Produkcja wsadowa środków higieny osobistej
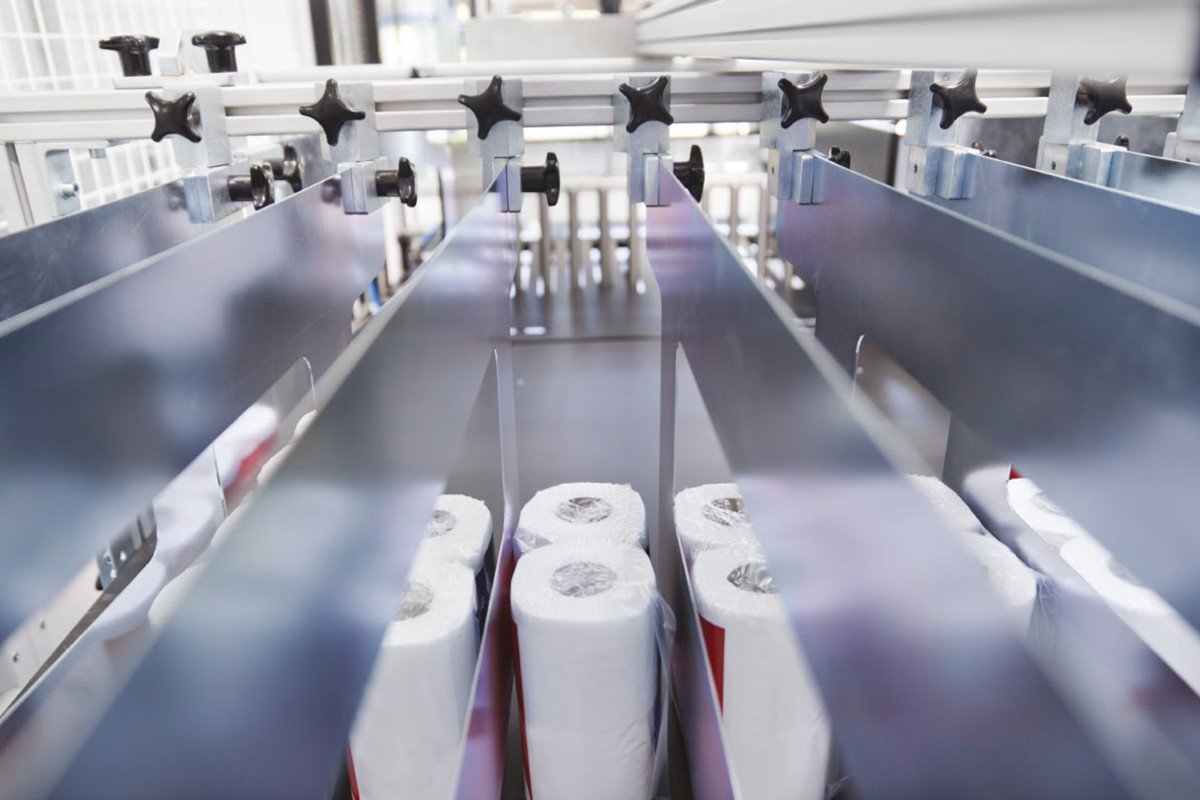
Nagromadzenie maszyn specjalistycznych stanowią także zautomatyzowane linie produkcyjne środków higieny osobistej, na przykład past do zębów. Typowo w ich składzie znaleźć można: wodę, humektanty (substancje o właściwościach hydrofilowych oraz higroskopijnych), środki powierzchniowo czynne, materiały ścierne, zagęszczacze, barwniki, aromaty, konserwanty. W zależności od typu pasty do zębów dodawane są środki bakteriobójcze, wybielacze oraz fluor. Zwykle produkowane są one w ramach procesu wsadowego w reaktorach składających się z kilku zbiorników.
W przykładowym wykonaniu główny z nich wyposażony jest w mieszadła przeciwbieżne, mieszadła kotwicowe z ostrzami oraz zgarniaczami, centralnie zamontowane mieszadło łopatkowe i mieszadło wbudowane w dno zapewniające jednorodność mieszanki. Częścią zestawu są również: zbiornik pomocniczy z mieszadłem łopatkowym do mieszania składników dodatkowych, progresywna pompa wnękowa do wyładunku produktu, pompa próżniowa oraz regulator temperatury. Surowce ładowane są przez system dozowania z kontrolą wagi. Komponenty reaktora są ze sobą połączone mechanicznie, elektrycznie i pneumatycznie na ramie nośnej.
