Wyzwania w pakowaniu w kartony
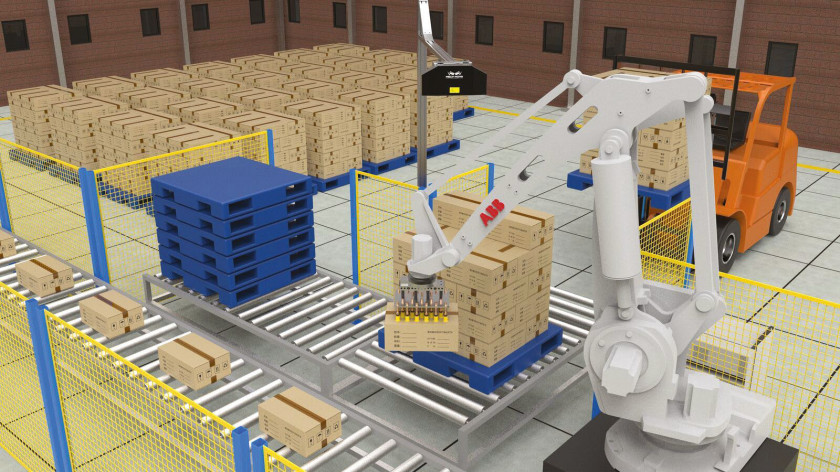
Opakowaniem jednostkowym mogą być także pudełka kartonowe. Przykładowa linia pakowania w kartony może się składać z: składarki kartonów, zaklejarki łączącej dolne klapki pudełek, maszyny wkładającej produkty do kartonów i zaklejarki górnych klapek. W takim ciągu technologicznym w pierwszym kroku kartony są pobierane z podajnika i składane. Następnie, po zamknięciu dolnych klap, są wypełniane produktem. Na koniec pudełka zamyka się od góry i transportuje na stanowisko paletyzowania. Gdy brzegi kartonów są sklejane, etapem pośrednim jest jeszcze aplikacja kleju.
Karton jest specyficznym rodzajem opakowania, łatwym do zarysowania i rozdarcia. Podatność na uszkodzenia zależy od jego jakości. Tańszy, ale gorszej jakości może, mimo oszczędności przy zakupie, być źródłem dużych strat, jeśli przez niezgodność ze specyfikacją, na przykład grubości, będzie blokować albo spowalniać maszynę kartonującą. Może też być powodem nieszczelności opakowań, co w przypadku płynnych i sypkich towarów zanieczyszcza linię produkcyjną oraz prowadzi do strat produktu. Poza tym jakość opakowań finalnych jest zwykle wtedy niezadowalająca, co, jeżeli tak zapakowane produkty trafią do sprzedaży, negatywnie przekłada się na decyzje zakupowe konsumentów.
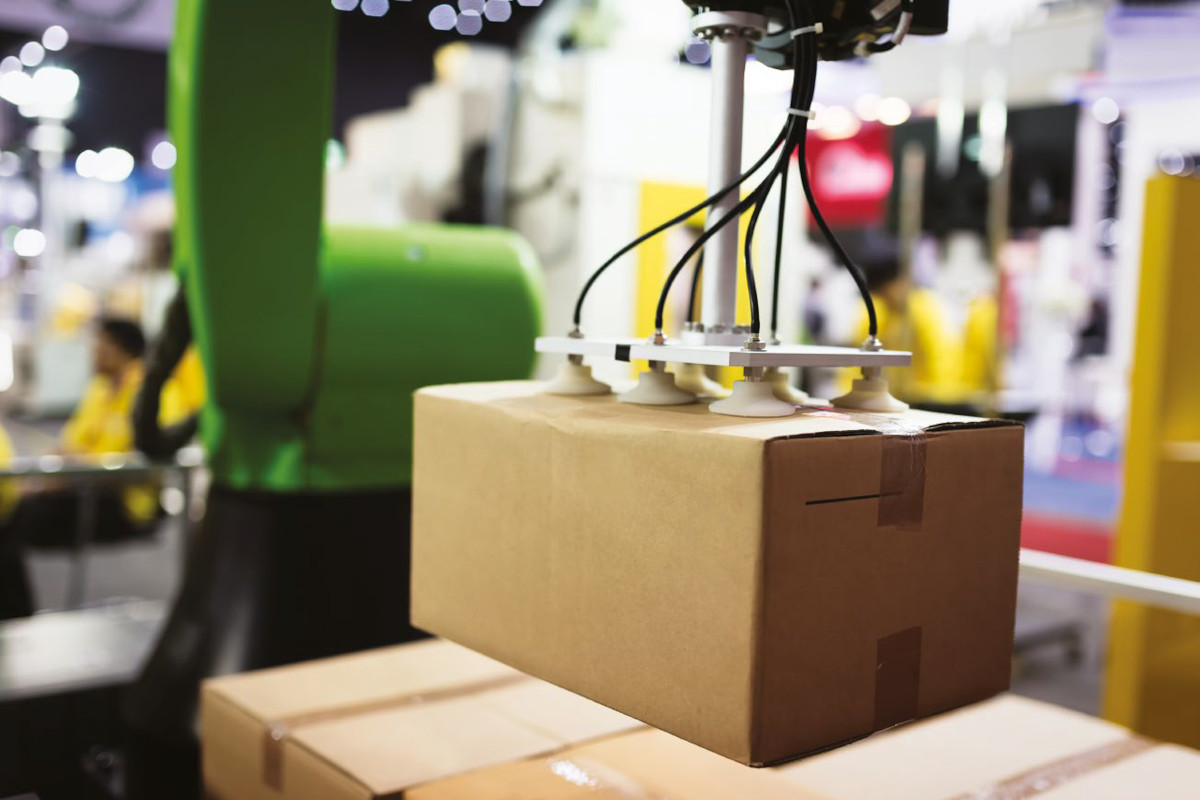
By uniknąć problemów podczas kartonowania, ważne jest też, by przechowywać materiał opakowań w odpowiednich warunkach. Wynika to z właściwości papieru, który wchłania albo oddaje wilgoć w zależności od wilgotności w otoczeniu. Dlatego zimą, w ogrzewanym magazynie, w którym jest zbyt sucho, składowane kartony zaczną wysychać. Latem z kolei, jeżeli jest bardzo parnie, ulegną zawilgoceniu. Skutkiem jest różna sztywność suchych i mokrych kartonów, co może powodować problemy w działaniu maszyny je składającej.
