Kompatybilność elektromagnetyczna złączy
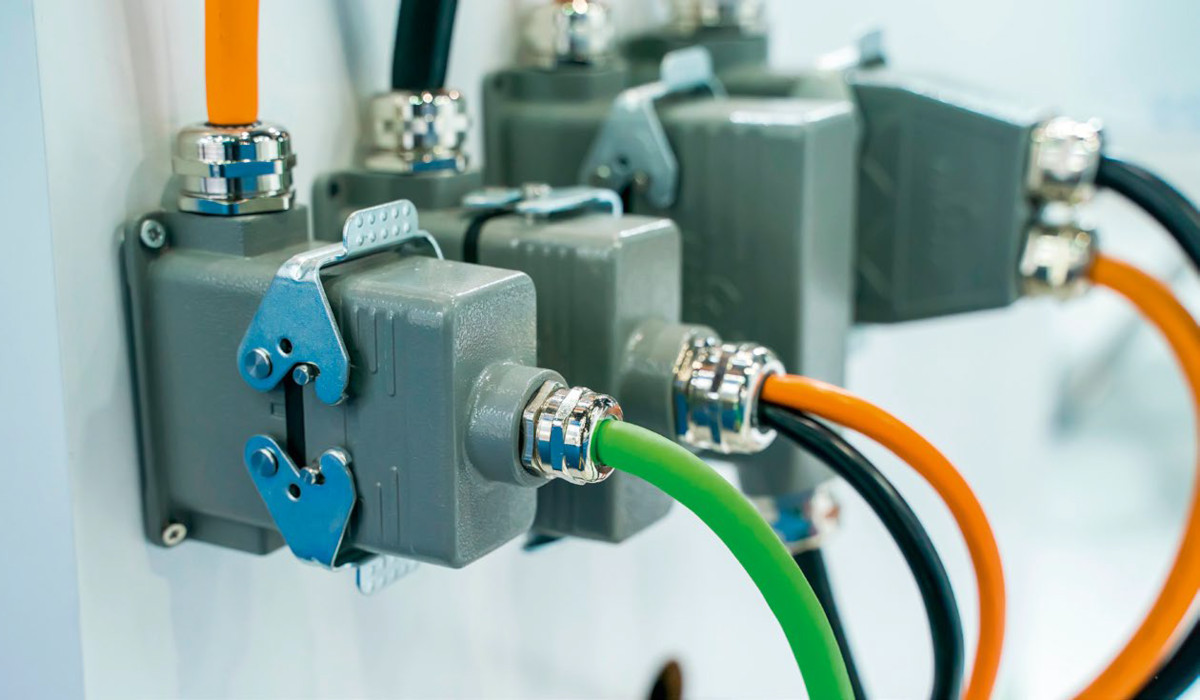
Złącza jako pasywne komponenty nie emitują zaburzeń elektromagnetycznych ani nie są wrażliwe na wpływ takich zaburzeń, które pochodzą ze źródeł zewnętrznych. Ponieważ jednak ich gniazda przerywają ciągłość obudowy (ekranu) mogą się okazać słabymi punktami, jeśli urządzenie, w które je wbudowano, nie zostało zaprojektowane z uwzględnieniem zasad EMC.
Poza tym źródłem zaburzeń elektromagnetycznych, wrażliwym również na te pochodzące ze źródeł zewnętrznych, są przewody prowadzone wewnątrz złączy. Ich kompatybilność elektromagnetyczna zależy od właściwości ekranujących obudowy wtyczki, obudowy gniazda, dławnicy kablowej, które warunkują stopień tłumienia zaburzeń w obu kierunkach.
Wpływ na właściwości ekranujące mają głównie: przewodność elektryczna materiału oraz grubość ekranu. Dlatego na przykład obudowy wykonywane są jako odlewy z metali. Ważna jest poza tym ciągłość połączeń między wymienionymi elementami złączy. Dlatego, by zwiększyć powierzchnię kontaktową na styku gniazda z wtykiem, m.in. wykonuje się je w taki sposób, żeby nachodziły na siebie. Korzysta się też z przewodzących uszczelnień. By ekranowanie było skuteczne, kompletując złącze, trzeba mieć pewność, że jego komponenty zapewnią zbliżony poziom tłumienia zaburzeń elektromagnetycznych.
