PACKML - STANDARD DLA MASZYN PAKUJĄCYCH
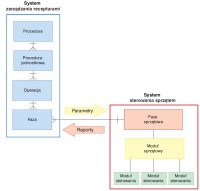
Rys. 5. System zarządzania recepturami i system sterowania sprzętem najczęściej komunikują się na poziomie fazy
Gotowe produkty, już w ramach procesów dyskretnych, są pakowane. Na przykład lody porcjuje się i przekłada do pojemników. Maszyny pakujące to w większości złożone urządzenia mechatroniczne. Są one zbudowane z: serwonapędów sterujących wieloma osiami ruchu elementów wykonawczych, zintegrowanych systemów wizyjnych, paneli operatorskich, systemów zabezpieczeń i interfejsów komunikacyjnych, itd.
Funkcjonalność tych podzespołów scala program sterujący maszyną. Ponieważ brak normalizacji tego ostatniego utrudniał integrację wyposażenia linii pakującej, opracowano standard PackML (Packaging Machinery Language) (ISA-TR88.00.02). Na potrzeby przemysłu opakowaniowego zaadaptowano w nim rozwiązania wprowadzone w ISA-88.
Jakie korzyści zapewnia PackML?Zgodność ze standardem PackML zapewnia w branży opakowaniowej podobne korzyści, jak przestrzeganie wytycznych ISA-88 w produkcji wsadowej. Najważniejsze z nich to: ułatwiona integracja maszyn w obrębie linii pakowania dzięki modułowości sprzętowej (plug and play) i standardowym danym wejściowym i wyjściowym (sprawna komunikacja), jednolite środowisko programowe dla operatorów, uproszczone specyfikacje maszyn, szybszy rozwój oprogramowania i łatwiejsze jego testowanie, komponenty sprzętowe oraz programowe wielokrotnego użytku, dzięki którym maszyny, ich eksploatacja i konserwacja są tańsze. Ponadto producenci mogą się skupić na rozwoju funkcjonalności, która wyróżni ich urządzenie na tle konkurencji, zamiast tracić czas na implementację jego podstawowych funkcji. |
TRYBY PRACY PAKOWARKI WEDŁUG PACKML
Tryby (modes) pracy maszyny (m.in. automatyczny, półautomatyczny, ręczny, konfiguracji) zdefiniowano w nim jako uporządkowane zbiory: stanów (states), charakteryzujących daną czynność, przejść pomiędzy nimi odbywających się w ustalonej kolejności (patrz: ramka) i komend. Stany, których przewidziano 17 (nie trzeba korzystać ze wszystkich, można również określić własne), podzielono na trzy rodzaje: aktywne (acting), oczekiwania (wait) oraz dualne (dual).
Do ostatniej grupy, łączącej w sobie cechy dwóch pierwszych, zaliczane jest tylko działanie (execute). Inne standardowe stany to m.in.: zatrzymanie (stopped, idle), przerwanie zadania (aborting) albo jego wstrzymanie spowodowane blokadą procesu nadrzędnego, podrzędnego (suspended) lub decyzją operatora (held). Zależnie od maszyny w danym stanie realizowane są różne zadania.
CZYM SĄ PACKTAGS?
Robot pick & place na przykład w trybie automatycznym w stanie działania podnosi produkty z taśmociągu i przekłada je na paletę. W trybie konfiguracji jest on programowany. Tryby, stany i sekwencje określone są w normie ISA-TR88.00.02 i są uniwersalne, czyli można za ich pomocą opisać pracę różnych urządzeń, nie tylko maszyn pakujących.
W PackML zdefiniowano także format przepływu danych z i do maszyny w postaci tzw. PackTags. Podzielono je na trzy kategorie: PackTags z komendami sterującymi (na przykład przełączające tryb lub stan pracy), danymi o statusie urządzenia (m.in. prędkości, trybie, stanie) i administracyjnymi (przykładowo o alarmach). Te ostatnie są przeznaczone dla systemów nadrzędnych. Nie ma obowiązku korzystania ze wszystkich tagów (te nadmiarowe dodatkowo komplikują program).
