- Gdzie są wykorzystywane klimatyzatory do szaf przemysłowych? Skąd potrzeba ich produkcji oraz generalnie rozwoju tego obszaru biznesu w firmie Rittal?
Thomas Steffen: Odpowiedź na to pytanie należy rozpocząć od omówienia rozwoju oferty samych obudów i szaf elektrycznych. Jeżeli spojrzymy na rynek pół wieku wstecz, to produkty takie praktycznie nie istniały jako wyroby dostępne z katalogu. Dawniej szafy wykonywano dopiero po zaprojektowaniu lub wykonaniu urządzenia, a one same stanowiły kłopotliwy i jednocześnie kosztowny element procesu produkcyjnego.
Okazało się, że kolejność wytwarzania można zmienić dzięki standaryzacji i wprowadzeniu systemów obudów. Sądzę, że Rittal, tworząc ofertę wyrobów o różnych wielkościach i przeznaczeniu, zapoczątkował zmianę w całej branży maszynowej i związanej z prefabrykacją szaf elektrycznych.
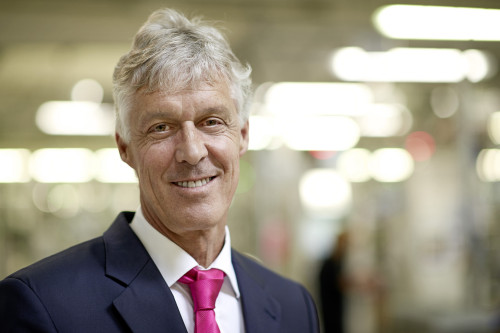
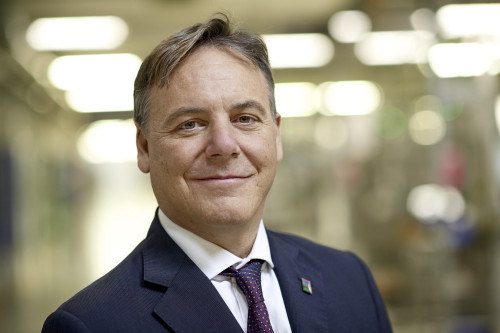
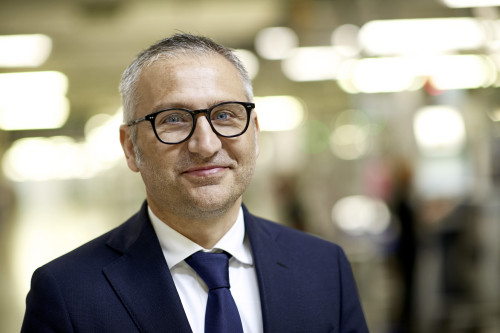
W latach 80. zeszłego wieku zaczęliśmy rozszerzać nasz obszar działalności w kierunku urządzeń do wentylacji i klimatyzacji. Powody były czysto pragmatyczne - w szafach montowanych było coraz więcej urządzeń elektrycznych oraz elektronicznych, co w efekcie skutkowało wzrostem średnich temperatur w nich panujących. Dotyczyło to zarówno automatyki, energetyki, jak też w coraz większym stopniu aplikacji IT. Te ostatnie stanowią dzisiaj - obok przemysłu - główny z obszarów naszego zainteresowania rynkowego.
Jeżeli chodzi o przemysł, są to klimatyzatory wykorzystywane w bardzo wielu jego obszarach - praktycznie wszędzie tam, gdzie szafy wymagają chłodzenia ze względu na zainstalowane w nich urządzenia i muszą pracować w obszarach o podwyższonych temperaturach otoczenia. Przykładowo nasze klimatyzatory można znaleźć na wyposażeniu hut metali czy fabryk Fiata, gdzie w jednym z zakładów zastosowanych jest ponad 400 takich jednostek.
Z kolei BMW korzysta w 85% wszystkich aplikacji z urządzeń marki Rittal. Zastosowania klimatyzatorów mogą być też mniej typowe - przykładem jest ta w Bibliotece Watykańskiej, gdzie systemy Data Center są chłodzone z wykorzystaniem naszych urządzeń.
- Spotykamy się w zakładzie produkcyjnym w Valeggio sul Mincio (północne Włochy). Jaka jest jego rola w globalnej strukturze firmy oraz skala tutejszej produkcji?
