Typowe parametry cobotów
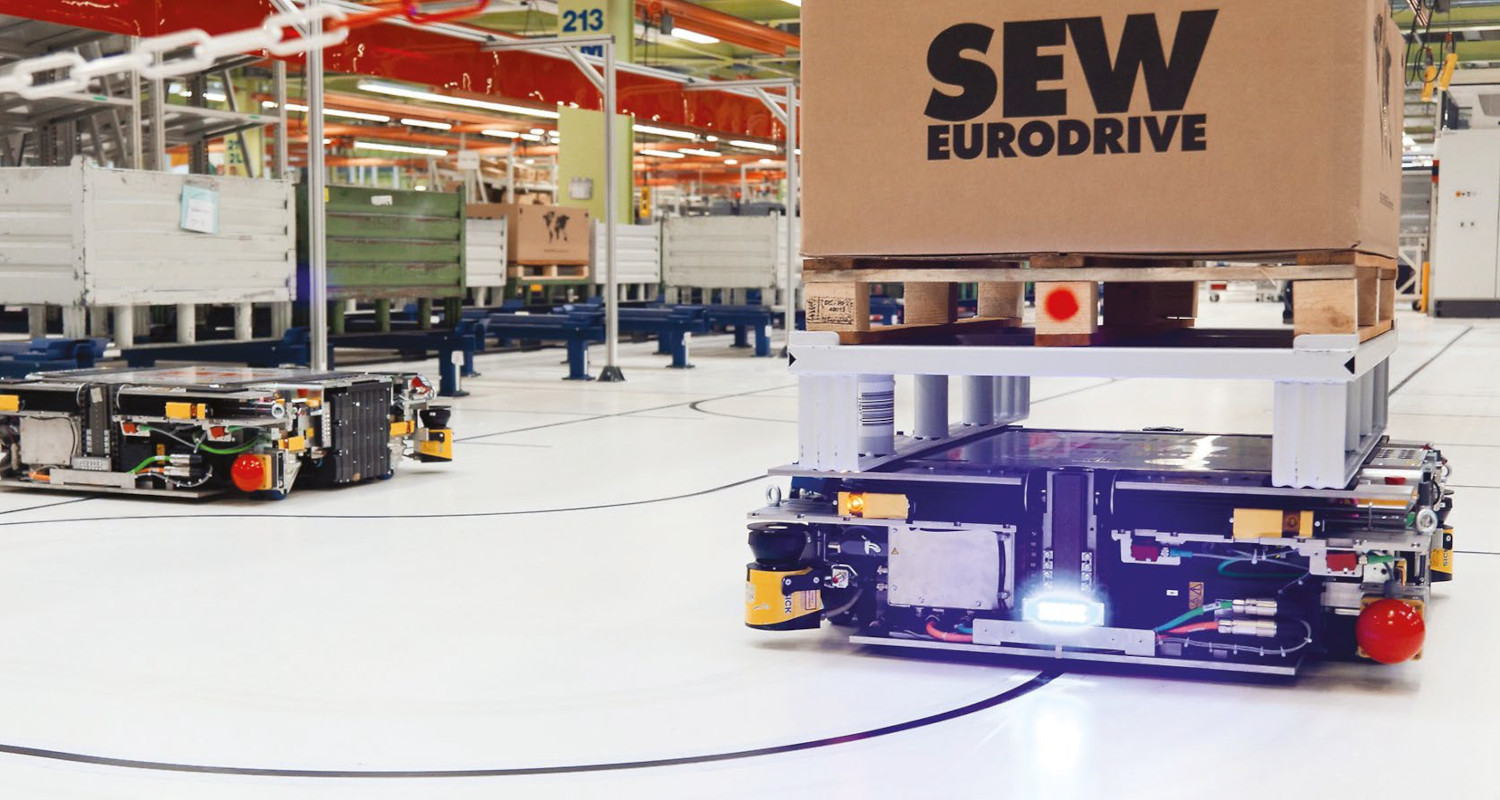
Nośność typowych cobotów zaczyna się już 0,5 kg, a kończy się na wartości 40 kg. Maksymalny zasięg opisanych w tabeli urządzeń wynosi od około 600 mm do około 2000 mm. Poza nielicznymi wyjątkami maszyn specjalizowanych, większość dostawców cobotów oferuje rozwiązania nadające się do wszelkiego rodzaju prac, takich jak spawanie i zgrzewanie, malowanie, montaż, pakowanie, paletyzacja, przenoszenie, uszczelnianie oraz mycie i czyszczenie. Większość robotów dostosowana jest także do manipulowania towarami delikatnymi – występującymi m.in. w przemyśle spożywczym. Oferowane urządzenia nadają się także bardzo często do obróbki mechanicznej i polerowania oraz montażu elektroniki i naturalnie obsługi gniazd produkcyjnych. Dostawcy dostarczają bogate wyposażenie dla swoich modeli, m.in. chwytaki, czujniki, osłony i elementy wizyjne.
