Do wyrobów cukierniczych zaliczanych jest wiele rodzajów produktów, w tym m.in.: słodkie pieczywo, ciasta, cukierki, batony, czekolady, lody, dżemy, gumy do żucia oraz desery w proszku. O ich specyfice decydują dodatki, jednak podstawowymi składnikami używanymi do ich produkcji, z których przynajmniej jeden można znaleźć w każdej z wyżej wymienionych słodkości, są mąka oraz cukier.
AUTOMATYKA I POMIARY W MAGAZYNACH ZBÓŻ
Istnieje wiele rodzajów mąk. Produkuje się je z różnych roślin, na przykład migdałów, kokosów, ziemniaków, te najczęściej używane do wypieków uzyskuje się natomiast ze zmielonych ziaren zbóż, przede wszystkim z pszenicy oraz z żyta. Na etapach ich odbioru od rolników, a następnie magazynowania wiele zadań można zautomatyzować.
Przykładami są: ważenie pojazdów, którymi zboże jest transportowane, przy użyciu elektronicznych wag z czujnikami tensometrycznymi oraz pobieranie próbek ziaren poddawanych następnie kontroli jakości. W silosach, w których zboże jest przechowywane, korzysta się też z czujników i systemów łączności, którymi transmitowane są wyniki pomiarów.
W związku z rozmiarami takich obiektów przeważnie są to sieci bezprzewodowe. Sensory służą do monitorowania jakości i ilości ziaren w celu kontroli stanu zebranych zapasów. W połączeniu z systemami automatyki mają one, poza zwiększeniem wydajności, za zadanie ograniczyć bezpośredni kontakt personelu ze zbożem. Chociaż bowiem pojedyncze ziarna są niepozorne, w dużych ilościach mogą być bardzo niebezpieczne (patrz: ramka).
CO WPŁYWA NA JAKOŚĆ ZBÓŻ?
Aby ziarno zbóż w silosach nie uległo zepsuciu, powinno być przechowywane w odpowiednich warunkach. Dwie wielkości, które mają szczególne znaczenie dla jego jakości oraz trwałości, to: temperatura oraz wilgotność.
W przypadku silnego zawilgocenia ziaren łatwiej rozwijają się grzyby, pleśń, insekty. Jest to też czynnik sprzyjający oddychaniu oraz kiełkowaniu zboża. To ostatnie zachodzi szybciej, jeżeli w zbiorniku jest ciepło. W takich warunkach aktywniejsze są również owady, pleśń oraz grzyby. W niższych temperaturach szkody przez nie czynione postępują wolniej.
Jeżeli dopuści się do powstania gorących i wilgotnych skupisk ziaren, nasili się ich oddychanie, a wtedy jeszcze zwiększy się ilość wydzielanych przez nie w tym procesie ciepła i wilgoci. Więcej będą ich produkować również insekty oraz mikroorganizmy rozwijające się w zbożu.
Ponadto ogniska ciepła i wilgoci będą się rozszerzać na resztę zbiorów dzięki konwekcji (patrz ramka) i faktowi, że ziarno jest dobrym termoizolatorem pod warunkiem, że struktura kopca, w który się uformuje w silosie, nie zostanie naruszana na przykład przez wymieszanie.
JAK MIERZYĆ TEMPERATURĘ ZIARNA?
Temperatura i wilgotność są zatem wielkościami, które w silosach koniecznie trzeba monitorować. Dawniej w tym celu korzystano z nieprofesjonalnych technik. Na przykład temperaturę oceniano przez wbicie w okolicy środka stosu ziaren metalowego pręta. Po dłuższym czasie, na przykład odczekaniu pół godziny, wyjmowano go i dotykowo sprawdzano jego temperaturę w różnych punktach odpowiadającą temperaturze na różnych głębokościach w zbożu.
Obecnie zdecydowanie odchodzi się od tego typu praktyk, używając przenośnych mierników temperatury obsługiwanych przez personel, który w czasie pomiaru przebywa w silosie, lub stacjonarnych termometrów wielopunktowych, mierzących pionowy rozkład temperatur w zbiorniku, montowanych w nim, z których sygnał pomiarowy jest wyprowadzany do systemu nadrzędnego.
Elementem pomiarowym w tych drugich jest rura metalowa albo wąż, wewnątrz których umieszczane są sensory. Osłony chronią czujniki. Są także wykonywane w taki sposób, by zapewnić odpowiednią wytrzymałość liny pomiarowej na zerwanie.
Ponadto ich powierzchnia powinna być na tyle gładka, żeby produkt w zbiorniku do niej nie przywierał. W przeciwnym razie, z czasem oblepiając rurę, zafałszowywałby wyniki pomiaru. W dużych silosach korzysta się często z kilku lin wpuszczanych w głąb silosu w różnych miejscach.
Punkty pomiarowe mogą być wzdłuż ich długości rozmieszczone w jednakowych odległościach albo każda z nich może sprawdzać temperaturę na innych głębokościach i/albo w różnej liczbie punktów.
STEROWANIE DMUCHAWAMI
Oprócz temperatury wielopunktowe sensory mogą mierzyć również stopień zawilgocenia ziarna i stężenie dwutlenku węgla. Nagły wzrost wartości tej drugiej wielkości jest ważnym objawem zwiększenia aktywności mikroorganizmów rozwijających się w zbożu i/albo pogorszenia się jakości ziaren.