Jak produkowane są złącza?Złącza stosowane zamiast połączeń stałych mają wiele zalet: usprawniają montaż i pozwalają na podłączanie i odłączanie sekcji sprzętu w celu konserwacji, naprawy, doraźnego użytkowania. Różnorodność typów złączy nie ułatwia jednak ich wyboru. W tym ostatnim pomocna jest znajomość funkcji poszczególnych elementów oraz materiałów i metod ich wykonania złączy. Główne komponenty złączy to obudowy i styki. Pierwsze chronią komponenty wewnątrz i wykonuje się je z tworzyw sztucznych albo metali. Z kolei styki są zazwyczaj miedziane, pokrywane cyną albo złotem w celu poprawy przewodności i trwałości połączenia. Niestety powłoki są podatne na korozję. W przypadku złota rozwija się ona, jeżeli jego warstwa jest za cienka, porowata, nieciągła. Wówczas pomiędzy metalem bazowym a środowiskowymi chemicznie agresywnymi czynnikami zachodzą reakcje, których produkty rozprzestrzeniają się (pełzają) po powierzchni powłoki z metalu szlachetnego. Zapobiega temu pokrycie styków niklem przed nałożeniem złota. Powłoki z cyny z kolei ulegają korozji ciernej na skutek tarcia spowodowanego mikroruchami styków w zamkniętym złączu pod wpływem wibracji. Zapobiega jej ich lepsze dopasowanie. Obudowy z tworzywa sztucznego są zazwyczaj formowane wtryskowo. W procesie tym wypełnia się formę stopionym plastikiem. Uzyskuje on w niej określony kształt, który utrwala się przez jego schłodzenie. Obudowy metalowe wykonuje się jako odlewy ciśnieniowe albo obrabia maszynowo z metalu bazowego. Ich powierzchnię wygładza się, a następnie powleka – na przykład kadmem albo niklem, w celu poprawy odporności na korozję i ścieranie. Na koniec poddaje się je kontroli jakości, aby wykryć nierównomiernie naniesione powłoki, pęknięcia, wżery, pęcherze. Wkładka z nieprzewodzącego materiału utrzymuje styki w określonym położeniu i separuje je od obudowy. W obudowach z metalu jest to oddzielny komponent, niezbędny, by zapobiec problemom elektrycznym. W tych z tworzyw sztucznych jest wykonywana jako integralna część obudowy w procesie jej formowania wtryskowego. Kontrola jakości wkładek pozwala wykryć takie wady jak: nadmierne naprężenia wewnętrzne, nierównomierna grubość, odkształcenia i zatkane gniazda. Styki z kolei są tłoczone lub obrabiane maszynowo z metalu bazowego. Montaż to ostatni etap produkcji złącza elektrycznego. Oprócz kontroli jakości komponentów składowych poddaje się jej też gotowe złącza. ![]() |
Złącza hermetyczne
Jeżeli złącza będą użytkowane w warunkach, w których czynniki środowiskowe mogą przenikać do wnętrza obudowy, by do tego nie dopuścić, korzysta się z modeli z uszczelnieniem. W tym zakresie można wybrać, w zależności od konkretnych wymagań, złącza wodoodporne i pyłoszczelne albo hermetyczne.
Wodoodporność i pyłoszczelność zapewniają uszczelnienia z tworzyw sztucznych. Ich skuteczność charakteryzuje dwucyfrowy stopień ochrony IP. Pierwsza cyfra w jego zapisie, z przedziału od 0 do 6, opisuje pyłoszczelność, zaś druga, z zakresu od 0 do 9, charakteryzuje wodoszczelność przy różnym nasileniu oddziaływania wody, od pojedynczych kropel, przez polewanie strugą, aż po zanurzenie. Na przykład stopień ochrony IP67 w porównaniu z IP68 oznacza, że choć złącza są pyłoszczelne, pierwsze jest odporne na krótkotrwałe zanurzenie w wodzie, a drugie pozostanie szczelne nawet przy ciągłym zanurzeniu.
W złączach hermetycznych z kolei izolację kontaktów wykonuje się ze szkła, ceramiki albo żywicy. Są one zaprojektowane tak, aby wytrzymywały wysokie ciśnienie. Gazoszczelność wymagana jest zwykle w zastosowaniach specjalnych, na przykład w wojsku, lotnictwie i zadaniach realizowanych na dużych głębokościach, na przykład w eksploracji dna morskiego.
Dużą popularnością cieszy się zwłaszcza pierwszy z wymienionych materiałów. Wśród zalet złączy hermetycznych z uszczelnieniem ze szkła wymienić należy: trwałość, wytrzymałość mechaniczną i wysoką temperaturę pracy. Proces uzyskiwania gazoszczelności polega na topieniu szkła w piecu do czasu, aż wypełni ono przestrzeń między kontaktami i obudową wkładki, a pomiędzy szkłem i metalem wytworzą się trwałe wiązania. Wtedy temperatura jest obniżana, aż do czasu schłodzenia wkładów. Aby zapewnić szeroki zakres temperatur pracy, szkło i metal muszą charakteryzować się podobnymi współczynnikami rozszerzalności cieplnej. Zapobiega to powstawaniu niekontrolowanych naprężeń i przesunięć komponentów wkładki przy zmianach temperatury.
Technika obtrysku
Złącza i przewody wykonywane metodą obtrysku (overmolding) stanowią jedną część. Formuje się je wtryskowo. W tym celu zespół elementów umieszcza się w formie, którą zalewa się stopionym tworzywem sztucznym. Po ostygnięciu plastik zastyga, przyjmując kształt formy wokół połączenia pomiędzy złączem a przewodem, które jest szczelne, a zarazem elastyczne. Kluczowy jest wybór materiału obtrysku. Wymagana jest kompatybilność między nim a tworzywem osłony kabla. W tym zastosowaniu popularnych jest kilka materiałów.
PVC jest trwały, odporny na warunki atmosferyczne, chemikalia, rozciąganie, ścieranie. Sztywnieje w niskich temperaturach. Polipropylen to tworzywo tanie, uniwersalne, elastyczne, wytrzymałe na rozciąganie, kwasy i zasady. Z drugiej strony nie jest odporne na promieniowanie UV ani wysokie temperatury. W niskich staje się kruche. ABS jest tani, nie kurczy się, ale jest mało odporny na czynniki pogodowe oraz rozpuszczalniki. Paląc się, silnie dymi. Termoplastyczny poliuretan TPU wyróżnia odporność na ścieranie, elastyczność, niskie temperatury, oleje, smary i rozpuszczalniki. Jest droższy. Kauczuk termoplastyczny TPR jest odporny na czynniki atmosferyczne, elastyczny, ale łatwo ulega odkształceniom. Politereftalan butylenu PBT jest odporny na oleje, rozpuszczalniki, wysokie temperatury.
Obtrysk ma liczne zalety. Chroni kabel i złącze przed ingerencją z zewnątrz, zużyciem, wpływem czynników z otoczenia i wibracjami. Ułatwia montaż i odłączanie. W ten sposób zabezpiecza się kable i złącza narażone na ekstremalne warunki pogodowe, mycie pod wysokim ciśnieniem, częstą dezynfekcję, naprężanie, zginanie.