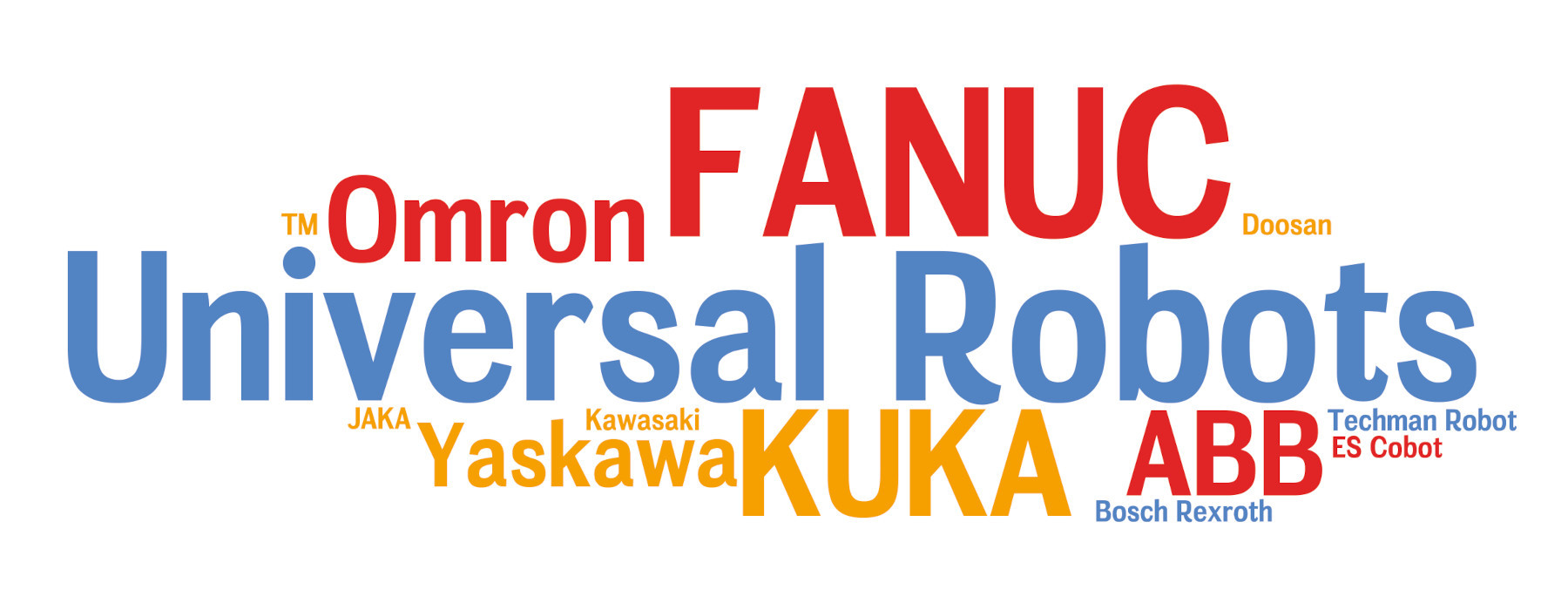
Rynek robotów mobilnych
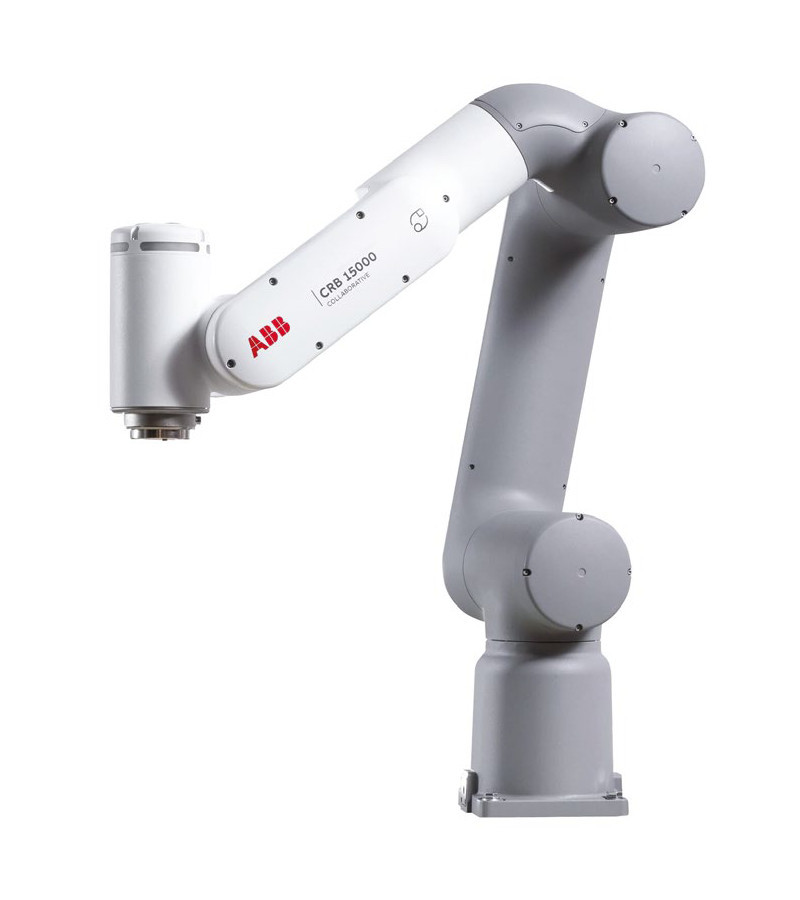
Szacunki ankietowanych dotyczące rynku robotów mobilnych znacząco się różnią między sobą. Oceny liczby dostarczanych maszyn wahają się od 80 do aż 1000 sztuk rocznie, a tempo wzrostu rynku krajowego – od 5% do 80%. W 2021 roku wartość rynku szacowana była przez naszych ankietowanych na 30‒500 sztuk rocznie, natomiast szacunki rocznego wzrostu podawane były w granicach od 10% do 250%. Jednak wyrażane przez pewną część naszych ankietowanych bardzo optymistyczne prognozy przyspieszenia sprzedaży wpisują