Jak działają inteligentne korowarki?
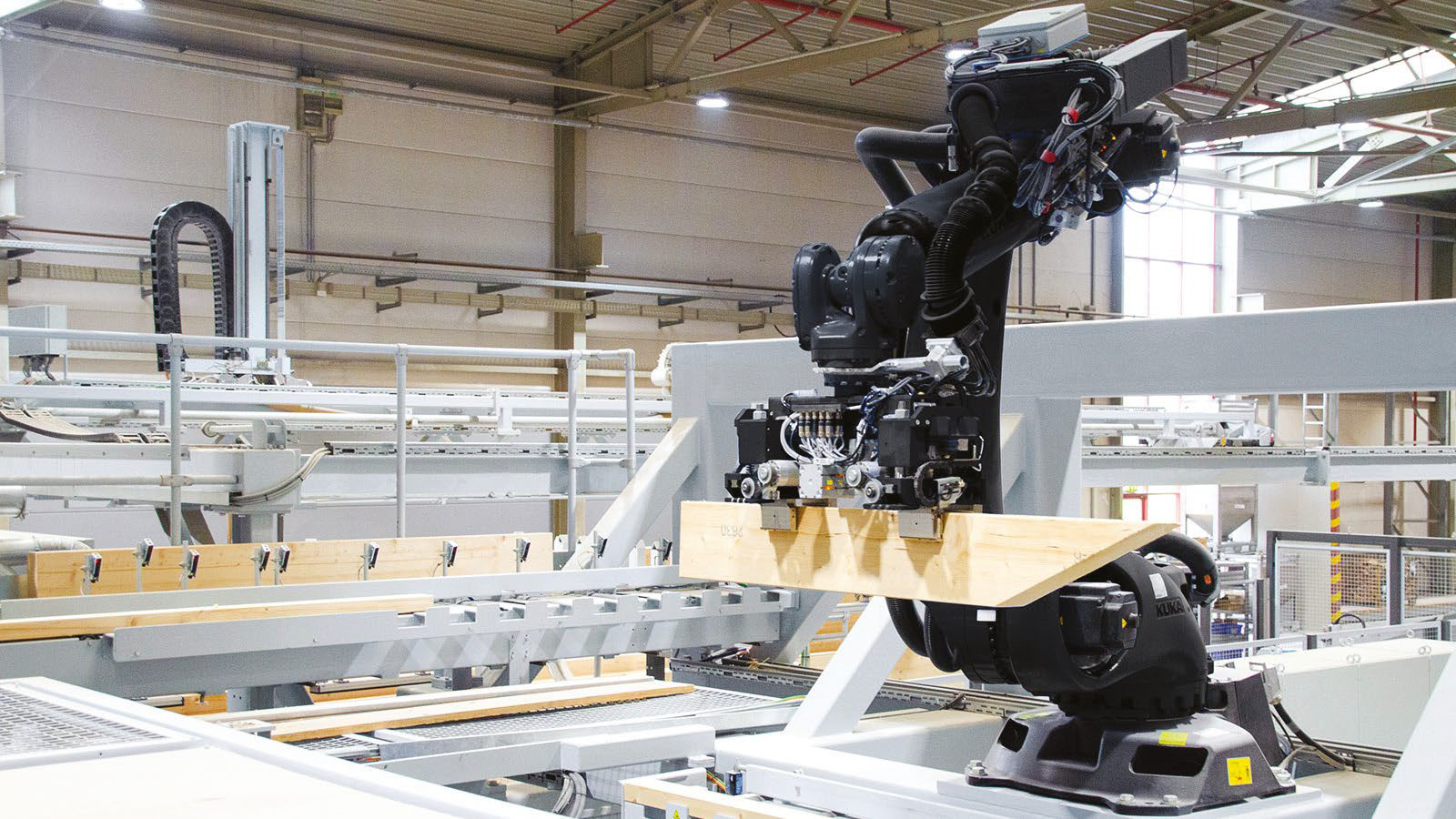
Wykorzystują to producenci inteligentnych korowarek. Tego typu urządzenia mają możliwość samoregulacji oraz uczenia się przez analizowanie cech kłód. W przykładowej realizacji taka maszyna składa się z trzech podsystemów. Pierwszy, w oparciu o szereg czujników, mierzy najważniejsze cechy kłód i warunki, w jakich odbywa się korowanie (średnice wzdłuż pnia, długość kłody, jej skrzywienia i stożkowatość, temperaturę). Na tej podstawie drugi dobiera odpowiednie parametry obróbki, czyli w tym przypadku siłę nacisku ostrzy, prędkość posuwu taśmociągu z kłodami oraz prędkość wirowania ostrzy. Są one równocześnie modyfikowane w oparciu o dane dostarczane w pętli sprzężenia zwrotnego z systemu wizyjnego kontrolującego jakość kłód (ilość pozostawionej kory, stopień utraty włókien, gładkość powierzchni), który współpracuje z oprogramowaniem, w którym zostały zaimplementowane algorytmy uczenia maszynowego. Te, analizując związek między ustawieniami narzędzi tnących i przenośnika a końcową jakością pni, wyciągają wnioski i parametry pracy korowarki sukcesywnie korygują, żeby uzyskać jak najlepsze wyniki.