Czujniki umieszczone w zbiorniku dostarczają informacji sterownikowi systemu przewietrzania ziarna powietrzem atmosferycznym w celu jego schłodzenia i/albo osuszenia. Są to instalacje z wymuszonym obiegiem powietrza.
Składają się z: zespołu wentylatorów, nagrzewnic, kanałów wentylacyjnych i otworów wylotowych. Stanowią one alternatywę dla okresowego wysypywania części zboża, zwykle jednej trzeciej, z silosu na zewnątrz, o ile panujące tam warunki (temperatura, wilgotność) na to pozwalają, a następnie wsypywania ich z powrotem.
Dmuchawy są uruchamiane, kiedy temperatura i/lub wilgotność ziaren osiągają wartości graniczne, i pracują do czasu ich obniżenia do wartości optymalnych lub do chwili, gdy parametry powietrza na zewnątrz zbiornika zasilającego system wentylacji staną się na tyle nieodpowiednie (będzie ono za suche, zbyt wilgotne, za ciepłe, zbyt zimne), że dalsze wietrzenie, chłodzenie albo osuszanie nim zboża nie będzie już skuteczne. Na przykład w lecie schładzanie ziarna w silosach powietrzem atmosferycznym możliwe jest głównie nocą, o ile częścią systemu nie jest chłodziarka, która obniżałaby jego temperaturę.
ZALETY POMIARÓW INLINE
Ważną rolę w produkcji mąki odgrywa kontrola jakości surowca, z którego zostanie zmielona. Właściwości ziaren zależą nie tylko od ich gatunku, ale ma na nie wpływ także m.in. klimat. W związku z tym nawet plony zbierane z tego samego pola w kolejnych latach mogą się znacząco różnić pod względem jakości.
Tymczasem od właściwości ziaren zależy to, co będzie można z mąki wyprodukować, na przykład czy lepiej upiec z niej chleb, przeznaczyć ją na wypieki, czy użyć do produkcji makaronu. Oprócz tego ocenie poddawane są cechy zboża, od których zależy, czy jego przerób będzie efektywny, czyli czy przy określonych nakładach producentowi uda się uzyskać mąkę w takiej ilości oraz jakości, które zapewnią ich zwrot i zysk.
W związku z tym w zakładach przetwórstwa zbóż mierzy się wiele parametrów charakteryzujących przemiałową i użytkową wartość ziaren. Przykładowe wskaźniki to: wilgotność, masa hektolitra, stopień wyrównania ziarna, ilość zanieczyszczeń, zawartość popiołu (miara ilości cennych dla zdrowia substancji mineralnych), zawartość glutenu, ogólna zawartość białka, liczba opadania (charakteryzuje poziom enzymów amylolitycznych, za niski powoduje samozagrzewanie ziarna, zbyt wysoki uniemożliwia wyrośnięcie chleba) i wskaźnik sedymentacyjny (niski ma ziarno, które nadaje się tylko na pasze). Do wyznaczania wartości większości z tych wielkości wykorzystywane są m.in. analizatory widma w zakresie bliskiej podczerwieni.
Preferowanym rozwiązaniem stają się pomiary inline, których wyniki są dostępne w czasie rzeczywistym. Zastępują one okresowe pobieranie próbek, nie zawsze reprezentatywnych, i przeprowadzanie na nich testów w zakładowym albo zewnętrznym laboratorium. To pierwsze rozwiązanie jest tańsze, szybsze, nie powoduje przestojów, umożliwia badanie całej partii, co zwiększa dokładność i pozwala na optymalizację procesu przemiału na bieżąco.
Roboty w paletyzacji mąkiCase study 1
Jeśli pracownicy nie przestrzegali tych zasad groziły im poważne urazy kręgosłupa. Pomimo starań takich wypadków nie udawało się całkowicie uniknąć, z czym wiązały się przestoje, koszty leczenia, zwolnień, odszkodowań. Ponadto przy ręcznym załadunku worków zachodził bezpośredni kontaktu pomiędzy pracownikami, a mąką, co ze względów higienicznych nie było pożądane. W związku z tym zdecydowano się proces paletyzacji worków z mąką w pełni zautomatyzować. W tym celu wyposażenie zakładu powiększyło się o przenośniki, którymi opakowania są transportowane na stanowisko załadunku. Tam natomiast pracuje robot przemysłowy posługujący się specjalnymi chwytakami widłowymi przystosowanymi do podnoszenia worków z mąką, którymi przekłada je na palety. W krótkim czasie inwestycja zwróciła się, dzięki znaczącemu zwiększeniu wydajności paletyzacji i odciążeniu pracowników, którzy mogli zająć się innymi zadaniami. |
MASZYNY SPECJALISTYCZNE W CZYSZCZARNI ZIAREN
Produkcja mąki jestem procesem wieloetapowym. Można w nim wyróżnić dwie zasadnicze fazy: przygotowanie ziarna do przemiału i jego mielenie. W realizacji tych zadań korzysta się z szeregu maszyn specjalistycznych.
W pierwszym kroku ziarno trafia do czyszczarni. Najpierw usuwa się zanieczyszczenia, które występują w nim swobodnie i pod względem m.in. rozmiarów, kształtu, koloru, masy, struktury powierzchni znacząco się od niego różnią. W skład linii technologicznej do usuwania ciał obcych tego rodzaju wchodzą z reguły takie maszyny jak na przykład: wialnia, oddzielacze magnetyczne, suche oddzielacze kamieni, które służą do usuwania ze zboża zanieczyszczeń ciężkich, takich jak, poza odłamkami skał, na przykład szkło i tryjery, używane do sortowania ziaren według długości i odrzucania tych za długich albo zbyt krótkich.
