CC-LINK
CC-Link został opracowany ponad dwadzieścia lat temu przez firmę Mitsubishi Electric. W sieci tego typu też wyróżnia się węzły typu master oraz slave. Te pierwsze wysyłają komunikaty do wszystkich stacji podporządkowanych jednocześnie, a potem odpytują je osobno (broadcast polling). Prędkość transmisji, w zależności od długości segmentu sieci, wynosi od 156 kb/s (maksymalnie 1,2 km) do 10 Mb/s (najwyżej 100 m). Wykorzystując wzmacniacze sygnału, największą szybkość przesyłu danych można uzyskać na odległości ponad 4 km.
Protokół CC-Link poza "zwykłą" wersją jest dostępny w wersjach: LT, Safety oraz IE. W pierwszej maksymalnie uproszczono najważniejsze aspekty działania sieci, dlatego CC-Link/LT uznaje się za odpowiednik standardu AS-i. CC-Link Safety zapewnia niezawodność transmisji odpowiednią dla aplikacji bezpieczeństwa zgodnych z IEC 61508 SIL3 i EN 954-1/ISO 13849-1 kategoria 4. W sieciach CC-Link IE (Industrial Ethernet) można natomiast uzyskać prędkość przesyłu danych rzędu gigabitów na sekundę przy maksymalnej odległości pomiędzy stacjami powyżej 500 m.
CAN/CANOPEN, DEVICENET
Specyfikacja CAN (Control Area Network) została opracowana w latach 80. zeszłego wieku przez firmę Bosch na potrzeby branży samochodowej. W związku z tym, że w oparciu na sieciach tego typu zamierzano zorganizować systemy sterowania w samochodach, musiały one spełniać określone wymagania. Najważniejsze z nich to: duża szybkość transmisji danych, odporność na zakłócenia i elastyczność w zakresie liczby węzłów sieci. Sprawiło to, że magistralą CAN zainteresował się przemysł. Wkrótce też powstała organizacja CAN in Automation, która do dzisiaj zajmuje się rozwojem oraz promocją sieci tego typu.
Według modelu OSI standard CAN wykorzystuje warstwę fizyczną oraz warstwę łącza danych. Zostały one scharakteryzowane w zbiorze norm IEC 11898. Jeżeli natomiast chodzi o warstwę aplikacji, to opracowano wiele protokołów bazujących na standardzie CAN. Przykładami są: CANopen i DeviceNet. Oba protokoły zostały opracowane w latach 90. zeszłego wieku, pierwszy przez organizację CAN in Automation, natomiast drugi przez firmę Allen-Bradley.
Jeśli chodzi o CANopen, to zdefiniowano w nim szereg profili dla konkretnych urządzeń oraz aplikacji, na przykład zespołów maszyn o określonej funkcjonalności. Ułatwiają one projektowanie, a następnie integrację urządzeń w sieci w myśl zasady plug and play. DeviceNet, którego promocją oraz rozwojem zajmuje się organizacja ODVA (Open DeviceNet Vendors Association), opiera się z kolei na protokole CIP (Common Industrial Protocol).
Wojciech PopekB&R Automatyka Przemysłowa
Z naszego punktu widzenia jako dostawcy kompletnych systemów sterowania, Ethernet POWERLINK jest pierwszym wyborem przy realizacji połączeń pomiędzy urządzeniami. Jest to deterministyczna sieć przemysłowa oparta o otwarty protokół openPOWERLINK. Takie rozwiązanie zalecamy do wszystkich nowo budowanych systemów, gdyż umożliwia najlepsze wykorzystanie właściwości urządzeń i pozwala na realizację dowolnej topologii sieci. W przypadku wyboru sieci do systemu sterowania istotną kwestią jest możliwość sprawnej diagnostyki ewentualnej awarii. Jeżeli system sterowania jest oparty na wielu typach sieci to jego diagnostyka wymaga większych nakładów, dlatego dobrą tendencją jest stosowanie jednej sieci w ramach całego systemu. Wybierając wcześniej wymieniony protokół, w ramach jednej fizycznej sieci możemy zrealizować zadania związane ze sterowaniem, obsługą protokołu systemu bezpieczeństwa oraz równolegle w asynchronicznej części protokołu przesyłać dane niezwiązane ze sterowaniem - np. obrazy wideo.