Jak efektywnie ciąć drewno na deski?
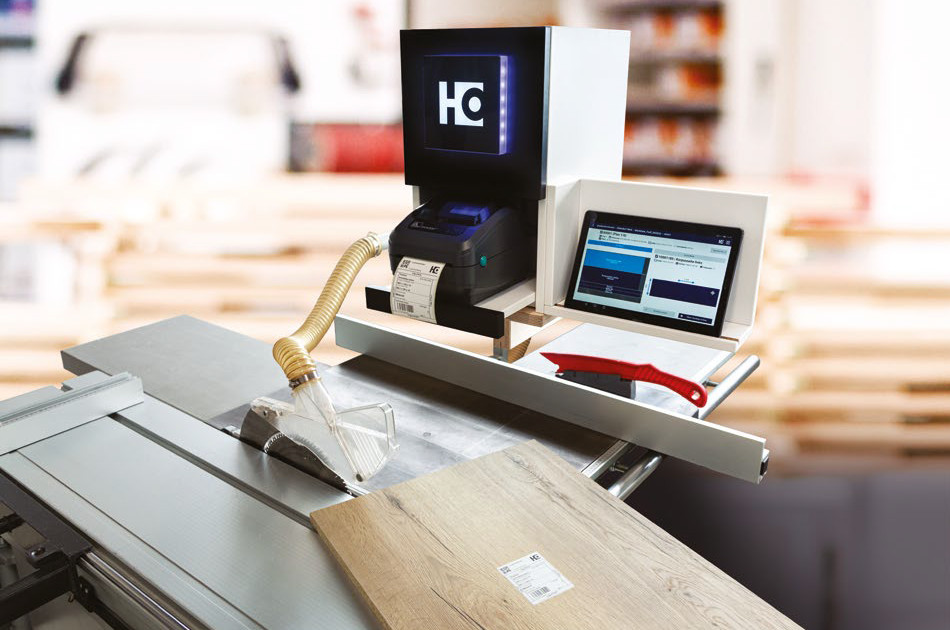
W kolejnym kroku kłody tnie się na deski. Pnie drzew rozcina się po łuku. W ten sposób ogranicza się straty drewna na wyrównywanie, z którymi trzeba by się liczyć, chcąc prosto ciąć powyginane kłody. Dotyczy to zwłaszcza tych o mniejszych średnicach.
Rozcinanie po łuku realizuje się w ten sposób, że dla każdego kawałka drewna wyznacza się ścieżkę cięcia zoptymalizowaną pod kątem jakości oraz wytrzymałości desek, przy możliwie najmniejszej stracie surowca. Dwie pierwsze cechy uzyskuje się, omijając defekty i podążając za wzorem słojów. Otrzymane w ten sposób zakrzywione deski są później prostowane w czasie suszenia.
Rozcinanie drewna po łuku jest przeważnie realizowane na jeden z dwóch sposobów. W pierwszym manipuluje się pniami naprowadzanymi na stacjonarne piły, natomiast w drugiej metodzie przesuwa się ostrza. Optymalny profil ich ruchu jest wyznaczany na podstawie danych na przykład ze skanera laserowego oraz stacji inspekcji rentgenowskiej. W sterowniku ostrzy jest on zestawiany z aktualną pozycją piły, która jest następnie regulowana odpowiednio do wyniku tego porównania.