Paweł KrzesakBosch Rexroth
Najwyższe standardy higieniczne cechujące branże spożywczą, w szczególności w miejscach bezpośredniego kontaktu z produktami, wymagają dostarczanie komponentów wykonanych z najlepszych materiałów zgodnych z certyfikatem FDA. Częste mycie i czyszczenie układów wymaga odpowiedniej szczelności i odporności na wysokie temperatury, dlatego Bosch Rexroth stawia na takie elementy jak stal nierdzewna bądź wysokiej jakości tworzywa sztuczne. Zarówno w dziedzinie napędów elektrycznych, w technice przemieszczeń liniowych czy systemów transportowych Rexroth ma rozwiązania dedykowane.
Głównymi odbiorcami rozwiązań są przede wszystkim producenci maszyn, ale ważnymi rynkami zbytu są również działy utrzymania ruchu i sektor części zamiennych. Oprócz spełnienia wymagań technicznych o wyborze dostawcy decyduje szybkość dostaw komponentów, czas reakcji serwisowej oraz wymagania zachowania standardów u użytkowników końcowych.
Efektywność energetyczna, elastyczność i technika bezpieczeństwa to kluczowe zagadnienia na najbliższe lata. Zmiany zachodzące w zachowaniach konsumentów będą miały bezpośredni wpływ na produkcję i pakowanie artykułów spożywczych. Wymagania odnośnie do automatyzacji będą zaostrzały konkurencję z coraz krótszym cyklem życia produktów. Co najmniej taka sama wydajność przy mniejszym zużyciu energii, inteligentna regulacja, szybki czas przezbrojeń czy odzysk energii w procesie hamowania - to one będą decydowały o wyborze optymalnych rozwiązań podczas projektowania. |
DWA PODEJŚCIA
Zalecane są dwie metody implementacji wytycznych standardu PackML w nowo tworzonym albo już wdrożonym kodzie. Z pierwszego należy skorzystać, kiedy w gotowym programie trudno jest zastosować model stanów opracowany w ISA-TR88.00.02.
Nie warto wówczas na siłę go wdrażać, ponieważ pogorszy to jakość oraz czytelność jego kodu. To ostatnie skomplikuje jego dalszy rozwój, trudniej będzie także wykryć błędy. W zamian lepiej dane wejściowe oraz wyjściowe sterowników PLC przekonwertować do formatu PackTags. Zapewni to przynajmniej wspólny interfejs komunikacyjny z innymi komponentami linii pakowania.
Drugie podejście zakłada kompleksową implementację zaleceń normy ISA-TR88.00.02 włącznie z tymi dotyczącymi modułowości kodu. Realizuje się to na dwa sposoby: pisząc nowy program, na przykład dla dopiero projektowanej maszyny lub przepisując stary w formacie PackML. To drugie wymaga szczegółowej wiedzy na temat istniejącego kodu i trwa dłużej niż przekonwertowanie go tylko do formatu PackTags.
|
Stany pracy maszyn pakujących według PackML![]() Diagram stanów PackML Drugi oraz trzeci są stanami stabilnymi, tzn. mogą trwać przez dłuższy czas. Czas trwania stanów "zielonych" jest ograniczony, a przejście do kolejnego etapu odbywa się bez udziału operatora (SC - state complete). Działanie w pętli ze stanem wstrzymania Suspended oznacza oczekiwanie np. na dostawę produktu, a w pętli ze stanem Held - zatrzymanie w wyniku decyzji operatora. Po wykonaniu zadania maszyna przechodzi ze stanu Execute do Complete. Może się wówczas rozpocząć kolejny cykl pracy. Przerywa go komenda Abort oznaczająca błąd albo Stop, którą wybiera operator. |
KRÓTKO O CIP I SIP
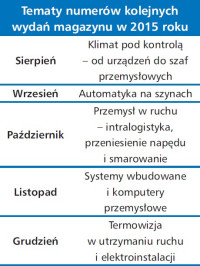
Tematy numerów kolejnych wydań magazynu w 2015 roku
Mycie i sterylizacja na miejscu polegają na spłukiwaniu wnętrza wyposażenia linii produkcyjnych (głównie zbiorników, rurociągów, pomp, itp.) w przerwach między kolejnymi jej uruchomieniami, bez konieczności rozmontowywania jej elementów albo wprowadzania do ich wnętrza urządzeń czyszczących lub wchodzenia do nich (dotyczy to dużych zbiorników, na przykład mieszalników). W systemach CIP i SIP realizuje się to, wymuszając przepływ środków myjących i odkażających przez te urządzenia i obiekty i ich powrót do głównego zasobnika.