Wialnia działa zazwyczaj na zasadzie oddzielania zanieczyszczeń większych (na przykład plewy, kłosy, kawałki słomy) lub mniejszych od ziaren zbóż i/lub od nich lżejszych. W związku z tym częścią takiej maszyny są sita o różnych rozmiarach otworów i/albo układ wentylator-cyklon. Jeżeli chodzi o separatory magnetyczne, to często korzysta z tych urządzeń w wersji podwieszonej. Są one montowane nad taśmociągiem lub rynną, którymi transportowane jest zboże.
Ich częścią jest źródło pola magnetycznego, na przykład magnes trwały, przyciągające metaliczne ciała obce. W ramach zautomatyzowanych linii czyszczenia korzysta się przeważnie z oddzielaczy samooczyszczających się. Cząstki metali, które gromadzą się na czole magnesu, są w nich okresowo usuwane samoczynnie za pomocą specjalnej taśmy, bez konieczności angażowania operatora.
|
JAK SIĘ PRODUKUJE MĄKĘ, A JAK CUKIER?
Kolejnym etapem jest kondycjonowanie ziarna. Polega ono na jego nawilżeniu, a następnie odczekaniu odpowiedniego czasu (leżakowanie), w czasie którego zboże przechowuje się w specjalnych komorach. Następnie przy użyciu maszyn ścierających usuwane są zanieczyszczenia, które przylegają do powierzchni ziaren i ich okrywy. W kolejnym kroku sporządza się mieszanki ze zbóż różnej jakości.
Dzięki temu uzyskuje się zakładane właściwości przemiałowe oraz użytkowe przy jednoczesnym utrzymaniu opłacalności produkcji. Na przykład do zboża wartościowszego dodawane jest ziarno średniej jakości jako wypełniacz.
Jest tańsze, a przy tym nie wpływa na ostateczną jakość mąki. Z kolei zboże, które nie spełnia standardów, miesza się z dodatkiem ziarna wartościowszego. Dzięki temu niewielkim kosztem znacząco poprawia się jakość mieszanki. Następnie zboże mieli się do uzyskania mąki.
Drugim niezbędnym składnikiem wypieków jest cukier. Produkuje się go przede wszystkim z trzciny cukrowej oraz buraka cukrowego. Dalej, na przykładzie drugiego surowca przedstawiamy najważniejsze etapy tego procesu. Są to: spławianie, oczyszczanie, mycie buraków, pozyskiwanie z nich soku, oczyszczanie i zagęszczanie go, krystalizacja cukru.
Buraki cukrowe najpierw są ważone. Następnie usuwa się z nich zanieczyszczenia - na przykład korzystając z otrząsaczy rolkowych, a potem kroi na plastry, co ma na celu zwiększenie kontaktu buraków z wodą i dzięki temu ułatwienie wypływu cząstek cukru. Krajanka poddawana jest ługowaniu w dyfuzorach.
Efektem tego jest sok i produkt uboczny - wysłodki, które prasuje się, a następnie suszy. Sok poddaje się defekacji (nawapnianiu) z wykorzystaniem mleka wapiennego. Produkt tego procesu przechodzi kilkustopniową saturację.
Po oddzieleniu błota saturacyjnego powstaje sok rzadki. Kolejne etapy jego przetwarzania to: odwapnianie, siarczynowanie i zatężanie. Ich efektem jest sok gęsty. W wyniku gotowania ulega on krystalizacji. Dalej jest odwirowywany i poddawany rafinacji.
PAKOWANIE PRODUKTÓW SYPKICH
Aby mąkę i cukier można było rozdystrybuować do odbiorców, trzeba je podzielić na porcje o określonej masie, a potem zapakować. Chcąc te procesy zautomatyzować, należy uwzględnić specyfikę postaci, w jakiej występują. Przy tej okazji można przedstawić kilka ogólnych wytycznych prawdziwych również w przypadku innych sypkich produktów, których wiele produkuje się w przemyśle spożywczym, jak na przykład kakao, przyprawy, zupy, mleko w proszku, zmielona kawa.
Organizując stanowisko pakowania, powinno się rozstrzygnąć kilka kwestii. Jedną z nich jest zakwalifikowanie wyrobu, który należy umieścić w opakowaniu, do jednej z dwóch kategorii. Do pierwszej zalicza się produkty sypkie, których cząstki nie są wzajemnie przyczepne.
Przykładami takich są: cukier granulowany oraz sól kuchenna. W ich przypadku z reguły wywarcie większego nacisku nie spowoduje zmniejszenia objętości ani nie zachowają uzyskanego przez to kształtu.
Ich przeciwieństwem są takie produkty jak na przykład mleko w proszku, kakao, zmielona kawa. Uciśnięcie spowoduje zmniejszenie ich objętości, a po ustąpieniu nacisku mogą zachować nadany im kształt.
Specyfika obu grup wyrobów wpływa przede wszystkim na wybór sposobu ich przenoszenia. W transporcie pierwszych można wykorzystać siłę grawitacji, drugie wymagają popychania, a w związku z tym korzystania na przykład z pakowarek ślimakowych.
Do drugiej kategorii zaliczana jest też mąka. Jej transportowi towarzyszy powstawanie pyłów w ogromnych ilościach, nie tylko kiedy jest w ruchu, ale także podczas gwałtownego rozruchu albo zahamowania transportera. Są one w stanie rozprzestrzenić się na dużej przestrzeni i przywrzeć do w zasadzie każdego typu powierzchni. Może to być przyczyną poważnych problemów w działaniu urządzeń linii pakowania mąki i innych sypkich produktów.
