Opakowanie pełni szereg funkcji. Jego podstawowym zadaniem jest ochrona produktu – zapobiega jego uszkodzeniu i zanieczyszczeniu podczas transportu i magazynowania. Uniemożliwia też jego uwolnienie do otoczenia, na przykład rozsypanie się albo wycieknięcie. Substancje płynne i sypkie dzięki opakowaniu zyskują formą przestrzenną. Jego stan jest ponadto gwarancją nienaruszalności produktu. Umieszcza się na nim informacje o zawartości, jak skład i data przydatności do spożycia w przypadku żywności. Może być także wyróżnikiem na tle oferty konkurencji. Opakowania poza tym grupują produkty.
Opakowania jednostkowe, zbiorcze, transportowe
Wyróżnia się trzy typy opakowań. Jednostkowe mają bezpośredni kontakt z produktem. Ich funkcją jest jego ochrona i konserwacja właściwości. Ułatwiają konsumentom korzystanie z ich zawartości. Przykładami opakowań jednostkowych są: kartony z mlekiem, puszki z piwem, plastikowe butelki wypełnione detergentem.
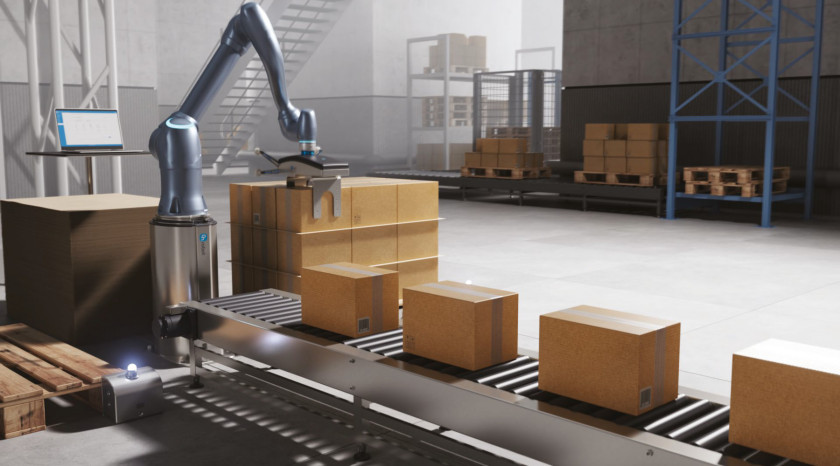
Zbiorcze grupują pewną liczbę produktów w celu utworzenia jednostki magazynowej. Zapewniają też dodatkową ochronę, pomagając zachować integralność opakowania jednostkowego i ułatwiają korzystanie z mniejszych produktów, łącząc je w jedną paczkę. Przykładami są: kartonowe pudełka, w które po kilka pakowane są plastikowe woreczki z kaszą albo ryżem i zgrzewki butelek wody mineralnej opakowanych w folię termokurczliwą.
Trzeci typ grupuje większą liczbę jednostek magazynowych, by umożliwić ich transport. Kluczowe w tym przypadku są: gęstość upakowania i stabilność ładunku, które decydują o tym, czy dostępna przestrzeń magazynowa jest wykorzystana optymalnie, a towary są przechowywane bezpiecznie. Przykładem są palety załadowane owiniętymi folią stretch pudłami kartonowymi z butelkami wina.
Dan Rossek
Omron
Typowe maszyny w liniach pakujących to: zgrzewarki, nalewaczki, zakręcarki, etykieciarki, kartoniarki, casepackery, flowpackery, paletyzatory i owijarki. Grupę tę można podzielić na maszyny standardowe do produktów typowych, specjalne – np. casepackery pod niestadardowe kształty produktów, a także wersje zrobotyzowane. Te ostatnie służą przykładowo do pakowania drobnych produktów do tacek z dużą wydajnością, a także używane są do paletyzacji końcowej.
Jeżeli chodzi o odbiorców, to są to branże takie jak: spożywcza, w tym napojowa, FMCG, farmaceutyczna, produkcji środków czystości, kosmetyczna, tytoniowa oraz logistyczna. Typowe kryteria doboru to: wydajność, typ produktu, gabaryty/waga, typ opakowania, różnorodność formatów, długość serii i częstotliwość koniecznych przezbrojeń. Pakowanie jest silnie powiązane z branżą spożywczą, więc wymagania do pewnego stopnia pokrywają się. Pakowanie pierwotne wymaga zachowania czystości, higieny, regularnego mycia, natomiast pakowanie wtórne, zbiorcze i paletyzacja – już mniej. Procesy pakowania zawsze cechuje wysoka wydajność i mały margines błędu. Ważne są tu kwestie dotyczące potencjalnych awarii oraz kontroli jakości opakowań (wygląd, szczelność). Opakowanie wymaga oznaczenia (numer partii, data ważności), a oznaczenie – kontroli jego jakości, np. systemem wizyjnym.
