Przepusty kablowe
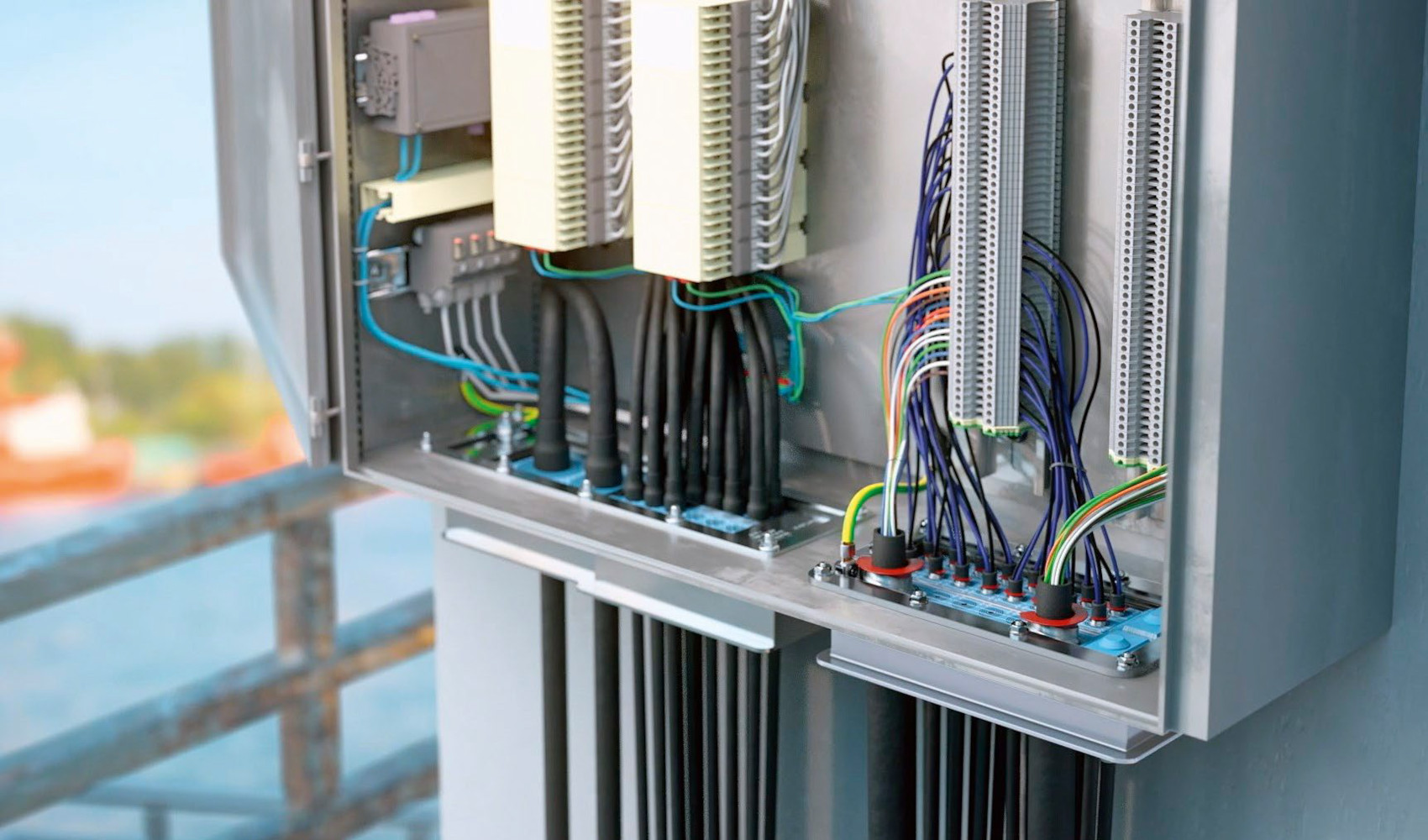
Złącza przemysłowe zbudowane są z następujących komponentów: dławnicy kablowej, obudowy wtyczki, wkładów męskiego i żeńskiego ze stykami oraz obudowy gniazda. Pierwsza pełni złożoną funkcję. Przede wszystkim dławnica kablowa pozwala na przeprowadzenie kabla przez otwory w obudowach maszyn lub innych urządzeń. Oprócz możliwości zamocowania zapewnia uszczelnienie wejścia kabla. Dzięki temu do urządzenia nie wnikają zanieczyszczenia, jak kurz, pyły, płyny, które mogłyby je uszkodzić. Dodatkowo chroni kabel przed skręcaniem się i nadmiernym zużyciem w wyniku częstego zginania, a jego końcówkę przed uszkodzeniem. Zabezpiecza go również przed przypadkowym wyciągnięciem albo wyrwaniem.
Główne komponenty dławnicy to: korpus, którym prowadzony jest kabel, uszczelki i mocowania (nakrętki). Korpus wykonuje się z materiałów odpornych na uszkodzenia mechaniczne i agresywne czynniki środowiskowe. Dostępne są dławnice z tworzyw sztucznych i metali. Pierwsze są tańsze i sprawdzają się w większości zastosowań. Przeważnie plastikowe korpusy dławnic wykonuje się z tworzyw sztucznych jak poliamid i nylon. Popularne metale w tym zastosowaniu to natomiast: stal nierdzewna, mosiądz niklowany galwanicznie, aluminium. Korpusy metalowe są trwalsze od tych z tworzyw sztucznych, ponieważ charakteryzuje je większa odporność na różnego rodzaju obciążenia mechaniczne, naprężenia oraz korozję.