By im zapobiec, należy stosować specjalne rozwiązania konstrukcyjne. Na przykład ruchome, elektryczne czy pneumatyczne podzespoły maszyn powinny być zabezpieczone obudową o odpowiednim stopniu ochrony przed wnikaniem do niej drobin pyłów, co najmniej IP5X, a nawet IP6X.
Poza tym duże zapylenie zagraża nie tylko ciągłości pracy linii pakowania, ale i szczelności opakowań, jeżeli bowiem cząstki pyłów zanieczyszczą spoiwo, zgrzew nie będzie trwały. By do tego nie dopuścić, linię pakowania sypkich produktów spożywczych powinno się uzupełnić o urządzenia do odpylania.
Konwekcja w zbożu![]() Rys. 1. Konwekcja w ziarnie Na rysunku 1 przedstawiono mechanizm rozwijania się tytułowego zjawiska, nasilającego się tym bardziej, im większa jest różnica między temperaturą zboża wewnątrz silosu a temperaturą na zewnątrz. Zakładając, że ziarno zostało ułożone w spiczasty stos, na jego powierzchni i tuż pod nią jest wilgotne, a ognisko ciepła znajduje się w samym środku stosu, strzałkami został zaznaczony przepływ prądów konwekcyjnych. Jest on następujący: schłodzone powietrze przepływa wzdłuż ścianek w głąb zbiornika. Na dnie silosu zostaje zassane do wnętrza stosu ziarna przez skierowany do góry strumień cieplejszego powietrza. Tam zostaje ono ogrzane i płynie w kierunku wilgotnej powierzchni zboża, gdzie schładza się i ulega kondensacji. Wówczas cały cykl się powtarza. |
PRZETWARZANIE JAJEK
Uzupełnieniem mąki i cukru niezbędnym do produkcji słodkich wypieków są jajka. W produkcji na masową skalę jednym z zadań, które warto jest zautomatyzować w celu poprawy wydajności oraz spełniania norm higieny przez ograniczenie kontaktu ludzi z płynną zawartością skorupy, jest jej rozbijanie. W tym celu korzysta się z maszyn specjalistycznych - wybijarek.
Udział ludzi w obsłudze tych urządzeń jest ograniczony do załadunku i kontroli jakości. Oba zadania można również zautomatyzować, korzystając z robotów przemysłowych i systemów automatycznej inspekcji wizyjnej. W przypadku jednak, gdy robot nie jest częścią stanowiska rozbijania jajek, pierwszym zadaniem operatora jest załadowanie ich na podajnik grawitacyjny wybijarki.
W tym celu posługuje się zwykle chwytakiem próżniowym, w jaki we w pełni zautomatyzowanych stanowiskach wyposaża się robota. Urządzenie to składa się z kilku rzędów przyssawek, dzięki czemu umożliwia podniesienie i przełożenie z wytłaczanki na podajnik jednocześnie większej liczby jajek.
Są to zazwyczaj ssawki mieszkowe wykonywane z materiału dopuszczonego do użytku w przemyśle spożywczym, na przykład z silikonu. Jeśli szybkość pracy wybijarki można regulować, pozwala to na jej dostosowanie, spowolnienie lub przyspieszenie, do bieżących potrzeb w zakresie wydajności produkcji lub możliwości pracownika, który zajmuje się załadunkiem.
Jajka, przesuwając się na podajniku, są rozdzielane i przenoszone oddzielnymi korytami do części wybijarki, w której przy użyciu zestawu ostrzy odtwarzany jest sposób, w jaki ręcznie rozbija się skorupki. W tym celu jajka najpierw pojedynczo wypadają z koryt i wpadają w dołki, w których zostają unieruchomione z boków i z góry.
Wtedy od spodu w skorupkę uderza nóż i rozchyla ją. Przeważnie głębokość, na jaką wnika ostrze i to, jak szybko to następuje, można regulować w zależności od jakości jajek i tego, czy celem jest dokładne rozdzielenie żółtka i białka, o ile w wybijarce istnieje taka możliwość.
W takim przypadku najpierw obie części jajka spływają razem do rynny. Zadaniem operatora jest oddzielanie tych niespełniających wymagań jakościowych, na przykład rozlanych żółtek, przez ich przekierowanie przy użyciu łopatki do koryta odpływowego. Reszta trafia na rozdzielacz, z którego żółtka i białka spływają do oddzielnych zbiorników.
|
AUTOMATYZACJA MIESZANIA I ZAGNIATANIA CIASTA
Po dodaniu do mąki, cukru i jajek środka spulchniającego należy te wszystkie składniki razem ze sobą wymieszać, a następnie zagnieść ciasto. Zadania te nie należą do fizycznie lekkich, a przy tym sposób, w jaki zostaną wykonane - przede wszystkim dokładność mieszania, szybkość, przyłożona siła i powtarzalność ruchów - wpływają na jakość wyrobu końcowego, bez względu na to, czy jest to domowe ciasto, czy cała seria wypieków przeznaczonych do sprzedaży.
Dlatego, tak jak w kuchniach w domach prywatnych, obecnie rzadko już czynności te są wykonywane ręcznie, także w piekarniach korzysta się z mikserów i robotów kuchennych. Dokładniej są to odpowiedniki takich sprzętów, rozmiarowo większe i wydajniejsze, które przygotowują duże, liczone w setkach kilogramów, ilości ciasta.
