Pod koniec października 2016 roku zainaugurowana została działalność zakładu Volkswagen Poznań we Wrześni, w którym produkowana jest nowa generacja samochodów Volkswagen Crafter. Jest w nim wytwarzanych blisko 60 wariantów tych pojazdów, docelową wydajność wynoszącą sto tysięcy aut rocznie.
Dla APA wywiadu udzielili: |
|
![]() |
![]() |
- Jakie były powody budowy nowego zakładu produkcyjnego? Jak generalnie wygląda struktura produkcyjna firmy Volkswagen Samochody Użytkowe w Polsce?
Ulrich Krick: Volkswagen AG to 15 znanych marek pojazdów, w tym takie jak VW, Audi, Seat, Škoda Auto, ale też Bentley, Bugatti oraz Lamborghini, a od 2009 roku również Porsche. Koncern ma też udziały w firmach produkujących samochody użytkowe i ciężarowe, takie jak Scania, MAN i, co najważniejsze ze względu na miejsce, w którym się znajdujemy - Volkswagen Nutzfahrzeuge. Ta ostatnia specjalizuje się w produkcji pojazdów dostawczych i ciężarowych.
W poprzednich latach firma Volkswagen Samochody Użytkowe miała w Europie dwa zakłady produkcyjne - w Hanowerze oraz w Poznaniu, gdzie produkowane są samochody Volkswagen Caddy oraz Transporter. Jeżeli chodzi o model Crafter, to do 2016 roku powstawał on we współpracy z Daimlerem na bazie Mercedesa Sprintera. Umowa w zakresie produkcji joint-venture zakończyła się w zeszłym roku, stąd też konieczna była budowa nowego zakładu.
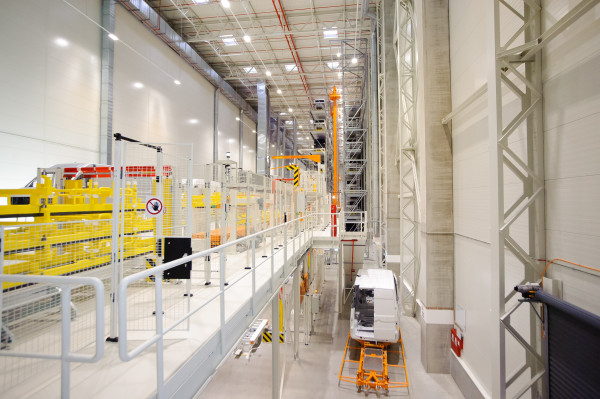
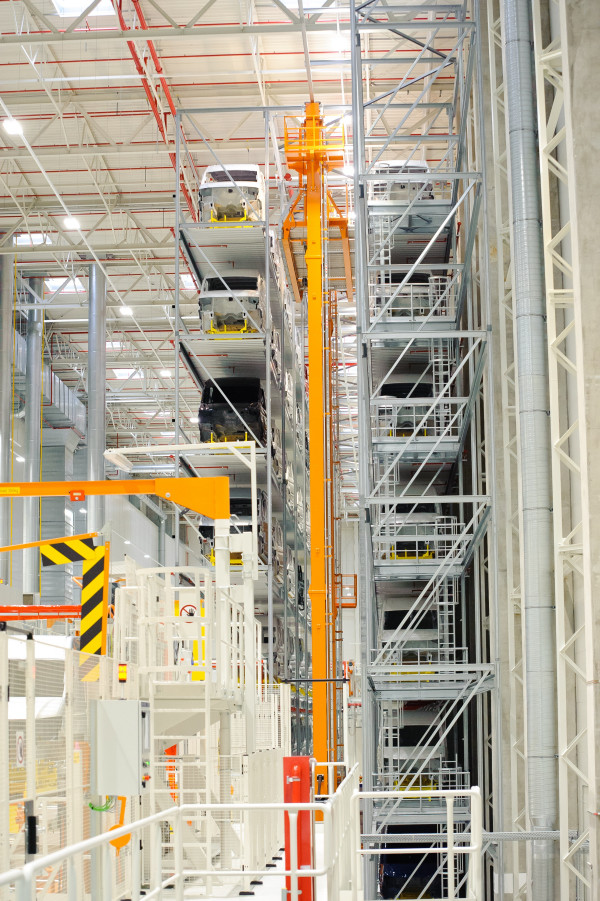
Głównymi rynkami zbytu dla pojazdów Volkswagen Crafter są m.in. Europa Centralna oraz Turcja. Z uwagi na nasze dobre doświadczenia związane z produkcją w Polsce decyzja o wyborze lokalizacji nowego zakładu produkcyjnego została podjęta bardzo szybko. Rozważaliśmy przy tym różne miejsca - od Krakowa do Stargardu Gdańskiego. Na Wrześnię, a dokładnie Białężyce, postawiliśmy ze względu na bliskość Poznania, gdzie firma ma już kilka zakładów produkcyjnych, w tym w szczególności Volkswagen Poznań w Antoninku. Poznań to także dostępność wykwalifikowanej kadry pracowniczej. Planujemy zatrudniać docelowo około 3 tys. osób, w tym kilkuset specjalistów i menadżerów.
