Projektowanie sprzętu VR
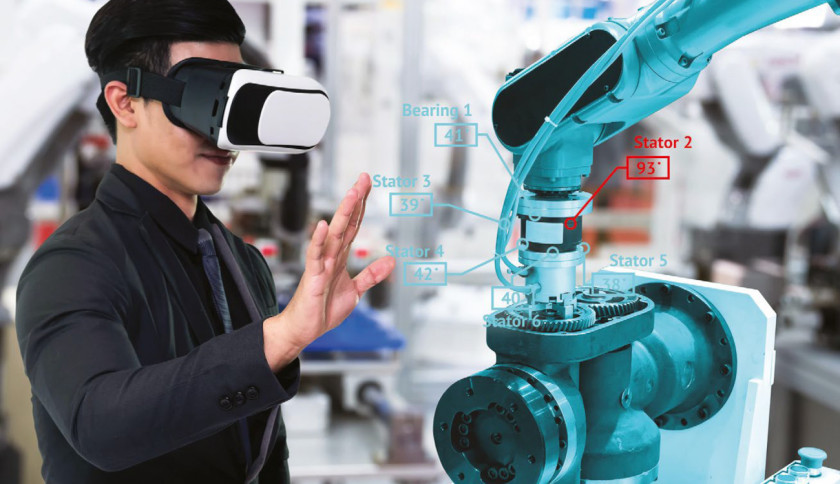
Jedną z pierwszych decyzji projektowych jest liczba stopni swobody zestawu VR – z technicznego punktu widzenia jest to parametr mający największy wpływ na stopień skomplikowania sprzętu i oprogramowania, a zatem czas wprowadzenia na rynek i koszty. Generalnie zestawy VR mają 3 albo 6 stopni swobody, co oznacza, że tyle różnych osi jest jednocześnie śledzonych w celu wykrycia położenia oraz ruchu urządzenia. Dostępna jest szeroka gama czujników MEMS, akcelerometrów i żyroskopów, zintegrowanych po kilka w jednej obudowie, by śledzić ruch wielokierunkowo, zaś ich cena ciągle maleje dzięki ich rosnącej popularności w elektronice użytkowej. Pomimo to pod względem sprzętowo-programowym zestawy VR z 6 stopniami swobody, wymagające dodatkowych czujników, zwykle optycznych, oraz większej mocy obliczeniowej, są generalnie bardziej skomplikowane i droższe. Dlatego trzeba się dobrze zastanowić, czy wymagane jest śledzenie aż 6 osi – w niektórych przypadkach wystarczy obserwacja ruchu w 3. Dotyczy to aplikacji, w których nie jest konieczne wywołanie w użytkowniku wrażenia, że w pełni zagłębił się w wirtualnej rzeczywistości. Do takich zaliczają się te, w których z zestawu VR korzysta się na siedząco, na przykład symulatory jazdy, lotu, sterowania. Sześć stopni swobody jest z kolei wymaganych w śledzeniu bezwzględnego ruchu użytkownika w przestrzeni 3D. W takim przypadku może się on dowolnie poruszać, mając przy tym wrażenie, że jest obecny w wirtualnej rzeczywistości całym ciałem. Możliwość m.in. schylania się, obchodzenia obiektów dookoła, kucania, spoglądania na obiekty z góry oraz od dołu sprawdza się szczególnie w takich aplikacjach, jak wirtualne szkolenia, w których pracownik zdalnie odwiedza fabrykę, chodząc po jej cyfrowej replice, aby zapoznać się z wyposażaniem i planem budynku.
Techniki śledzenia
Kluczowym etapem tworzenia aplikacji oraz urządzeń do obsługi wirtualnej rzeczywistości jest zaprojektowanie systemu śledzenie pozycji i ruchu użytkowników. W tym zakresie stosuje się zazwyczaj jedno z dwóch podejść, wykorzystując czujniki różnych typów. W pierwszym rozwiązaniu (outside-in) ruch hełmów VR jest śledzony przez czujniki rozmieszczone w pomieszczeniu. Tę konfigurację wyróżnia większa dokładność i mniejsze opóźnienia, co sumarycznie poprawia wrażenia użytkowników. Z drugiej strony jednak są oni śledzeni dopóty, dopóki znajdują się w zasięgu czujników – gdy tylko znajdą się poza nim albo coś ich przesłoni, przestają być śledzeni, co skutkuje nagłym, dezorientującym opuszczeniem wirtualnej rzeczywistości.
W alternatywnej konfiguracji (inside-out) czujniki są umieszczone na hełmie, którego pozycja powinna być śledzona i odwzorowywana w wirtualnej rzeczywistości. Jej zmiany odnosi się względem otoczenia, wykorzystując w tym celu znaczniki w nim rozmieszczone, chociaż w niektórych systemach nie są one niezbędne. Zaleta tego rozwiązania to możliwość swobodnego przemieszczania się, nieograniczona przestrzenią w polu widzenia czujników, natomiast nie dorównuje pierwszej konfiguracji dokładnością ani opóźnieniem i wymaga większej mocy obliczeniowej lokalnie, w kasku VR. Ważnym aspektem projektowym jest rozmieszczenie czujników na hełmie i kontrolerach, którymi posługują się użytkownicy. Konstrukcja tych ostatnich powinna zapewniać pełną swobodę ruchu. Projektując je, trzeba uwzględnić też wymagania ergonomii.
