Rynek cobotów
Dla większości ankietowanych przez nas dostawców coboty stanowią tylko część oferowanego asortymentu, jednak około 25% z nich dostarcza wyłącznie te maszyny. Respondenci tegorocznej ankiety szacują krajowy rynek cobotów na 150‒600 sztuk rocznie, a tempo jego wzrostu – od 5% do 60%. Dwa lata wcześniej, tj. w badaniu z 2021 roku, wartość rynku oceniana była na 100‒500 sztuk rocznie, natomiast przyrosty – od 3% do 150%. Wyraźna tendencja wzrostowa raportowana przez naszych ankietowanych znajduje także potwierdzenie w trendach światowych. Według raportu "Collaborative Robot Market" wykonanego przez MarketsandMarkets¹ globalny rynek robotów współpracujących wzrośnie z 1,1 mld USD w 2022 r. do 9,2 mld USD w 2028 r., przy średnim wzroście rocznym (CAGR) na poziomie 41,5%.
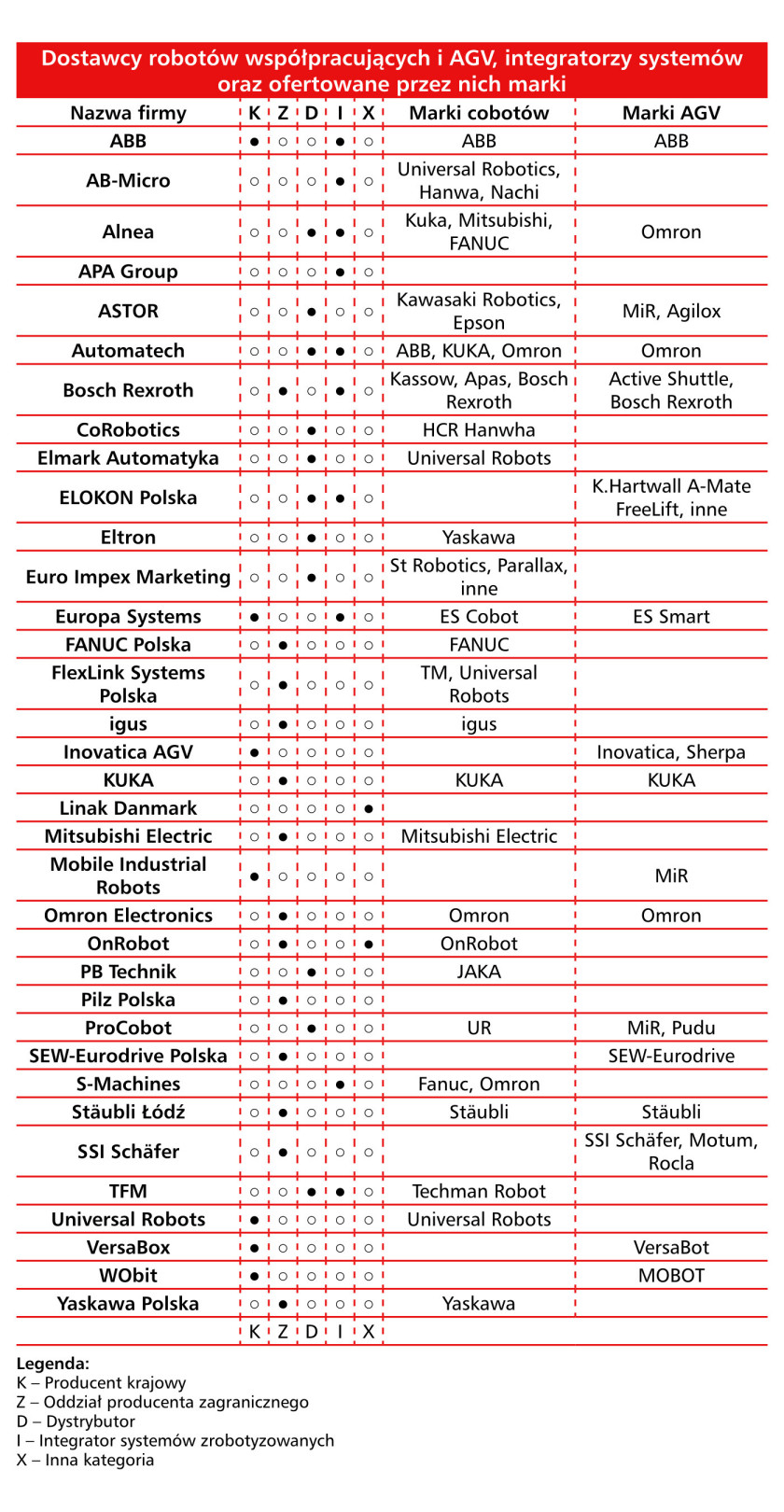
Najczęstsze zastosowania robotów współpracujących na rynku polskim to: pick & place (wskazane przez 90% ankietowanych), pakowanie (84%) oraz paletyzacja (83%). Do nieco mniej popularnych aplikacji należą montaż (71% wskazań), machine tending i obsługa gniazd (68%) oraz montaż elektroniki (63%).