- Jak wyglądał proces projektowy oraz budowa samej fabryki?
Ulrich Krick: Korzystamy ze standaryzowanego procesu budowy zakładów produkcyjnych - tzw. FEP, w ramach którego około 30 miesięcy przed rozpoczęciem produkcji samochodu rozpoczynana jest budowa fabryki. W przypadku Wrześni budowa ruszyła w październiku 2014 roku, zaś seryjną produkcję Craftera rozpoczęliśmy 23 miesiące później. Jest to absolutny rekord na poziomie globalnym.
Osiągnięcie bardzo krótkiego czasu budowy i uruchomienia zakładu jest tym bardziej znaczące, że wytwarzanych jest tutaj wiele wersji samochodów. Volkswagen Crafter to trzy różne długości i trzy wysokości pojazdu, wykonania z oknami i bez nich, z drzwiami przesuwnymi po różnych stronach, wersje otwarte i zamknięte, a także pojazdy z kabinami jedno- i dwurzędowymi.
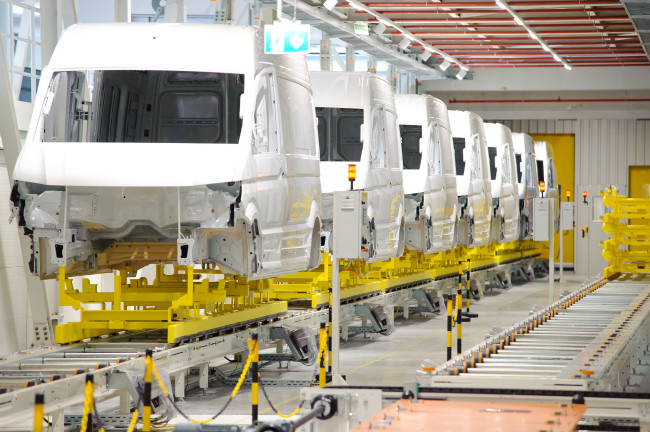
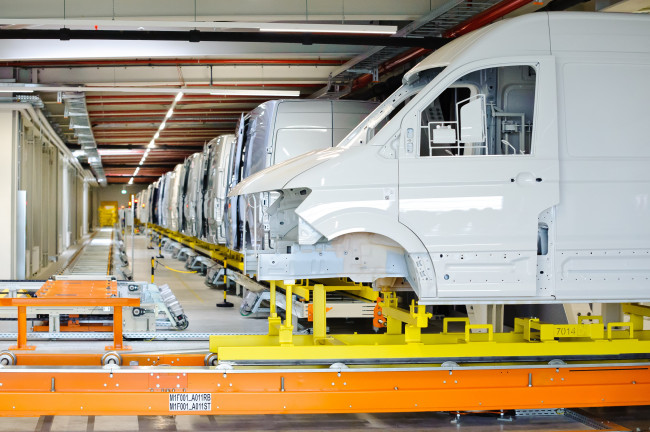
Daje to ponad 50 rodzajów samochodów, do tego dochodzą jeszcze różne elementy wyposażenia, przeniesienia napędu, skrzyni biegów, itd. Wszystko to stanowiło duże wyzwanie podczas projektowania procesów produkcyjnych, bowiem konieczne było zapewnienie wytwarzania każdego z samochodów na jednej linii produkcyjnej.
Warto dodać, że wytwarzane samochody są - w porównaniu z autami osobowymi, gabarytowo bardzo duże. Stworzyło to zupełnie nowe wyzwania pod względem malowania, transportu i montażu. Obecnie wdrażamy produkcję dwuzmianową, rozpocznie się produkcja na trzy zmiany. Wartość całej inwestycji w fabrykę Volkswagen Crafter wyniosła około 800 mln euro.
- Jaka była w budowie zakładu rola firmy Siemens?
Mirosław Salwach: Jesteśmy jednym z głównych dostawców technologii produkcyjnych do fabryki samochodów użytkowych Volkswagen Poznań we Wrześni. W zakładzie systemy Siemensa odpowiadają za przemieszczanie części i pojazdów składanych na liniach produkcyjnych, przy czym stworzona tu została kompleksowa linia transportowa obejmująca części naziemne oraz transport podwieszany - od momentu wyjścia z lakierni, aż do opuszczenia fabryki przez pojazdy na własnych kołach.