Przykładowy proces produkcyjny rozpoczyna się od włączenia mieszadeł w zbiorniku głównym, w tym tego na dnie, i ustawienia ich startowych prędkości obrotowych, jeszcze przed załadowaniem składników. Następnie pompa próżniowa dozuje część płynnych surowców. Podczas ich łączenia mieszadła są sekwencyjnie włączane i wyłączane. Regulowana jest też prędkość ich obrotów. W kolejnym kroku ze zbiornika odpompowuje się powietrze, a regulator ciśnienia automatycznie utrzymuje je na stałym poziomie, zwykle kilku milibarów. Potem pompa próżniowa wlotem w dolnej części zbiornika dozuje składniki stałe. Są tłoczone wolno, by uniknąć uformowania się grudek. Zapewnia to także czas na ich zwilżenie i równomierne rozprowadzenie w mieszaninie.
Kiedy osiągnie ona wymaganą lepkość, mieszadło wbudowane w dno zostaje zatrzymane, a prędkość obrotów pozostałych jest zmniejszana do wartości startowej. Po czasie określonym w recepturze dozowane są pozostałe ciekłe składniki. Po ich zmieszaniu ciśnienie w zbiorniku jest stopniowo zwiększane i dodawane są aromaty, które krótko się miesza. Po zatrzymaniu mieszadeł pobrana zostaje próbka pasty do kontroli jakości. Gotowy produkt jest ze zbiornika odprowadzany przez pompę wnękową.
Radomir Ochocki
igus
Sektor FMCG charakteryzuje się wysokimi wolumenami produkcyjnymi i presją kosztową. Dlatego zawsze w tym obszarze spotykamy nacisk na maksymalizację czasu pracy maszyn, co implikuje minimalizację czasu przestojów. Dzięki naszym produktom z obszaru systemów doprowadzenia energii możemy osiągnąć dziesiątki milionów cykli bezawaryjnej pracy. Grupa łożysk dry-tech charakteryzuje się natomiast pracą bezobsługową, na sucho, bez konieczności stosowania smarów. Dodatkowo możemy wyliczyć trwałość łożysk, co pozwala na odpowiednie zaplanowanie przestojów w formule predykcyjnej. Maksymalizacja wydajności – tak bardzo potrzebna w sektorze FMCG – sprzyja stosowaniu nowinek technicznych. Takim obszarem jest Przemysł 4.0, który już pojawia się w naszych produktach. W ofercie mamy e-prowadniki kablowe oraz łożyska ślizgowe liniowe, które informują o swoim zużyciu.
Docieramy z naszą gamą produktową w Polsce do każdego segmentu przemysłu. Od jednoosobowych działalności gospodarczych, przez firmy integrujące rozwiązania, aż po finalnych klientów, liderów FMCG. Najważniejsze zagadnienia wpływające na rozwój w tym obszarze to: szybka dostępność produktów, fachowy dobór i doradztwo, a także chęć rozwiązywania problemów po stronie klienta. Od ponad roku rozwijamy naszą firmę jako najłatwiej dostępnego dostawcę w przemyśle – i to jest nasz główny kierunek zmian. Właśnie prostota uzyskiwania przez klientów nawet skomplikowanych rozwiązań technicznych jest dla nas kluczowym zadaniem na kolejne lata. |
Mycie w maszynach do produkcji antyperspirantów
W ramach produkcji wsadowej wytwarzane są też antyperspiranty. Zaliczane są one do tej samej kategorii kosmetyków co dezodoranty, ale działają inaczej. Te drugie jedynie maskują zapach za pomocą składnika alkoholowego, natomiast antyperspiranty zawierają środki, które zapobiegają poceniu się, zatykając pory skóry. Dostępne są w różnych postaciach, na przykład w sprayu lub w kulce. W drugim przypadku płynny środek jest przechowywany w opakowaniu zamkniętym okrągłym korkiem, który połową styka się z jego zawartością. Przesuwanie kulki po skórze aplikuje antyperspirant. Zazwyczaj w składzie takich kosmetyków można znaleźć: wodę demineralizowaną, zagęszczacze, humektanty, środki powierzchniowo czynne, sole glinu, które zapobiegają poceniu się, zapach, środek antybakteryjny i dodatki, jak regulatory pH. Składniki oraz ich proporcje mogą się różnić w zależności od producenta.
Antyperspiranty produkowane są w reaktorach podobnych do tych opisanych wcześniej. W ich przypadku pierwszy krok to rozpuszczenie zagęszczacza w gorącej wodzie w zbiorniku głównym i wymieszanie środków powierzchniowo czynnych w tym pomocniczym. Po oddzielnym przygotowaniu tych składników są one łączone w zbiorniku głównym. Wówczas dodawane i mieszane są sole glinu, a na zakończenie zapach oraz środek antybakteryjny.