Porównując obecną popularność poszczególnych aplikacji ze wskazanymi przez naszych respondentów w 2021 roku, nie dostrzeżemy zbyt dużych różnic. Dwa lata temu, podobnie jak obecnie, na pierwszym miejscu znajdowało się pick & place. Nieznacznie mniej popularniejszym zastosowaniem, w porównaniu do obecnych odczytów, był montaż oraz machine tending i obsługa gniazd. Jednak zarówno w 2021 roku, jak też obecnie, pierwsza piątka najpopularniejszych aplikacji zawiera te same pozycje.
Do najbardziej znanych marek cobotów w kraju należą: Universal Robots, FANUC i KUKA. Do tego grona aspirują nieco mniej rozpoznawalne w tym segmencie rynku: Omron, ABB i Yaskawa. W porównaniu do odczytu z 2021, czołówka w tej grupie pozostaje bez zmian. Można jednak zauważyć poprawę popularności marki KUKA, w każdym razie jeżeli chodzi o wskazania raportowe.
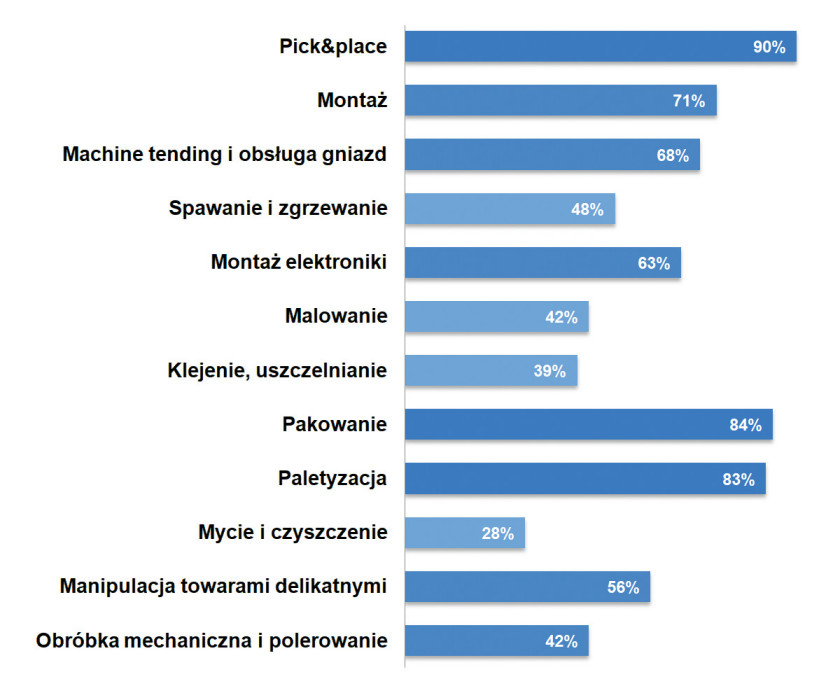
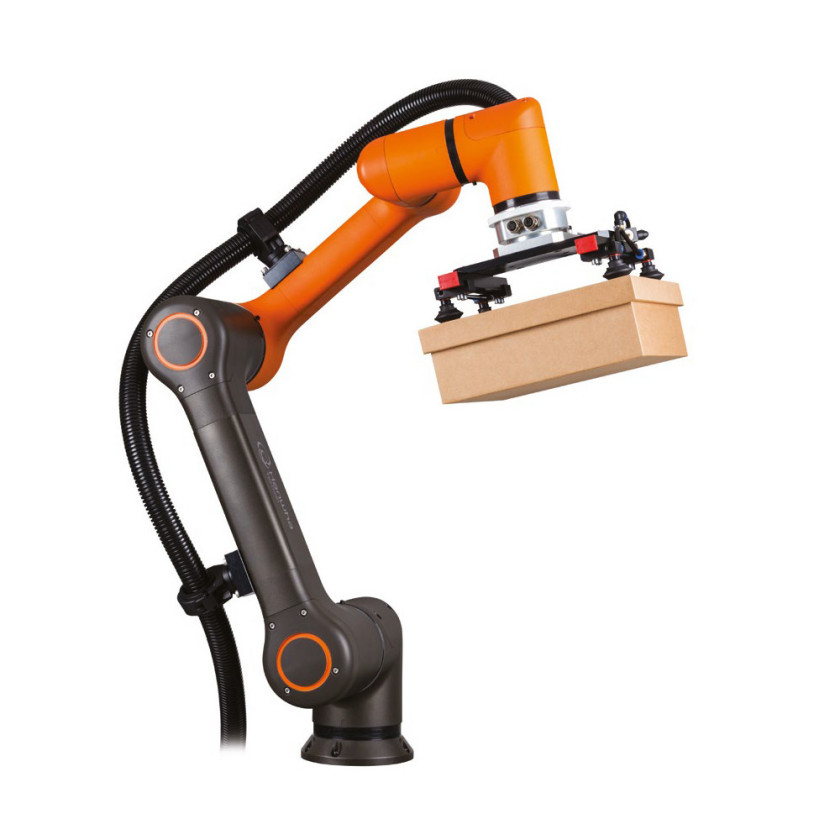