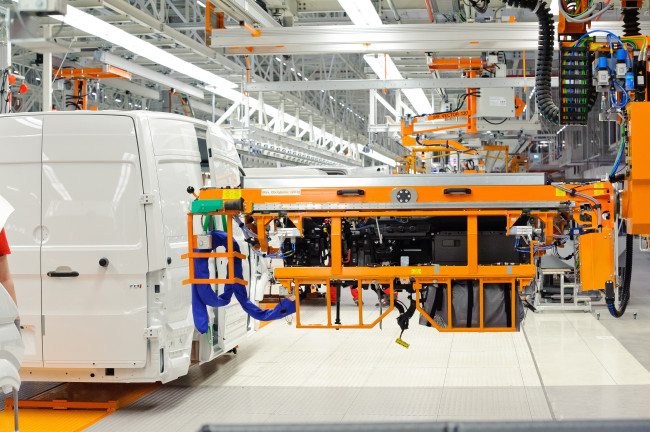
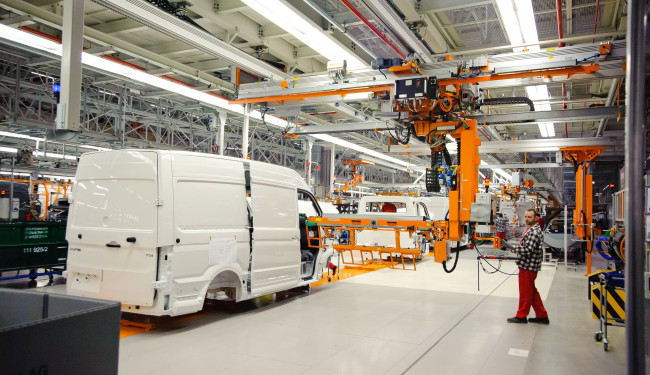
Opracowane przez Siemensa i zastosowane w fabryce systemy obejmują m.in. całą gamę sterowników przemysłowych, ich oprogramowanie oraz rozwiązania komunikacyjne odpowiedzialne za sterowanie i zbieranie informacji z czujników oraz przekazywanie ich do centralnego systemu zarządzającego produkcją.
Z inwestycją jestem osobiście związany od 2015 roku, przy czym firma Volkswagen przekazała nam niejako samą halę składającą się m.in. z podłogi, słupów oraz konstrukcji dachu, zaś całą resztę wykonaliśmy sami. Dotyczyło to zarówno konstrukcji stalowych, montażu przewodów, jak też wyposażenia technologicznego. To ostatnie obejmuje zarówno urządzenia Siemensa, jak też innych firm, które zostały zintegrowane w obrębie linii montażowej.
Zakład produkcyjny w liczbach
Dodatkowe informacje o zakładzie produkcyjnym:
|
- Jaki jest przebieg procesu montażowego?
Ulrich Krick: Jeżeli mówimy o początku procesu montażu, to jego początkiem jest przejęcie pojazdu z lakierni. Jest to de facto sama karoseria pojazdu, która została wytworzona w hali budowy karoserii, a następnie przeszła procesy malowania w lakierni. Poprzez magazyn wysokiego składowania i zespół przenośników trafia ona do hali montażu, gdzie transport samochodów odbywa się na poziomie 5-6 metrów, natomiast sam montaż - na poziomie zerowym.
Proces produkcji samochodów został podzielony na etapy na taśmie montażowej, czyli tzw. takty - każdy o długości 8,5 metra. W każdym z nich wykonywane są określone procesy montażowe w przemieszczających się pojazdach. Czas jednego taktu liczy 110 sekund, a cała linia montażowa obejmuje 120 takich taktów.