Nicola Salandini: Zakład jest najważniejszą w grupie jednostką produkcyjną w zakresie klimatyzatorów, wymienników ciepła i chłodziarek termoelektrycznych. Powstaje tu rocznie 120 tys. urządzeń, całość produkcji odbywa się na około 9 tys. m2. Montażem urządzeń zajmuje się obecnie 220 pracowników, zaś sam zakład przeszedł w ostatnich latach modernizację i rozbudowę. Planowane są też kolejne zmiany, jako że w fabryce skoncentrowana będzie cała produkcji klimatyzatorów w obrębie europejskich struktur Rittala.
Można zapytać, dlaczego akurat Valeggio i Włochy, a nie np. Niemcy czy inny kraj. Region Wenecji Euganejskiej, który znajduje się w północno-wschodnich Włoszech, ma wieloletnie tradycje w zakresie produkcji urządzeń klimatyzacyjnych i chłodniczych. Znajduje się tutaj ponad 150 przedsiębiorstw działającej w branży, których sumaryczne możliwości produkcyjne stanowią 60% tych dotyczących całej Europy. Również działalność naukowa - przykładowo na uniwersytecie w Padwie - jest silnie skoncentrowana wokół technologii chłodzenia.
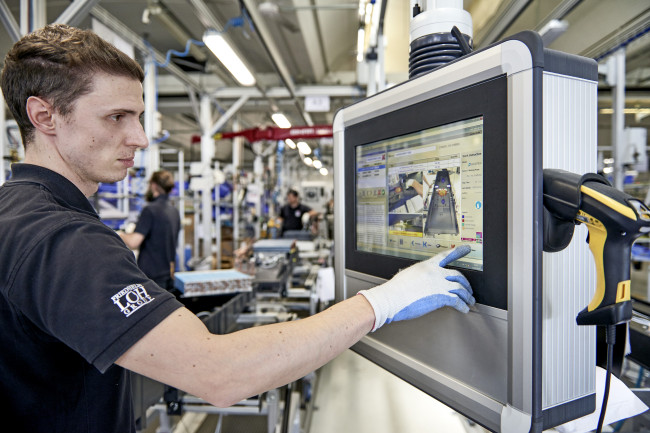
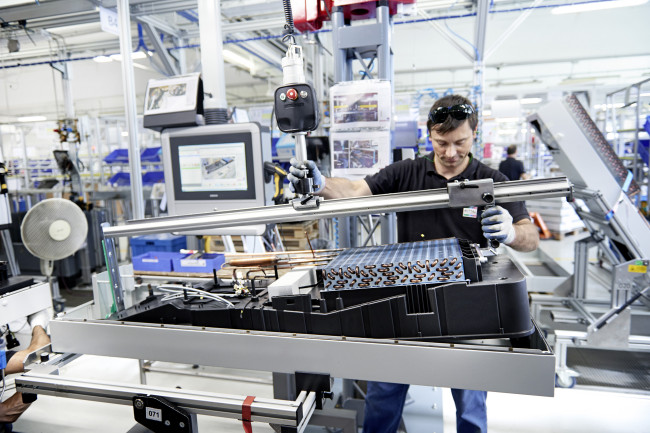
TS: Początki produkcji klimatyzatorów w Valeggio sięgają 1988 roku, przy czym zakład ten należał wtedy do włoskiej firmy Kelvin. Została ona przejęta przez Rittala w 2000 roku i od tego czasu powstawały tu kolejne generacje produktów, głównie marki TopTherm.
Przez półtorej dekady przeszliśmy dwie rewizje tych ostatnich, które obejmowały wprowadzenie powłoki RiNano oraz, w 2011 roku, zwiększenie efektywności energetycznej urządzeń. Bazując na tych doświadczeniach, w 2013 roku rozpoczęliśmy prace nad nową generacją urządzeń, czego efektem było wprowadzenie na rynek urządzeń Blue e+ pod koniec zeszłego roku.
- Jaka była motywacja do ich opracowania?
Marco Villa: U podstaw znalazła się potrzeba zwiększania efektywności energetycznej, co jest tematem ważnym nie tylko globalnie, ale też coraz częściej pojawiającym się w kontekście przemysłu. Oceniamy, że w Europie zainstalowanych jest około dwóch milionów klimatyzatorów przemysłowych o sumarycznej mocy 2 GW.