Jak dobierać obejmy?Obejmy utrzymują grupy kabli razem. Są dostępne w postaci opasek lub owijek zaciskowych. Przy ich wyborze należy zwrócić uwagę na: materiał wykonania, wytrzymałość na rozciąganie, maksymalną średnicę obejmowanej wiązki kabli, długość i szerokość, zakres temperatur użytkowych. Popularne materiały to: aluminium, tkaniny, nylon, PTFE, PVC, stal nierdzewna. Materiał powinien być odporny na warunki środowiskowe. Musi być również kompatybilny z materiałem osłony kabli, by nie powodować jej korozji, nadmiernego zużycia ani uszkodzeń. Ważna jest też wytrzymałość obejmy na rozciąganie. Zależy ona od konstrukcji blokady oraz właściwości materiału. Maksymalna średnica opaski warunkuje to, czy będzie w stanie utrzymać wiązkę kabli. Ważne, by można było owijkę zapętlić i zablokować (nadmiar jej materiału powinien znajdować się za blokadą, aby zapobiec przeciągnięciu). Do obejmy można przymocować etykiety identyfikacyjne. |
Jak zamontować dławnicę?
Korpus składa się z części stykowej, która może mieć pierścienie uszczelniające, dzięki czemu nie są potrzebne dodatkowe uszczelki oraz części nagwintowanej. Dostępne są różne długości i rodzaje gwintów. Uszczelnienia wykonuje się z materiałów o różnych właściwościach, na przykład o dużej wytrzymałości na wysokie temperatury. Częścią dławnic są też nakrętki. Przykładem są te mocujące przewód, których dokręcenie powoduje zaciśnięcie się uszczelki i mechaniczne zamocowanie kabla w przepuście. Ich wewnętrzna strona może być ożebrowana. Ożebrowanie to zaczepia o skrzydełka na korpusie dławnicy. To zabezpiecza nakrętkę przed odkręceniem pod wpływem drgań. Poza tym skrzydełka dociskane nakrętką zaciskają na przewodzie gumową uszczelkę, co zwiększa stopień ochrony IP. Nakrętki słusłużą również do mocowania dławnicy w otworze niegwintowanym.
Przepusty kablowe montuje się w otworach gwintowanych albo przelotowych. Pierwsze podejście sprawdza się, jeżeli ściana obudowy wykonana jest z materiału grubszego, a zatem otwór w niej jest głębszy niż część nagwintowana dławnicy. Wlot ten musi być odpowiednio nagwintowany. Drugi sposób praktykuje się w przypadku, gdy ściana obudowy jest za cienka, by możliwe było wkręcenie dławnicy. Wówczas jest ona do niej przymocowywana za pomocą nakrętki.
Czasem trzeba zamontować dławnicę w otworze w obudowie za dużym lub zbyt małym w stosunku do jej rozmiarów. Ma to miejsce zazwyczaj w razie wymiany kabli na te o mniejszej albo większej średnicy w stosunku do tych wprowadzanych danym wlotem wcześniej. Wówczas korzysta się z adapterów, które wypełniają nadmiarową przestrzeń albo wpasowują się w tę ograniczoną, która jest dostępna. W obu przypadkach ich wewnętrzna średnica jest zgodna z rozmiarem dławnicy, którą wmontowuje się w adapter.
Jak dobierać korytka i prowadnice?Korytka są przeznaczone do zastosowań stacjonarnych. Kable nimi prowadzone są chronione przed zanieczyszczeniami lub wentylowane, w zależności od konstrukcji zamkniętej lub otwartej. Korytka pozwalają też separować różne typy kabli. Dostępne są w wykonaniu z różnych materiałów, m.in. stali nierdzewnej, aluminium, tworzywa sztucznego, włókna szklanego. Prowadnice przeznaczone są do zastosowań o dużej dynamice ruchu, jak roboty, obrabiarki i duże maszyny przemysłowe. Mogą wytrzymać ciężar dużej liczby kabli i ograniczają promień gięcia, a dzięki temu naprężenia z nim związane, zwykle ograniczając gięcie do jednej płaszczyzny. Chronią również okablowanie przed uszkodzeniem, zapobiegając jego splątaniu się, zgniataniu, zwisaniu, naciąganiu, zużyciu ściernemu i zaczepieniu o ruchome elementy maszyny. Kluczowe parametry przy wyborze prowadnicy to minimalny promień gięcia oraz wymiary. Jeżeli chodzi o pierwszy parametr, dla elektrycznych kabli zasilających i sygnałowych należy zastosować się do wskazówek producenta, przewodów pneumatycznych – trzeba dopilnować, by był on równy pięciokrotności ich średnicy, a w przypadku przewodów hydraulicznych zalecana wartość jest 7,5 razy większa niż ich średnica. Promień gięcia prowadnicy należy dobierać w odniesieniu do kabla / węża o największej średnicy, przyjmując zapas 10%, aby uwzględnić niespodziewane naprężenia. Margines bezpieczeństwa warto również uwzględnić, aby zapewnić luz między kablami wewnątrz prowadnicy. W tym celu należy ich średnice określić z zapasem 10% dla kabli elektrycznych, 15% dla przewodów pneumatycznych i 20% w przypadku tych hydraulicznych. Sumując ich wartości dla wszystkich kabli planowanych do umieszczenia w osłonie, uzyskuje się wymaganą szerokość wnęki prowadnicy. Jeśli chodzi o wysokość, to powinna ona wynieść tyle, ile średnica najgrubszego kabla powiększona o zapas odpowiedni dla jego typu. Ważny jest też wybór materiału wykonania. Dawniej prowadnice kablowe były wykonane głównie ze stali, a obecnie w większości zastosowań metalowe zostały zastąpione tymi z tworzyw sztucznych. ![]() |