Nowe technologie w systemach wizyjnych
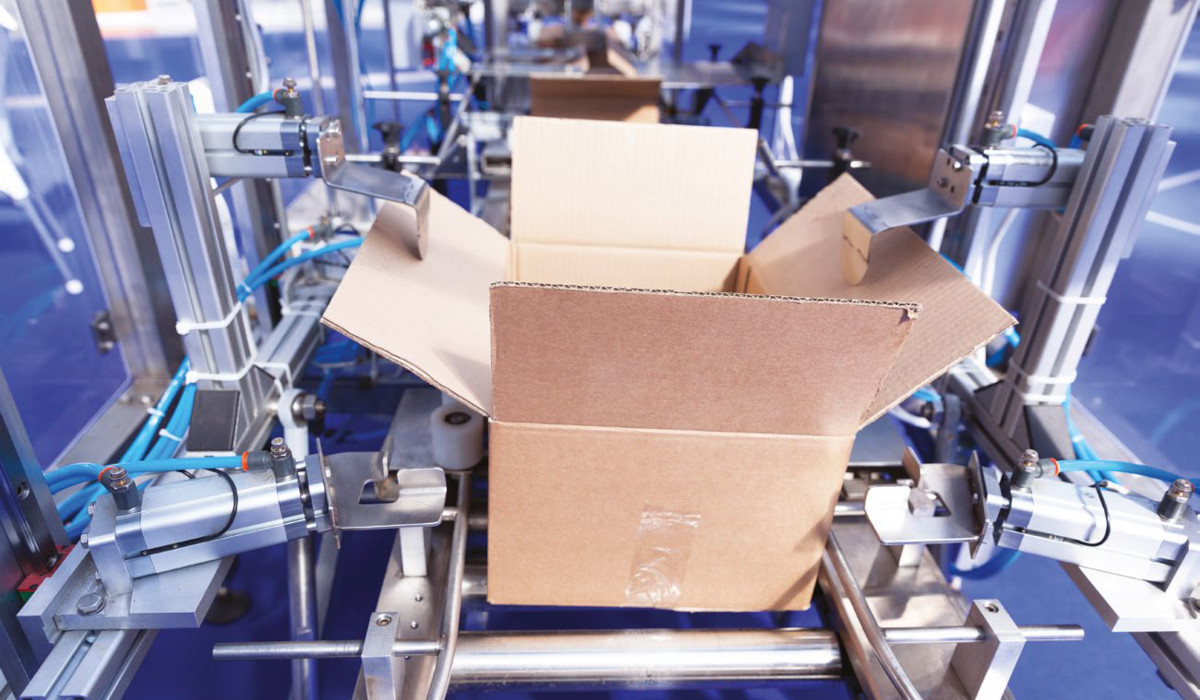
Aby operacja pick and place w odniesieniu do artykułów spożywczych zakończyła się sukcesem, musi uwzględniać jego specyfikę. Na przykład siła chwytania musi być wystarczająco mała, aby uniknąć uszkodzenia produktu, ale musi być jednocześnie odpowiednio duża, aby wykonać zadanie podnoszenia i odkładania bez jego upuszczania. Ponadto produkty spożywcze mają wiele odmian i występuję między nimi duże różnice w kształcie, rozmiarze, wadze, stanie powierzchni, miękkości i innych właściwościach fizycznych. By ułatwić pracę konstruktorom chwytaków, jak i później ich użytkownikom, prowadzi się prace nad kategoryzacją artykułów żywnościowych pod względem manipulowania nimi przez roboty przemysłowe. Dzięki temu w przyszłości być może będzie można zrezygnować z testów i szybciej projektować chwytaki przeznaczone do obsługi konkretnych grup produktów.
Wyzwaniem jest także sposób rozmieszczenia produktów na przenośniku. W produkcji spożywczej pod tym względem wyróżnia się generalnie dwa rozkłady: w pierwszym artykuły są ułożone w jednej linii albo są porozrzucane na przenośniku bez nakładania się, zaś w drugim są rozmieszczone losowo w pojemniku, w którym mogą się na siebie nakładać i ze sobą stykać. Do rozróżnienia poszczególnych obiektów w pierwszym przypadku wystarczy zwykle analiza obrazu 2D – wówczas zakłada się bowiem, że znane są informacje o głębokości produktu i należy rozpoznać tylko jego położenie i orientację w płaszczyźnie poziomej. W różnicowaniu produktów zazwyczaj wykorzystuje się informacje o kolorze i techniki dopasowywania wzorców. Coraz częściej w tym zastosowaniu stosuje się także techniki uczenia maszynowego. Jeżeli produkty mogą się na siebie nakładać i ze sobą stykać, wymagana jest analiza obrazu w 3D. W tym zakresie znane techniki dopasowania wzorców sprawdzają się przede wszystkim w rozpoznawaniu produktów o dobrze zdefiniowanych geometriach. W pozostałych przypadkach coraz częściej również sięga się po nowe rozwiązania, które stają się dostępne dzięki rozwojowi technologii sztucznej inteligencji.