Nowa generacja naszych urządzeń zapewnia kilkudziesięcioprocentowe oszczędności energii i, w teorii, wymiana wszystkich obecnie stosowanych na Blue e+, pozwoliłaby na zmniejszenie kosztów chłodzenia na poziomie ponad 500 mln euro miesięcznie. Pod względem redukcji energii jest to ekwiwalent około 900 turbin wiatrowych czy też 1,5 tradycyjnej elektrowni węglowej. Warto też wspomnieć o zmniejszeniu obciążenia środowiska naturalnego - w tym przypadku wielkość redukcji szacujemy na tonę metryczną CO2 rocznie.
Wymogi w zakresie oszczędności energii to nie wszystko. Tworząc nową generację urządzeń rozmawialiśmy z różnymi grupami naszych klientów, pytając ich o to, czego rzeczywiście potrzebują. Producenci maszyn stwierdzili, że kluczowe jest dla nich uniwersalne zasilanie urządzeń, tj. dowolnym napięciem, co zapewni im możliwość ich globalnego stosowania oraz łatwa parametryzację.
Prefabrykatorzy szaf mieli analogiczne wymogi, podkreślali również potrzebę łatwości montażu. Z kolei dla klientów końcowych liczyła się przede wszystkim efektywność energetyczna oraz możliwości związane z oszczędnościami w całym procesie życia produktu. To ostatnie obejmuje m.in. łatwość serwisowania oraz utrzymania ruchu - czyli np. szybką diagnostykę.
- Jakie są cechy i parametry nowych klimatyzatorów?
TS: Kluczową cechą Blue e+ jest wykonanie tych urządzeń w technologii hybrydowej, gdzie połączyliśmy klasyczny klimatyzator z systemem chłodzenia pasywnego. W tym ostatnim korzystamy z "heat pipe", czyli ciepłowodu, zaś ciepło rozpraszane jest z wykorzystaniem wentylatorów. Taki połączony system zapewnia znaczne ograniczenie średniego czasu działania sprężarki, przez co jest znacznie wydajniejszy energetycznie niż te bazujące tylko na klimatyzatorach.
Większość pozostałych cech klimatyzatorów wynika wprost ze zdefiniowanych wcześniej wymogów. Blue e+ mają możliwość zasilania wielonapięciowego, dzięki czemu producenci i prefabrykatorzy szaf z nich korzystający mogą oferować takie same wyroby niezależnie od aplikacji ich produktów. Jest to znacząca zmiana również dla klientów końcowych, bowiem nie jest już konieczne używanie różnych wersji w różnych częściach świata.
Ważnymi cechami urządzeń są też ich możliwości komunikacyjne. Klimatyzatory zostały wyposażone m.in. w interfejsy NFC, co pozwala obsłudze na ich szybką konfigurację z wykorzystaniem tabletów czy smartfonów. Do tego dochodzi łatwiejsza kontrola i utrzymanie systemów oraz możliwość zaoferowania klientom zupełnie nowego modelu serwisowego.
- Jakie są efekty wykorzystania technologii hybrydowej?
TS: W dużej części aplikacji przemysłowych temperatury wynoszą od kilkunastu do około 30°C - w takich warunkach zwykle wystarczające jest wykorzystanie pasywnego obiegu ciepła i korzystanie z wentylatorów. Znacząco zmniejsza to zużycie energii - w naszych testach laboratoryjnych okazało się ono średnio cztero-, pięciokrotnie niższe niż dla urządzeń standardowych. Przeprowadzone testy były ekstensywne - m.in. ze względu na fakt, że nowe urządzenia zawierają znacznie więcej elektroniki niż ich poprzednie generacje.