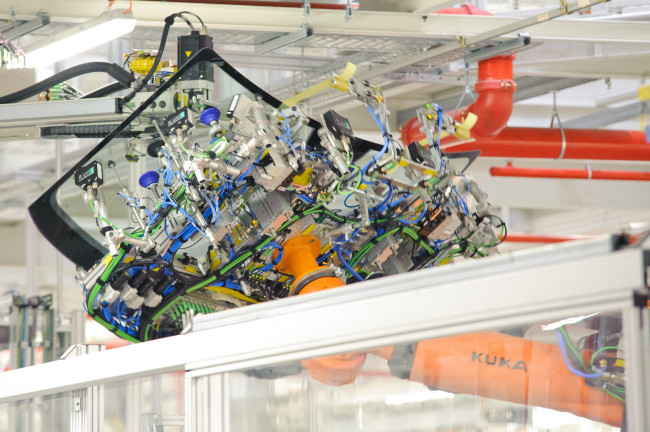
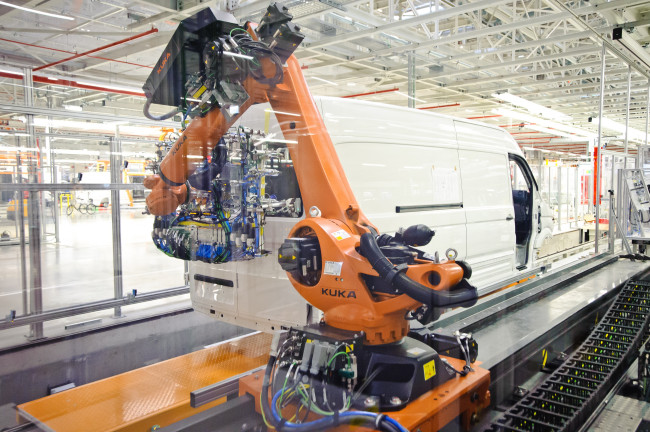
Przykładowo na początku linii w pierwszym takcie demontowane są m.in. drzwi, które trafiają na tzw. linię podmontażu. Tam następuje ich wyposażenie w niezbędne elementy i trafiają one ponownie do pojazdu na końcu całego procesu - oczywiście każde do pierwotnego auta. Na kolejnych etapach montowany jest kokpit wraz z wiązką elektryczną, drzwi przesuwne, szyby, wyposażenie wnętrza i inne elementy. W tym procesie dodatkowo występuje coś, czego nie ma w przypadku aut osobowych - samochód jest obracany o 90°, tak aby jego podłogę tylną, która waży około 60 kg, mógł zamontować robot.
Do powyższego momentu transport odbywa się naziemnie, gdzie samochód stoi na czterech szpilkach, następnie następuje przeładunek na transport podwieszany i dalszy montaż - m.in. elementów zawieszenia i systemu ogrzewania. Ważnym etapem w produkcji jest tzw. Hochzeit, czyli wesele, gdzie łączone jest nadwozie z podwoziem. Później następuje jeszcze zabudowa frontu, montaż siedzeń, kół oraz różne testy. Na końcu auto zjeżdża z linii na własnych kołach poprzez tunel świetlny i jest sprawdzane.
- Jak jest zbudowana wykorzystywana w obszarze montażu linia transportowa?
Mirosław Salwach: Część transportu naziemnego składa się z wózków transportowych oraz taśm opartych na przenośnikach łańcuchowych. W pierwszym z przypadków są to 64 wózki transportowe SKID tworzące linię o długości 1600 metrów, które przemieszczają samochody podczas ich montażu. W drugim mamy do czynienia z dwiema liniami transportu taśmowego wyposażonymi w przenośniki łańcuchowe z tworzywa sztucznego. W fabryce działa jeszcze trzecia taśma transportowa w obszarze tzw. Finish Line - jest to dwutorowy przenośnik płytowy, na którym poruszają się pojazdy z zamontowanymi kołami.
W zakładzie zastosowane są dodatkowe 25-metrowe przenośniki transportowe dla pracowników. Są to swego rodzaju ruchome chodniki, które poruszają się równolegle, w tempie przemieszczającego się samochodu. Zapewnia to lepszą ergonomię pracy oraz efektywność pracowników podczas montażu.