Daniel Oblamski
Yaskawa Polska
Coraz większym zainteresowaniem cieszą się zaawansowane systemy wizyjne, które pozwalają na samoadaptację maszyn do warunków pracy. Jedną z najbardziej dynamicznie rosnących branż na rynku jest e-commerce. Procesy pakowania w handlu elektronicznym wyglądają zupełnie inaczej niż w standardowej branży produkcyjnej. Chodzi tu przede wszystkim o umieszczanie paczek o różnych rozmiarach, w różnych opakowaniach na jednej palecie, która następnie trafia do kuriera, a finalnie do nas – odbiorców. Wykonanie takiej operacji przez system automatyczny, bez wykorzystania systemów wizyjnych jest niemożliwe. Yaskawa ma gotowe rozwiązanie – Pack Master, które radzi sobie z tego typu problemami. Jest to automat wyposażony w jednego lub dwa roboty, uniwersalny chwytak, zaawansowany system wizyjny 3D oraz układ zarządzający paletami. Pozwala na paletyzację pomiędzy 800 a 1500 najróżniejszych paczek w ciągu godziny. Na podstawie systemu wizyjnego algorytm wskazuje, w którym miejscu robot ma odłożyć paczkę. Zapraszamy zarówno centra logistyczne, duże e-commerce oraz firmy zainteresowane wdrażaniem tego typu rozwiązań u klientów. |
Paletyzacja
W opakowania transportowe produkty opakowywane są na paletach. Układa się je na nich w stos w taki sposób, by jak największa ich liczba zajmowała jak najmniej miejsca. Jednocześnie ważna jest stabilność ładunku. Nie wolno też dopuścić do jego przesuwania się na palecie, jej przewrócenia ani zniszczenia poszczególnych paczek. Zadanie to w całości lub częściowo się automatyzuje.
W półautomacie paletyzacja przebiega następująco: najpierw paczki są przenoszone taśmociągiem na stanowisko, gdzie po dotarciu do ogranicznika układane są jedna przy drugiej, tworząc z kilku sztuk rząd. Następnie paczki ustawione w linii operator przesuwa na podnośnik. Na nim, rząd po rzędzie, układana jest warstwa. Gdy jest już gotowa, paczki zostają ze wszystkich stron wyrównane przez prowadnice. W kolejnym kroku płyta podnośnika przesuwa się nad paletę, gdzie zostaje wycentrowana nad poprzednią warstwą paczek. Następnie stopniowo wysuwa się spod nich, a te rząd po rzędzie układają się na ich poprzedniej warstwie. Gdy paleta jest pełna, paczki są ponownie wyrównywane i zabiera ją wózek widłowy.
Jak uniknąć problemów podczas paletyzacji?![]() Organizując i nadzorując zrobotyzowany system paletyzacji, należy rozważyć szereg kwestii, by nie doświadczać przestojów, uzyskać maksymalną wydajność i by załadunek na palety nie pogarszał jakości produktów. Dobierając komponenty systemu, jak chwytaki, powinno się przede wszystkim wziąć pod uwagę zmienność wymiarów opakowań układanych na palety. Jeżeli tolerancja ich rozmiarów nie zostanie uwzględniona, mogą być upuszczane i zgniatane. Także przez opakowania o nieregularnych kształtach załadowane palety nie będą się prezentować schludnie, co ma wpływ na opinię konsumentów, jak również stabilność stosów, w które są układane produkty. Pojedyncze mogą z nich nawet wypadać podczas transportu. Na pracę dystrybutora palet wpływa ich jakość. Przykładowo te zamoczone podczas przechowywania na zewnątrz będą się sklejać, zwłaszcza w chłodniejszych warunkach. Dlatego warto je odstawić do wysuszenia dzień przed załadunkiem. Sczepiać będą się również palety z wystającymi gwoździami i podniszczonymi deskami. Znaczenie ma też tolerancja ich wymiarów. Przykładowo mokre palety pęcznieją. Różnice wymiarów w stosunku do tych spodziewanych znacząco wpływają na jakość paletyzacji. Dotyczy to szczególnie wysokości. Na przykład jeżeli paleta jest niższa, przy załadunku produkt zostanie upuszczony z większej wysokości, a jeżeli wyższa – zostanie wgnieciony. Ponadto jeśli robot nie jest wyposażony w czujnik wysokości palet, jego chwytak może się zderzyć ze stosem. Ważna jest też jakość przekładek używanych do separowania kolejnych warstw produktów. Istotne są ich wymiary i płaskość, uwaga zatem na wilgoć w otoczeniu, przez którą mogą ulec wypaczeniu. |
Aby zwiększyć przepustowość, usprawnia się tworzenie rzędów i warstw wykorzystując złożone systemy przenośników w pełni automatyzujące paletyzację. W zależności od konfiguracji systemu palety są obniżane z każdą uformowaną warstwą (układanie w dół) albo pozostają nieruchome, gdy podnoszone są warstwy paczek na podnośniku (układanie w górę). Półautomatyczne i automatyczne stanowiska paletyzacji dodatkowo wyposaża się w automatyczne foliarki. Owijają one w folię rzędy albo warstwy pakunków, co chroni je przed uszkodzeniem i stabilizuje ładunek palety.
W paletyzacji korzysta się też z robotów. Wyróżnia je większa elastyczność w zakresie zmiany typu obsługiwanych palet i wzorca układania paczek oraz szybkość. Najpopularniejsze typy robotów w tym zastosowaniu to: kartezjańskie, SCARA, przegubowe. Pierwsze zwykle nie sprawdzają się w paletyzacji z dużą przepustowością. Roboty SCARA wyróżnia większa wydajność operacyjna w porównaniu z kartezjańskimi, ale z drugiej strony ich udźwig nie przekracza 20 kilogramów. Sprawdzają się za to w wielotorowych liniach pakowania. Najelastyczniejsze rozwiązanie to roboty przegubowe. Charakteryzuje je również duża szybkość i udźwig, dlatego są najczęściej używane w paletyzacji.
Monika Jaworowska