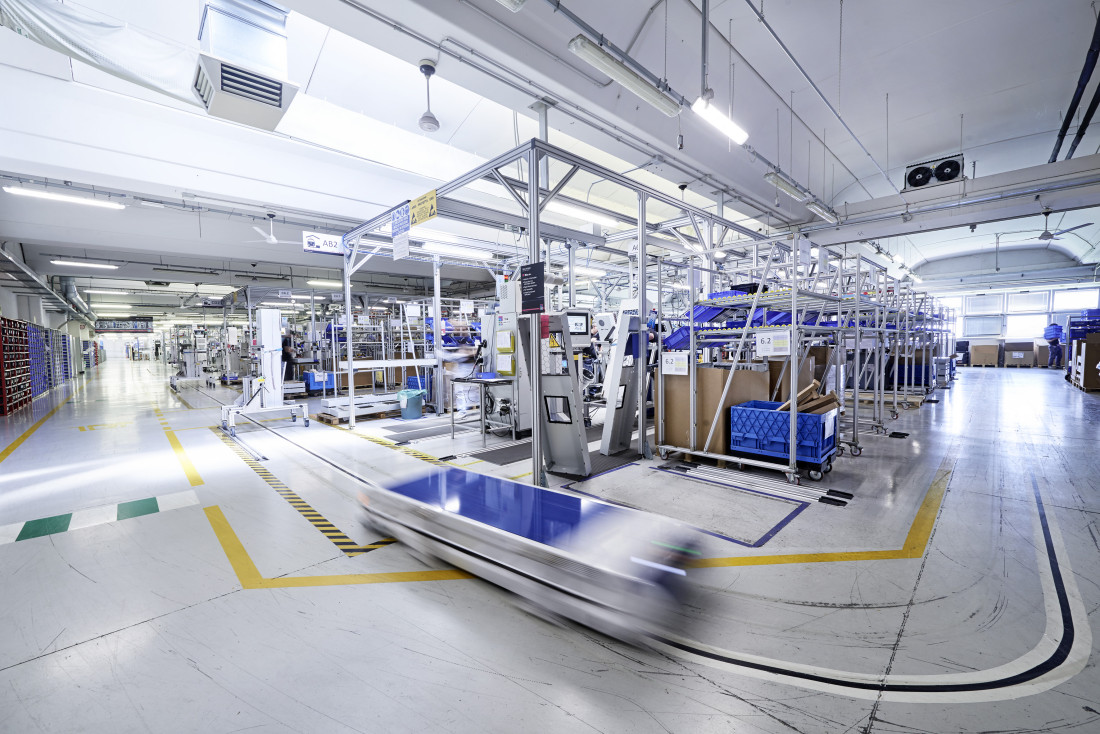
Oczywiście kluczowe było pozyskanie wyników z "realnego świata", stąd też poprosiliśmy naszych klientów o sprawdzenie działania klimatyzatorów w ich zakładach. Wyniki zaskoczyły nas samych! Firma Bihler uzyskała oszczędności w stosunku do standardowego chłodzenia na poziomie 89% - tj. zużywała około 1/10 energii w porównaniu do tej wykorzystywanej pierwotnie. W przypadku Audi oszczędności były na poziomie 77%, zaś Daimler zmniejszył użycie energii aż o 91%!
Średnia dla wszystkich testów, a te przeprowadzane były również m.in. w zakładach produkcyjnych Renault, Volkswagena, Smurfit Kappa czy Volvo, wyniosła 80%. Dodatkowo wraz ze zmniejszeniem zużycia energii uzyskano zmniejszenie histerezy - dawniej wynosiła ona 5°C, obecnie temperatura jest prawie stała. Jest to ważne pod kątem czasu życia komponentów i urządzeń.
- Jak przekonujecie klientów do inwestycji w nowe urządzenia? Czy sam aspekt energooszczędności jest wystarczający?
MV: Naszym celem, zresztą nie tylko w przypadku Blue e+, ale też innych urządzeń, jest zaoferowanie odbiorcom produktów z wartością dodaną. Tę ostatnią stanowią usługi posprzedażowe i serwis, możliwość dostarczenia produktów globalnie z zapewnieniem tej samej jakości oraz zaoferowanie wyliczeń w zakresie potencjalnych oszczędności energii. Nie myślimy dzisiaj o produktach oddzielnie, ale interesuje nas kompletna oferta, a więc szafy, obudowy, klimatyzatory, systemy rozdziału energii i inne, które składają się na standaryzowany i jakościowy system. Do tego dochodzi oprogramowanie i wspomniane usługi.
TS: Inwestycja w rozwiązania energooszczędne zawsze wymaga przekonywania klientów do patrzenia na TCO, czyli całkowite koszty posiadania. Wielu naszych odbiorców - a takimi są przykładowo producenci maszyn - nie jest w praktyce użytkownikami klimatyzatorów i innych wyrobów, i to nie oni płacą rachunki za energię elektryczną.
Stąd też musimy informować i przekonywać klientów końcowych - i jest to zadanie dla naszych inżynierów sprzedaży. Sądzę, że na tym polu odnosimy sukcesy, szybko rośnie też świadomość przedstawicieli firm przemysłowych odnośnie do możliwości oszczędzania. Tak jest szczególnie w sektorze motoryzacyjnym, gdzie zespoły w zakładach produkcyjnych mają wyznaczane bardzo konkretne cele w zakresie redukowania zużycia energii elektrycznej.
