Część 1: Pojazdy AGV
Wózki AGV (Automated Guided Vehicles) to bezzałogowe, samojezdne pojazdy wyposażone w napęd elektryczny i zasilane z akumulatorów. W oparciu o nie tworzy się zautomatyzowane systemy transportowe do przewozu ładunków w obrębie zakładów przemysłowych, magazynów i między nimi. Ich ładowność wynosi typowo od kilku kilogramów do kilkuset ton.
W przeciwieństwie do robotów współpracujących czy dronów nie są one nowym wynalazkiem. Pojazdy tego typu są użytkowane już od lat 50. zeszłego wieku. Pierwsze z nich w 1954 roku holowały przyczepy w magazynach spożywczych, zaś w latach 70. w swoich fabrykach zaczęła z nich korzystać firma Volvo. Służyły tam one za ruchome platformy montażowe.
Dzięki rozwojowi techniki AGV są jednak sukcesywnie ulepszane. W rezultacie, chociaż są uważane za proste urządzenia, których funkcjonalność ogranicza się do transportu i ewentualnie załadunku / rozładunku towarów, w ostatnich latach w przemyśle i logistyce wciąż zyskują na popularności.
AGV - TYPY I ZASTOSOWANIA
Ze względu na sposób transportu wózki samojezdne dzieli się na kilka grup. Jednym z nich jest holowanie.
Pojazdy holownicze mogą jednocześnie ciągnąć wiele przyczep, co jest efektywniejszym rozwiązaniem od przewozu ładunku każdej z nich oddzielnym wózkiem. Najlepiej ten rodzaj pojazdów AGV sprawdza się w transporcie na większych odległościach, na przykład na zewnątrz, pomiędzy budynkami i w rozległych magazynach, długimi korytarzami, dużych ilości towarów. Ich ładowność sięga przeważnie kilkudziesięciu ton.
Kolejnym typem pojazdów samojezdnych są wózki pojedynczego załadunku. Ich charakterystyczną cechą jest kompaktowa konstrukcja, mają one bowiem postać platformy, na której umieszcza się ładunek. Najlepiej sprawdzają się w transporcie dużych ilości towarów - ich ładowność sięga przeważnie kilkudziesięciu ton, na krótkich i średnich odległościach. Pojazdy pojedynczego załadunku są zwrotniejsze niż wózki holownicze. Dzięki temu łatwiej manewrują w wąskich przestrzeniach.
Dostępne są też samojezdne wózki widłowe o ładowności zazwyczaj kilku ton. Do transportu drobniejszych ładunków wykorzystuje się natomiast pojazdy AGV o małych rozmiarach oraz udźwigu, za to zwrotne i szybkie. Ich przykładowe zastosowania to: przewóz podzespołów pomiędzy stanowiskami montażu oraz rozdział paczek w centrum logistycznym.
PRZEGLĄD METOD NAWIGACJI AGV
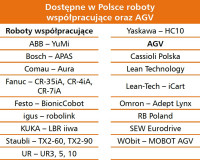
Dostępne w Polsce roboty współpracujące oraz AGV
W zakresie sterowania ruchem pojazdów AGV można wyodrębnić kilka głównych zadań. Jednym z nich jest nawigacja, dzięki której wózki podążają z góry wyznaczoną trasą, zoptymalizowaną pod kątem jak najefektywniejszego przepływu ładunków.
Wyróżnić można wiele sposobów nawigacji. Przykładowe z nich to metody: pętli indukcyjnej, pętli magnetycznej, optyczna, laserowa, ultradźwiękowa i w oparciu o system GPS.
W pierwszej z nich pod podłogą umieszcza się kabel. Na skutek przepływu prądu elektrycznego dookoła przewodu wytwarzane jest pole magnetyczne. Wózek wyposażony jest z kolei w układ odbiorczy, mierzący jego natężenie. Sterownik koryguje kierunek, w jakim pojazd się porusza, tak aby wartość ta była jak największa.
Metoda nawigacji z wykorzystaniem pętli indukcyjnej ma wiele zalet. Najważniejsze z nich to: duża niezawodność i duża dokładność kierowania pojazdem, odporność na czynniki zewnętrzne, takie jak na przykład zabrudzenia, a w przypadku kiedy pojazd porusza się na zewnątrz budynku, na śnieg czy lód i stosunkowo niski koszt. To ostatnie nie dotyczy niestety sytuacji, w której trzeba zmienić trasę. Ponieważ kable są wbudowane w podłoże, ich usunięcie jest drogie i pracochłonne. Ponadto obecność metalu w podłożu może zakłócić pomiar natężenia pola.
JAKIE SĄ ZALETY METODY PĘTLI MAGNETYCZNEJ?
W podłogę wbudowuje się również znaczniki, aktywne, które emitują sygnał odbierany przez antenę w wózku albo pasywne, które antena zasila, kiedy pojazd znajduje się nad znacznikiem. Układa się je w rzędy lub w ścieżkę. Zalety i wady tego sposobu nawigacji są analogiczne do metody pętli indukcyjnej.
Z kolei w metodzie pętli magnetycznej wykorzystuje się namagnesowaną taśmę, którą nakleja się na podłodze. Jej zaletą jest prosta i niedroga instalacja, a co najważniejsze przebieg trasy można zmodyfikować łatwo i tanio. Niestety, taśma magnetyczna nie jest trwała. Nietrudno także o jej uszkodzenie.
