Roboty w pakowaniu pick & place
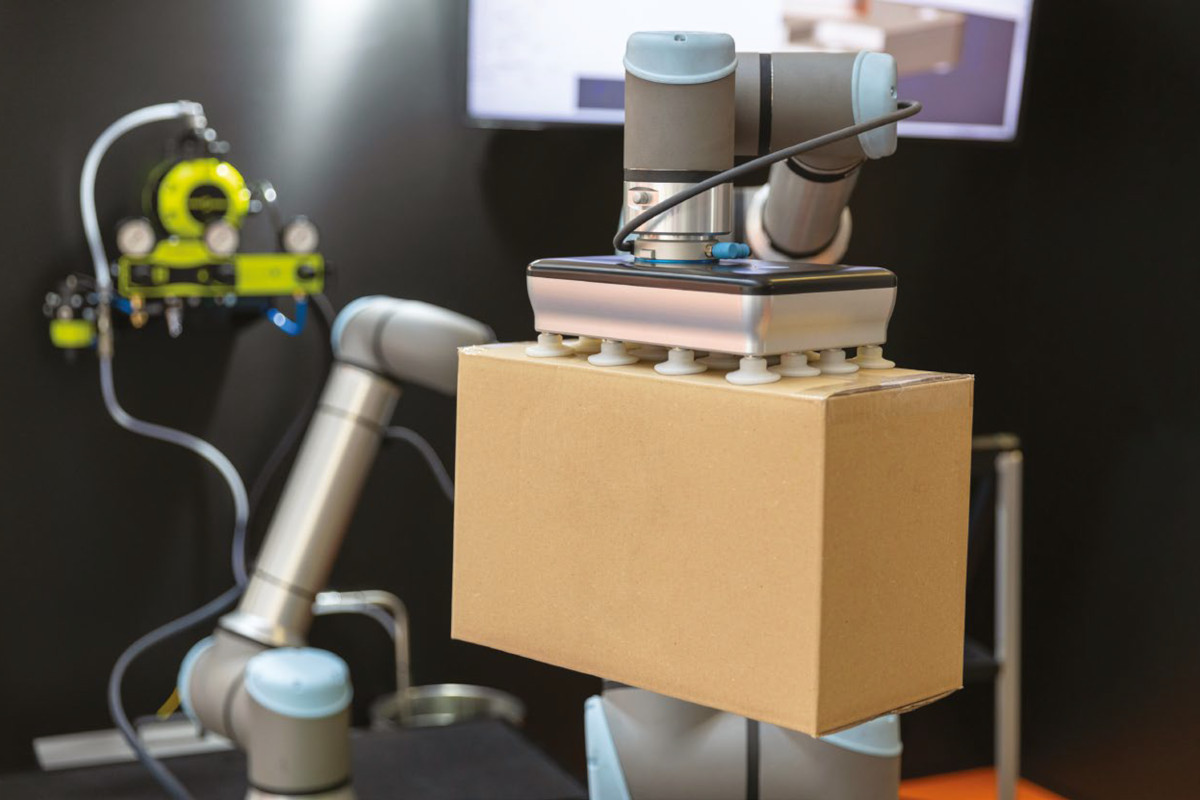
Na liniach pakowania powszechne są też roboty przemysłowe. Zwykle realizują zadania typu pick and place. Składa się na nie następująca sekwencja czynności: podniesienie obiektu, jego przeniesienie, a potem odłożenie go w miejscu docelowym, często z zachowaniem konkretnej orientacji. Takiego podejścia wymagają produkty, które należy, ze względu na ich specyfikę, podnosić i odkładać pojedynczo. Przykładami są drobne artykuły spożywcze o delikatnej strukturze, jak ciastka czy czekoladki, które przez roboty na stanowiskach pakowania są przekładane z taśmociągu linii produkcyjnej do pudełek. Wspólnymi cechami typowych aplikacji pick and place są: bardzo duża szybkość operowania przekładanymi obiektami i stosunkowo krótkie odległości, na jakie są one przenoszone.
