Rittal to największa z firm należących do koncernu przemysłowego Friedhelm Loh Group. Została ona założona w 1961 roku i zatrudnia obecnie 9300 osób, koncentrując się na produkcji obudów i szaf przemysłowych, systemów dystrybucji zasilania, urządzeń do kontroli temperatury w środowisku przemysłowym oraz elementów infrastruktury IT.
Główna jej siedziba mieści się w Herborn (Niemcy), firma ma też 13 fabryk, z czego najstarsza zlokalizowana jest w Rittershausen - mieście, od którego pochodzi nazwa przedsiębiorstwa. W tym roku rozpoczęto produkcję w nowym zakładzie w Haiger, co ma pozwolić na wstrzymanie produkcji w Herborn i przeznaczenie części fabrycznej tej placówki na opracowywanie innowacji i zadania serwisowe. W Haiger mieści się też siedziba Friedhelm Loh Group, której łączne przychody w 2018 roku wyniosły 2,6 mld euro.
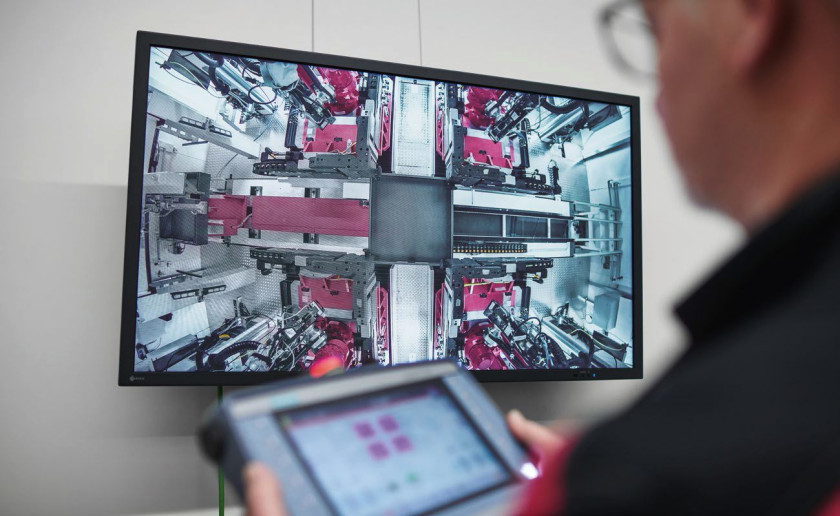
MASZYNY 4.0
Rittal zaprojektował nową fabrykę z technologicznym rozmachem, stawiając na wykorzystanie nowoczesnych rozwiązań na każdym etapie produkcji. Nowa fabryka zajmuje powierzchnię 24 tys. m², zainstalowano w niej 60 robotów, zaś liczba dużych, nowoczesnych maszyn przekracza sto sztuk. Wśród nich jest też 20 pojazdów autonomicznych, które służą do transportu materiałów, półproduktów i gotowych wrobów po terenie zakładu.
W zakładzie wytwarzane są obudowy przemysłowe niedużych rozmiarów: od 150×150×80 mm do około 1000×1400×400 mm. Docelowo ma być produkowane 150 różnych podstawowych rodzajów obudów (w Herborn było to 60 rodzajów), przy zużyciu 25 tys. ton metrycznych stali rocznie. Przekłada się to na 9000 obudów na dzień, nad których wytworzeniem będzie czuwać 300 osób. Statystycznie z fabryki w Haiger nowa obudowa będzie wyjeżdżać co 9,6 sekundy.
Projektując nowy zakład, wzięto pod uwagę praktycznie wszystkie aktualnie istotne trendy. Naturalnie zadbano o wysoką efektywność produkcji, a przy tym sprawną logistykę i komunikację. To, co można było zautomatyzować, zostało zautomatyzowane. Widać to już teraz, gdy fabryka jest w etapie rozruchu i na jej terenie jest po prostu mało ludzi. Ich praca koncentruje się na obsłudze maszyn, a więc kontroli poprzez komputery, choć są też pojedyncze czynności mechaniczne, które nie zostały zautomatyzowane.
Największe wrażenie robi autonomiczny system transportu. Po hali poruszają się płaskie roboty (AGV) - zautomatyzowane wózki, które czekają w gotowości, aby dowieźć potrzebne materiały lub produkty tam, gdzie są akurat potrzebne. Wiele z tych czynności odbywa się bez jakiegokolwiek udziału człowieka.
