Sztandarowym przykładem produktów szybko zbywalnych są słodycze i przekąski, jak batony, czekolady, czipsy, cukierki czy gumy do żucia. Jeśli chodzi o te ostatnie, to nie każdy wie, że produkuje się je z... tworzyw sztucznych. Są składnikiem bazy gumowej, nierozpuszczalnej substancji, która sprawia, że gumy można długo żuć bez znaczącej zmiany ich właściwości i jest nośnikiem dla substancji smakowych, ale sama jest niejadalna. Dlatego gum do żucia lepiej nie połykać. Podstawowe składniki bazy gumowej to: elastomery, żywice, środki zmiękczające i wypełniacze – stanowią mieszaninę składników naturalnych i syntetycznych, w zależności od receptury. Oprócz bazy, w składach gum do żucia można typowo znaleźć: substancje słodzące, zatrzymujące wilgoć, dodatki smakowe, koloryzujące oraz aromaty. Powleka się je rozpuszczającymi się w ślinie powłokami, które przedłużają ich trwałość. Ich produkcja jest zwykle całkowicie zautomatyzowana. Dalej przedstawiamy przykłady maszyn specjalistycznych wchodzących w skład ciągów technologicznych w fabrykach gum do żucia.
Jak się produkuje gumy do żucia?
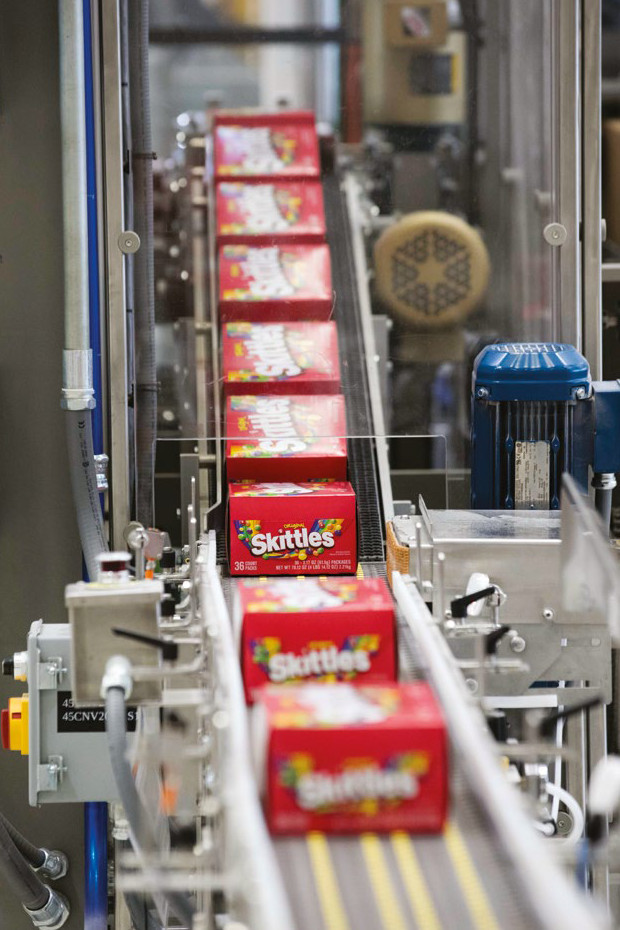
Proces produkcyjny gumy do żucia jest wciąż udoskonalany. Mimo to jego główne etapy pozostają takie same – rozpoczyna się od wymieszania składników, potem gotowej masie nadaje się kształt i się ją schładza. W tym celu bazę gumową najpierw topi się i przelewa do mieszalników lub ładuje się ją do nich w postaci elastycznych arkuszy. Tam łączy się z pozostałymi składnikami. Korzysta się z maszyn pracujących w trybie wsadowym lub ciągłym, jeżeli wymagana jest duża wydajność produkcji. Są to zwykle mieszalniki wolnoobrotowe wyposażone w specjalne podwójne mieszadła w kształcie litery Z, które obracając się w przeciwnych kierunkach i z różną prędkością, zapewniają dużą siłę ścinającą potrzebną do ugniatania wsadów o dużej lepkości. Typowo zbiornik mieszalnika jest podgrzewany – dzięki stapianiu składników w trakcie łączenia powstaje jednorodna mieszanka.
Kolejnym krokiem jest kształtowanie w wytłaczarkach. Maszyny te formują masę z mieszalnika na przykład w arkusze albo wałki, w zależności od docelowego kształtu gumy do żucia. Przeważnie korzysta się z dwóch wytłaczarek, wstępnej i głównej, z komorami o regulowanej temperaturze i głowicami podającymi masę dalej. Pierwsza jest konieczna, aby zapewnić równomierny dopływ surowca do drugiej. Nim zostanie tam doprowadzony, musi się skrystalizować.
Wytłaczarki i powlekarki w produkcji gum do żucia
By to umożliwić, między wytłaczarkami instaluje się przenośnik o regulowanej prędkości przesuwu. Jeżeli trzeba połączyć kilka wałków gumy o różnych smakach lub kolorach, korzysta się ze współwytłaczarek z wymiennym głowicami. Ciąg technologiczny na tym etapie uzupełnia się również o maszyny zmniejszające średnice wałków lub grubość arkuszy za pomocą rolek o regulowanym nacisku, formujące kulki oraz nacinające wałki i arkusze za pomocą ostrzy o regulowanym rozstawie, od którego zależy rozmiar kawałków. W kolejnym etapie wałki i paski chłodzi się w tunelu na wielopoziomowym przenośniku – dzięki temu tunel jest kompaktowy, a wsad pokonuje wystarczająco długą drogę, by zdążył ostygnąć. Kulki z kolei schładza się na wibrujących pasach z perforacją – dzięki drganiom nie deformują się. Wydajność chłodzenia w tunelu zależy od sposobu cyrkulacji powietrza, zaś kontrola temperatury punktu rosy zapobiega zawilgoceniu. Po schłodzeniu, gdy guma jest twarda i krucha, wałki i arkusze są dzielone na kawałki. Kolejnym etapem jest powlekanie. Środki glazurujące nanosi się w maszynach z obrotowym bębnem, w którym kawałki gumy są jednocześnie przewracane i spryskiwane. Na koniec, po wyschnięciu, są zawijane w papierki i po kilka opakowywane.