W zadaniu tym najczęściej wykorzystuje się roboty typu delta i SCARA. Producenci implementują w nich rozwiązania, dzięki którym lepiej sprawdzają się w takich aplikacjach. Przykładowo, biorąc pod uwagę fakt, że na stanowisku pakowania robot powinien się zmieścić razem z przenośnikiem i innym wyposażeniem pomocniczym, na przykład podajnikami opakowań zbiorczych, optymalne wykorzystanie dostępnej przestrzeni jest kluczowe. Spełnienie tego wymogu jest łatwiejsze dzięki robotom o ultralekkim i kompaktowym wykonaniu. Pracę w ograniczonej przestrzeni ułatwia też prowadzenie okablowania przez ramię robota, co zapewnia skuteczną ochronę przewodów bardziej narażonych na uszkodzenie w ciasnej przestrzeni.
Oprócz tego, aby zapewnić współpracę z przenośnikami o różnych szerokościach, wprowadzane są rozwiązania zwiększające zasięg robota, jak na przykład dodatkowe ramię i obrotowa platforma w robotach typu delta. Pamiętając o tym, że w zadaniu pick and place liczy się szybkość, ramiona robotów są konstruowane w taki sposób, aby duża prędkość była osiągalna w całym zakresie ruchu. Ważne jest także równomierne obciążenie napędów, od którego zależy powtarzalność i płynność ruchu chwytaka. Dzięki wieloosiowym nadgarstkom roboty mogą swobodnie obracać przedmioty.
Ponadto biorąc pod uwagę ogromny udział przemysłu spożywczego w branży opakowaniowej, producenci robotów do aplikacji pick and place z myślą o pakowaniu produktów żywieniowych oferują roboty w wykonaniu spełniającym wymogi higieniczne tego zastosowania. Typowe ich cechy to: gładkie, łatwe do czyszczenia powierzchnie, stosowanie smarów dopuszczonych do użytku w przemyśle spożywczym, stopień ochrony IP69K.
Maszyny i roboty usprawniają pakowanie i paletyzację![]() Case study 1: Producent kostek lodu rozbudował park maszynowy. Przez większą wydajność produkcji pakowanie, które nie jest zautomatyzowane, stało się wąskim gardłem. Już wcześniej był to problematyczny etap, ręczne operacje odbywały się bowiem w warunkach niekorzystnych dla personelu. Po pierwsze, ponieważ temperatura w tej sekcji wynosiła +5ºC, dla zachowania jakości produktu od pracowników wymagano dużej szybkości pracy. Problemem były także ograniczenia przestrzenne, przez które musieli się oni ciągle obracać, żeby sięgnąć po karton, który formowali w pudełko i po produkt w nim umieszczany. Rozwiązaniem okazała się częściowa automatyzacja pakowania. W tym celu zainstalowane zostały dwa ciągi przenośników umieszczone na optymalnej wysokości w stosunku do nieco niższych stanowisk ręcznego pakowania. Służą one do transportu woreczków z kostkami lodu. Wspólnym dla obu ciągów przenośnikiem ustawionym między nimi dostarczane są pudełka składane w zautomatyzowanej formownicy. Pakowacze mogą regulować prędkość podawania pustych pudełek odpowiednio do szybkości transportu worków z lodem. Pełne opakowania ustawiają na trzecim, wspólnym przenośniku, transportującym je do zaklejarki. Dzięki temu zlikwidowano wąskie gardło, jednocześnie poprawiając warunki pracy. Case study 2: Producent żywności paczkowanej chciał zwiększyć przepustowość paletyzacji. Wymagał również obsługi różnych typów palet i opakowań i elastyczności w sposobie załadunku palet. By spełnić te wymagania, skompletowano stanowisko jak na rysunku 2. Paleta jest przekazywana z zasobnika palet 1 na przenośnik palet 2. Z zasobnika przekładek 3 pobierana jest przekładka umieszczana na palecie. Równocześnie opakowania są przekazywane na przenośnik akumulacyjny 4, a następnie obracane o 90º (5). W strefie kompletacji są liczone i przenoszone na stanowisko robota (6). Jest on wyposażony w chwytak do podnoszenia jednocześnie wielu pudełek. Przenosi je na stanowisko kompletacji palet (7). Załadowana paleta jest przenoszona na stanowisko odbioru (8), oddzielone kurtyną świetlną dla bezpieczeństwa. Stąd wywozi ją wózek widłowy. Cele projektowe udało się spełnić dzięki temu, że chwytak robota dobrano tak, żeby unosił do 10 opakowań jednocześnie, a zwalniał cały rząd lub jego część. Pudełka są obracane i