Jeśli pakiet półproduktów jest gotowy i należy go dostarczyć do odległego miejsca fabryki, sygnał trafia do systemu monitorującego ruch robotów i najbliższa z maszyn podjeżdża, następuje otwarcie osłon strefy załadunku, a następnie AGV samodzielnie pobiera półprodukty, po czym przewozi je do strefy załadunku kolejnej maszyny i tam pozostawia.
Pojazdy te poruszają się pomiędzy ludźmi, dostosowując swój ruch do otaczających je warunków. Taki system pozwolił uniknąć tworzenia bardzo długich, złożonych taśmociągów. Umożliwił też swobodne zaprojektowanie linii produkcyjnych, optymalizując ich ułożenie. A włożono w to wiele starań, bo cała fabryka została zamodelowana w komputerze i przez 3000 godzin symulowano jej działanie, poszukując optymalnej konfiguracji.
Półprodukty, które nie są w danej chwili potrzebne, trafiają do zautomatyzowanego magazynu. Tam również dostarczane są przez maszynę, z której towary odbiera robot będący połączeniem wózka widłowego i windy - jest to po prostu ogromny robot kartezjański.
Palety z materiałami i półproduktami mają unikalne kody kreskowe, dzięki czemu można je z łatwością rozpoznać w sposób automatyczny i zapamiętywać, gdzie znajdują się poszczególne elementy. Całość jest magazynowana na regałach wysokiego składowania, do których człowiek w ogóle nie ma dostępu.
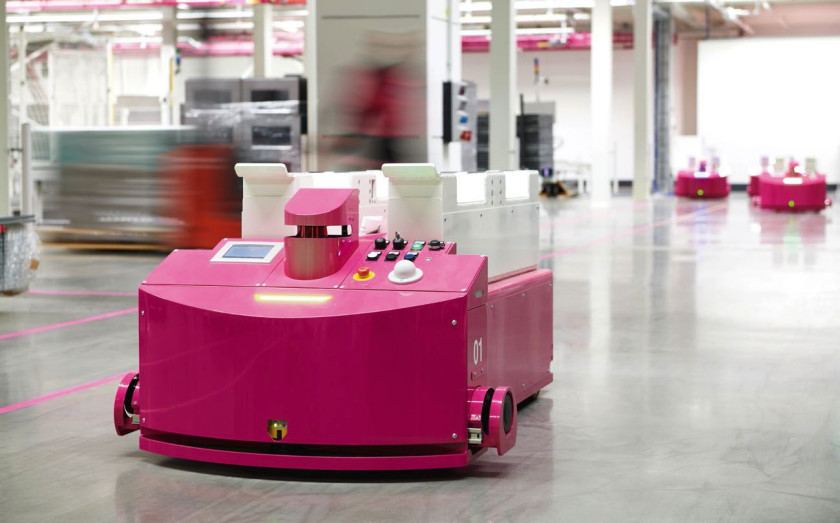
PRODUKCJA 4.0
Praca w nowym zakładzie w Haiger będzie odbywać się na trzy zmiany. Jej sposób organizacji to podręcznikowy przykład wdrożenia idei Przemysłu 4.0 od początku do końca. Działanie wszystkich maszyn jest planowane centralnie - każdego dnia na nowo. W trakcie zmiany nocnej analizowane są zamówienia i za pomocą symulacji układa się optymalny plan produkcji.
Trwa to cztery godziny, w trakcie których decyduje się o kolejności wykonywania poszczególnych elementów obudów, rozmieszczeniu wytłoczeń na blachach oraz całej związanej z tym logistyce. Ponieważ zastosowano wiele maszyn, które wycinają elementy laserowo, oraz użyto też robotów, czas potrzebny na przezbrajanie końcówek wykonawczych został w większości przypadków całkowicie wyeliminowany. Wystarczy jedynie pobrać kolejny projekt do pamięci, aby wyciąć czy zespawać nowy wzór.
Ułożony, indywidualny plan działania uwzględnia czasy przejazdów autonomicznych pojazdów pomiędzy maszynami, minimalizację operacji składowania półproduktów w magazynie oraz harmonogram transportu gotowych wyrobów. Symulacje, które decydują o tym, w jaki sposób danego dnia fabryka będzie operować, bazują na dotychczasowych wynikach, a więc system z każdym dniem uczy się dodatkowych zależności i optymalizuje swoje działanie, co ma pozwolić mu docelowo osiągnąć założoną wydajność.