się w światowe trendy na rynku robotów mobilnych. Według raportu badawczego wykonanego w 2022 roku przez Market Research Future (MRFR) "Mobile Robotics Market Research Report"² do 2030 roku należy spodziewać się wartości rynku AGV wynoszącej 25,3 mld USD przy średnim rocznym tempie wzrostu (CAGR) na poziomie 21,4%. Z kolei według Interact Analysis globalny rynek robotów mobilnych odnotował w 2022 roku aż 53-procentowy wzrost dostaw³. Analitycy tej firmy badawczej spodziewają się, że w najbliższych latach przychody na światowym rynku będą rosły średnio o 30‒40% rocznie.
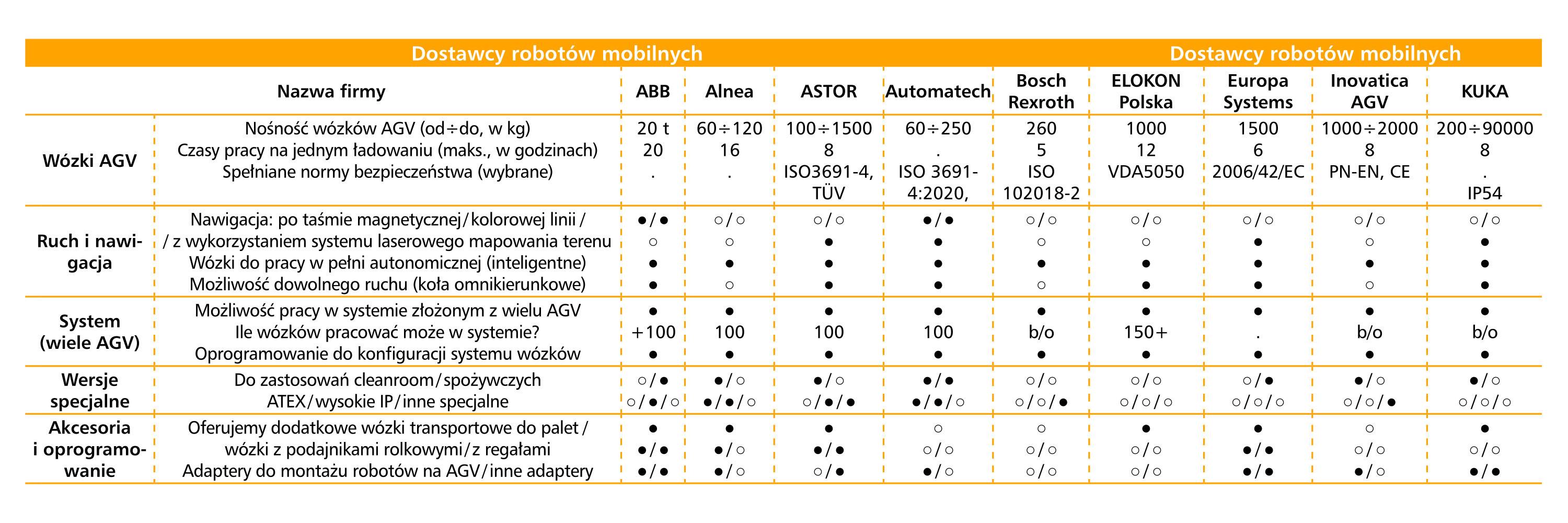