W przekonywaniu klientów pomaga nam również oprogramowanie, dzięki któremu możemy łatwo symulować zmiany i wyliczać potencjalne oszczędności wynikające z wdrożenia nowych urządzeń. Dodam, że koszty zakupu obecnych klimatyzatorów są jedynie o około 10% większe niż tych poprzednio oferowanych, zaś średni czas zwrotu z inwestycji wynosi kilka miesięcy.
Jaka jest skala działalności firmy Rittal? Jak wygląda struktura grupy Friedheim Loh?
W Grupie jest też LKH - producent wyrobów z tworzyw sztucznych, a także będąca dostawcą blachy firma Stahlo. Ta ostatnia jest o tyle istotna, że Rittal jest największym w Niemczech (po firmach z branży motoryzacyjnej) odbiorcą blachy płaskiej. Tej ostatniej zużywamy około 400 ton… dziennie! Firma ma globalnie 78 oddziałów zależnych, zaś jej obroty w 2015 roku wyniosły 2,2 mld euro. Rittal został założony w Rittershausen, gdzie również znajduje się nasz główny zakład produkcyjny, w którym wytwarzane są systemy obudów TS 8. Drugą historycznie z fabryk jest ta założona w Herborn, gdzie z kolei mieści się też obecnie centrala firmy. Przez wiele lat rozwój Rittala następował regionalnie, przez co w promieniu 30 km od Herborn zlokalizowanych jest sześć zakładów produkcyjnych firmy. Planujemy tutaj pewne zmiany związane z konsolidacją i otwarcie nowej "superfabryki" w Haiger (na zdjęciu). W tej ostatniej w wysoce zautomatyzowanych procesach wytwarzanych będzie około 9 tys. obudów dziennie. Zmiany dotkną również zakładu w Valeggio, do którego przeniesiona zostanie cała produkcja klimatyzatorów z innych jednostek w Europie. Jeżeli zaś chodzi o inne zakłady poza Europą, to do tych większych należą m.in. te w Ohio w USA, gdzie pracuje 600 osób, w indyjskim Bangalore oraz w Szanghaju. Sumarycznie mamy 11 zakładów produkcyjnych. |
- Jak wyglądają procesy produkcyjne nowych urządzeń?
NS: Wytwarzanie urządzeń Blue e+ odbywa się inaczej niż w przypadku poprzednich modeli klimatyzatorów. Modyfikacje w procesach produkcyjnych zaczęliśmy wprowadzać w 2012 roku, wdrażając produkcję typu lean oraz przechodząc na nowy model organizacji zadań pracowników. O ile dawniej wytwarzane były każdorazowo partie produkcyjne, o tyle teraz stosujemy metodologię "one piece flow", czyli produkcji pojedynczych urządzeń jedno po drugim.
W 2015 roku, wraz z rozpoczęciem wytwarzania Blue e+, wdrożyliśmy też cyfrowy system "prowadzenia" operatorów na stanowiskach produkcyjnych. W żadnym z miejsc nie korzystamy ze zleceń papierowych, zaś wszystkie informacje niezbędne do montażu urządzeń są wyświetlane na ekranach operatorów - zawsze w zakresie odpowiednim dla wytwarzanej w danym momencie wersji.
Powyższe modyfikacje były o tyle istotne, że produkujemy dzisiaj zarówno urządzenia katalogowe, jak też personalizowane na zamówienie klientów. Tych ostatnich jest zresztą coraz więcej, stąd też zasadna była rezygnacja z produkcji dużych partii standardowych produktów.
Podczas reorganizacji wdrożyliśmy wykorzystanie wózków oraz robotów AGV przenoszących klimatyzatory pomiędzy stanowiskami produkcyjnymi i testującymi. Zapewniają nam one pełną elastyczność wytwarzania. Warto tu zaznaczyć, że niezależnie od modelu w każdym z przypadków produkty przechodzą pełny proces testów funkcjonalnych.