Jeśli chodzi o przyszłość technologii sieciowych, to warto zwrócić uwagę na standard OPC UA TSN. Jest to rozszerzenie protokołu OPC UA dla systemów wymagających determinizmu czasowego podczas przesyłania danych, czyli np. w sieciach przemysłowych. Standard ten ma sprostać wymaganiom stawianym przez Industrial IoT, takim jak Big Data, bezpieczeństwo, przesyłanie informacji w czasie rzeczywistym, integracja z systemami nadrzędnymi (ERP, SCADA), otwarte standardy, łatwość konfiguracji i diagnostyki. B&R jako członek OPC Foundation pracuje aktualnie nad OPC UA TSN dla systemów we/wy, co pozwoli spełnić wymagania, jakie będą stawiane w przyszłości przed systemami automatyki. |
ETHERNET POWERLINK
POWERLINK został opracowany w 2001 roku przez firmę B&R, a obecnie jego rozwojem zajmuje się organizacja Ethernet POWERLINK Standardization Group (EPSG). W zakresie kontroli dostępu do łącza jest w nim wykorzystywany mechanizm szczelin czasowych (timeslots), które są przyporządkowywane poszczególnym stacjom oraz procedura odpytywania (polling).
W sieci funkcję nadrzędną pełni węzeł typu MN (Managing Node), który koordynuje transmisję danych. Przydziela on uprawnienia do nadawania węzłom podrzędnym typu CN (Controlled Node) i synchronizuje je. W każdym cyklu transmisji wyróżnić można trzy przedziały. W pierwszym MN wysyła do wszystkich CN ramkę SoC (Start of Cycle), która synchronizuje te węzły.
Następnie zachodzi wymiana danych izochronicznych. MN wysyła kolejno w stałym porządku do poszczególnych CN zapytanie (Poll Request). Każdy z węzłów podrzędnych natychmiast na nie odpowiada, dzięki czemu unika się kolizji. Ramka odpowiedzi (Poll Response) jest dostępna również dla pozostałych CN (broadcast).
W trzeciej fazie cyklu przesyłane są dane asynchroniczne. Mogą to być duże pakiety danych o niekrytycznym znaczeniu, które są dzielone na części i transmitowane oddzielnie, w kilku cyklach. W ten sposób przesyła się na przykład dane konfiguracyjne albo ramki TCP/IP.
Aby dany węzeł mógł rozpocząć transmisję takich informacji, musi o tym poinformować wcześniej w odpowiedzi na zapytanie MN. Na tej podstawie węzeł nadrzędny tworzy listę oczekujących CN, według której dane asynchroniczne są później nadawane.
ANALIZA RYNKU SIECIOWEGO
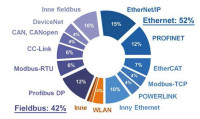
Rys. 1. Wyniki badania rynku przemysłowego pod kątem wykorzystywanych sieci komunikacyjnych (źródło: HMS Industrial Networks, 2018)
Wybór przykładowych protokołów sieci fieldbus i Ethernetu przemysłowego, jak i kolejność, w jakiej zostały one opisane, nie były przypadkowe. Zestawienie to powstało na podstawie wyników analizy globalnego rynku nowo instalowanych urządzeń sieciowych w zakładach przemysłowych, którą w 2017 roku przeprowadziła firma HMS Industrial Networks.
Wynika z niej, że segment Ethernetu przemysłowego zyskiwał na znaczeniu szybciej niż w latach ubiegłych - jego roczny wzrost zwiększył się z 20% do 22%, natomiast udział w całkowitym rynku sieci przemysłowych wyniósł 46%, w porównaniu do 38% rok wcześniej (rys. 1). W tej grupie pierwsze pozycje zajmowały: EtherNet/IP oraz Profinet, z jednakowym udziałem wynoszącym 11%.
Ten drugi cieszy się popularnością przede wszystkim w Europie Środkowej, zaś z sieci EtherNet/IP korzysta się głównie w Ameryce Północnej. Drugie miejsce globalnie zajmuje EtherCAT (7%), natomiast udział protokołów Modbus-TCP i Ethernet POWERLINK wyniósł zaledwie po 4%.
W dalszym ciągu częściej niż z Ethernetu przemysłowego korzysta się z sieci polowych. Ich udział w światowym rynku sieci przemysłowych według HMS wyniósł 48%, co oznacza spory spadek w porównaniu do wyniku sprzed roku (58%). Pierwszą pozycję w tym segmencie zajmuje protokół Profibus DP (14%). Udział sieci Modbus-RTU oraz CC-Link wyniósł po 6%, CANopen - 5%, natomiast DeviceNet tylko 4%.