Nauka ta bazuje nie tylko na ogólnych danych, takich jak liczba wyprodukowanych obudów lub energia zużyta danego dnia, ale uwzględnia też wszystkie, nawet najbardziej szczegółowe informacje związane z produkcją. Jest to możliwe dzięki całkowitej integracji systemów - od poziomu pojedynczych sterowników PLC, aż do systemów MES i ERP.
Osoba mająca odpowiednie uprawnienia jest w stanie w czasie rzeczywistym podglądać nie tylko dane zbiorcze z linii produkcyjnej, ale i odczyty z pojedynczych sensorów. Każdego dnia łącznie generowane będzie ponad 11 TB takich danych. A wszystko to zgodnie z ideami lean manufacturing.
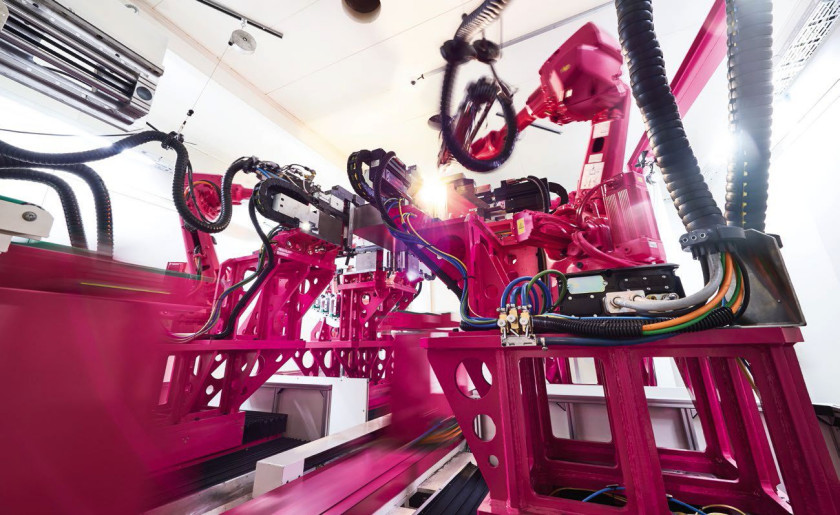
OFERTA 4.0
Koncepcje związane z Przemysłem 4.0 zostały w Rittalu wdrożone nie tylko w odniesieniu do działania maszyn w firmie, ale też poprzez zmodernizowanie oferty i wychodzą one daleko poza to, co dzieje się w samej fabryce. Wraz z uruchomieniem nowego zakładu produkcyjnego Rittal rozbudowuje swoją ofertę - nie tylko o nowe modele obudów, ale też zmienia się ich serwis oraz gwarantowany czas dostawy.
Po pierwsze, dzięki zoptymalizowanej linii produkcyjnej i logistyce, firma zapewnia 24-godzin oczekiwania na wybraną obudowę. Naturalnie dotyczy to klientów z Niemiec, ale i w odniesieniu do firm z innych państw Europy gwarantowane jest 48 godzin na dostawę od momentu złożenia zamówienia - i trwają prace nad skróceniem tego czasu.
Oferowane produkty, choć są standardowymi obudowami z katalogu, mogą zawierać liczne opcje (akcesoria, wycięcia), również dobierane z pozycji katalogowych. W efekcie klient zamawia produkt kosztujący tyle co standardowy, ale dostosowany do specyficznych potrzeb jego aplikacji.
To jednak nie wszystko, bo oprócz samego produktu Rittal oferuje też kompletną dokumentację, wliczając w to modele 3D dokładnie reprezentujące zamówiony produkt. Można je wykorzystać m.in. w oprogramowaniu ePLAN, za pomocą którego można przeprowadzić różnego rodzaju symulacje. Modele te uwzględniają wszelkie zamówione opcje i wprowadzone zmiany. Dostęp do nich odbywa się poprzez kod QR naklejony na każdym gotowym produkcie.
Użyte kody graficzne mają też dodatkowe znaczenie. Oznaczane są nimi komponenty i gotowe produkty pod koniec produkcji, a więc już po pomalowaniu obudów. Wtedy też każdy produkt zaczyna istnieć jako indywidualny element w systemie komputerowym Rittala. Jest to moment, w którym przestaje być jednym z materiałów lub półproduktów, umieszczonych na palecie z konkretnym kodem graficznym (używane są kody Data Matrix), ale jest indywidualnym wyrobem.