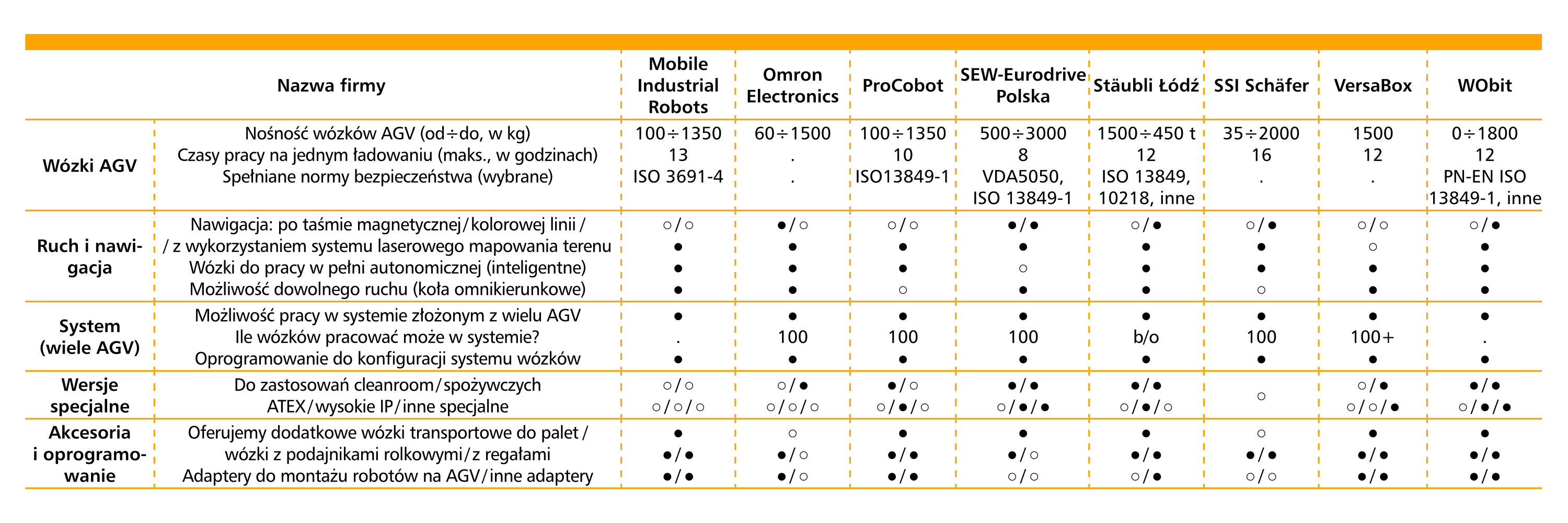
Zdaniem respondentów ankiety do najczęstszych zastosowań AGV należą dwie aplikacje wyróżniające się w sposób szczególny. Pierwsza to produkcja i intralogistyka (91% wskazań respondentów), natomiast drugą jest logistyka magazynowa (85%). Roboty mobilne występują także, choć są już mniej popularne, w takich zastosowaniach jak laboratoria i R&D oraz inne aplikacje komercyjne oraz te poza przemysłem. Porównując sytuację z 2021 rokiem, nie widać znaczących różnic. Wyjątkiem jest pojawienie się w tegorocznym zestawieniu po raz pierwszy pozycji "Laboratoria, R&D, itp.".