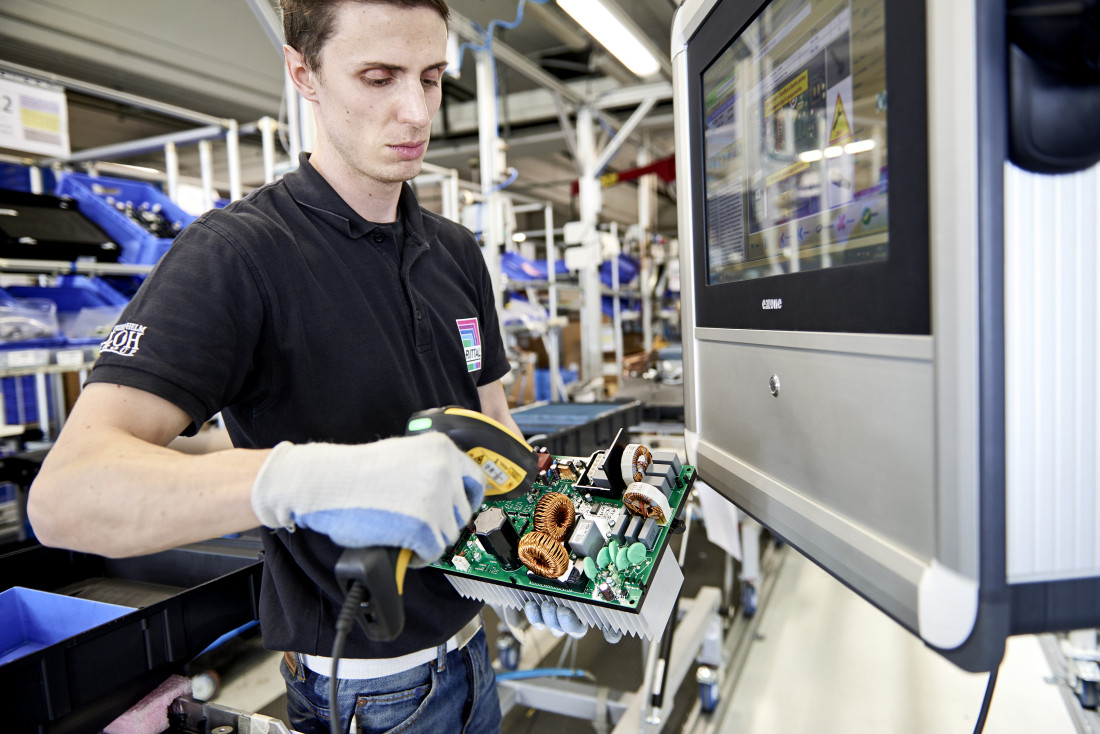
Wprowadzone zmiany zapewniły nam niespodziewany wzrost produktywności, który wyniósł ponad 30%. Drugą z korzyści było zwiększenie jakości. Dzięki temu, że pracownicy każdorazowo skanują kod znajdujący się na instalowanym komponencie, możliwa jest nie tylko pełna ich weryfikacja, ale też możliwość śledzenia genealogii gotowych produktów.
Możemy dla każdego z produktów końcowych uzyskać informacje o wykorzystanych podzespołach i ich historii. Dbamy też o ciągłe doskonalenie - codziennie organizujemy spotkania w hali produkcyjnej, gdzie operatorzy i inni pracownicy wspólnie z kierownikami rozwiązują problemy i wprowadzają usprawnienia.
W przyszłości planowane są dalsze kroki rozwojowe. Do takich należy wprowadzenie systemu RFID, które umożliwi w pełni automatyczne pobieranie elementów na stacjach montażowych. Myślimy również o zastosowaniu rozwiązań logistycznych pick-by-light oraz robotów współpracujących, co nastąpi prawdopodobnie w przyszłym roku.
- Jak wyglądały ostatnie lata w Rittalu w kontekście ewolucji idei Przemysłu 4.0?
TS: Nasza przygoda z Przemysłem 4.0 rozpoczęła się jeszcze zanim inicjatywa ta została sformalizowana przez niemiecki rząd. W 2010 roku rozpoczęliśmy duży projekt mający na celu określenie przyszłych wymogów klientów, przy czym nasze myślenie skupione było głównie wokół kwestii wielowariantowości wyrobów oraz dostarczania odbiorcom spersonalizowanych szaf i obudów. Była to zresztą reakcja na potrzeby klientów, którzy coraz częściej potrzebowali modyfikacji wersji standardowych.