To właśnie dzięki tym kodom użytkownik może pobrać dokumentację produktu. Inżynierowie Rittala zauważyli, że ich klienci często potrzebują informacji na temat parametrów danej obudowy, będąc już w terenie, podczas prowadzenia prac instalacyjnych. Dlatego też możliwość szybkiego pobrania odpowiednich plików dla danej obudowy, nawet już po jej instalacji, jest tak cenna.
Co ważne - w kodzie naklejonym na gotowy produkt "zaszyty" jest także numer seryjny. Oznacza to, że jeśli tylko klient dołoży starań, aby rejestrować zmiany, jakie samodzielnie wprowadzi w nabytych obudowach, pod naklejonym kodem QR zawsze będzie się znajdować aktualna wersja dokumentacji wraz z modelem trójwymiarowym obejmującym wszystkie modyfikacje.
Dzięki temu idee Przemysłu 4.0 pozwalają nie tylko usprawnić działanie fabryki, ale przekładają się też na realne korzyści dla klientów. Rittal nazywa to mianem tworzenia wartości 4.0.
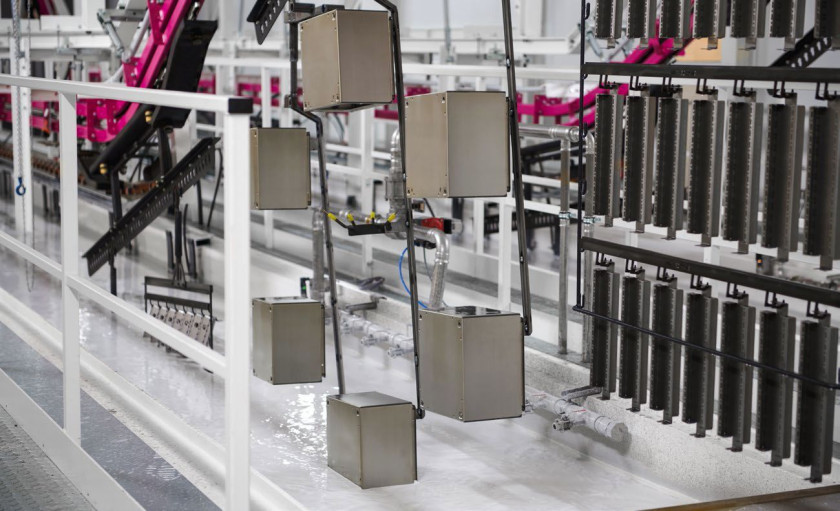
EKONOMIA 4.0
Wszystkie opisane innowacje można by było wdrożyć tak samo w fabryce w Niemczech, jak i gdziekolwiek indziej na świecie. Dlaczego więc Rittal nie zdecydował się tym bardziej zmniejszyć kosztów i zbudować nowej fabryki w kraju, gdzie koszty produkcji są niższe? O to również zapytaliśmy podczas wizyty i powodów jest wiele.
Przede wszystkim utrzymanie produkcji w Niemczech pozwala na oferowanie błyskawicznej dostawy indywidualnych zamówień na rynku niemieckim, a więc tam, gdzie Rittal jest niezrównanym potentatem. Ale z ekonomicznego punktu widzenia bardziej znaczące jest to, że w fabryce tego typu wynagrodzenia pracowników stanowią znikomą część całkowitych kosztów jej funkcjonowania.
Nowy zakład będzie w stanie produkować 8000 obudów malowanych dziennie (czyli tyle co poprzedni), a dodatkowo 1000 obudów ze stali nierdzewnej, a to wszystko przy ograniczeniu personelu o ok. 25%. Redukcja zatrudnienia nie brzmi atrakcyjnie z PR-owego punktu widzenia, ale trzeba mieć na uwadze, że minimalizowanie kosztów produkcji jest konieczne w celu utrzymywania konkurencyjności na rynku.
W rzeczywistości więc Rittal wybrał drogę korzystną dla swojego niemieckiego zespołu, gdyż, w przeciwieństwie do innych producentów, zamiast relokować zakład do Azji, postawił na utrzymanie jak największej liczby miejsc pracy na rodzimym rynku. A to było możliwe tylko dzięki inwestycjom w nowoczesne technologie.
Warto też dodać, że Rittal, który regularnie znajduje się na szczycie list najlepszych pracodawców w Niemczech, zatroszczył się o pracowników zamykanego zakładu. Formalnie rzecz ujmując, żadna z osób z dotychczasowej załogi nie została zwolniona. Wszystkim zaoferowano bezpłatne szkolenia, na które wydano już łącznie ponad milion Euro.
