ZWĘŻKI
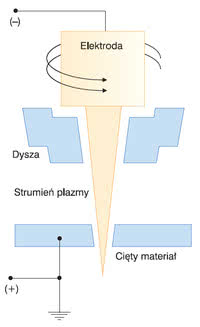
Rys. 5. Gaz z dyszy, przepływając przez łuk elektryczny, ulega jonizacji. Strumień powstałej w ten sposób plazmy przecina materiał
Jedną z ważniejszych części dyszy jest zwężka. Wykonuje się ją z kamienia szlachetnego - zazwyczaj rubinu, szafiru lub diamentu. Właściwości materiału zwężki mają duży wpływ na eksploatację i konserwację dysz oraz jakość strumienia wody. W waterjetach popularne są zwężki z szafiru, w przypadku których czas użytkowania przy zachowaniu wody dobrej jakości wynosi od 50 do 100 godzin cięcia. Niestety w przypadku abradżetów okres użytkowania zwężek z tego materiału jest o połowę krótszy, stąd szafir rzadko jest w nich wykorzystywany.
Odwrotnie jest w przypadku rubinu. Nadaje się on przede wszystkim do produkcji zwężek do maszyn tnących materiałem ściernym, w których żywotność takich komponentów wynosi nawet 100 godzin cięcia, natomiast do waterjetów nie jest zalecany. Najbardziej wytrzymałym materiałem jest diament - żywotność zwężek tego typu wynosi zazwyczaj od 800 do 2 tys. godzin.
Istotne jest też to, że zwężki diamentowe - w przeciwieństwie do elementów z pozostałych materiałów - można czyścić na przykład ultradźwiękami. Dlatego też, chociaż diament jest droższy niż szafir i rubin, w maszyny ze zwężkami tego typu warto jest inwestować w przypadku, gdy urządzenie będzie pracować nieprzerwanie przez dłuższy czas.
CIĘCIE TLENOWE, PLAZMĄ, LASEREM
CIĘCIE TLENOWE I JEGO OGRANICZENIA
W pierwszej z tytułowych metod wykorzystuje się proces chemicznego spalania metalu w strumieniu czystego tlenu, który jednocześnie wydmuchuje ze szczeliny powstałe w wyniku tej reakcji tlenki. Proces ten jest poprzedzony szybkim podgrzaniem metalu w miejscu cięcia do temperatury zapłonu (rys. 3). Metal podgrzewa się, wykorzystując płomień z palnika zasilanego mieszaniną gazową, na przykład acetylenu z tlenem lub propanu z tlenem.
Wybór paliwa gazowego jest uzależniony m.in. od wymaganej jakości krawędzi ciętego materiału oraz grubości ciętego materiału. Ważne są też koszty - na przykład ze względu na cenę acetylenu mieszankę acetylenowo- tlenową zaleca się do obróbki cienkich materiałów, do podgrzania których nie zużywa się dużych ilości gazu. Propan z kolei, pomimo że ma niższą temperaturę płomienia, jest znacznie tańszy niż acetylen i stąd jest bardzo popularny w maszynach tnących, zwłaszcza tam, gdzie dobra jakość krawędzi nie jest priorytetem.
Oprócz wymienionych gazów w planikach do cięcia tlenem wykorzystuje się też często propylen, gaz ziemny i wodór. Ze względu na specyfikę tej metody znajduje ona zastosowanie jedynie w cięciu metali charakteryzujących się określonymi właściwościami. Przede wszystkim, aby możliwe było utrzymanie temperatury zapłonu metalu w miejscu cięcia, zaistnieć musi dodatni bilans cieplny, tzn. więcej ciepła powinno do materiału docierać, niż się w nim rozpraszać.
|
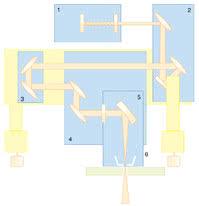
Rys. 6. Maszyna do cięcia laserem składa się z komory rezonatora lasera (1), układu luster (2, 3, 4) oraz soczewek skupiających (5) w głowicy tnącej (6) (źródło: ESAB)
Stąd metal powinien się charakteryzować odpowiednio małą wartością przewodnictwa cieplnego. Ponadto temperatura zapłonu metalu w tlenie powinna być niższa niż jego temperatura topnienia. Na przykład w przypadku stali o spełnieniu tego warunku decyduje zawartość węgla - powyżej 1,5% temperatura zapłonu jest wyższa niż temperatura topnienia. Dlatego cięcie tlenowe jest wykorzystywane głównie w obróbce stali niskowęglowych.
Ważne też, aby temperatura topnienia tlenków metalu była niższa od temperatury topnienia metalu. W przeciwnym wypadku niemożliwe jest ich usunięcie ze szczeliny strumieniem tlenu. Wówczas zwiększają one straty cieplne, a nawet mogą zablokować dalsze cięcie. Rozwiązaniem problemu trudnotopliwych tlenków jest dodanie do strumienia tnącego tlenu sproszkowanego żelaza (rys. 4). Ulegając szybkiemu utlenianiu, dostarcza ono dodatkowej energii potrzebnej do stopnienia wysokotopliwych tlenków.
CIĘCIE PLAZMĄ
W metodzie tej do cięcia wykorzystuje się łuk plazmowy. Powstaje on, gdy gaz przepływający przez jarzący się między elektrodami (elektrodą nietopliwą i ciętym materiałem) łuk elektryczny ulega jonizacji (rys. 5). Strumień plazmy ukształtowany w specjalnie schładzanej dyszy osiąga bardzo wysoką temperaturę i uderzając w cięty materiał, miejscowo go wytapia, jednocześnie wydmuchując jego resztki z powstałej w ten sposób szczeliny.
Plazmę wytwarza się z różnych gazów, w tym na przykład z azotu, argonu, wodoru, tlenu oraz suchego sprężonego powietrza. Wybór gazu zależy od specyfiki ciętego materiału. Na przykład tlen jest używany czasem do cięcia stali węglowej oraz stali niskostopowej o grubości do 20mm, natomiast sprężone powietrze znajduje zastosowanie w cięciu cienkich blach ręcznie sterowanymi głowicami tnącymi.
Azot jest z kolei wykorzystywany do cięcia przykładowo stali nierdzewnej oraz aluminium, natomiast mieszanina argonu z wodorem jest używana do cięcia grubych materiałów (do 100mm), w tym na przykład stali nierdzewnej, aluminium, miedzi oraz tytanu. Udział wodoru w mieszance zależy od rodzaju ciętego metalu.