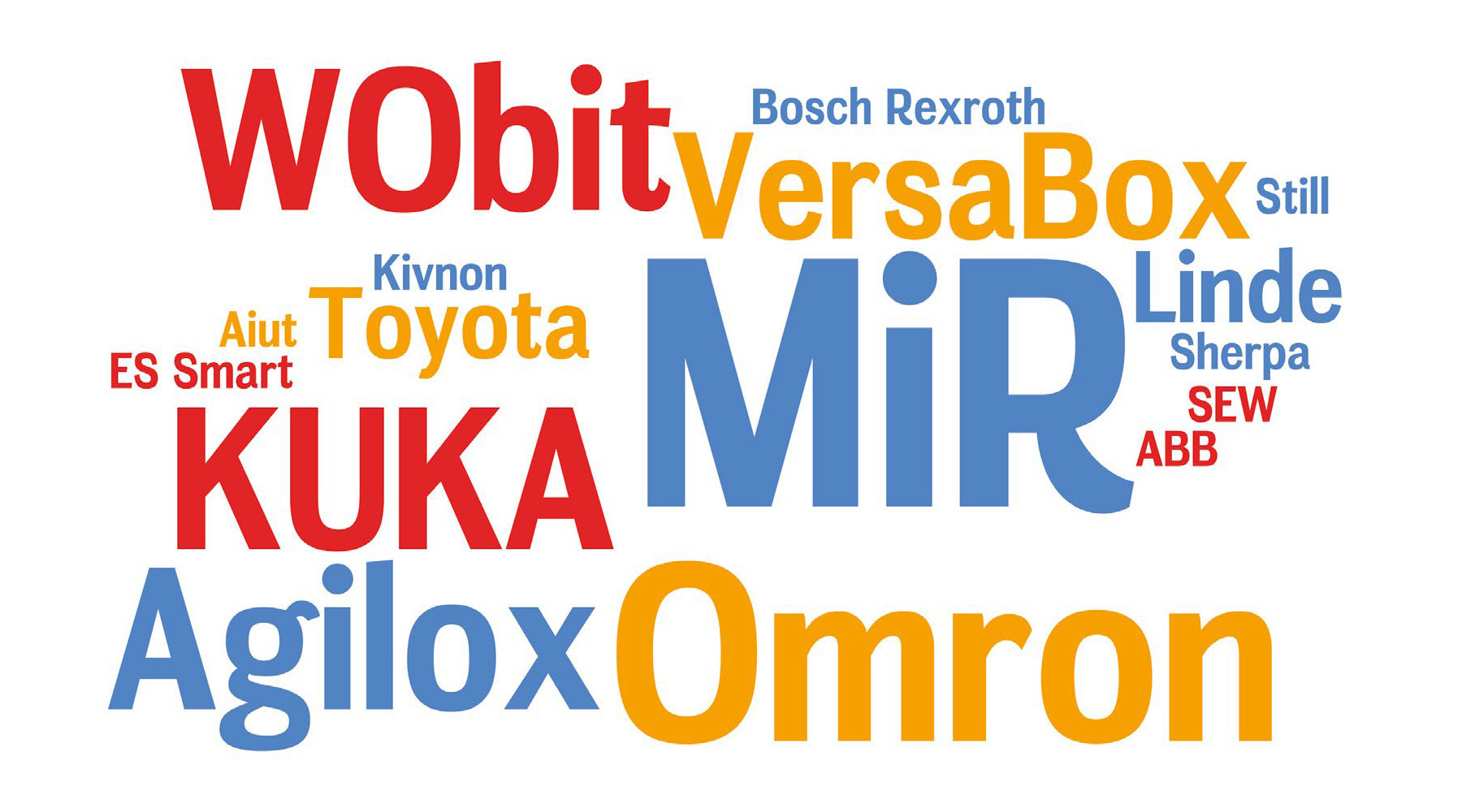
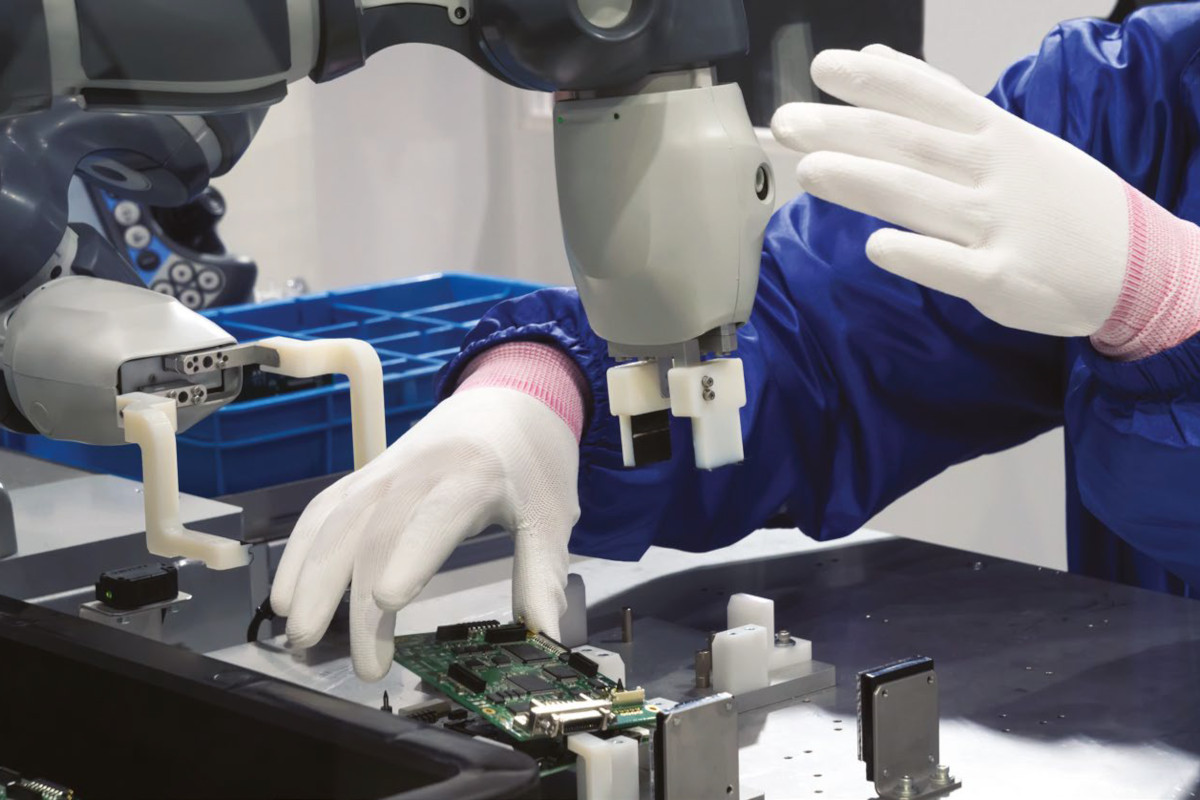
Wybierając AGV, klienci zwykle kupują je pojedynczo, aby sprawdzić możliwości tych maszyn, a następnie rozbudowują swoją flotę o nowe jednostki. Taki model inwestycyjny wskazało 75% respondentów, natomiast 19% ankietowanych skłania się ku opcji, w której klienci planują od razu złożony system składający się z wielu AGV pracujących wspólnie. Według 6% ankietowanych klienci kupują te roboty pojedynczo, na sztuki. W porównaniu z 2021 roku widać znaczącą zmianę w zachowaniach odbiorców. Dwa lata temu klienci częściej (45%) planowali