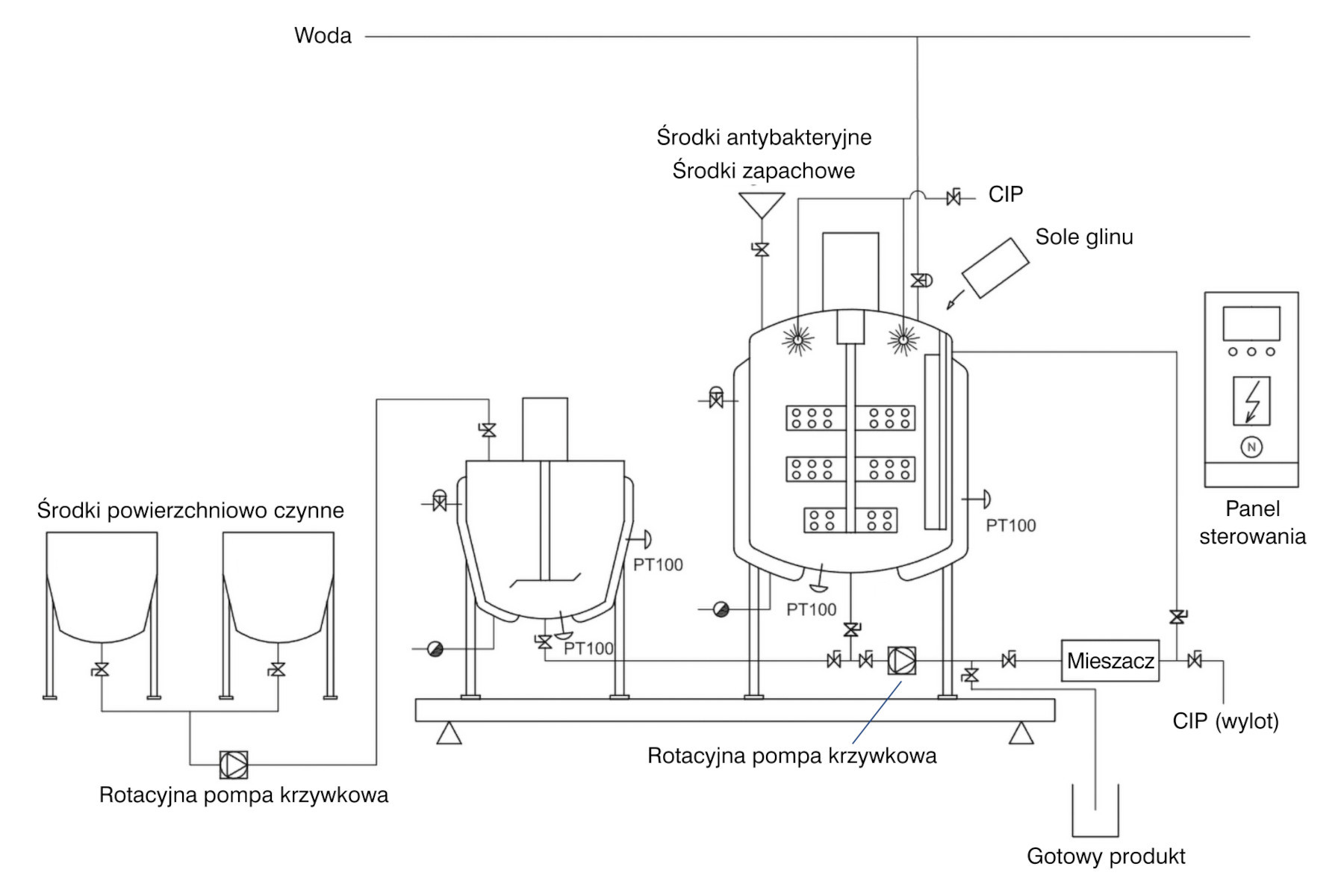
Ważnym aspektem użytkowym reaktorów do produkcji wsadowej jest ich mycie – jest konieczne, aby wydłużyć żywotność maszyny i zapewnić odpowiednią jakości produktu finalnego. Przykładowa procedura obejmuje wstępne płukanie wodą z detergentem przeciwpieniącym, właściwe mycie wodą z odpowiednim do typu zanieczyszczeń detergentem, a na koniec spłukanie czystą ciepłą wodą. Producenci reaktorów do procesów wsadowych w zakresie realizacji oferują różne opcje, w tym: automatyczne mycie na miejscu w systemie CIP (Cleaning In Place), ręczne mycie w systemie CIP oraz całkowicie ręczne mycie za pomocą na przykład myjki ciśnieniowej. Automatyczny system CIP nie wymaga demontażu urządzenia – jest to podejście najefektywniejsze i najszybsze. Ręczny system CIP wykorzystuje zbiornik z wodą lub wodą z detergentem oraz pompę do cyrkulacji tych środków w urządzeniu. Zbiornik należy napełniać lub opróżniać samodzielnie, zgodnie z cyklem czyszczenia.
Monika Jaworowska