przekierowywane mechanicznym popychaczem w locie. Zasobnik zwalnia nową paletę, gdy poprzednia opuszcza stanowisko. Jest przystosowany do magazynowania i zwalniania palet różnego typu. ![]() Case study 3: Producent soku w kubeczkach, aby zwiększyć przepustowość i odciążyć personel w obsłudze oraz rozwiązywaniu problemów, postanowił zautomatyzować stanowisko ich pakowania. Warunkiem było też, by w trakcie tej operacji uszkodzeniu nie ulegały foliowe wieczka kubeczków. Pierwszy cel osiągnięto, wykorzystując dwa roboty. Pierwszy układa warstwy z maksymalnie 24 kubeczków jednocześnie w jednym lub dwóch pudełkach. Drugi, zsynchronizowany z nim, pobiera z zasobnika przekładki i wkłada je między warstwami. Wybrane modele zapewniły przepustowość pakowania 500 kubeczków na minutę, co przekraczało cel projektowy (300 sztuk/min). Zapewniało to margines w przypadku wzrostu wydajności produkcji bez konieczności wprowadzania zmian na stanowisku pakowania. Aby z kolei zapobiec przebijaniu zafoliowanych wieczek i rozlewaniu soku, wykorzystano system prowadnic zaprojektowanych tak, by zapobiec ich przewracaniu się i zaczepianiu, a robot pakujący wyposażono w przyssawki. Obsługę ułatwia to, że przezbrajanie elementów stanowiska można wykonywać beznarzędziowo, za pośrednictwem panelu operatorskiego. |
Wyzwania w robotyzacji zadania pick & place
Tytułowe zagadnienie przedstawiamy na przykładzie przemysłu spożywczego. Do zadań z dziedziny produkcji i przetwarzania żywności przeważnie wykorzystywane są maszyny zaprojektowane pod kątem specyfiki produktu. Dedykowanych rozwiązań wymaga również pakowanie. W przypadku stanowisk zrobotyzowanych obejmują one głównie specjalne chwytaki, algorytmy rozpoznawania obrazów i techniki manipulowania.
Sekwencja operacji, podnieś i odłóż, dla ludzi nie jest trudna do wykonania. Robot może mieć z nią jednak szereg trudności, zwłaszcza jeżeli ma manipulować artykułem spożywczym, szczególnie w operacji pakowania, gdy jego zadaniem jest podniesienie, a potem odłożenie produktu surowego lub przetworzonego o specyficznych właściwościach. Artykuły spożywcze są bowiem w większości niesztywne, czasami kruche i łatwo ulegają odkształceniu, obtłuczeniu i pobrudzeniu, gdy wchodzą w kontakt z twardą powierzchnią. Są też podatne na skażenie. Trzeba ponadto uwzględnić to, że na ich właściwości wpływają warunki środowiskowe, jak temperatura, wilgotność i ciśnienie.
Aby temu sprostać, chwytaki robotów powinny móc operować obiektami miękkimi, z nierównymi powierzchniami i niejednolitymi kształtami oraz spełniać wymagania higieniczne. Ponadto muszą dostosowywać się do różnych typów powierzchni, na przykład mokrych i lepkich. Powinny też składać się z niewielkiej liczby elementów mechanicznych, by ograniczyć prawdopodobieństwo ich wpadnięcia do produktu spożywczego. W celu spełnienia tych wymagań opracowywane są różne konstrukcje chwytaków. Można je podzielić na kilka kategorii ze względu na sposób, w jaki stykają się z podnoszonym obiektem (rys. 1). Dalej przedstawiamy wybrane z nich.
Chwytaki
Do grupy manipulatorów, które chwytają przedmiot od góry (rys. 1a) zalicza się m.in.: przyssawki, chwytaki Bernoullego, te wykorzystujące naturalną przyczepność produktu, chwytaki zamrażające wilgotne powierzchnie i te wbijające w produkt igłę. Pierwsze wyróżnia prosta konstrukcja oraz stabilny chwyt. Z drugiej strony przyssawki najlepiej sprawdzają się, gdy powierzchnia obiektu jest płaska, gładka oraz sucha. Mogą jednak zostawiać ślady, w szczególności na surowych produktach spożywczych.
Wady te nie dotyczą chwytaków Bernoullego o minimalnej styczności z obiektem podnoszenia. Jednak ich chwyt nie jest stabilny. Zakres zastosowania chwytaków dwóch kolejnych typów jest ograniczony. Te wykorzystujące siłę adhezji są używane do podnoszenia produktów o klejącej powierzchni, jak na przykład ciasto, a zamrażające do tych mokrych, m.in. świeżych ryb. Te drugie wymagają dodatkowego mechanizmu do uwolnienia przenoszonego obiektu, na przykład przez odcięcie nożem albo podgrzanie.