od razu zakup całego systemu AVG złożonego z wielu jednostek pracujących wspólnie. Różnicę tę można traktować albo jako anomalię, wynik zbyt niskiej próbki danych lub interpretować w ten sposób, że obecnie więcej przedsiębiorstw wprowadza eksperymentalnie AGV do swoich zakładów, tak by sprawdzić ich użyteczność.
Zdaniem naszych respondentów do najbardziej popularnych producentów AGV oferowanych w Polsce należą marki: MiR, Omron, KUKA, Agilox i WObit. W porównaniu z poprzednim badaniem nie widać żadnej różnicy w czołówce zestawienia.
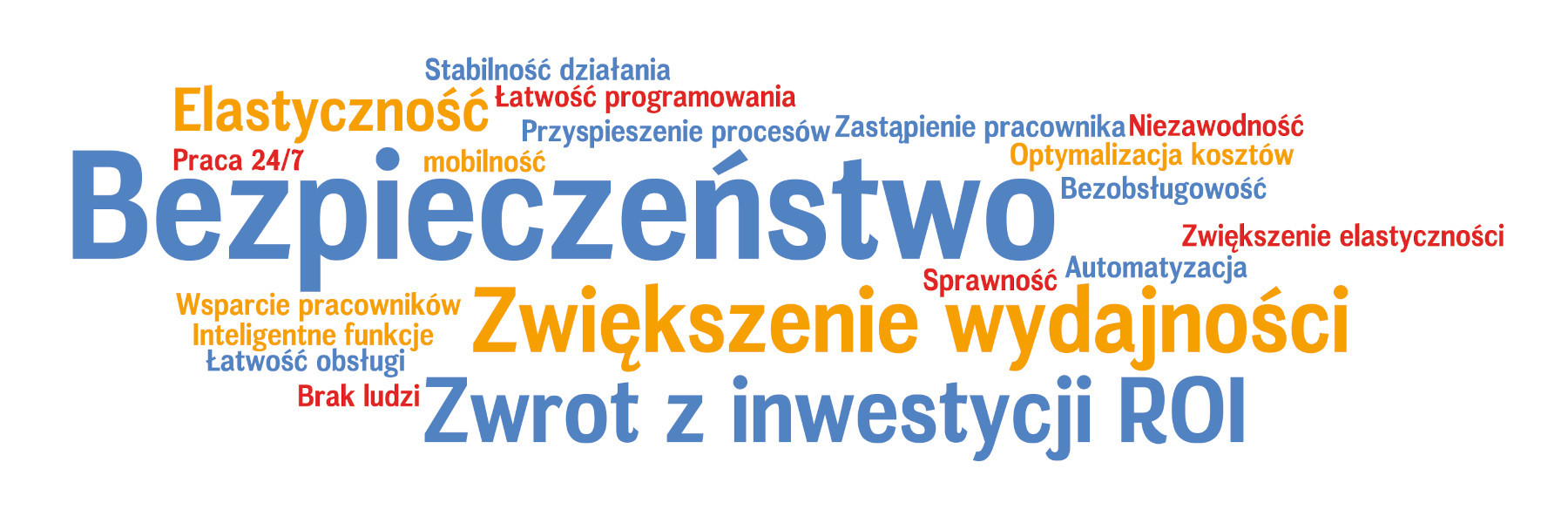
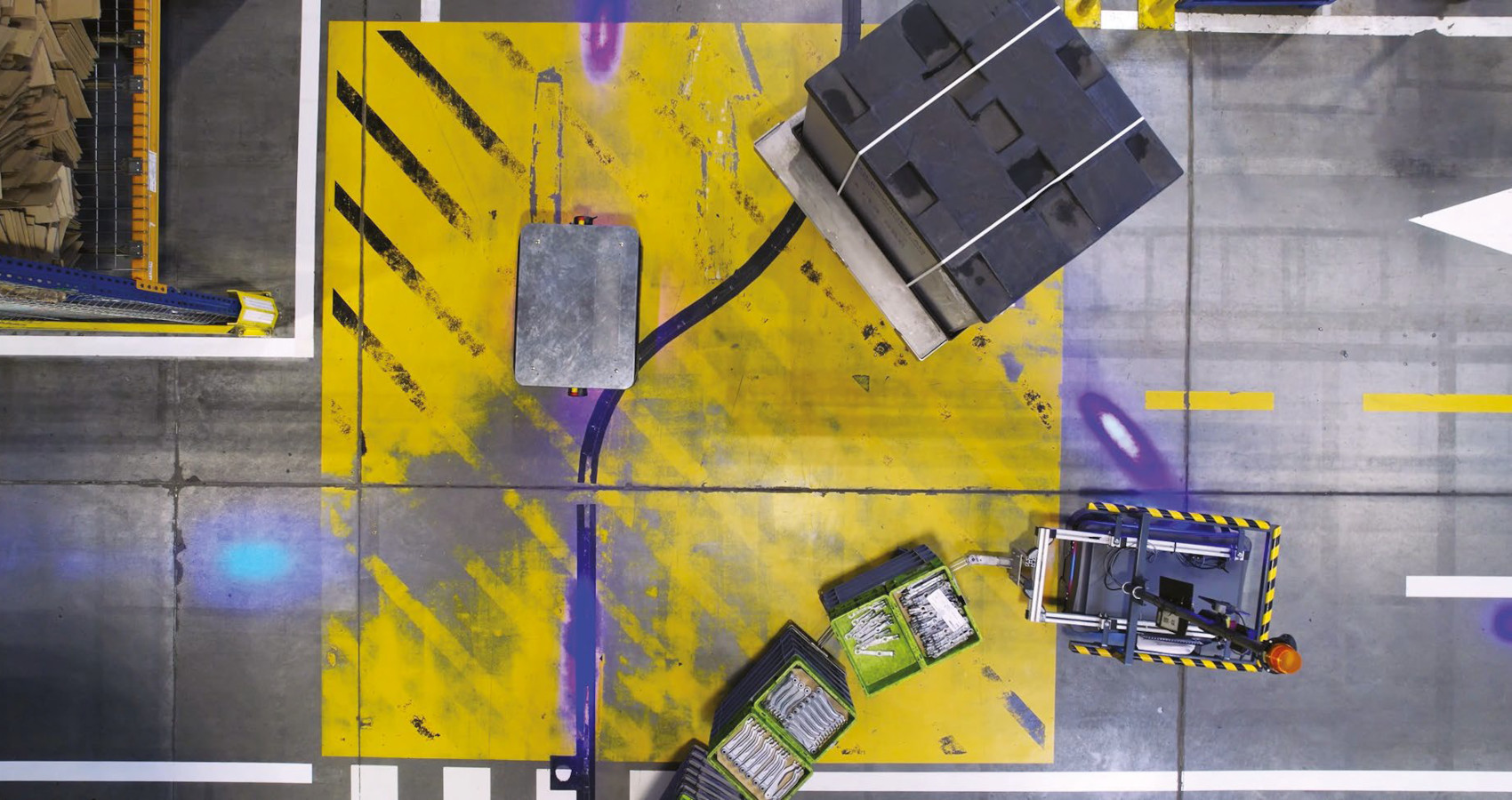
Według krajowych dostawców cechą, która w pierwszej kolejności przekonuje klientów do korzystania z AGV, jest bezpieczeństwo. Wśród innych ważnych własności robotów mobilnych wymieniane są także: szybki zwrot z inwestycji i poprawa wydajności produkcji. Porównując te wskazania z 2021 rokiem, nie widać istotnej różnicy. Także dwa lata temu na pierwszym miejscu znajdowało się bezpieczeństwo, natomiast pozostałe cechy plasujące się dość wysoko to: obniżenie kosztów, zwiększenie wydajności i optymalizacja procesów, które można traktować jako synonimy cech wskazanych w bieżących badaniu.