Najważniejsze powody dla których zdaniem respondentów klienci decydują się na stosowanie robotów współpracujących to: bezpieczeństwo, brak konieczności odgradzania cobotów, elastyczność aplikacyjna i łatwość programowania. Wszystkie wymienione cechy odróżniają je od tradycyjnych robotów, które w mniejszym stopniu spełniają te oczekiwania. Porównując przekazywane przez naszych respondentów argumenty przemawiającymi za cobotami obecnie do tych z 2021 roku, należy ocenić, iż nie zmieniły się one istotnie i bezpieczeństwo ogrywa wśród nich rolę najważniejszą.
Najważniejsze powody dla których zdaniem respondentów klienci decydują się na stosowanie robotów współpracujących to: bezpieczeństwo, brak konieczności odgradzania cobotów, elastyczność aplikacyjna i łatwość programowania. Wszystkie wymienione cechy odróżniają je od tradycyjnych robotów, które w mniejszym stopniu spełniają te oczekiwania. Porównując przekazywane przez naszych respondentów argumenty przemawiającymi za cobotami obecnie do tych z 2021 roku, należy ocenić, iż nie zmieniły się one istotnie i bezpieczeństwo ogrywa wśród nich rolę najważniejszą.
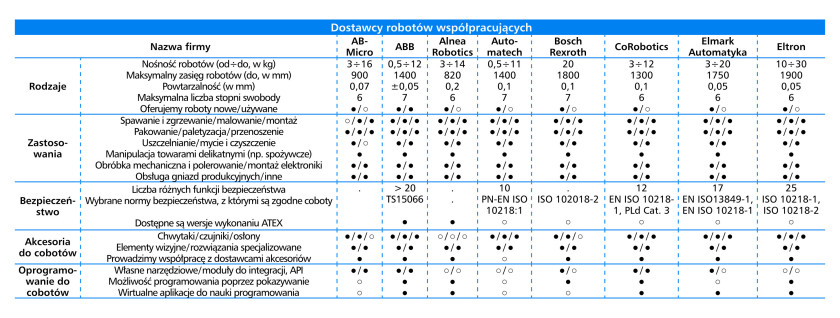
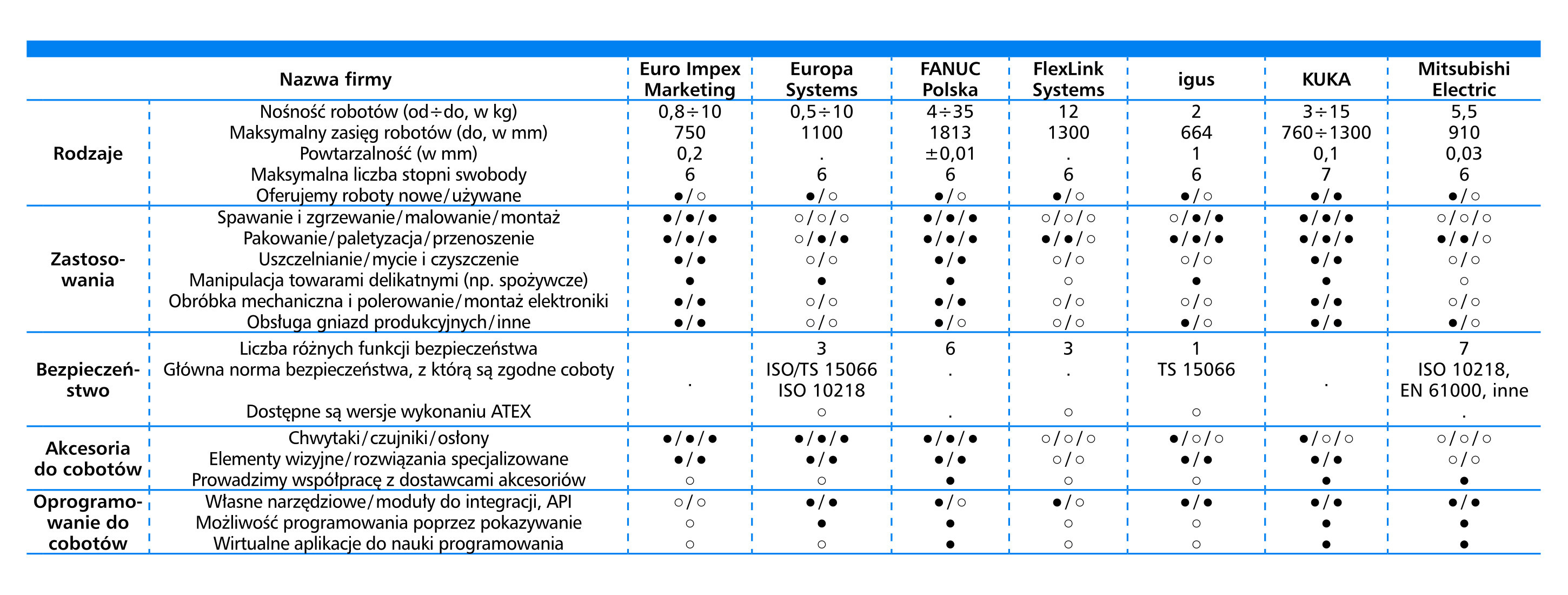
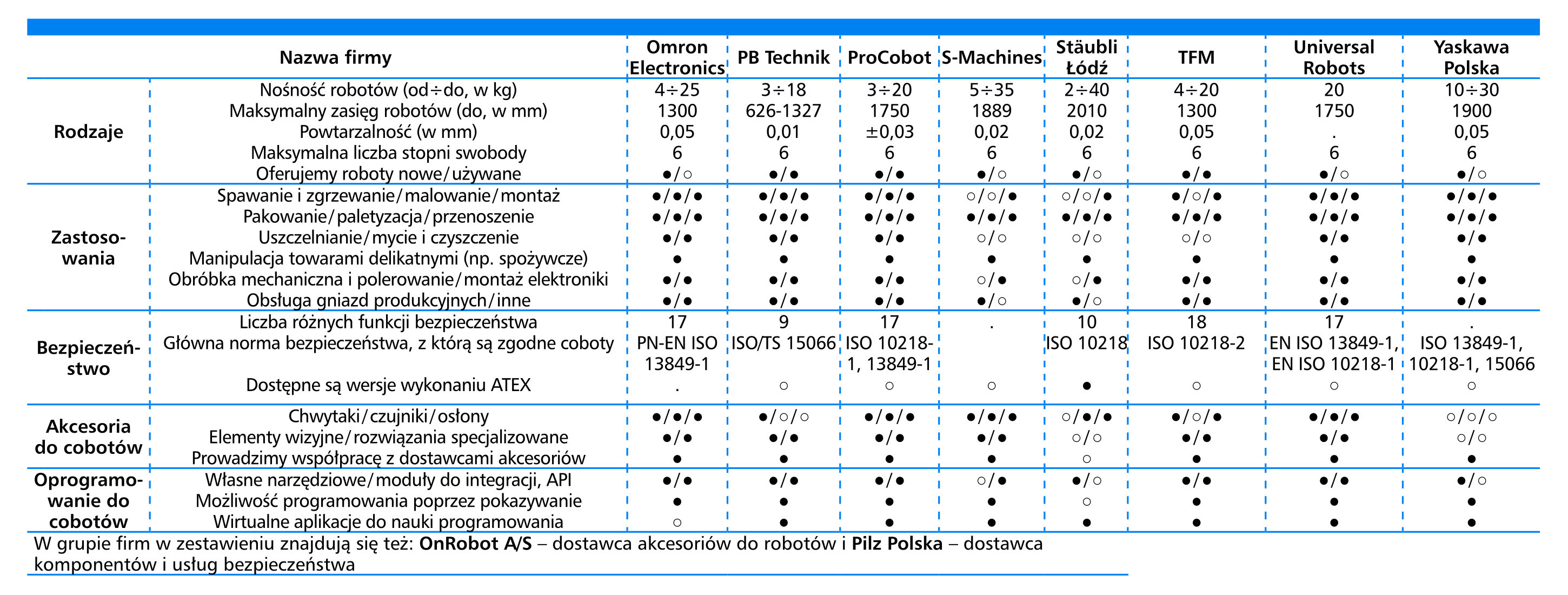
Z kolei na pytanie "w jakich aplikacjach najefektywniejsza i najczęstsza jest współpraca z ludźmi lub zamiast ludzi?" respondenci zwykle udzielali odpowiedzi: przy paletyzacji, montażu, spawaniu, pakowaniu oraz pick & place. W porównaniu do 2021 roku widzimy po raz pierwszy pojawienie się w tym zestawieniu aplikacji związanej ze spawaniem, której jeszcze dwa lata temu nie wymieniono.
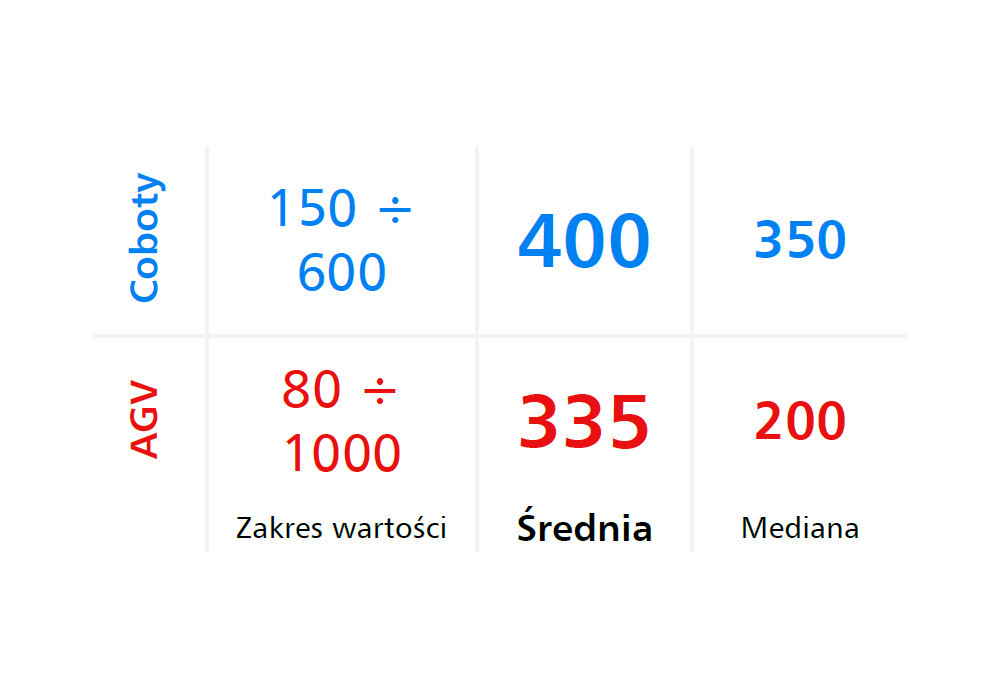
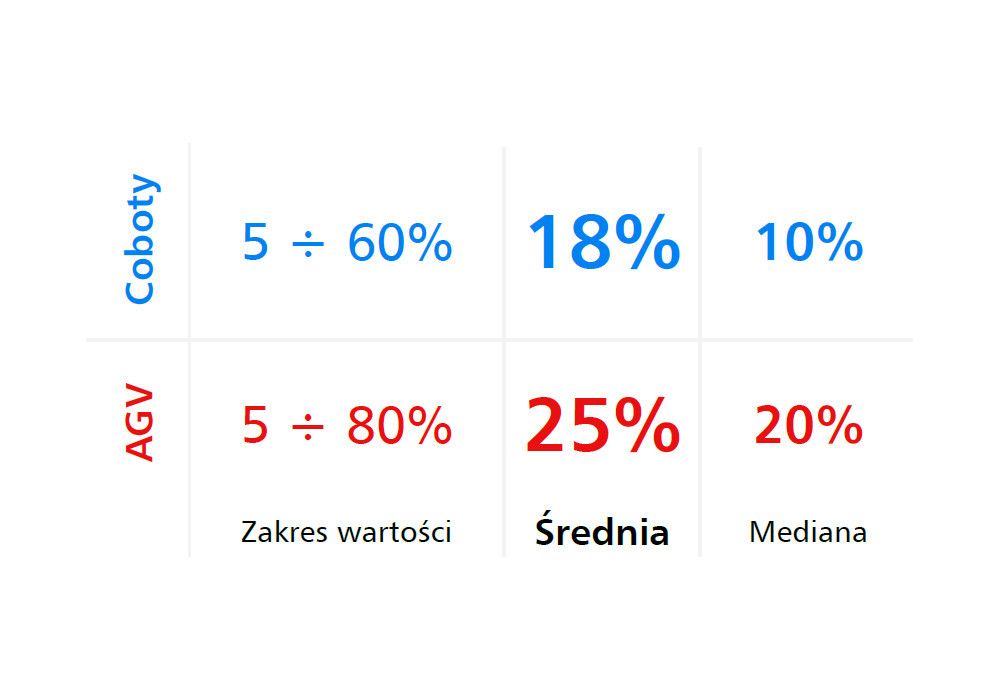
Obawy pracowników związane z cobotami
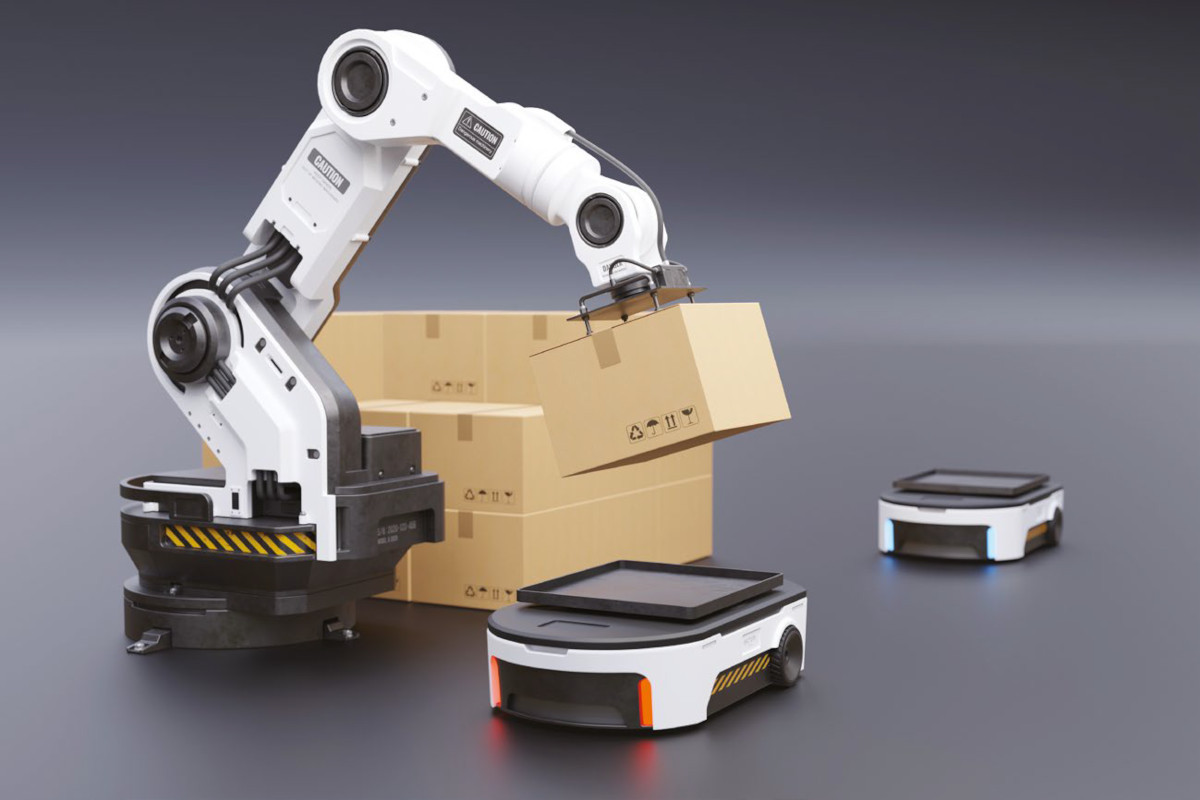