Nowościami są m.in.: coraz powszechniejsze zastosowanie robotów pick & place (SCARA, delta) w procesie pakowania pierwotnego produktów do tacek lub kompletowania w ramach co-packingu, a także coraz powszechniejsze zastosowanie cobotów w procesie paletyzacji. Należy zauważyć, że paletyzacja ma obecnie do dyspozycji komputerowe, nowoczesne algorytmy optymalnego planowania przestrzeni na palecie. W branży wykorzystywane są również nowoczesne algorytmy do kontroli jakości opakowań z wykorzystaniem AI, a także wydajne czujniki do niezawodnej detekcji tacek i folii transparentnych. Z naszej perspektywy ważne są też technologie znakowania produktów kodami 2D (etykiety, lasery, drukarki) i rozwiązania do traceability (czytniki kodów, weryfikatory). |
Pakowanie jednostkowe w pakowarkach
Do umieszczania produktów w opakowaniach jednostkowych służą m.in. pakowarki. Są to zwykle zautomatyzowane maszyny, chociaż dostępne są wersje półautomatyczne. Wykorzystują folię do uformowania torebki przez zgrzewanie jej boków, wypełniają ją produktem, na koniec zamykając przez zgrzanie brzegów. Pakowarki mają wiele zalet. Zapewniają szybkie i tanie pakowanie, gdyż w obrębie jednego stanowiska automatyzują wiele zadań: formowanie opakowania, jego napełnianie i zamykanie. Wyróżnia je elastyczność – pozwalają na pakowanie produktów stałych, płynnych i sypkich. Na opakowaniach, które wykonują, jest dużo miejsca na nadruk.
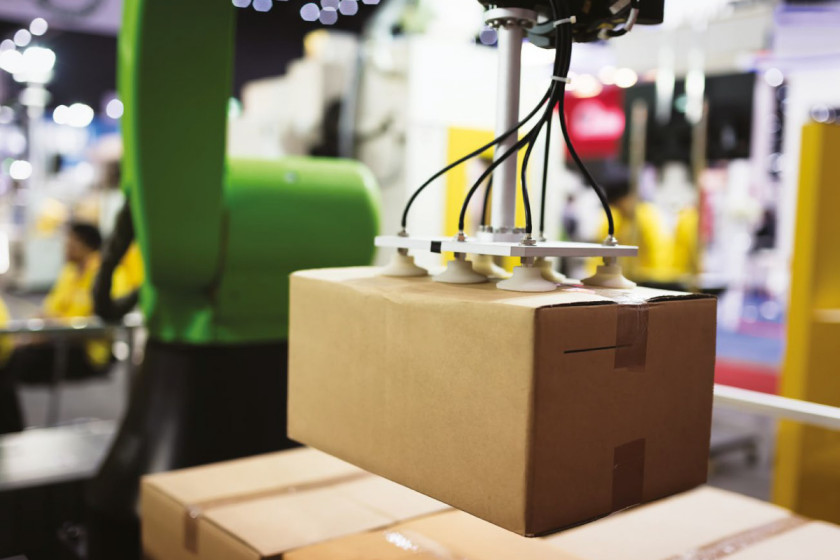
Popularne typy to pakowarki poziome i pionowe. Ich główne komponenty to: rolka z nawiniętym materiałem opakowania, układ prowadnic, którymi jest on rozwijany i prowadzony do kołnierza formującego torebkę, wsyp produktu, zgrzewarka. Torebki wytworzone w pakowarkach zazwyczaj mają trzy szwy: biegnący wzdłuż, który powstaje przez złączenie, zazwyczaj na zakładkę, brzegów folii, dolny, który zamyka spód torby oraz górny, uszczelniający ją od góry. Główna różnica między pakowarkami poziomymi i pionowymi dotyczy sposobu organizacji przestrzennej – w pierwszych sekcje maszyny są rozciągnięte horyzontalnie, w drugich wertykalnie. Dlatego pakowarki pionowe zajmują zwykle mniej miejsca, dzięki czemu można dostępną przestrzeń wykorzystać efektywniej.
Czujniki oraz sterowanie pakowarkami
Pakowarki wyposaża się w liczne czujniki i systemy sterowania. Przykładem są sensory ultradźwiękowe używane do bezkontaktowego pomiaru średnicy beli materiału, na przykład folii, nawiniętego na rolkę, z której jest stopniowo odwijany, gdy formowane są kolejne opakowania. Kiedy promień beli jest znany, sterownik maszyny oblicza, ile jeszcze folii zostało, a gdy jest jej zbyt mało, sygnalizuje operatorowi, że powinien uzupełnić podajnik.
Czujniki ultradźwiękowe są także używane w pomiarach ustawienia napinacza folii, który reguluje stopień naciągnięcia jej wstęgi. Na ich podstawie sterownik maszyny decyduje, czy należy zwolnić, czy raczej powinno się przyspieszyć obroty rolki, która odwija folię.
Kolejny przykład to sensory wykrywające znaczniki na materiale rozmieszczane w odległościach równych długości kolejnych torebek. Odczytując je, sterownik maszyny w odpowiednim momencie wysyła sygnały
wyzwalające do obcinarki odcinającej kawałki materiału i zgrzewarki, która łączy jego brzegi. W tym zastosowaniu wykorzystuje się czujniki optyczne.
W zakresie sterowania pakowarkami kluczowe znaczenie dla jakości i wydajności pakowania ma synchronizacja zadań formowania opakowania i jego napełniania. W tym celu część pakowarki odpowiedzialna za uwalnianie/dozowanie produktu musi we właściwym momencie odebrać sygnał wyzwalający albo odwrotnie – kiedy napełni opakowanie, powinna taki sygnał wysłać do części pakowarki formującej kolejne. Przeważnie stosuje się pierwsze podejście, synchronizując dozownik z pakowarką. Jeżeli zgrzewane opakowania są wkładane do pudełek, nadrzędną funkcję w obrębie linii pakowania składającej się w takim przypadku z pakowarki pionowej i automatu składającego, wypełniającego oraz zaklejającego kartony, pełni zazwyczaj ten ostatni.