Stopień zautomatyzowania mieszania i zagniatania ciasta, jak i kolejnych etapów przygotowywania go do pieczenia, zależy od wielu czynników. Najważniejsze to: skala produkcji, specyfika ciast - na przykład niektóre muszą wyrosnąć, na co potrzeba czasu i zapewnienia odpowiednich warunków, dostępności miejsca do zorganizowania zautomatyzowanego stanowiska i oczywiście środków, jakie przedsiębiorstwo może na ten cel przeznaczyć.
W produkcji na mniejszą skalę korzysta się często z rozwiązań półautomatycznych. Przykładami są: ubijaczki oraz mieszarki. Pierwsze służą do przygotowywania lekkich ciast, a poza tym kremów, ubijania jaj, majonezu, masła i margaryny, zaś drugie do mieszania różnych składników w celu otrzymania ciast cięższych.
Wyposaża się je w panel sterowniczy do wprowadzania ustawień (prędkości i czasu ubijania / mieszania, zmiany kierunku obrotów misy, jeżeli jest ruchoma, włączenia specjalnych trybów pracy, na przykład mieszania ciasta z mąki o dużej zawartości glutenu), a czasem też wprowadza możliwość zapasowego sterowania awaryjnego. Większość funkcji z zakresu manipulowania misą (dzieżą) jest w nich zautomatyzowanych, na przykład: jej mocowanie, zwalnianie, podnoszenie oraz opuszczanie.
Modernizacja zrobotyzowanego stanowiska dekorowania ciastCase study 2 W pewnej piekarni zaopatrującej supermarkety na terenie USA odnotowano spadek liczby zamówień. Przyczyną tego były problemy w dziale dekorowania ciast, z powodu których kilkakrotnie nie przyjęto zlecenia, jeżeli klient oczekiwał wymyślnych, bardzo różniących się od standardowo wykonywanych, zdobień. Oprócz tego czas realizacji kilku zamówień tak bardzo się przedłużył z powodu konieczności ręcznego dekorowania ciast, że zamawiającemu należało wypłacić dużą rekompensatę za opóźnienie. Do piekarni zaczęły też docierać skargi na jakość zdobień. W związku z tym w końcu zdecydowano o zmodernizowaniu istniejącej w zakładzie zrobotyzowanej linii dekorowania. Jak działała "stara" linia?Najpierw kamera rejestrowała obraz kolejnych ciast na przenośniku, a oprogramowanie systemu wizyjnego obliczało współrzędne położenia wypieków na taśmociągu i mierzyło ich górną średnicę. Dane te przesyłano do sterownika robota. Na ich podstawie zdobił on wierzch ciasta. Po przeanalizowaniu działania tego systemu uznano, że powodem jego ograniczeń było bazowanie na informacjach z dwuwymiarowego systemu wizyjnego i przyjęcie założenia, że wszystkie ciasta mają stałą wysokość. Tymczasem nie zawsze jest to prawdą. Na przykład wystarczy lekka zmiana temperatury i nadzienie nieznacznie gęstnieje albo się rozpuszcza, przez co tworzy grubszą albo cieńszą warstwę. To z kolei powoduje, że ciasto jest minimalnie wyższe lub niższe. Podobnie większe zawilgocenie lub zbyt suche powietrze sprawia, że ciasto pęcznieje lub opada pod ciężarem kremu. Do tego dochodzą niedokładności maszyn na liniach cięcia biszkoptów i ich przekładania kremem. Różnice między rzeczywistą wysokością ciasta, a przyjmowaną w obliczeniach przez sterownik robota powodowały, że zdobienia przez niego wykonywane były zniekształcone. Ponadto jeśli dekoracjami należało otoczyć dolną podstawę ciasta, której dokładnego rozmiaru nie znano, zadanie to należało wykonać ręcznie. RozwiązanieRozwiązaniem okazało się zastąpienie systemu wizyjnego 2D laserowym skanerem 3D. Za jego pośrednictwem sterownik robota pozyskiwał informacje nie tylko o dokładnej wysokości każdej sztuki ciasta, ale i o jego kształcie. Dzięki temu mógł ozdabiać nie tylko górną warstwę, ale i dekorować dolną podstawę, a nawet nanosić wzory na bokach ciasta. Znacząco poprawiła się też dokładność odwzorowywania projektów klientów, a dzięki możliwości całkowitej rezygnacji ze zdobienia ręcznego, również szybkość realizacji zamówień. |
MASZYNY PÓŁAUTOMATYCZNE, CIĄGI ZAUTOMATYZOWANE
Z ubijaczkami i mieszarkami współpracują podnośniki. Ich zadaniem jest przekładanie ciasta do kolejnej maszyny, na przykład wagodzielarki. Jest to realizowane przez podniesienie misy, a następnie jej przechylenie nad lejem wagodzielarki. Podnośniki wyposaża się w skrobaczki automatycznie czyszczące dzieżę po wyładowaniu z niej jej zawartości, co znacznie ułatwia ich mycie.
Korzystając z maszyn półautomatycznych, trzeba pamiętać o licznych niebezpieczeństwach, na które jest narażony operator pomimo zautomatyzowania zasadniczego zadania musi on bowiem wykonywać wiele innych pomocniczych, takich jak m.in. załadunek i dodawanie składników w trakcie mieszania.