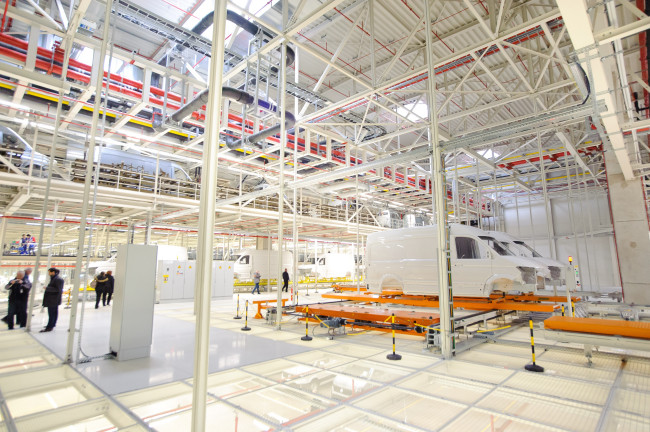
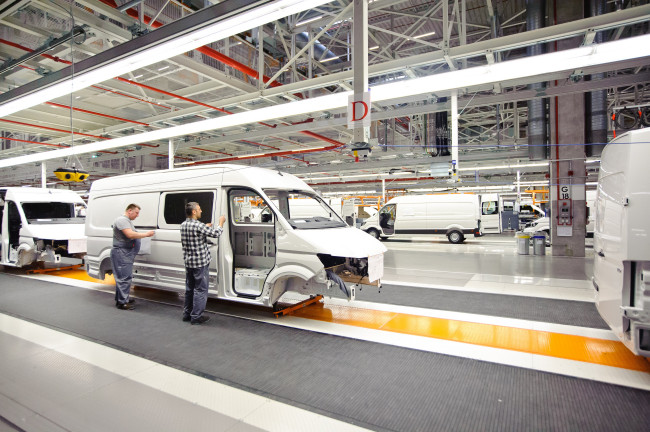
Inną formą transportu jest ten podwieszany. Pierwsza z linii transportu podwieszanego EHB o długości 1250 metrów składa się z 94 zawieszek produkcyjnych, które umożliwiają przemieszczanie karoserii w pionie i poziomie z zadanymi prędkościami. Cała linia została przymocowana do zbudowanej w tym celu specjalnej stalowej instalacji, która jest z kolei podczepiona do konstrukcji dachu.
Do tego wykorzystane zostały jeszcze dwie dodatkowe linie podwieszane - składająca się ze 190 zawieszek przeznaczonych do transportu drzwi oraz zbudowana z 25 zawieszek, która służy do przemieszczania kokpitów samochodowych. Stanowią one "podlinie", na których wyposaża się drzwi i kokpit, a następnie montuje te ostatnie w samochodach. Dodatkowo na potrzeby montażu drzwi przesuwnych zostało również zainstalowane 12 specjalnych zawieszek.
- Co wyróżnia omawianą instalację?
Mirosław Salwach: Z pewnością nowoczesność oraz zastosowanie unikalnych rozwiązań, a także dostosowanie całości do potrzeb firmy Volkswagen. Linia była "szyta na miarę", co wynikało z rodzaju i wielkości produkowanego auta. Dodatkowo nowy Volkswagen Crafter był zaprojektowany całkowicie od podstaw, stąd też systemy produkcyjne musiały być wykonane poniekąd również od podstaw. Udało się to zrobić nie tylko dobrze, ale też bardzo szybko.
Linia transportowa to zestaw kilkuset połączonych ze sobą urządzeń, w pełni skomunikowanych, co pozwala zachować kontrolę, diagnostykę i możliwość natychmiastowej reakcji na potrzeby produkcyjne. Całość funkcjonuje w trybie automatycznym zgodnie z zadanymi parametrami, zapewniając wysoką efektywność produkcji.
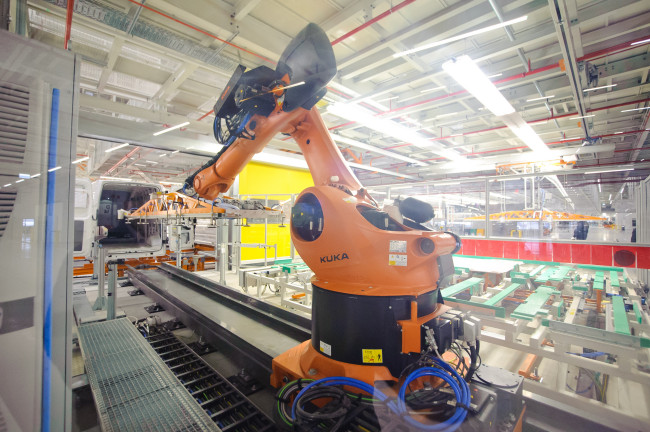
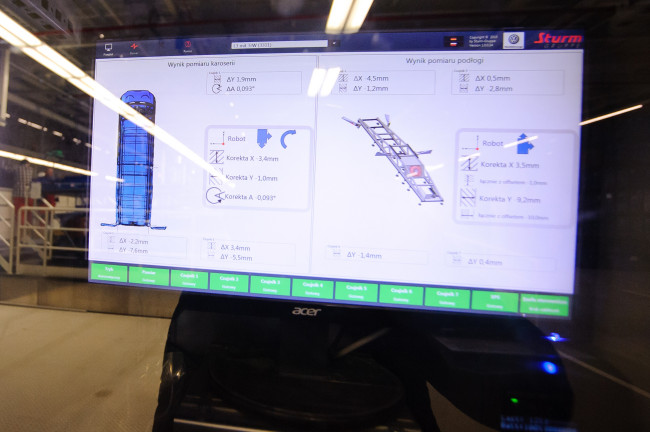
Ulrich Krick: Warto zwrócić uwagę na nowości nie tylko w hali montażu, ale też w lakierni. Pojazdów generalnie nie można malować etapami, gdyż wysychająca farba tworzyłaby nierówności - trzeba to robić za jednym przejściem robota malującego. Auto takie jak Crafter ma powierzchnię wielokrotnie większą, niż popularne samochody osobowe, a jednocześnie nie można dowolnie zwiększać liczby robotów malujących. Stąd też było dla nas dużym wyzwaniem, aby zapewnić jednolite malowanie w ciągu około trzech minut, bo w tym czasie malowany jest nowy Crafter.