Nesting w produkcji mebli tapicerowanych
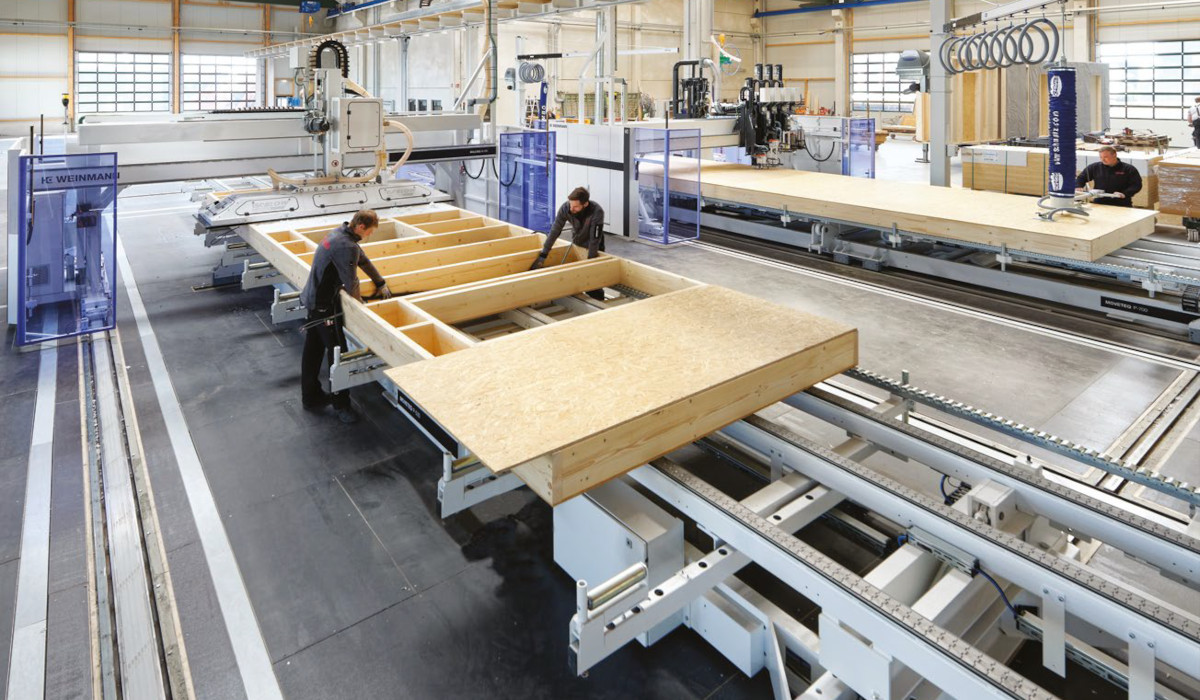
Deski wyprodukowane w tartaku są wykorzystywane jako materiał budowlany i wykończeniowy. Ważnym klientem tych zakładów jest również przemysł meblarski. Wyróżnić można kilka typów mebli, w tym z litego drewna, z wikliny i tapicerowane. Potencjał automatyzacji jest szczególnie duży w przypadku tych ostatnich.
Przykładowo popularnym rozwiązaniem w produkcji mebli tapicerowanych jest wykorzystanie centrów obróbczych CNC do rozcinania płyt drewnianych na części potrzebne do wykonania stelaża, cięcia pianki poliuretanowej, którą obudowuje się stelaż i rozcinania na części tkanin, którymi obija się mebel. Aby zapobiec marnotrawieniu materiałów, na każdym z tych etapów wdraża się metodę nestingu (zagnieżdżania).
Polega ona na rozplanowaniu elementów do wycięcia na dostępnej powierzchni płyty, pianki lub materiału w taki sposób, aby pozostało na niej jak najmniej niewykorzystanego miejsca. Dzięki temu w jednym cyklu pracy maszyny CNC wycinane są od razu wszystkie części. Nie trzeba zatem angażować pracowników, żeby zmieniali ułożenie materiału do kolejnych cięć, a ilość powstałych przy tym odpadów jest ograniczona do minimum. Nesting wykorzystuje się przy wycinaniu kształtów nieregularnych, wymagających cięć krzywoliniowych oraz regularnych, wykrawanych cięciami prostymi.