W ujęciu regionalnym w Europie i na Środkowym Wschodzie wciąż najwięcej jest sieci Profibus, jednak najszybciej przybywa tych w oparciu na protokole Profinet. Na rynku amerykańskim dominują sieci oparte na protokole CIP. Warto dodać, że pod względem udziałów w tym regionie EtherNet/IP wyprzedził sieci DeviceNet. Jeśli chodzi o rynek azjatycki, to jest on bardzo rozdrobniony, przez co żaden protokół nie dominuje - szeroko używane są sieci Profibus oraz Profinet, EtherNet/IP, Modbus czy CC-Link, w tym na znaczeniu zyskuje protokół CC-Link IE, tak jak i EtherCAT.
Z analizy firmy HMS wynika również, że popularyzują się sieci bezprzewodowe (patrz: ramka). Ich roczny wzrost wyniósł 32% (rok wcześniej 30%), zaś udział zwiększył się z roku na rok z 4% do 6%. W rezultacie łączny udział sieci bezprzewodowych i Ethernetu przemysłowego przekroczył 50%.
SPECYFIKA SIECI A JEJ ZASTOSOWANIE
Chociaż mogłoby się wydawać, że wprowadzenie technologii Ethernetu do sieci przemysłowych sprawi, że granica między nimi a "zwykłymi" sieciami stopniowo zacznie się zacierać, nie ulega wątpliwości, że fundamentalnie różnią się one wymaganiami, jakie stawiają im ich zastosowania. Zasadnicza różnica polega na tym, że sieci przemysłowe połączone są z urządzeniami i systemami, których parametry oraz działanie za ich pośrednictwem monitorują i zmieniają inne urządzenia albo systemy. Dlatego oczekuje się od nich, że m.in. będą bardziej niezawodne oraz umożliwią wymianę danych w czasie rzeczywistym. W zależności od specyfiki gałęzi przemysłu albo rodzaju produkcji wymagania te mogą się nieco różnić.
Na przykład w produkcji dyskretnej wyroby na kolejnych etapach mają skończoną formę, dlatego poszczególne stanowiska są w zasadzie autonomiczne i wymagają przeważnie łączności tylko na wyższym poziomie, na przykład z głównym system zarządzania zakładem. Z kolei w produkcji procesowej poszczególne fazy produkcji zazębiają się oraz charakteryzuje je duża dynamika, w związku z czym konieczna jest niezawodna komunikacja w czasie rzeczywistym na najniższym poziomie. W automatyce budynkowej różnorodność struktur budynków znajduje odzwierciedlenie w różnorodności topologii sieciowych. Specyficzne dla instalacji dystrybucji mediów użytkowych są natomiast duże odległości. Podobne wymagania dotyczą sieci w systemach transportowych, na przykład w sterowaniu ruchem pociągów. W tym przypadku dochodzą też kwestie bezpieczeństwa. Jeśli z kolei chodzi o komunikację w obrębie maszyn albo pojazdów, to ponieważ sieci są skupione na bardzo małym obszarze, są narażone na trudne warunki pracy (wysokie temperatury, zaburzenia elektromagnetyczne), zaś od ich niezawodności zależy bezpieczeństwo korzystających z danego sprzętu.
W ramce szerzej przedstawiamy wymagania wspólne dla większości sieci przemysłowych. Wyjaśniamy również, w jakich aspektach różnią się one od tych stawianych "zwykłym" sieciom.