Mówiąc o malowaniu, wskazałbym tutaj również na takie innowacje, jak zastosowanie nowego procesu wstępnego czyszczenia i przygotowania karoserii, a także różnych rozwiązań proekologicznych. Tradycyjnie w lakierniach stosuje się system wodny zbierający tzw. overspray, co powoduje powstawanie dużych ilości ścieków. W naszym zakładzie wykorzystywane jest rozwiązanie bazujące na mączce mineralnej, dzięki któremu powstaje o wiele mniej produktów ubocznych.
Linia transportowaPodstawowe informacje
Transport naziemny
|
- Jakie były inne kluczowe zagadnienia techniczne do rozwiązania?
Redakcja: Zgodnie z komentarzami przedstawicieli firm, do najtrudniejszych zadań w zakresie automatyzacji było przejście z transportu naziemnego na wiszący. Ponieważ tworzona linia miała być w pełni zautomatyzowana, jak najprostsza w obsłudze i utrzymaniu ruchu, zdecydowano się na wygrodzenie miejsc zmiany sposobu transportu osłonami - po to, aby zapobiec możliwości przebywania pracowników w tych obszarach. To ostatnie jest istotne również ze względu na kwestie uzyskiwania odbiorów Urzędu Dozoru Technicznego. W przypadku zastosowanego rozwiązania odbiory takie przechodzić muszą jedynie stosowane zawieszki, przy czym tak zaprojektowano linię, aby odbywało się to poza procesem produkcyjnym. Dzięki temu nie ma potrzeby planowania przerw produkcyjnych na czas corocznych wizyt przedstawicieli UDT.
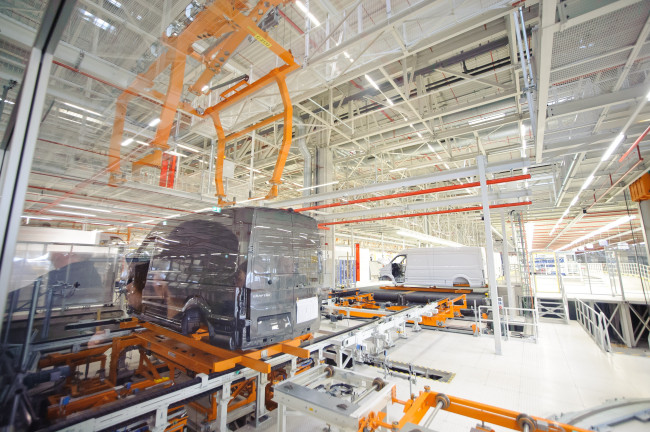
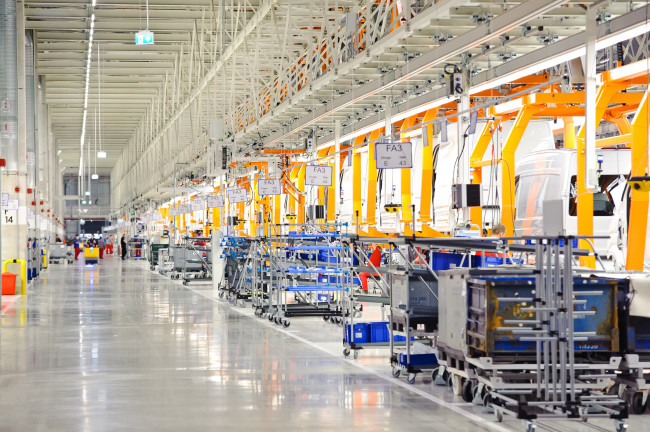
Mirosław Salwach: Proces montażu pojazdów użytkowych różni się znacząco od produkcji samochodów osobowych ze względu na liczbę możliwych wariantów i rozmiarów auta. Dotyczy to zwłaszcza obszaru tylnej części pojazdu, bardziej złożonej w przypadku samochodów ciężarowych. Stąd też, odpowiadając na wymagania przedstawione przez fabrykę Volkswagena w Poznaniu, dostosowaliśmy działanie linii produkcyjnej tak, aby uczynić tę część procesów technologicznie łatwiejszą. Pojazd jest obracany podczas przemieszczania go na linii montażowej, co pozwala na łatwiejszy montaż elementów znajdujących się w tyle samochodu - w szczególności ciężkiej podłogi.