Przykładowe zagrożenia to uszkodzenie kręgosłupa lub naciągnięcie mięśni w czasie ręcznego ładowania ciężkich surowców, czemu zapobiega ich podział na mniejsze porcje i urazy spowodowane kontaktem z ruchomymi częściami obsługiwanych urządzeń, na przykład w razie włożenia ręki pomiędzy pracujące łopaty miksera albo wciągnięcia przez nie włosów, ubrania, biżuterii, co powinny uniemożliwić osłony otaczające misę. Wyposaża się je w czujniki, które zatrzymują pracę maszyny w przypadku ich podniesienia.
W produkcji na masową skalę korzysta się z w pełni zautomatyzowanych ciągów technologicznych, składających się z maszyn specjalistycznych i systemów transportowych. W tym zakresie dostępne są różne rozwiązania i konfiguracje.
Przykładem są linie karuzelowe. W tego typu ciągach kluczowym komponentem jest kilkuramienna ruchoma rama nośna. Na jej poszczególnych odnogach umieszczane są misy. Rama okresowo się obraca. Z każdym jej przesunięciem ramiona, a wraz z nimi misy, przemieszczają się z jednego stanowiska roboczego na drugie.
Dzięki temu kolejno przechodzą przez etapy, na przykład mieszania składników, zagniatania ciasta, jego leżakowania, odgazowania oraz wyładowania. Zaletą linii technologicznych w tej konfiguracji jest oszczędność miejsca dzięki ich kompaktowości oraz duża wydajność. Uzyskuje się ją dzięki temu, że jednoczesna realizacja kolejnych faz procesu produkcji ciasta pozwala na równoczesne produkowanie kilku jego partii.
FORMOWANIE I CIĘCIE CIASTA
Kolejnym przykładem zastosowania maszyn specjalistycznych na etapie przygotowania ciasta do pieczenia jest automatyzacja jego cięcia i formowania w różne kształty. W tym zakresie oferta dostawców jest bardzo bogata. Przykładowe urządzenia to: wagodzielarki, zaokrąglarki, dzielarko-zaokrąglarki, wałkownice, rogalikarki, maszyny do ciastek i krajalnice ultradźwiękowe (patrz ramka).
Pierwsze z wymienionych służą do dzielenia ciasta na porcje o określonej masie, a dwie kolejne do objętościowego porcjowania oraz zaokrąglania kęsów ciasta na przykład na bułki albo pączki. W tym celu korzysta się z noży i tłoków zasysających i odmierzających, co pozwala uniknąć efektu męczenia ciasta i zapewnia jego napowietrzenie.
Kolejne maszyny są używane do wałkowania i zwijania kawałków ciasta w rogaliki, paluchy itp., a ostatnie do formowania ciastek, w zależności od modelu z ciasta jedno- albo wielokolorowego, z nadzieniem wewnątrz albo na zewnątrz.
W urządzeniach tego typu wprowadza się specjalne rozwiązania konstrukcyjne, które zapobiegają przywieraniu ciasta. Na przykład ich elementy pokrywa się teflonem, stosuje się specjalne faktury powierzchni, wyposaża się je w automatyczne posypywacze mąki z płynną regulacją intensywności posypywania w zależności od prędkości działania oraz systemy olejenia. W maszynach do ciastek z kolei korzysta się z pomp zębatych, co pozwala na formowanie ich z ciast twardszych oraz z dodatkami, na przykład kawałkami orzechów.
AUTOMATYZACJA SPRYSKIWANIA
W ramach przygotowania do pieczenia niektóre rodzaje ciast wymagają pokrycia cienką warstwą środków konserwujących, oleju lub wody, bez albo z dodatkiem na przykład słodkiego syropu. Ta ostatnia zapewnia lepsze przyleganie ziaren lub innych dodatków, którymi ciasto jest obsypywane.
Ponadto stosuje się środki antyadhezyjne, którymi pokrywa się na przykład przenośniki. Mają one za zadanie zapobieganie przywieraniu ciasta do powierzchni, z którymi ma kontakt.
Ręczne nanoszenie powłok ma wiele wad. Przede wszystkim jest czasochłonne. Poza tym może powodować zabrudzenie otoczenia i osoby, która tę czynność wykonuje, bowiem mgiełki rozpylanych substancji unoszące się w powietrzu w końcu osiadają na niej, wyposażeniu stanowiska, podłodze. Jest to niehigieniczne, ponieważ nawarstwienie się oleistych substancji sprzyja przywieraniu do nich brudu.
Przez to z kolei częściej trzeba sprzątać, a zwłaszcza czyścić powierzchnie mające kontakt z żywnością, na przykład taśmy przenośników, co powoduje częstsze przestoje. Może to być też niebezpieczne, jeśli bowiem olej albo woda nagromadzą się na podłodze, tworząc plamy albo kałuże, stanie się ona śliska.
Ponadto ręczne spryskiwanie ciasta prowadzi do marnotrawstwa i trudno zapewnić jego dokładność i powtarzalność. Ma to wpływ na efekt końcowy. Na przykład zwilżenie surowego ciasta zbyt dużą ilością wody może spowodować, że podczas pieczenia nie urośnie albo ziarna się zepsują, natomiast jeżeli będzie jej za mało, dodatki będą odpadać. Zwiększy to liczbę wyrobów, które nie przejdą kontroli jakości.
Wszystko to zachęca do zautomatyzowania tego zadania. Uzupełniając linię przygotowania ciasta do wypieku o automatyczne dozowniki eliminuje się powyższe wady, zyskując pewność, że zawsze zaaplikowana zostanie odpowiednia ilość substancji we właściwym miejscu i momencie.
