pozornie odległe, np. audyt dostępów do szaf sterowniczych, stacji PLC czy monitoringu – wszystkie one mają na celu zwiększanie bezpieczeństwa danych.
- Jak rozwój nowych koncepcji i technologii ma się do tradycyjnej sprzedaży produktów?
Sprzedaż „tradycyjnych” produktów pozwala nam inwestować w rozwój innowacji, w rozwiązania software'owe. Pozwala na opracowywanie nowych pomysłów, na ich testowanie i na naukę – np. na budowanie u klientów prototypów Digital Twin i symulowanie procesów. Daje to też naszemu działowi przestrzeń na rozwój know-how w zakresie cyfryzacji.
- A jak jest w firmach? Kto sprzyja wdrażaniu cyfryzacji, a gdzie są czynniki ją hamujące?
Coraz częściej transformację cyfrową wspierają zarządy. Z moich obserwacji wynika, że prezesi akceptują proponowane działania, patrząc na tzw. szeroki obrazek. W tym widzą bowiem optymalizację kosztów i możliwości zwiększania efektywności. Blokady pojawiały się co prawda na poziomie np. działów utrzymania ruchu, które nie chciały zmieniać status quo. Na szczęście to już coraz częściej przeszłość i wszyscy zaczynają rozumieć i akceptować konieczność zmian, generować potrzeby, rozmawiać z nami i innymi dostawcami.
To dobry przykład obrazujący też, jak zmieniają się role na rynku. Dawniej przez wiele lat pukaliśmy do różnych drzwi, oferując klientom gotowe rozwiązania. Teraz to firmy są driverem zmian – przychodzą do nas i mówią o swoich potrzebach, zresztą zbieżnych z naszą wizją przyszłości przemysłu. W kokreacji z nimi powstają rozwiązania optymalnie dostosowane do zmieniających się potrzeb rynku. I staje się to zjawiskiem coraz bardziej powszechnym.
- Czy wzrost świadomości – czy to automatyków, czy też osób z działów IT – nie jest też związany ze zmianami pokoleniowymi?
Na pewno! W branży pojawiają się coraz młodsi ludzie, którzy w tym obszarze są zazwyczaj bardziej otwarci niż ich starsi koledzy. Ich już nie interesuje, jak napisać program, jak robiło się to żmudnie wiele lat temu podczas laboratoriów na politechnice. Dzisiaj chcą wykonać to zadanie, łącząc bloki programowe, czy też korzystając z gotowych apletów. Jednym słowem – chcą szybko rozwiązać problem, np. pozyskać potrzebne dane. Jednocześnie wśród tych osób umiejętności cyfrowe są czymś powszechnym, a one same mają potrzebę nabywania kolejnych kompetencji i ciągłego rozwoju.
- Digital Twin, chmura, rozwiązania brzegowe, rozszerzona rzeczywistość – wszystkie te technologie zmniejszają też ilość dodatkowej, często powtarzalnej pracy…
Dodajmy do tego coboty – choć akurat my ich w ofercie nie mamy, ale mają je nasi partnerzy. W każdym z przypadków ważne jest, aby nie wymyślać koła na nowo, a korzystać – na trochę wyższym poziomie – z tego, co już jest dostępne i dopasowywać to do aktualnych potrzeb.
Przykładem takiego rozwiązania jest wspomniana wcześniej platforma Siemens Xcelerator. Przez wiele lat firmy próbowały narzucać własne standardy technologiczne i zazwyczaj nie wychodziło to wszystkim na dobre. Firmy z Azji miały swój standard, Europa swój, USA również własny. Teraz pojawia się coś, co jest przeciwieństwem narzucania standardów – idea jest następująca: zróbmy wszystko razem, niech każdy działa w obszarze, na którym się zna, a klient wybierze to, co mu pasuje. I taką funkcję pełni Siemens Xcelerator – połączenie marketplace'u, systemu współpracy i narzędzia integrującego kompetencje.