Najstarszy z pracowników, który z nich skorzystał, ma 55 lat. Ponadto części osób, które były blisko wieku emerytalnego, zaoferowano wcześniejsze emerytury. W efekcie z przedsiębiorstwa odeszły tylko te osoby, które zdecydowały się wcześniej przejść na emeryturę lub nie chciały skorzystać ze szkoleń i uznały, że wolą poszukać pracy w innej firmie.
A trzeba mieć na uwadze, że nowe stanowiska pracy są bardziej komfortowe i bezpieczniejsze niż te w poprzednim zakładzie - zamiast wykonywać prace manualne, pracownicy w przeważającej części nadzorują teraz komputerowo pracę maszyn. Można więc powiedzieć, że nowy zakład Rittala stanowi wzorcowy przykład tego, do czego prowadzi automatyzacja na rynku pracy: zatrudnienie maleje w niewielkim stopniu, a nowo powstałe miejsca pracy są bardziej atrakcyjne.
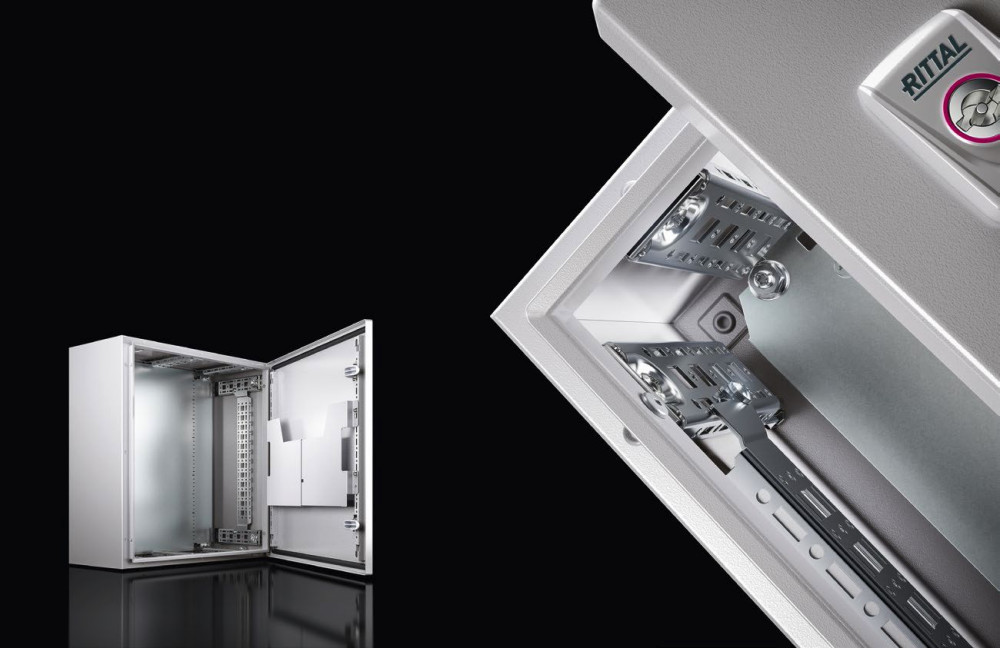
PODSUMOWANIE
Nowa fabryka Rittala to pod wieloma względami wzór do naśladowania i z całą pewnością będzie tak traktowana przez inne firmy produkcyjne - szczególnie z państw zachodnich. Przedstawiciele przedsiębiorstwa podczas spotkania podkreślali, że wprowadzenie idei Przemysłu 4.0 wcale nie przychodzi z łatwością i że w trakcie procesu zmian napotyka się ogromne ilości problemów, z którymi po prostu trzeba sobie poradzić.
Zapytani o główną radę, jaką mogliby przekazać innym firmom, które planują lub wdrażają podobne przemiany, stwierdzili, że najważniejsze jest, aby stanowczo trzymać się raz podjętej decyzji - pomimo wszelkich przeszkód, które przytrafiają się po drodze.
Warto pytać o szczegóły doświadczonych inżynierów i menedżerów fabryk oraz czytać prasę branżową opisującą różnorodne wdrożenia, ale podstawową kwestią jest to, aby w pełni zaangażować się w zmiany i nie wycofywać przy pierwszych porażkach. Tylko w ten sposób można zaoferować lepsze usługi i produkty, zachowując konkurencyjne ceny i utrzymując miejsca pracy w Europie czy Ameryce Północnej.
Marcin Karbowniczek