Mobilność, materiały konstrukcyjne
Na etapie projektowania należy również zdecydować, w jakim stopniu dany zestaw VR będzie przenośny. Jeśli wymagana jest duża mobilność, na przykład konieczne jest przechodzenie między pomieszczeniami, oczywiście nie można polegać na mocy obliczeniowej zewnętrznych urządzeń ani łączyć się z nimi kablami. W zamian korzystać trzeba z komunikacji bezprzewodowej, co powoduje, że należy liczyć się z opóźnieniami, przynajmniej do czasu spopularyzowania się łączności 5G, oraz opierać się na lokalnej mocy obliczeniowej i zasobach pamięci.
Kolejna ważna kwestia to wybór materiałów do wykonania sprzętu VR. Wpływają one na jego właściwości użytkowe, na przykład ergonomię i trwałość, i ogólne wrażenia użytkownika, na przykład dotykowe. Ich wybór warunkują poza tym kwestie techniczne – przykładowo okienka czujników muszą przepuszczać promieniowanie o określonej długości fali, jak podczerwień, zaś pozostałe blokować. Powierzchnie kontaktowe powinny także charakteryzować się odpowiednimi właściwościami termicznymi, by nadmiar ciepła generowany w związku z dużą mocą obliczeniową był rozpraszany do otoczenia, a nie oddawany do ciała użytkownika. Przy zmianach temperatury nie mogą się także zmieniać wymiary elementów, w przypadku których pogarszałoby to jakość obrazu.
Cyfrowe bliźniaki i VR/AR w przemyśleFirma Ford wykorzystuje dane pomiarowe z czujników ruchu ciała pracowników podczas montażu, aby w wirtualnym środowisku analizować ryzyko obrażeń i długoterminowe skutki nieprawidłowej postawy. To pozwala na zmodyfikowanie wyposażenia i procedur, by zmniejszyć liczbę wypadków i poprawić ergonomię na stanowiskach pracy. Inżynierowie i projektanci firmy BMW wykorzystują wirtualną rzeczywistość, by sprawdzić, jak wyglądają różne elementy samochodu bez wykonywania fizycznych prototypów. Znacznie obniża to koszty. Technologia wirtualnej rzeczywistości jest w firmie Airbus wykorzystywana do integracji cyfrowych makiet w środowiskach produkcyjnych. Zapewnia to pracownikom montażowym dostęp do kompletnych modeli 3D produkowanego samolotu, skracając czas inspekcji z tygodni do dni. Inżynierowie Simensa wykorzystują wirtualną rzeczywistość do wizualizacji cyfrowych replik urządzeń. VR i cyfrowe bliźniaki umożliwiają inżynierom Forda testowanie samochodów z perspektywy osób o różnych cechach fizycznych. W firmie Enel przeprowadzane są wirtualne szkolenia z zakresu montażu, demontażu, serwisowania, naprawy, konserwacji. Projektanci Forda współpracują na odległość nad projektami, które oglądają i komentują w wirtualnej rzeczywistości. Technicy firmy Boeing za pośrednictwem rzeczywistości rozszerzonej otrzymują instrukcje montażu okablowania samolotów – skraca to czas realizacji tego zadania i zmniejsza liczbę błędów. Inżynierowie z EDF Energy używają Google Glass do wykonywania zdjęć i filmów w czasie instalowania inteligentnych liczników, które przesyłają następnie do centrali, w celu zweryfikowania oraz potwierdzenia instalacji. W Pacific Gas and Electric z kolei pracownicy dokonują zdalnej inspekcji sprzętu w wirtualnej rzeczywistości, w oparciu na danych pomiarowych zbieranych w terenie. Znacząco zwiększa to bezpieczeństwo personelu, który nie naraża się bezpośrednio nie przeprowadzając inspekcji na miejscu. Natomiast w przedsiębiorstwie Welsh Water inżynierowie wykorzystują wirtualną rzeczywistość w projektowaniu i wizualizacji sieci wodociągów, kanalizacji i planowaniu przestrzennym. Technicy Porsche używają okularów z rozszerzoną rzeczywistością, które wyświetlają im instrukcje i schematy, a jednocześnie umożliwiają zdalnym ekspertom obserwowanie tego, co widzą technicy i przekazanie im informacji zwrotnej. AR jest wykorzystywana przez projektantów Forda do przeglądania projektów oraz cyfrowych bliźniaków podzespołów tak, jakby były częścią rzeczywistego pojazdu. (źródło: Capgemini). |