Efektywność rozplanowania elementów zależy od skuteczności algorytmów zaimplementowanych w oprogramowaniu realizującym zadanie nestingu. Na uzyskane oszczędności wpływa dodatkowo wymiana informacji między taką aplikacją a system przyjmowania i zarządzania zamówieniami.
Produkcja wkładów sprężynowych do materacy
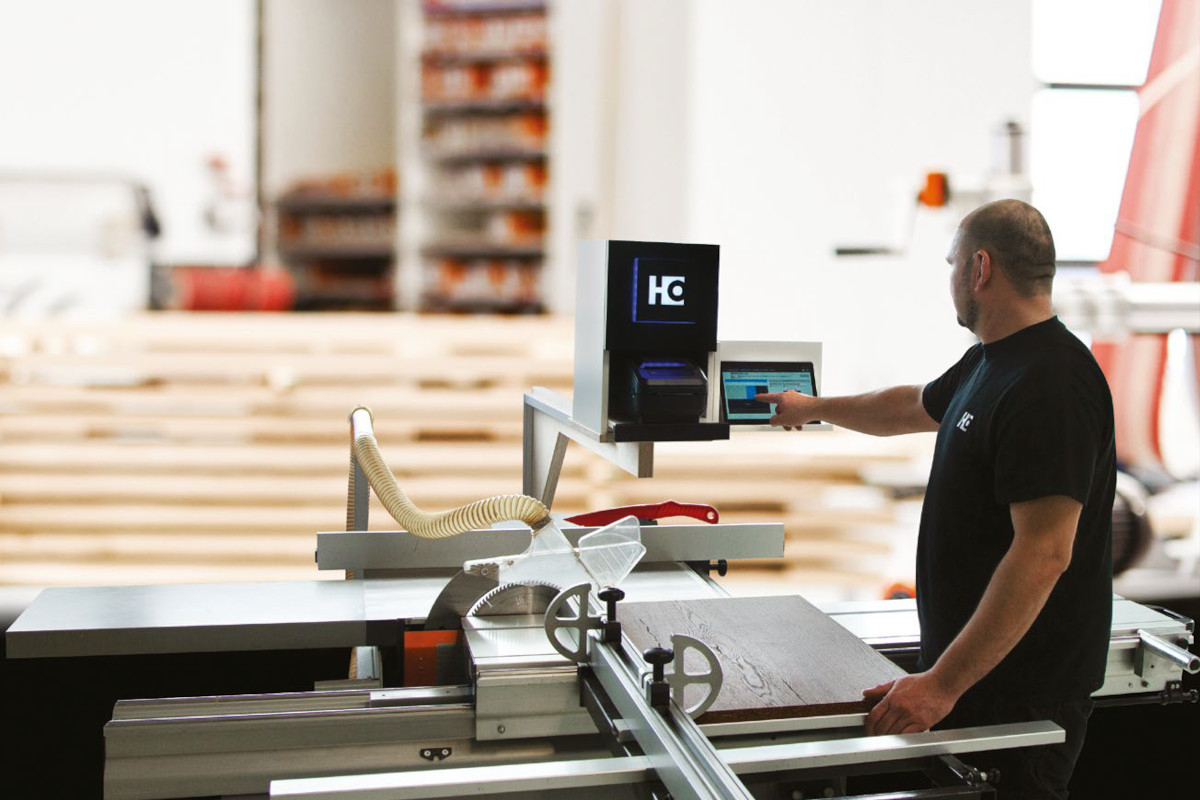
Poza meblami wypoczynkowymi tapicerowanymi, jak wersalki, fotele, sofy, ważnym podtypem tej kategorii są łóżka złożone ze stelaża i materaca. O tym, czy łóżko będzie wygodne, decyduje przede wszystkim wypełnienie materaca.
Rosnącą popularnością cieszą się materace ze sprężynami kieszeniowymi. Ten rodzaj wypełnienia coraz częściej wypiera z rynku sprężyny bonellowe, co wynika z zalet sprężyn zamykanych, każda oddzielnie, w kieszonkach z materiału. Przede wszystkim dzięki temu, że nie są ze sobą połączone, zapewniają podparcie w miejscu nacisku niezależnie i podążają za zmianą pozycji osoby na nich leżącej. To jest korzystne dla kręgosłupa. Ponadto nie przenoszą drgań.