PIECE I KONTROLA WARUNKÓW PIECZENIA
Wybierając piec do piekarni albo cukierni, trzeba wziąć pod uwagę głównie rodzaj jego zasilania, poziom produkcji i rodzaj wypiekanych produktów. Do produkcji chleba przeważnie wybierane są piece cyklotermiczne, a w pieczeniu bułek, ciast i ciastek sprawdzają się piece obrotowe.
Warunki, w jakich zachodzi proces pieczenia, w ogromnym stopniu wpływają na jakość wyrobu końcowego. Jedną z wielkości, którą należy monitorować i regulować, jest wilgotność powietrza w piecu. Przykładem wyrobu, w przypadku którego wartość i zmienność tej wielkość odgrywa dużą rolę, są krakersy.
Jeżeli powietrze będzie zbyt wilgotne pomimo obróbki w wysokiej temperaturze, którą stopniowo się zwiększa typowo od 150 do 300°C, ciastka te pozostaną zbyt mokre, przez co nie uzyskają cechy je wyróżniającej, jaką jest ich kruchość. Ponadto łatwiej będą się psuć. Z drugiej strony zbyt suche powietrze w piecu też nie zapewni optymalnych warunków pieczenia.
Skutki przesuszenia bywają dwojakie. Powierzchnia krakersów może na przykład zbyt szybko wyschnąć, co sprawi, że wilgoć zawarta w głębszych warstwach ciasta zostanie w nich "uwięziona". Wpłynie to negatywnie na ich smak i kruchość. Drugim skutkiem przesuszenia może być to, że ciastka będą zbyt łamliwe.
To może utrudnić ich pakowanie, a później zniechęcić klientów do kolejnego zakupu, jeżeli po otwarciu opakowania wysypią się z niego, zamiast ciastek, ich okruchy. Ponadto nadmierne osuszenie powietrza alarmuje o marnotrawstwie energii zasilającej.
W związku z tym piece wyposaża się w czujniki i regulatory temperatury oraz wilgotności. Warunki, jakie panują wewnątrz tych urządzeń, wymagają stosowania specjalnych rozwiązań konstrukcyjnych, na przykład ceramicznych osłon, przewodów przyłączeniowych w izolacji z włókna szklanego, długich sond oraz kołnierzowych zestawów instalacyjnych umożliwiających instalację przez materiały izolacyjne z regulowaną głębokością montażu.
|
WYGLĄD MA ZNACZENIE
Ostatecznie to smak przesądza o tym, czy dany wyrób spożywczy przypadnie klientowi do gustu i w przyszłości zdecyduje się on na jego kupno ponownie. Mimo to wrażenie, jakie odniesie, nabywając go po raz pierwszy, zależy często głównie od jego wyglądu.
Dlatego producenci tak ogromną wagę przywiązują do tego, by opakowania produktów w ich ofercie były estetyczne i przyciągały wzrok. W przypadku wyrobów cukierniczych, które są często sprzedawane na wagę, w związku z tym, że wabikiem nie może być opakowanie klienta, o tym, że są smaczne i warto je kupić, musi przekonać to, jak się same prezentują.
W przypadku słodkich wypieków pierwszym wyznacznikiem jakości jest kolor, bowiem na jego podstawie można instynktownie wywnioskować, jak będą smakować. Wynika to stąd, że ta cecha wyrobu, na przykład ciastek, odzwierciedla przebieg złożonych reakcji chemicznych (na przykład karmelizacji), które zachodzą w cieście poddanym obróbce w wysokiej temperaturze, powodujących jego zbrązowienie, jak również zmianę jego smaku, zapachu oraz struktury.
Zagrożenia w silosachZiarna, chociaż pojedyncze są niepozorne, w dużych ilościach, w jakich są magazynowane w silosach, których pojemności wynoszą od setek do tysięcy ton w jednym zbiorniku, mogą być bardzo niebezpieczne. Zagrożeniem jest nie tylko ich duża masa, ale i to, że gdy się poruszają, zachowują się jak ruchome piaski. Przez to w przechowalniach zbóż nietrudno o wypadek. Przykładowe zdarzenia to, na zewnątrz: zasypanie pracownika znajdującego się obok zbiornika na skutek awarii mechanizmu rury wysypowej, a wewnątrz: zapadnięcie się ziaren, które uformowały most pod osobą na nich stojącą lub jej wchłonięcie przez ziarna przemieszczające się w czasie na przykład ich wyładowywania. Wypadki, w których zboże w dużej ilości przygniecie człowieka zazwyczaj niestety kończą się śmiercią ofiary na skutek jej przyciśnięcia i/albo uduszenia. |
KONTROLA JAKOŚCI WYPIEKÓW
Jeżeli ciastka będą niedopieczone z powodu zbyt małej ilości ciepła, reakcje te w pełni nie zajdą, w związku z czym będą one miały za jasny kolor, będą miękkie i mdłe w smaku. Z kolei te przypalone wyróżniać będzie ciemniejszy kolor, będą nadmiernie kruche, zaś w smaku gorzkie.
W związku z tym, że producenci wiedzą o tym, że klienci mają świadomość zależności pomiędzy kolorem a smakiem wypieków, sprawdzanie tej cechy jest nieodzownym etapem kontroli jakości w przemyśle piekarskim.