Naszym pomysłem było stworzenie systemu z konfiguratorem, z którego mogliby korzystać zarówno odbiorcy, jak też my sami. Miał on pozwolić wybierać różne warianty produktów i łączyć je ze sobą, udostępniając automatycznie pozostałe dane. Ponieważ w portfolio mamy kilka tysięcy wyrobów, sporym wyzwaniem było określenie wszystkich - a przynajmniej większości - możliwych scenariuszy ich użycia.
Stąd też wybierając najpotrzebniejsze warianty, bazowaliśmy na historii zamówień klientów. Następnie dodaliśmy odpowiednie procesy logistyczne i zarządzanie zamówieniami, tak aby zapewnić możliwość ich realizacji w krótkim czasie i za konkurencyjną cenę.
- Jakie inne działania zgodne z Przemysłem 4.0 podjęliście?
TS: Przemysł 4.0 to zagadnienie tematycznie bardzo szerokie i obejmuje cyfrową inżynierię, integrację pionową systemów produkcyjnych, tj. od poziomu czujników do systemów ERP, a także integrację horyzontalną. Szczególnie interesowało nas pierwsze z zagadnień, u podstaw którego znalazł się nasz konfigurator wariantów. Postanowiliśmy go połączyć z oprogramowaniem EPLAN, tak aby projektanci mogli łatwo wybrać potrzebne produkty, następnie przesłać te dane do środowiska EPLAN i stworzyć w nim nie tylko kompletne zestawienie komponentów, ale też prototyp szafy czy urządzenia.
Pełna integracja konfiguratora oraz oprogramowania EPLAN wymagała zresztą zapewnienia przez nas znacznie większych ilości danych niż te posiadane w konfiguratorze. Musieliśmy m.in. stworzyć modele 3D wszystkich komponentów. Procesy te zajęły ponad dwa lata, ale dzięki nim możemy dzisiaj oferować producentom maszyn i prefabrykatorom systemów kompletne narzędzie do projektowania oraz wirtualnego prototypowania systemów.
- Czy akwizycja firmy Kiesling i rozszerzanie oferty Rittala o maszyny do produkcji stanowią kolejne kroki tego procesu?
TS: Tak - i to niejedyne. Jednym z ważnych obszarów jest dla nas rozwój oprogramowania. Przykładem jest Rittal Therm, czyli narzędzie służące do określania wymogów dotyczących klimatyzacji i wspomagające wdrożenia w tym zakresie. Rok temu wraz z firmą Phoenix Contact zaprezentowaliśmy również koncepcję Thermal Design Integration, która obejmuje rozszerzenie możliwości wirtualnego planowania 3D w EPLAN Pro Panel o zagadnienia związane z zarządzaniem ciepłem.
Rozwijamy ponadto narzędzia bazujące na technologii chmurowej, takie jak AXOOM. Służy ono do zdalnego monitorowania pracy klimatyzatorów i innych urządzeń u klientów, zapewniając możliwość wdrażania metodologii prewencyjnego utrzymania ruchu.
Jeżeli chodzi o firmę Kiesling Maschinentechnik, to jej akwizycja i zaoferowanie przez nas maszyn produkcyjnych były kolejnymi krokami w procesie tworzenia kompletnego łańcucha wartości dla naszych klientów. Mając już konfigurator produktów, ich modele 3D oraz system projektowy, mogliśmy pomyśleć o pełnej personalizacji obudów przez samych odbiorców.