Produkcja sprężyn jest oddzielnym procesem – producenci materaców zazwyczaj zaopatrują się w nie u zewnętrznych dostawców. W przypadku tych kieszeniowych najpierw sprężyny wkładane są do oddzielnych woreczków z tkaniny, które są ze sobą połączone. Powstają wówczas łańcuchy kieszonek, które rozcina się na odcinki o wymaganej długości. Te są ze sobą punktowo sklejane bokami za pomocą kleju termotopliwego. W zależności od wymagań powstałe w ten sposób płachty są obklejane z góry i od dołu tkaniną, na przykład polarową. Boczne łączenia punktowe zapewniają ruchomość poszczególnych sprężyn, zaś obklejenie tworzy powierzchnię nośną o dużej elastyczności.
Punktowe sklejanie boków jest kluczowym etapem w produkcji sprężyn kieszeniowych. O jakości, powtarzalności, wydajności i elastyczności tego procesu decydują głowice użyte do aplikacji kleju. Zwykle, dla uzyskania jak najlepszych efektów, wyposaża się je w kilka dysz, które można włączać i wyłączać niezależnie. Spotyka się też systemy aplikacji kleju z dwoma głowicami o indywidualnie regulowanej wysokości. Wykorzystywane są przeważnie dysze kątowe. Opcjonalnie integruje się je z systemem pomiaru i optymalizacji zużycia kleju.
Etapy w produkcji krzeseł
Meblami, których nie może zabraknąć w żadnym domu ani biurze, są krzesła. Te drewniane zalicza się do kategorii mebli z litego drewna, chociaż zawierają też elementy metalowe, zwykle ozdobne i łącznikowe oraz obicia, wypełnione na przykład gąbką, na siedzeniach.
Proces produkcji krzesła zaczyna się od strugania bloków drewna, na które zostały porozcinane pnie. Jego celem jest wyrównanie ich powierzchni – struganie to metoda obróbki skrawaniem polegająca na wiórowym usuwaniu materiału przez jednoostrzowe narzędzie wykonujące ruch prostoliniowy przerywany. W tym celu kawałki drewna są obracane i dociskane do stacjonarnej maszyny tnącej. Kolejne kroki to czopowanie i kołkowanie, podczas których wycina się występy, które później wkłada się we wpusty i łączy kawałki drewna za pomocą kołków. Następnie części krzesła są szlifowane. Ostatnie dwa etapy to montaż i wykończanie powierzchni. Ich kolejność może być różna. W zależności od typu krzesła oraz wymagań jakościowych mebel ten może być najpierw montowany, a potem wykończany albo odwrotnie, jest wykończany przed montażem.
Case study: Roboty składają meble![]() Naukowcy z Singapuru opracowali system robotów przemysłowych, które potrafią samodzielnie złożyć krzesło z Ikei. Składa się on z dwóch maszyn, których ramiona wyposażono w kamery 3D, chwytaki oraz zamontowane w nadgarstkach czujniki siły. Zadanie jest wykonywane etapowo. Pierwszym krokiem jest analiza widoku 3D elementów ułożonych na podłodze, które wcześniej rozpakowali i przygotowali do montażu ludzi. Zadaniem w tym celu zaimplementowanych algorytmów przetwarzania obrazów jest rozpoznanie i zlokalizowanie poszczególnych części krzesła. Następnie muszą zostać zaplanowane ścieżki ruchu obu ramion, tak aby poruszały się szybko i bezkolizyjnie. Ruchy powinny być skoordynowane z siłą nacisku chwytaków na części, dobraną tak, aby robot był w stanie odpowiednio silnie, ale bez zniszczenia, chwytać elementy krzesła i je ze sobą łączyć, na przykład za pomocą kołków montażowych. Wszystkie te czynności, które ludziom przychodzą naturalnie, w tym przypadku wymagały implementacji specjalnych algorytmów postępowania. W przyszłości naukowcy zapowiadają prace nad zwiększeniem autonomii systemu, dzięki wdrożeniu rozwiązań sztucznej inteligencji, by przykładowo roboty mogły uczyć się kolejnych etapów montażu przez obserwację ludzi, na podstawie instrukcji obsługi, a nawet tylko z obrazu zmontowanego krzesła. Skrócony ma być także czas ich pracy – w pierwszej wersji systemu roboty składały krzesło w 8 minut i 55 sekund, wcześniej przez 11 minut i 21 sekund, planując ścieżki ruchu i w 3 sekundy, lokalizując części. |
W pierwszym, częstszym przypadku unika się uszkodzeń finalnego wyrobu, o co jest nietrudno podczas jego składania. W ramach wykończania natomiast powierzchnię drewna powleka się specjalnymi środkami. W zależności od typu zabezpieczają one drewno przed wysychaniem, pękaniem, blaknięciem, zadrapaniami, poplamieniem, wilgocią.