Poza jakością materiału kluczowe znaczenie w procesie kartonowania ma jakość spoiwa i sposób jego nakładania. Przeważnie w tym zastosowaniu używa się kleju topliwego w postaci granulek, który jest topiony, a potem natryskiwany na karton. W zakresie aplikacji spoiwa trzeba przestrzegać pewnych zasad. Za gorący klej nie będzie sklejać wystarczająco szybko, natomiast ten o za niskiej temperaturze w ogóle nie będzie się lepić. W obu przypadkach brzegi kartonu nie zostaną sklejone. Ważne jest także wykończenie powierzchni – na przykład dla lepszej przyczepności sklejać należy powierzchnie nielakierowane. Niepożądany jest ponadto nadmiar kleju, ze względów estetycznych, jak i praktycznych. Silnie zaklejone opakowania będzie trudno otworzyć, a lepiące się zacieki mogą powodować sklejanie się pudełek i zbieranie zabrudzeń. Zbyt mała ilość kleju z kolei nie zapewni trwałego złączenie brzegów pudełka.
Newralgicznym komponentem kartoniarek jest też próżniowy system chwytania i wyjmowania arkuszy kartonu z zasobnika – jeżeli nie działa prawidłowo, łatwo może zablokować maszynę. Najczęściej w tym zakresie powtarza się kilka problemów. Przykładowo zużyte chwytaki próżniowe (popękane, przetarte) nie będą w stanie zapewnić wystarczająco dużego podciśnienia, aby podnieść arkusz. Dlatego trzeba je poddawać regularnie inspekcji, a zauważając oznaki uszkodzenia, jak najszybciej wymienić. Powodem nieszczelności mogą też być zbyt luźne połączenia elementów przyssawki. Przewód podciśnieniowy nie może być zgięty. Trzeba ponadto mieć świadomość, że pył towarzyszący cięciu kartonów może zatykać system wytwarzania podciśnienia, dlatego należy go co jakiś czas czyścić.