Warto również zwrócić uwagę na to, że na różnych etapach produkcji pracownicy realizują działania, posługując się szeregiem nowoczesnych narzędzi - np. służących do podnoszenia, dokręcania czy manipulowania częściami. Zostały one tak opracowane, aby zapewnić maksymalną ergonomię pracy, a także zachowanie wysokiej jakości produktów. Pracownicy nadzorują także pracę robotów odpowiedzialnych m.in. za montaż szyb.
Na wykonanie każdego z etapów montażu przewidziany jest czas, który nie powinien być przekroczony. Jednocześnie tempo prac przy każdym ze stanowisk jest zsynchronizowane z przesuwaniem się transportowanych elementów.
- Czy samochody produkowane są na zamówienie?
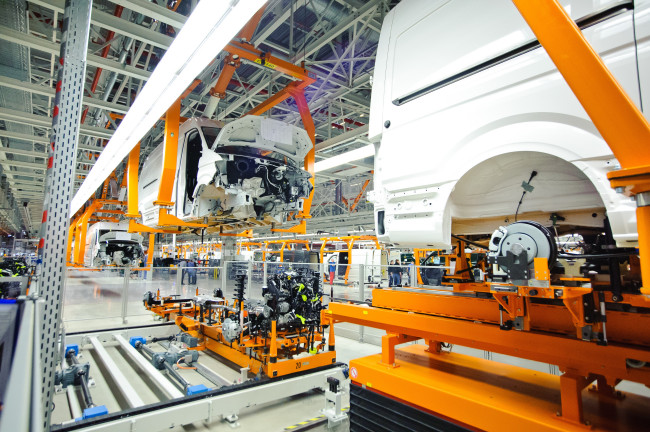
Redakcja: Samochody są w większości produkowane pod konkretne zamówienie, w tym występują w wielu wykonaniach specjalnych - np. na potrzeby klientów flotowych. Całością produkcji zarządzają systemy informatyczne, natomiast do pojazdów dołączane są plansze z zakodowanymi informacjami, które dotyczą sposobu ich zabudowy.
Zawierają one dane dla pracowników w zakresie montowanych podzespołów i wersji wykonania. Tych ostatnich może być bardzo dużo nie tylko ze względu na różne wielkości i wersje pojazdów, ale też ich wyposażenie - np. umiejscowienie kierownicy, rodzaje systemów nawigacyjnych, klimatyzacji czy świateł.
- Jak wyglądają kwestie logistyczne oraz regulacja prędkości pracy linii produkcyjnej?
Redakcja: Podpoznański zakład, podobnie jak inne tego typu firmy, korzysta z dostaw just-in-time, czyli "dokładnie na czas". Jest to metoda zarządzania mająca na celu redukcję pracy w toku oraz poziomu zapasów w procesach produkcyjno-magazynowych. W fabryce Volkswagen Poznań procesy logistyczne są tak zorganizowane, aby dostarczać części dopiero w momencie, gdy są one niezbędne, jednocześnie gwarantując odpowiednią kolejność ich trafiania na linię produkcyjną. Rozplanowanie ma również wymiar przestrzenny - materiały i komponenty trafiają do zakładu z trzech kierunków, zaś w czwartym - na południe - wyjeżdżają gotowe pojazdy.