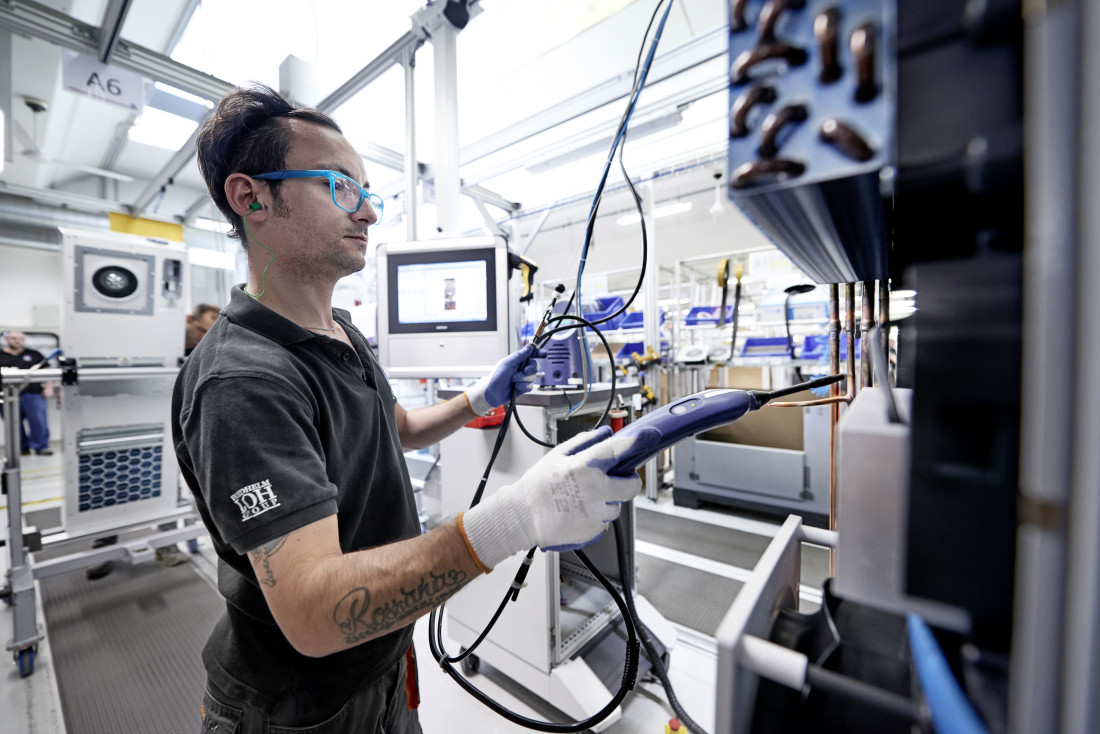
Kiesling to jeden z dwóch głównych producentów specjalistycznych maszyn obróbczych, z którym wcześniej od lat współpracowaliśmy, firma rozwijała też innowacyjne roboty do automatycznego kablowania rozdzielnic. Stąd też w 2013 roku podjęta została decyzja o zakupie przedsiębiorstwa i włączenia jej produktów do naszego portfolio.
Dzięki tym zmianom możemy dostarczać klientom m.in. wycinarki laserowe umożliwiające wycinanie trójwymiarowe, automaty do frezowania i wiercenia, a także wspomniane roboty. Sądzę, że coraz więcej przedsiębiorstw będzie w przyszłości zainteresowanych rozbudową o nie własnego parku maszynowego.
Chociaż w maszyny do modyfikacji mechanicznej szaf i obudów inwestują najczęściej firmy duże, chcemy je udostępniać również podmiotom działającym w mniejszej skali. Stąd też wprowadziliśmy m.in. możliwość pobierania plików DXF i bezpośredniego programowania maszyn obróbczych bez wykorzystywania EPLAN Pro Panel. Takie rozwiązanie nie wymaga tworzenia wirtualnego prototypu przez inżyniera elektryka i jest ukłonem szczególnie w stronę mniejszych firm.
- Czy z omawianych urządzeń będziecie również korzystali w nowo budowanym zakładzie produkcyjnym w Haiger?
TS: Zdecydowanie! W omawianej fabryce, która rozpocznie działalność w 2018 roku, planujemy ekstensywnie korzystać z maszyn z oferty Rittal Automation Systems. Dodatkowo wszystkie znajdujące się w nim instalacje produkcyjne - w działach obróbki blach, lakierowania i montażu - zostaną kompleksowo połączone w cyfrową infrastrukturę, w obrębie której funkcjonowały będą też systemy automatycznego transportu samodzielnie dostarczające komponenty.
W nowym zakładzie każdy zamówiony przez klienta produkt będzie można efektywnie wyprodukować w dowolnej liczbie egzemplarzy, bazując na około 300 podstawowych typach obudów.
Jeżeli zaś chodzi o dzisiejszą ofertę dla klientów, to mamy, podsumowując, kompletny łańcuch wartości i jasny przekaz: jeżeli jesteście zainteresowani Przemysłem 4.0 - zapewniamy komplet nowoczesnych produktów i narzędzi. Możecie zacząć od systemu EPLAN i skonfigurować kompletną szafę elektryczną z wyposażeniem, do tego dołączyć klimatyzatory i zasymulować ich pracę, zaś całość zakończyć na pełnej personalizacji, korzystając z automatycznych maszyn produkcyjnych i robotów.
- Dziękujemy za rozmowę.