NA CZYM POLEGA HARTOWANIE SZKŁA?
Jak wspomnieliśmy wcześniej, przechodząc od szczegółu do ogółu, na większą skalę oraz kompleksowo można modernizować całe procesy i linie produkcyjne. Dalej wyjaśniamy to na przykładzie hartowania szkła. Proces ten ma na celu zwiększenie wytrzymałości mechanicznej i termicznej tego materiału. Składa się z dwóch etapów. Pierwszym jest ogrzewania szkła do określonej, bardzo wysokiej temperatury. Następnie jest ono szybko oraz równomiernie schładzane w kontrolowanych warunkach.
HARTOWANIE SZKŁA – GDZIE ENERGIA JEST TRACONA?
Najbardziej energochłonną częścią linii hartowania jest sekcja pieca, ponieważ najwięcej energii zużywa się na ogrzewanie szkła. Na ilość ciepła, a tym samym ilość energii elektrycznej, potrzebnej do ogrzania szkła nie można wpłynąć – wymagana temperatura jest determinowana przez specyfikę tego procesu.
Niestety, ogrzewanie szkła w praktyce nie odbywa się bez strat, co trzeba uwzględnić w bilansie zużycia energii. Największe z nich to: straty energii na skutek uwalniania ciepła do otoczenia przez ściany pieca i straty ciepła towarzyszące przepływowi powietrza używanego do zwiększania sprawności przekazywania ciepła przez konwekcję.
Drugi etap procesu, czyli chłodzenie, również wnosi znaczący wkład w sumaryczne zużycie energii w procesie hartowania szkła – w przypadku cieńszych płyt w praktyce często udział ten odpowiada ilości energii zużytej na ogrzewanie szkła w pierwszym etapie. W procesie chłodzenia najbardziej energochłonnym komponentem są silniki dmuchaw wymuszających obieg powietrza, które hartuje szkło.
HARTOWANIE SZKŁA – GDZIE SZUKAĆ OSZCZĘDNOŚCI?
By poprawić efektywność energetyczną linii hartowania szkła, przede wszystkim powinno się ograniczyć straty energii cieplnej. W tym celu okresowo należy sprawdzać stan izolacji pieca, w miarę użytkowania bowiem zaczyna ona pękać oraz tracić swoje właściwości izolacyjne.
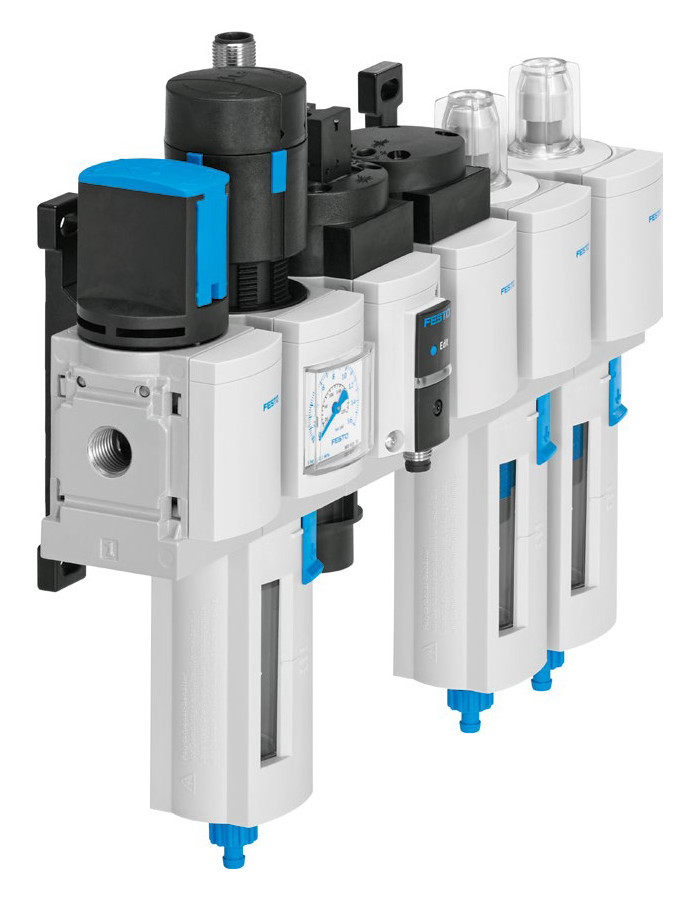
Regularne sprawdzanie, czy izolacja jest w dobrym stanie i czy odpowiada nowoczesnym standardom, ma dodatkową zaletę poza ograniczeniem strat energii – można w ten sposób uniknąć pylenia jej ubytków, co może pogarszać jakość finalnego wyrobu. Straty energii na tym etapie można również zmniejszyć, ograniczając do niezbędnego minimum czas i częstość otwierania pieca oraz zachowując w tym zakresie wśród personelu dyscyplinę.
