Kable ognioodporne
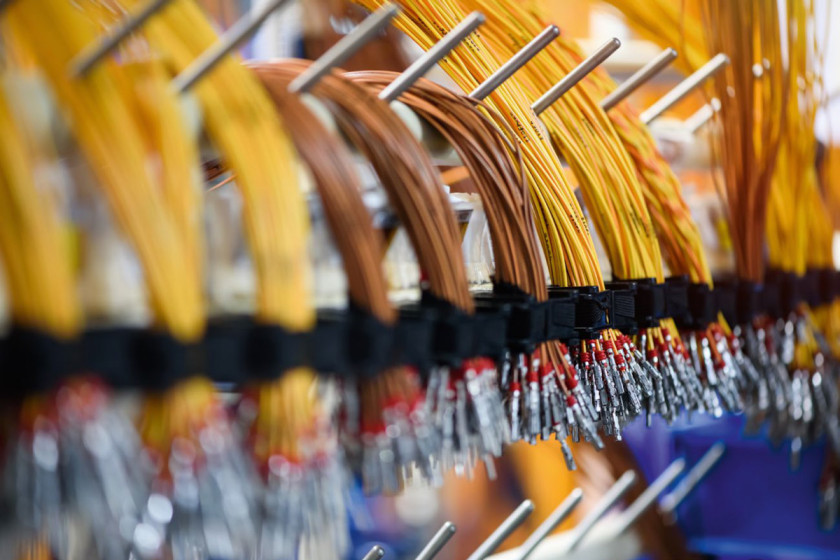
Specjalnej uwagi wymagają instalacje, w których występuje zagrożenie pożarem. Korzysta się w nich z kabli ognioodpornych, które w razie zapalenia się zachowują swoją funkcję, tzn. dostarczają zasilanie albo transmitują sygnał. Jest to zagwarantowane przez określony czas. Taką wytrzymałość zapewniają specjalne materiały, z których wykonywane są ich komponenty.
Temperatura topnienia przewodników w kablach ognioodpornych musi przekraczać +800°C. Ten wymóg dyskwalifikuje aluminium, którego temperatura topnienia nie przekracza +700°C. Spełnia go natomiast miedź, która topi się dopiero w temperaturze powyżej +1000°C. Ważne, by przewodnik w kablu ognioodpornym miał odpowiednią grubość – zaleca się, by pole powierzchni jego przekroju przekraczało 1 mm². Cieńsze przewody łatwo pękają z powodu lokalnego przegrzania. Ponadto ze względu na możliwość uszkodzenia taśmy mikowej w kablach ognioodpornych nie jest zalecane układanie żył sektorowo, czyli w kształt wycinka koła, ale tak, by uformowały koło. Jeżeli z kolei chodzi o same taśmy mikowe, w kablach tego typu powinno się wykorzystywać te wykonane z miki syntetycznej, która jest odporniejsza na wysokie temperatury niż naturalna z flogopitu. Popularnymi materiałami izolacyjnymi w kablach ognioodpornych są PE i XLPE.
W instalacjach, w których występuje zagrożenie pożarowe, trzeba korzystać z kabli wykonanych z tworzyw bez halogenów stosowanych, aby uzyskać określone właściwości tworzyw sztucznych. Do tych zaliczanych jest pięć pierwiastków: fluor, chlor, brom, jod oraz astat. Materiały je zawierające łatwo można rozpoznać, gdyż pierwiastki te są częścią ich nazwy. Przykłady to: polichlorek winylu, kauczuk chloroprenowy, propylen fluoroetylenowy i fluoropolimery. Tworzywa te podczas spalania się wydzielają trujące i korozyjne gazy, które w połączeniu z wodą tworzą żrące ciecze. Stanowi to zagrożenia dla mienia i zdrowia ludzi.
Przewody wysokotemperaturoweCase studyFirma używająca termopar do monitorowania wysokotemperaturowego procesu, na skutek wycofania się dotychczasowego dostawcy z rynku, straciła dotychczasowy dostęp do kabli do podłączania tych czujników do sterownika. Stosowane przewody wciąż można było rozpoznać po kolorze izolacji nawet przy pracy w temperaturach powyżej 600°C. Wypróbowane podczas testów kable z oferty innych producentów blakły już w temperaturze około 300°C. W efekcie rozpoznanie poszczególnych przewodów było trudne, a to wydłużało serwisowanie, powodowało błędy przy podłączaniu i w rezultacie przestoje. Aby temu zaradzić, zlecono zaprojektowanie niestandardowego okablowania. Jako materiał izolacji wybrano odporne na wysokie temperatury włókno szklane w kolorze białym, nadające się do impregnowania pigmentami. Te musiały mieć specjalny skład. Wymagany był również niestandardowy sposób ich aplikacji. Po zanurzeniu w nich włókna szklanego należało je poddać suszeniu etapami, zmieniając temperaturę. Utrwalone w ten sposób kolory nie blakły nawet w temperaturach powyżej 700°C. ![]() |