Problemy z opakowaniami – przyczyny i rozwiązaniaCase study 1: Stwierdzono, że produkt spożywczy ma inny niż oryginalny, nieprzyjemny smak. Podejrzewano, że powodem jest materiał opakowania jednostkowego, mający z nim bezpośrednią styczność. Aby wyjaśnić, skąd bierze się przykry posmak, przeprowadzono specjalistyczną analizę technikami mikroekstrakcji do fazy stałej, chromatografii gazowej i spektrometrii masowej. Badaniu porównawczemu poddano partię kontrolną produktu, jego partię zanieczyszczoną oraz opakowanie. Potwierdziło to, że materiał tego ostatniego wszedł w reakcję i przeniknął do produktu. Dalsza analiza wykazała, że doszło do tego w wyniku niekompatybilności materiału opakowania z jego zawartością, a niepożądane reakcje przyspieszyły nieodpowiednie warunki magazynowania. Case study 2: Producent żywności wykrył nieprzyjemny zapach swojego produktu pakowanego w pudełka importowane z Chin. Żeby wyjaśnić jego źródło, przeprowadzono analizę analogicznymi metodami jak w wyżej opisanym przypadku. W zarejestrowanych w ten sposób chromatogramach wykryto piki zgodne z profilem rozpuszczalnika węglowodorowego o niskiej masie cząsteczkowej, takiego jak spirytus mineralny albo nafta. Producent żywności przedstawił te informacje dostawcy problematycznych opakowań, który w obliczu takiego dowodu przyznał, że omyłkowo zamiast jak zwykle izopropanolu do ich czyszczenia przed wysyłką użył... benzyny ciężkiej. ![]() Case study 3: Stwierdzono, że opakowania pewnego produktu rozszczelniają się zaledwie po kilku dniach w magazynie. Jako przyczynę zaczęto podejrzewać zmianę formuły używanego do złączania ich boków topliwego kleju poliuretanowo-akrylowego. By to udowodnić, wykonano specjalistyczną analizę porównawczą składu nowego oraz wcześniej używanego spoiwa metodą chromatografii żelowo-permeacyjnej. Wykazała ona znaczące różnice w rozkładzie ich mas cząsteczkowych. To wyjaśniało niepełną polimeryzację, która z czasem prowadziła do degradacji właściwości kleju. Zalecono w związku z tym korektę formuły spoiwa. Case study 4: Zaobserwowano rozwarstwianie się epoksydowego pokrycia wewnętrznej strony metalowych puszek. Aby wykryć przyczynę, przetestowano je pod kątem niewłaściwej aplikacji żywicy, wykonując mikroskopowy pomiar grubości powłoki, jej niewystarczającego utwardzenia, przeprowadzając badanie techniką skaningowej kalorymetrii różnicowej i zanieczyszczenia żywicy wykonując analizy technikami chromatografii gazowej ze spektrometrią masową, spektroskopii fourierowskiej w podczerwieni i energodyspersyjnej analizy rentgenowskiej. Porównując uzyskane wyniki z rezultatami badań puszek, w których problem rozwarstwienia nie występował, w tych pierwszych wykryto obecność siarki na powierzchni metalu. Przesłanie tej informacji dostawcy puszki pozwoliło na zdiagnozowanie i rozwiązanie problemu na linii ich produkcji. Case study 5: Producent pewnego produktu, w składzie którego występował alkohol, zauważył, że po zapakowaniu go w butelki z zakrętkami z tworzywa sztucznego jego smak uległ pogorszeniu, a kolor się zmienił. Podejrzewano, że źródłem problemu są wieczka opakowań. W związku z tym przeprowadzono analizę porównawczą zakrętek, które spowodowały pogorszenie jakości produktu z wieczkami nieużywanymi. Wykonując badanie metodą chromatografii gazowej ze spektrometrią masową, w pierwszych wykryto obecność kaprolaktamu. Jest to rozpuszczalny w alkoholu składnik tuszu używanego do wykonywania nadruków na zewnętrznej powierzchni wieczek. Zagadką wciąż pozostawało jednak to, jak z wierzchu zakrętki przedostał się on na jej spód, gdzie miał kontakt z produktem. Dalsze dochodzenie wykazało ostatecznie, że podczas produkcji wieczka były układane jedno na drugim. To umożliwiło przeniesienie atramentu na stronę mającą styczność z żywnością i jego rozpuszczenie przez zawarty w niej alkohol. |