Bartłomiej BeszTurck
Sieci polowe od ponad 20 lat stanowią podstawę rozwiązań w automatyce przemysłowej. Urządzenia dla Profibus-DP, DeviceNet, CANopen czy Modbus-RTU stanowią podstawę wielu wdrożeń i z powodzeniem zrealizowanych aplikacji. Nie istnieje zatem realne zagrożenie, by sieci te z dnia na dzień straciły na znaczeniu. Ze względu na swego rodzaju hermetyczność rozwój klasycznych rozwiązań nie jest już jednak tak dynamiczny. Przemysł 4.0, IoT - koncepcja gromadzenia, przetwarzania i wymiany danych poprzez sieć, infrastruktury chmurowe wymagają znacznie szerszego dostępu do informacji. Takie możliwości daje standard Ethernet. Na jego bazie rozwinęły się takie protokoły jak Profinet-IO, Ethernet/IP czy Modbus-TCP. Dzięki poprawie parametrów oraz unifikacji topologii sieci, jakie niesie za sobą jego stosowanie, Ethernet stał się dominującą technologią. Obecnie coraz trudniej znaleźć na rynku urządzenia niemające funkcji wspierających ten standard. Ułatwia to scalanie systemów pracujących w różnych miejscach zakładów przemysłowych. Producenci widzą potencjał, jaki drzemie w integracji urządzeń na bazie Ethernetu dlatego obszar możliwych zastosowań rozwiązań polowych przesuwa się w kierunku aplikacji specjalistycznych, a Ethernet jawi się jako podstawowy sposób komunikacji w automatyce. Niemniej jednak nie upatrywałbym dominacji tylko jednego z wymienionych standardów. Wręcz przeciwnie, wydaje się pewne, że protokoły na bazie Ethernetu oraz rozwiązania polowe będą ze sobą koegzystowały. |
FIELDBUS VS. ETHERNET
Zarówno sieci fieldbus, jak i Ethernetu przemysłowego spełniają podstawowe wymagania stawiane sieciom w przemyśle. Dlatego w praktyce to ich specyficzne cechy decydują o tym, który typ sieci lepiej sprawdzi się w danym zastosowaniu.
Jeżeli chodzi o Ethernet, to do jego głównych zalet zalicza się dużą prędkość transmisji oraz, w razie zastosowania światłowodów, możliwość budowy rozległych sieci, co ułatwia organizację rozproszonych systemów sterowania. Użycie światłowodów pozwala również ograniczyć zakłócenia transmisji występujące w sieciach z okablowaniem miedzianym powodowane zaburzeniami elektromagnetycznymi emitowanymi przez maszyny.
Pierwsza z wymienionych zalet Ethernetu może się jednak w pewnych zastosowaniach okazać zbędna - duża prędkość transmisji nie jest na przykład wymagana w systemach regulacji wolno zmieniających się wielkości. Jeżeli weźmiemy pod uwagę zadanie przestawiania zaworów w celu zmiany temperatury cieczy w zbiorniku, to ilość jednorazowo przesyłanych danych jest rzędu tylko pojedynczych bajtów, natomiast ustawienia zaworów aktualizowane są z częstością rzędu sekund, dziesiątek sekund, a nawet minut w przypadku dużych zbiorników. Możliwość uzyskania czasów transmisji rzędu milisekund w tym wypadku pozostawałaby zatem całkowicie niewykorzystana.
Z drugiej strony prędkości transmisji rzędu Mb/s, które są osiągalne w sieciach fieldbus, nie są z pewnością wystarczające do przyszłych potrzeb. Wraz z rozwojem Przemysłowego Internetu Rzeczy (Industrial Internet of Things) i innych technologii, w których postępu możemy się spodziewać w erze Przemysłu 4.0, istnieją uzasadnione obawy, że nawet Ethernet o prędkości transmisji 1 Gb/s nie podoła ilości danych, które będą przesyłane w sieciach przemysłowych.
Popularność Ethernetu w LAN sprawia także, że niezbędny sprzęt sieciowy jest powszechnie dostępny. Ponadto na jego produkcję nie ma monopolu żaden konkretny producent, a urządzenia różnych marek są kompatybilne. Dzięki temu rozbudowa instalacji, integracja z innymi sieciami w przedsiębiorstwie i podłączenie do Internetu oraz wymiana uszkodzonych lub awaryjnych urządzeń są łatwe.
Konkurencja między dostawcami sprawia również, że urządzenia sieciowe są stosunkowo tanie. Powszechna jest też wiedza na temat Ethernetu, dzięki czemu nie brak kadry wyszkolonej w zakresie instalacji i konserwacji takich sieci. Wszystkie wyżej wymienione cechy Ethernetu sprawiają, że wdrożenie sieci na nim opartej może się okazać tańsze niż sieci fieldbus.
Każda dyskusja, która ma na celu wyłonienie zwycięskiej technologii w konfrontacji sieci fieldbus z Ethernetem przemysłowym, dotyka w końcu kwestii bezpieczeństwa. Ten aspekt przedstawiamy szerzej w ramce.
Monika Jaworowska