Branże, które są dla AGV najbardziej perspektywiczne, to zdaniem respondentów: logistyka, motoryzacja i, w nieco mniejszym stopniu, FMCG. Uzupełniając te spostrzeżenia, warto dodać, że identyczne branże wskazywali dostawcy w poprzednim badaniu rynku.
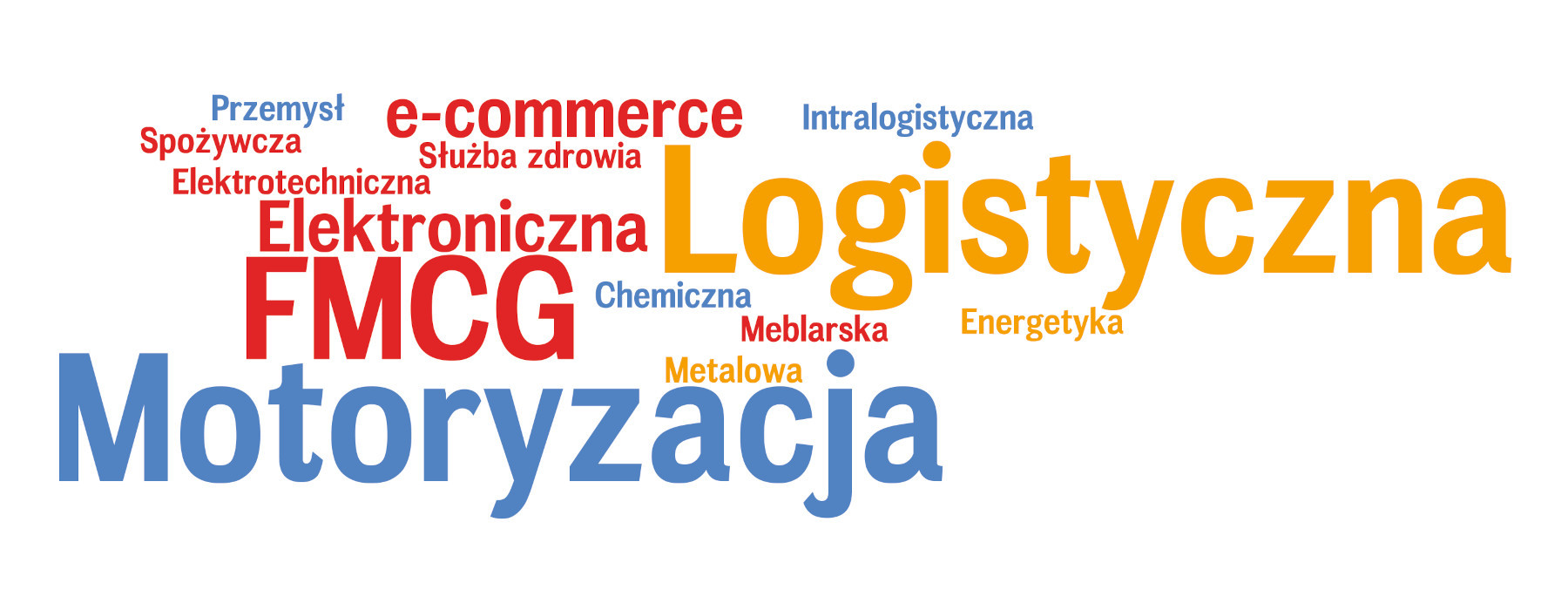