Substancje te dzieli się na: penetrujące i powlekające. Pierwsze wnikają pod powierzchnię, na którą je nałożono i zostają przez drewno wchłonięte, natomiast drugie tworzą na jego powierzchni trwałą powłokę ochronną. Środki penetrujące, przeważnie oleje naturalne, stosuje się, aby drewnu nadać naturalny wygląd i je zakonserwować. Przykłady to oleje: tungowy, lniany, duński (mieszanka naturalnego oleju na przykład lnianego z lakierem i rozpuszczalnikiem). Są zwykle łatwe w aplikacji, nietoksyczne dla ludzi, przyjazne środowisku. Przykłady środków tworzących na powierzchni drewna trwałe powłoki to natomiast: szelak, lakiery będące mieszanką żywic i rozpuszczalników, wosk, bejca, farby. Ich nakładanie jest trudniejsze i mogą być toksyczne.
W produkcji na masową skalę większość etapów produkcji krzeseł automatyzuje się z wykorzystaniem maszyn specjalistycznych. Ponadto m.in. szlifowanie, powlekanie, a nawet ich montaż coraz chętniej są robotyzowane (patrz: ramki).
Case study: Kontrola jakości w produkcji mebli![]() W pewnej firmie produkującej meble wdrożono zautomatyzowany system kontroli jakości laminowania płyt wiórowych. Zadanie to realizowane w ciągu technologicznym przebiega następująco: najpierw maszyna do laminowania nakłada folie z klejem na obie strony drewnianych paneli, potem maszyna tnąca odcina nadmiar materiału na krawędziach do odpowiedniej długości. Wiele parametrów procesu wpływa na jakość wyrobu końcowego. Musi on być także elastyczny, ponieważ stosowane są różne laminaty, z kilkoma wzorami imitującymi różne typy drewna i w różnych kolorach. Wydajność linii laminowania przekracza kilka tysięcy sztuk na dzień. To uniemożliwia ręczną inspekcję jakości online. Po pierwsze pracownikowi trudno byłoby sprawdzać jednocześnie obie strony panelu. Po drugie szybkość, z którą przesuwa się taśma, rzędu kilkudziesięciu m/min, nie pozwoliłaby mu wykryć wszystkich wad. Ręczna inspekcja byłaby też niebezpieczna, ponieważ wymagałaby podejścia blisko ruchomych części maszyn. Dlatego zdecydowano się wdrożyć zautomatyzowany system kontroli jakości, który zintegrowano z ciągiem technologicznym laminowania i docinania. Jego kluczowe komponenty, kamery wysokiej rozdzielczości wraz z oświetleniem, zainstalowano w obudowach maszyn. Rozstaw kamer, dzięki wbudowanym serwosilnikom, można zmieniać. To jest konieczne, gdyż szerokość poddawanych inspekcji paneli jest zmienna. Uzupełnieniem części sprzętowej jest oprogramowanie do analizy rejestrowanych obrazów. System został zaprojektowany do detekcji i eliminacji: nadmiaru kleju, niepełnego laminowania i odklejania się folii, po obydwu stronach płyt. Od paneli uznanych za wybrakowane odcinane są części zidentyfikowane jako niespełniające wymogów. Potem takie płyty są oznaczane jako uszkodzone i ręcznie sortowane pod kątem ewentualnego dalszego wykorzystania. Kontrola jakości zatem zapobiega sprzedaży wybrakowanych elementów, a równocześnie zmniejsza ilość odpadów. |
Monika Jaworowska