Straty ciepła towarzyszące przepływowi powietrza używanego do zwiększania sprawności przekazywania ciepła przez konwekcję na etapie ogrzewania szkła można ograniczyć, zastępując to medium dostarczane z zewnątrz systemem z obiegiem zamkniętym. Jest to bardziej energooszczędne, gdyż wtedy do sekcji grzewczej nie jest wdmuchiwane powietrze z zewnątrz, które następnie trzeba z pieca odprowadzić z oczywistą stratą.
Jeżeli chodzi o proces chłodzenia, to zoptymalizować należy pracę silników zasilających dmuchawy, na przykład przez doposażenie je w przemienniki częstotliwości. Dzięki temu na przykład w przypadku hartowania pewnych typów szkła, gdy potrzebna jest tylko niewielka ilość powietrza, obroty wentylatorów można zwolnić. Ważne też, by ograniczyć czas pracy ich napędów na biegu jałowym do niezbędnego minimum, na co ma wpływ sprawność organizacji załadunku pieca.
Oszczędność wody w praktyceOptymalizacja pracy instalacji CIPW wielu branżach, na przykład w przemyśle spożywczym i farmaceutycznym, utrzymanie czystości i/lub sterylności linii produkcyjnych jest kluczowe dla jakości i bezpieczeństwa finalnego produktu, a przez to wymagane nie tylko przez interes producenta, ale i normy, do których musi się stosować. Dlatego ich wyposażenie jest myte, a często również sterylizowane w celu usunięcia z powierzchni mających kontakt ze składnikami oraz wyrobami resztek tych substancji, na których mogą rozwijać się bakterie, oraz zabicia drobnoustrojów już tam obecnych. Wykonuje się to ręcznie albo w sposób zautomatyzowany w systemach CIP (Cleaning in Place) i SIP (Sterilisation in Place). ![]() Mycie i sterylizacja na miejscu polegają na spłukiwaniu wnętrza wyposażenia linii produkcyjnych, głównie zbiorników, rurociągów, pomp, w przerwach między kolejnymi jej uruchomieniami, bez konieczności rozmontowywania jej elementów albo wprowadzania do ich wnętrza urządzeń czyszczących czy wchodzenia do nich. To ostatnie dotyczy dużych zbiorników, na przykład mieszalników. W zamian w systemach CIP/SIP realizuje się to przez wymuszenie przepływu środków myjących oraz odkażających przez te urządzenia i obiekty, a następnie ich powrotu do głównego zasobnika. W porównaniu z ręcznym czyszczeniem instalacji produkcyjnych zautomatyzowane mycie i sterylizacja na miejscu mają wiele zalet, przede wszystkim w zakresie oszczędności zasobów, z których najważniejszymi, decydującymi o opłacalności, są: energia elektryczna, woda, chemikalia i czas. Dodatkowo optymalizując działanie systemów CIP/SIP, można jeszcze bardziej zmniejszyć ich zużycie. Przykładowo, jeżeli myte są zbiorniki o różnej wielkości, czas mycia może być zaprogramowany pod kątem tych największych. W takim przypadku warto jest go zróżnicować, dostosowując do rzeczywistych wymagań. Podobnie nie wszystkie cykle wymagają użycia gorącej wody. W przypadku temperatury wody trzeba jednak pamiętać o następującej zależności: jej podwyższenie pozwala zwykle skrócić czas czyszczenia. Typowa sekwencja mycia obejmuje etapy:
Jednak nie w każdym przypadku wszystkie cykle powinny być koniecznie przeprowadzane. Czas trwania etapu spłukiwania warto dostosować do zastosowanego detergentu – przykładowo generalnie te kwasowe spłukują się łatwiej, niż zasadowe. Podobnie w przypadku środków dezynfekujących – niektóre z nich wymagają mniej spłukiwania niż inne, a niektóre nadają się do wielokrotnego użytku. Poza tym wodę wykorzystywaną do finalnego płukania instalacji można powtórne zachować w kolejnym cyklu w pierwszym etapie wstępnego spłukiwania. |