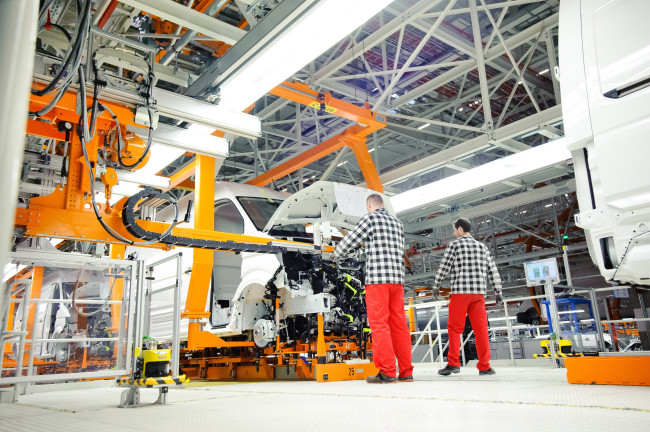
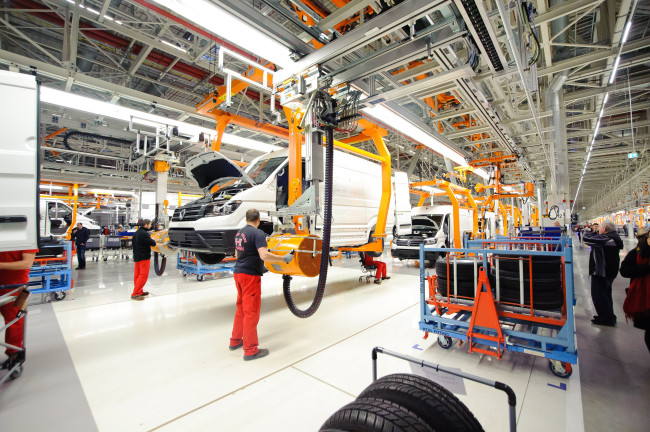
Firma współpracuje z kilkudziesięcioma dostawcami w Polsce, wśród kooperantów są m.in. producenci modułów czołowych, siedzeń i innych elementów. Silniki stosowane w Crafterze produkowane są w fabryce Volkswagena, zaś przed ich instalacją w samochodzie na linii produkcyjnej montowane są do nich rury, kable i układ przeniesienia napędu.
Pojazdy budowane są w określonej kolejności, co powiązane jest z dostawami logistycznymi oraz procesami sterowania pracą linii produkcyjnych. Tempo produkcji jest tak regulowane, aby była ona jak najbardziej płynna. Firma stworzyła bufor pomiędzy lakiernią a obszarem montażu końcowego, który obejmuje kilkupiętrowy magazyn wysokiego składowania. Zapewnia on nie tylko odpowiedni czas na dostawy poszczególnych elementów, ale przede wszystkim pozwala płynnie sterować prędkością produkcji samochodów. Z kolei na górnym poziomie hali jest miejsce transportowe tworzące bufor na wypadek, gdy w obszarze montażu występują opóźnienia.
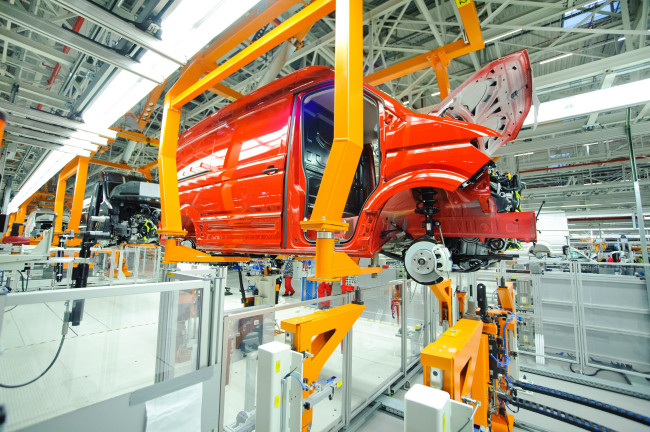
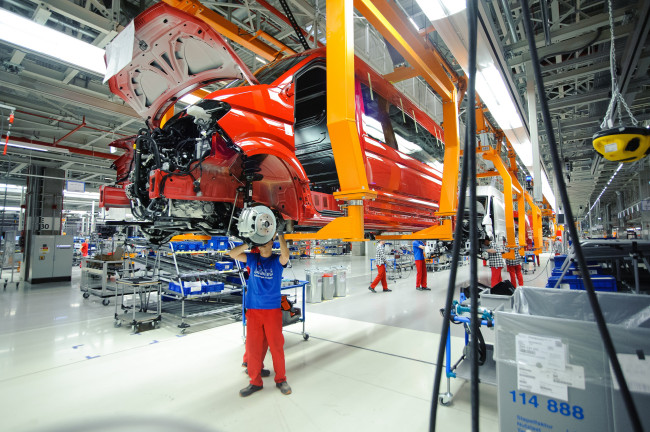
Kolejność produkcji samochodów jest tak dobierana, aby niejako przeplatać między sobą produkcję aut bardziej wyposażonych i wymagających większej liczby operacji montażu z tymi mniej wyposażonymi. Zapewnia to równoważenie pików produkcyjnych i "stabilizację" całego procesu. Zresztą naczelną zasadą działania każdej fabryki samochodów, jak przyznają rozmówcy, jest to, aby zagwarantować produkcję w jednym równym tempie. Wtedy można optymalizować procesy i dostawy, zwiększać efektywność i jakość wytwarzania.
- Dziękujemy za rozmowę.