Z kilku powodów w przypadku ciastek nie jest to łatwym zadaniem. Pierwszym utrudnieniem jest to, że nie są one jednolite pod względem kształtu, rozmiaru, tekstury oraz koloru, nawet w obrębie jednej partii produkcyjnej. Jeszcze więcej komplikacji sprawiają wypieki z dodatkami, na przykład posypane czekoladowymi drobinami.
Ponieważ takie kawałki czekolady są rozmieszczone losowo, a dodatkowo powodują powstawanie głębokich pęknięć, które na tle jaśniejszego ciasta też wydają się ciemniejsze, gołym okiem trudno jest szybko rozstrzygnąć, czy odmienny kolor jest wynikiem przypalenia, czy nie. Przez to ręczna kontrola jakości takiego pojedynczego problematycznego wypieku może się znacznie przeciągnąć.
Tymczasem ze względu na specyfikę procesu pieczenia nie można przeważnie przyjąć założenia, że jeżeli losowo wybrane ciastko lub nawet kilka sztuk spełnia wymogi jakościowe, reszta również nadaje się do sprzedaży lub odwrotnie, stwierdzić, że cała partia jest wybrakowana, jeżeli jedno albo kilka ciastek się przypali lub nie dopiecze.
Dlatego to zadanie automatyzuje się, korzystając na przykład z systemów wizyjnych lub spektrofotometrów. Dzięki temu można uzyskać dokładność i szybkość inspekcji, jakie są wymagane w produkcji na masową skalę.
Krajalnice ultradźwiękowe
Dzięki temu nie ma ono bezpośredniego kontaktu z rozcinanym materiałem. Pozwala to na szybkie, higieniczne oraz niezmieniające struktury ani wyglądu cięcie żywności (estetyka wyrobu w branży cukierniczej jest bardzo ważna), w tym również produktów wielowarstwowych, z masami o różnej gęstości i z tendencją do rozmazywania się, na przykład ciast nadziewanych kremem. Dzięki temu, że ich cząstki nie przywierają do ostrza, jego czyszczenie jest łatwiejsze, a żywotność dłuższa. |
JAK SIĘ PRODUKUJE KREMY DO CIAST?
W produkcji ciast i ciasteczek używa się szeregu różnego typu dodatków, które wzbogacają ich smak. Przykładami są: polewy czekoladowe, cukrowe posypki, nadzienia w postaci owocowych wsadów oraz kremów cukierniczych.
Tych ostatnich używa się w całej gamie wyrobów, od tortów, przez rolady, przekładane wafle i ciastka biszkoptowe, po markizy. Na ich przykładzie wyjaśniamy, jak specyfika produktu może wpłynąć na sposób organizacji i wyposażenie linii produkcyjnej.
Kremy cukiernicze stanowią półprodukt, którego podstawowymi składnikami są tłuszcz i cukier, a ich uzupełnieniem rozmaite dodatki, na przykład kakao, mleko w proszku, woda. Ich produkcja jest przeważnie realizowana w ramach ciągu procesów, m.in. wsadowych, takich jak: rozpuszczanie tłuszczu w stałej postaci w oleju, mieszanie tłuszczy z suchymi składnikami, głównie cukrem, krystalizacja, pasteryzacja.
Można wyróżnić zasadniczo trzy kategorie kremów cukierniczych: ciężkie, lekkie oraz lekkie, ale z dodatkiem wody. Różnice między ich właściwościami determinują ich zastosowania. Na przykład te ostatnie są używane głównie jako nadzienie w roladach.
Kremy zaliczane do kategorii lekkich, ale bez wody, są z kolei stosowane jako wypełnienie w przekładanych wafelkach. Przykładowe zastosowanie kremów ciężkich to natomiast wypełnienie ciastek typu markizy.
Od kremu, którym przekłada się markizy, oczekuje się, że będzie pełnił funkcję podpory i spoiwa ciastek. W związku z tym powinien być odpowiednio gęsty oraz mieć wyższą temperaturę topnienia. Aby uzyskać takie właściwości, dużą ilość cukru rozpuszcza się w rozgrzanym tłuszczu, nie dopuszczając do tego, żeby proces krystalizacji ich mieszaniny zakończył się, zanim połówki markizy nie zostaną nią przełożone.
Wynika stąd, że najlepiej kiedy kremy ciężkie są produkowane możliwie najbliżej stanowiska, na którym zostaną wykorzystane w wyrobie docelowym. Ponadto w ich transporcie należy korzystać z pomp przystosowanych do przenoszenia materiałów o właściwościach abrazyjnych. W związku z ich dużą gęstością i słabym płynięciem powinny być one wyposażone w napędy o odpowiednio dużym momencie obrotowym.
PODSUMOWANIE
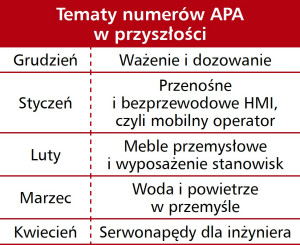
Tematy numerów APA w przyszłości
Jak wynika z przedstawionych w artykule przykładów z branży cukierniczej, w przemyśle spożywczym istnieje wiele zastosowań dla systemów automatyki, maszyn specjalistycznych oraz czujników. W produkcji żywności nie brakuje też zadań, w których ludzi wspierają albo zastępują roboty przemysłowe.
Poza tym, że wykorzystuje się je w automatyzacji pakowania i paletyzacji, z powodzeniem, zwykle we współpracy z systemami wizyjnymi, powierza im się wykonywanie czynności wymagających dużej precyzji, na przykład dekorowania ciast (patrz ramka).
Monika Jaworowska