Naszych respondentów zapytaliśmy o to, jakie obawy żywią pracownicy zakładów, w których wdrażane są roboty współpracujące. Jak można było się spodziewać – najczęściej wymieniana była niepewność własnego zatrudnienia. Tego rodzaju niepokój wśród pracowników potwierdza blisko połowa zapytanych przez nas respondentów.
Chociaż roboty współpracujące słusznie mają opinię maszyn względnie bezpiecznych dla człowieka – nie tylko ze względu na liczne stosowane zabezpieczenia, ale także mniejszą masę i rozmiary w porównaniu do tradycyjnych robotów, nie wszyscy pracownicy czują się w ich pobliżu rzeczywiście bezpiecznie. Inne wątpliwości wyrażone przez naszych respondentów w imieniu pracowników zakładów produkcyjnych to: możliwa awaryjność tych maszyn, trudne serwisowanie i konfiguracja oraz obawy o posiadane przez serwis zakładowy kompetencje w zakresie ich programowania i konfiguracji.
Kamil Niemyjski
igus
Najczęstsze zastosowania to aplikacje typu pick&place, pakowanie i malowanie/lakierowanie. W połączeniu z odpowiednim chwytakiem takie roboty mogą przenosić delikatne elementy, co jest szczególnie istotne w branży spożywczej. Wypierają standardowe roboty przemysłowe w miejscach, gdzie niezbędna jest praca w interakcji z człowiekiem, co ma znaczenie w aplikacjach trudnych do pełnej automatyzacji. Coraz więcej klientów decyduje się na samodzielne programowanie robotów i samodzielną integrację z maszyną, więc istotne jest zapewnienie odpowiedniego szkolenia. O wyborze konkretnego rozwiązania decyduje w dużej mierze znajomość marki i dostępność rozwiązania na naszym rynku. W dalszej kolejności istotna jest cena i łatwość programowania/integracji oraz zapewnione wsparcie techniczne.
Użytkownicy postrzegają coboty jako rozwiązania stosunkowo proste do wdrożenia i niedrogie – szczególnie jeśli weźmiemy pod uwagę czas zwrotu z inwestycji. W związku z tym firmy, które dotychczas nie stosowały w ogóle robotów, teraz decydują się automatyzować z ich pomocą pierwsze procesy w swoich fabrykach. Rynek automatyzacji stale rozwija się, problem z pozyskaniem pracowników nadal jest aktualny, a jednocześnie próg wejścia w inwestycję nie podnosi się, a nawet obniża za sprawą nowych producentów takich jak chociażby firma igus, która wprowadziła cobota w cenie około 25 tys. zł netto. W efekcie widać coraz więcej szans na rozwój branży robotów współpracujących w Polsce.
Pandemia i wojna chwilowo wstrzymały inwestycje, które teraz ponownie są rozpatrywane przez firmy pod kątem wdrożenia. Sytuacja na polskim rynku stabilizuje się, również dzięki dużym inwestycjom zagranicznym, co uwiarygadnia bezpieczeństwo rynku. Przewiduję, że w najbliższych miesiącach będzie widać ponowny wzrost inwestycji związanych z automatyzacją procesów produkcyjnych, a co za tym idzie wzrost sprzedaży cobotów. |