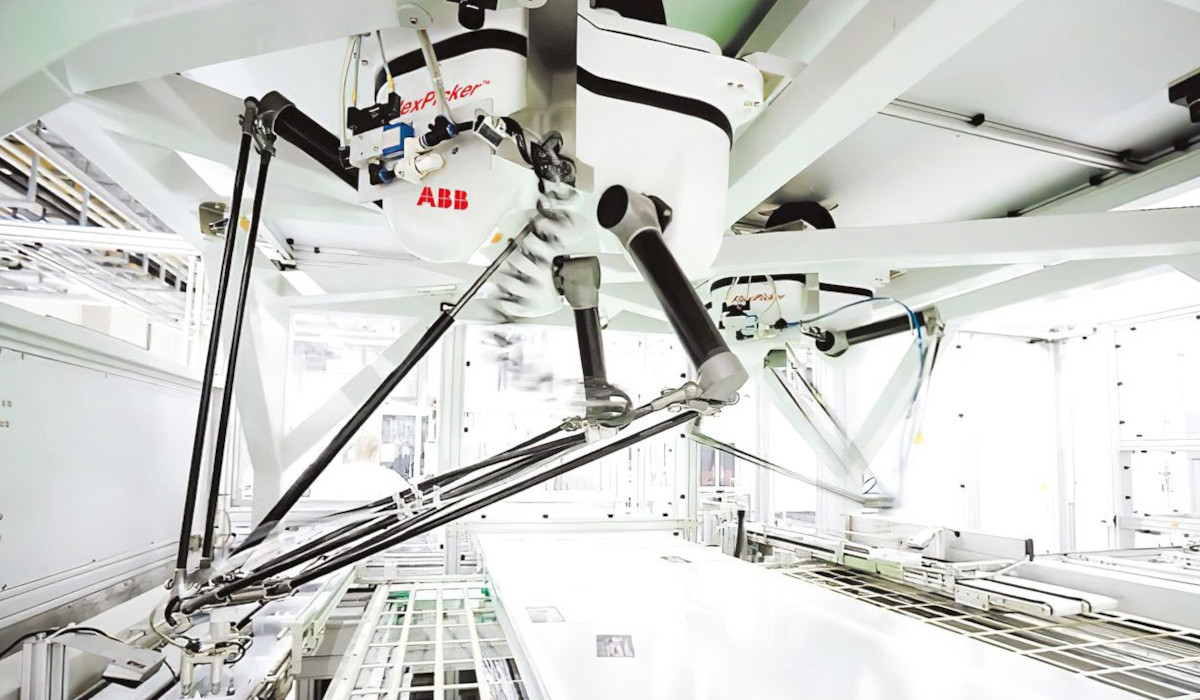
Zaletą podnoszenia produktu za jego boki, gdy jest on zamknięty wewnątrz chwytaka (rys. 1b), jest możliwość dokładnego wypozycjonowania obiektu i łatwość regulacji. Z drugiej strony rozmiar produktu musi być znany zawczasu, by chwytak mógł do niego dostosować swój rozstaw. Ważne jest także zapewnienie wystarczającej siły tarcia między powierzchnią obiektu i chwytakiem, by ten pierwszy się nie wyślizgnął. Do tej kategorii zaliczane są chwytaki palczaste – typowo dwu-, ale też i wielopalczaste. Konstrukcja tych do zastosowania w przemyśle spożywczym jest modyfikowana tak, by nie uszkadzały przenoszonej żywności. W ostatnich latach w tym zakresie nastąpił znaczny postęp – opracowanych zostało wiele miękkich chwytaków na potrzeby różnych typów artykułów spożywczych. Przeważnie są napędzane pneumatycznie i pokrywane materiałem silikonowym. Dostępne są też w wykonaniu z materiałów elastycznych, które dostosowują się do kształtu obiektu.