Dodam, że poprzednie rozwiązanie Siemensa, czyli platforma MindSphere dla przemysłowego Internetu Rzeczy, była dla użytkowników propozycją określonego standardu. Nie wszystkim to odpowiadało, ale dzięki niej powstało narzędzie, które teraz wykorzystujemy już do zupełnie czegoś innego – do tworzenia otwartych systemów. Takie podejście sprawdza się zresztą również w obszarze cyberbezpieczeństwa. Nie ma jednej, optymalnej metody na jego zagwarantowanie, dlatego nie możemy oferować jednego standardu. Klient najlepiej znający własne potrzeby musi mieć wybór, poczucie sprawczości i finalnie otrzymać jak najlepsze dla niego rozwiązanie.
- Czy publikujecie informacje o wdrożeniach wykonanych przez Was i partnerów?
Tak, część z nich dostępnych jest na naszej stronie internetowej, gdzie zamieszczamy rozmaite studia przypadków z podaniem konkretnych końcowych rezultatów finansowych. Można tam znaleźć i opisy wdrożeń zarówno cyfrowego bliźniaka, i rozwiązań obejmujących typową automatykę.
W naszej rozmowie może wspomnijmy o kilku – przykładami mogą być te wykonane w firmach Polfarma, Adamet, Northvolt oraz Agnella. Ta ostatnia jest wiodącym w Europie producentem dywanów, działającym jeszcze w latach 70. zeszłego wieku. Wprowadziliśmy tam modyfikacje m.in. związane z wentylatorami, ich sterowaniem oraz zasilaniem. Zapewniło to Agnelli aż 2 mln zł oszczędności rocznie na samym prądzie – i to według starych cen! Wdrożenie zostało sfinansowane w trybie ESCO [czyli wydajnym modelu realizacji inwestycji dla poprawy efektywności energetycznej – przyp. redakcji], zaś firma dodatkowo, dzięki zmniejszeniu emisji CO2, otrzymała tzw. białe certyfikaty o dużej wartości finansowej.
- To chyba doskonały argument biznesowy…
Gdy klientowi przedstawia się argument, że dzięki jakimś rozwiązaniom będzie prowadził zrównoważony, efektywny energetycznie biznes, to rzadko kiedy jest on wystarczający. Aczkolwiek gdy dodamy, że w perspektywie roku, dwóch czy trzech lat firma osiągnie w stosunku do poniesionych nakładów wymierne zyski, podejście zmienia się całkowicie.
Świetnym przykładem nietypowej współpracy z dużą firmą był nasz projekt z Orlenem. Wykorzystywana
w nim była technologia 5G z chmurą obliczeniową Google'a oraz algorytmami sztucznej inteligencji. Celem było gromadzenie danych o płomieniu i sterowanie pracą systemów. Prowadziło to do uzyskania certyfikacji w Ministerstwie Cyfryzacji, która z kolei miała służyć przyznaniu przemysłowych pasm w sieci 5G.
- Ilu klientów obsługujecie? Jak działacie dzisiaj jako organizacja?
Liczba aktywnych klientów przemysłowych wynosi około dwóch tysięcy rocznie. Pokazuje to skalę naszego działania. Oczywiście można by tu w przybliżeniu zastosować zasadę Pareta, zgodnie z którą 20% największych odbiorców i wdrożeń odpowiada za 80% obrotów.
W ostatnich latach Siemens zmienił się organizacyjnie. Mamy Grupę Siemensa, czyli Siemens Sp. z o.o., jest Siemens Software. W naszym warszawskim kampusie mieszczą się też Siemens Finance, Siemens Mobility, Siemens Energy oraz Siemens Healthineers. Działamy jako grupa wyspecjalizowanych organizacji, dzięki czemu staliśmy się bardziej elastyczni.
Dodam, że w wielu projektach nasze różne działy i spółki współpracują ze sobą. Część kompetencji dostarcza przykładowo oddział z Austrii, część centrala w Niemczech, a część należy do lokalnych filii. Tak było np. w przypadku współpracy z firmą Volkswagen i budową zakładu produkującego samochody Crafter.
Innym ciekawym, dużym projektem, przy którym Siemens obsługuje zarówno część przemysłową, jak i infrastrukturalną, jest gigafabryka materiałów akumulatorowych Umicore pod Nysą. Jest to potężna inwestycja, w której współpracujemy z kilkoma partnerami z okolic Wrocławia.
- Dziękujemy za rozmowę.