Ścieżkę, po której powinien poruszać się wózek, można także namalować. W tym celu używa się farb refleksyjnych lub maluje linie w kontrastowym kolorze, tzn. ciemne na jasnym podłożu lub jasne na ciemnym. Ich przebieg śledzi kamera zamontowana w pojeździe. Zaletą tej metody jest łatwość modyfikacji trasy, natomiast wadami łatwość zabrudzenia i starcia farby, przez co przy intensywnym użytkowaniu wymagane jest częste czyszczenie ścieżek, a z czasem też ponowne nałożenie farby.
NAWIGACJA LASEROWA
W dotychczas opisanych metodach pojazd podąża trasą wzdłuż ścieżki naniesionej na podłoże. I chociaż nadal można spotkać zautomatyzowane systemy transportu działające w oparciu o zasadę pętli indukcyjnej, w nowszych wózkach AGV częściej korzysta się z innych sposobów.
Jednym z nich jest nawigacja z wykorzystaniem skanera laserowego. Urządzenie to montuje się na dachu kabiny wózka. Skanuje ono pomieszczenie, wykrywając znaczniki zamocowane na ścianach. Do zalet tej metody zalicza się dokładność pozycjonowania oraz łatwość zmodyfikowania trasy. Znaczniki muszą być jednak umieszczone na tej samej wysokości i cały czas znajdować się w zasięgu skanera. Obecnie jest to jedna z popularniejszych metod nawigacji pojazdów AVG.
Na podobnej zasadzie, ale bez konieczności mocowania na ścianach znaczników, odbywa się nawigacja z wykorzystaniem sonarów. Następny sposób wymaga z kolei zapisania w pamięci sterownika wózka referencyjnych obrazów pomieszczenia, z którymi później porównywane są te rejestrowane w trakcie jazdy.
Zaletą nawigacji w oparciu o dane z systemu GPS jest natomiast łatwość wdrożenia. Niestety można z niej korzystać tylko na zewnątrz budynków.
ZARZĄDZANIE RUCHEM
Podążając trasą wytyczoną przez przewód w podłodze, pojazd AGV napotyka często na punkty, w których rozdziela się ona na dwie ścieżki biegnące w różnych kierunkach albo punkty, w których zbiega się kilka tras. Miejsca te są znakowane, na przykład przez zakopanie w nich metalowych znaczników, natomiast poszczególne ścieżki rozróżnia się na podstawie wartości częstotliwości prądu zasilającego podziemny przewód.
Po dotarciu do punktu, w którym trasa się rozdziela, właśnie na podstawie częstotliwości sterownik pojazdu wybiera właściwe rozgałęzienie. W przypadku innych metod nawigacji decyzja ta jest podejmowana na podstawie rozkładu jazdy zapisanego w pamięci sterownika.
W zautomatyzowanych systemach transportowych, w których jednocześnie przemieszcza się wiele wózków AGV, wymagane jest zarządzanie ich ruchem. W przeciwnym wypadku będzie dochodzić do kolizji. Można to zrealizować centralnie.
Wtedy to główny system zbiera informacje o położeniu poszczególnych wózków i pilnuje tego, by jednocześnie w jednej strefie nie przebywał więcej niż jeden pojazd. W przypadku decentralizacji pojazdy komunikują się bezpośrednio między sobą. Jeżeli jeden z nich wjeżdża do danej strefy, od razu informację o tym wysyła do innych, które zatrzymują się na jej obrzeżach do czasu uzyskania potwierdzenia, że jest pusta.
AGV w kopalni
Jednym z nich jest flota składająca się obecnie z prawie 70 autonomicznych, bezzałogowych pojazdów transportowych (Autonomous Haulage System). Wyposażono je w liczne czujniki (m.in. radarowe i laserowe). Dane przez nie mierzone są wykorzystywane przez system sztucznej inteligencji, dzięki któremu pojazdy uczą się topografii terenu kopalni. Trasy wywrotek, śledzone dzięki zamontowaniu w nich odbiorników GPS, są też poddawane analizie w centrum sterowania. Pozwala to koordynować ich przemieszczanie się i optymalizować przyszłe ścieżki i parametry ruchu (prędkość). Ponadto ciężarówki wyposażono w autonomiczny system detekcji kolizji. Na podstawie danych z licznych czujników, jeżeli na drodze pojawi się przeszkoda, automatycznie modyfikuje on zadaną trasę pojazdu. Sensory monitorują również stan wywrotki, m.in. ciśnienie w oponach, temperaturę płynów chłodzących, ich ciśnienie, poziom oraz stopień czystości, temperaturę i poziom wibracji łożysk, temperaturę oraz ciśnienie w układzie hamulcowym. Dzięki temu, zamiast angażować personel do wykonywania okresowych przeglądów floty, można przewidywać problemy eksploatacyjne i na bieżąco na nie reagować. W planach firma Rio Tinto ma również realizację autonomicznego systemu sterowania urządzeniami wiertniczymi (Autonomous Drilling Systems) i autonomicznego systemu transportu urobku linią kolejową (AutoHaul). Kopalnie w regionie Pilbara są nadzorowane zdalnie z centrali w Perth. |