Podnoszenie od spodu (rys. 1c) nie jest popularne w przemyśle ze względu na łatwość ześlizgnięcia się produktu. Dostępne są natomiast chwytaki do podnoszenia przez pochwycenie zarówno górnej, jak i bocznej powierzchni przedmiotu (rys. 1d). W tej grupie popularne jest łączenie siły ssania i chwytania – w użyciu są na przykład chwytaki wielopalczaste z przyssawkami na końcach palców. Chwytanie tylko za powierzchnie boczne i dolne (rys. 1e) w pakowaniu artykułów żywnościowych nie jest raczej praktykowane. Połączenie typów chwytania z rysunku 1d i 1e wykorzystują za to chwytaki łapiące za górną, boczną i dolną powierzchnię produktu (rys. 1f).
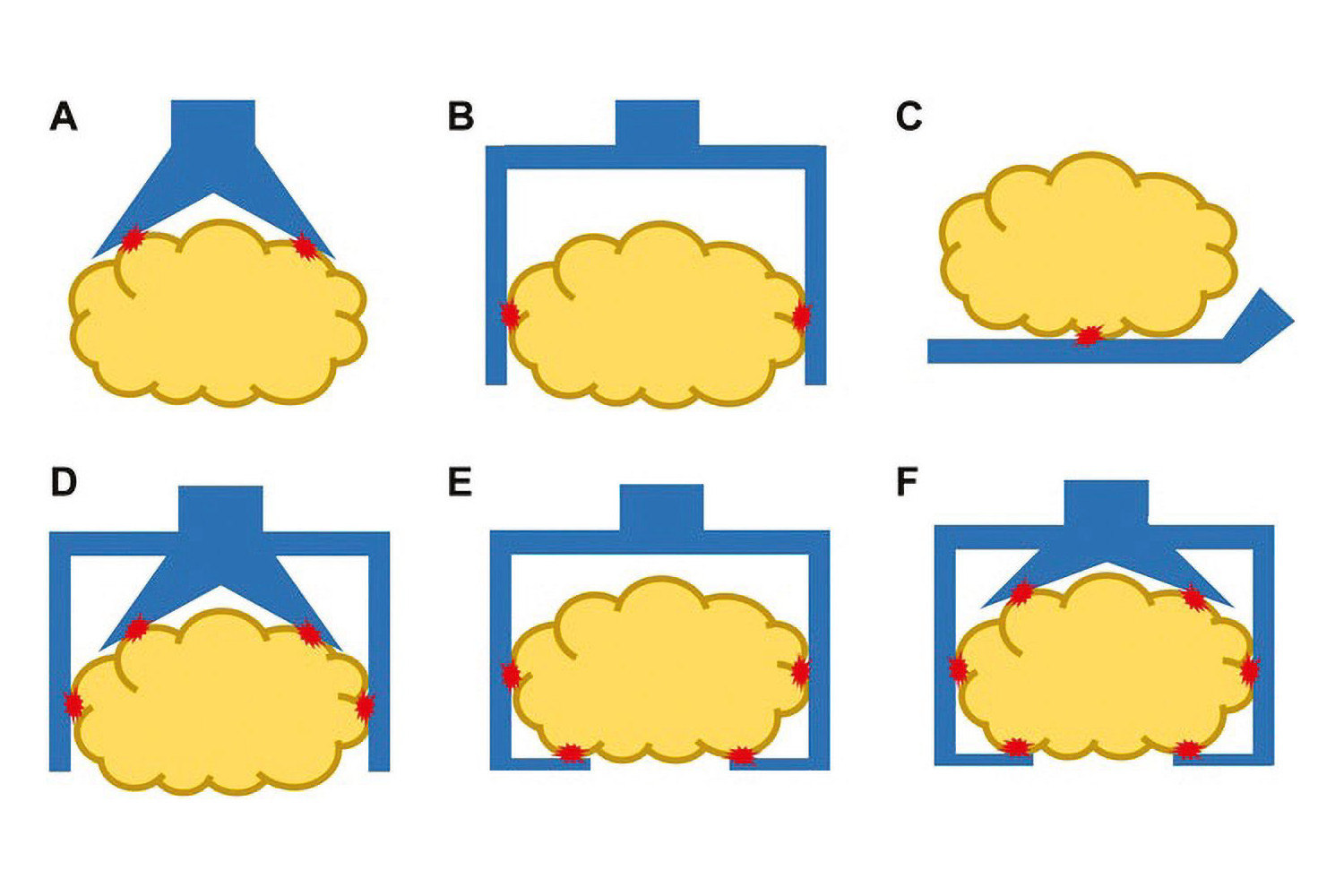