Do zalet mycia i sterylizacji na miejscu zalicza się: szybkość (nie trzeba demontować, a następnie składać wyposażenia linii produkcyjnej), dokładniejsze czyszczenie miejsc trudno dostępnych, lepszą kontrolę zużycia wody i chemikaliów (te ostatnie można poddać recyklingowi), a zatem mniejsze koszty i ograniczenie kontaktu personelu z substancjami dla niego niebezpiecznymi.
W DRUGIEJ CZĘŚCI ARTYKUŁU...
Ze względu na powyższe kwestie mycie i sterylizacja na miejscu są coraz popularniejsze nie tylko w branży spożywczej, ale i innych, w których konieczne jest zachowanie higienicznych warunków produkcji - na przykład farmaceutycznej oraz chemicznej. Aby metody CIP i SIP przyniosły wymierne korzyści, czyszczenie i sterylizacja muszą być staranne i skuteczne.
W drugiej części artykułu (publikacja we wrześniu) przedstawiamy czynniki, które na to wpływają - m.in. dobór odpowiednich środków chemicznych i parametrów procesu (natężenia przepływu, temperatury). Jak się okaże - w projektowaniu systemów sterowania instalacjami CIP i SIP znajduje też zastosowanie standard ISA-88.
Monika Jaworowska
- Procesy wsadowe w produkcji spożywczej
- Wyzwania w sterowaniu procesami wsadowymi
- Jakie problemy rozwiązała norma ISA-88?
- Klasyfikacja receptur według ISA-88
- Modele procedur receptury
- Model fizyczny sprzętu
- Moduł sprzętowy a moduł sterowania
- Jak to wszystko połączyć?
- PackML - standard dla maszyn pakujących
- Tryby pracy pakowarki według PackML
- Czym są PackTags?
- Dwa podejścia
- Czyste maszyny to higieniczna produkcja
- Krótko o CIP i SIP
- W drugiej częsci artykułu...
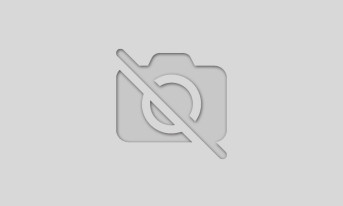
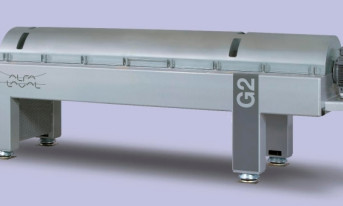
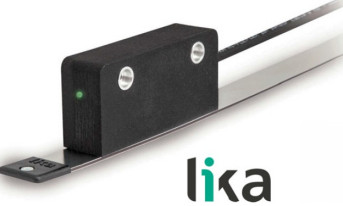
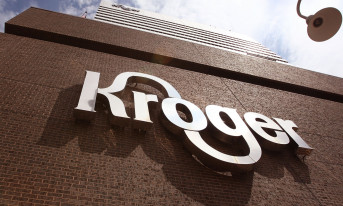
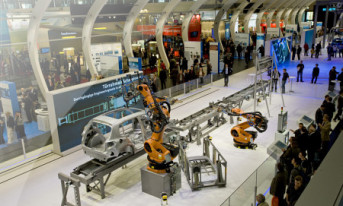
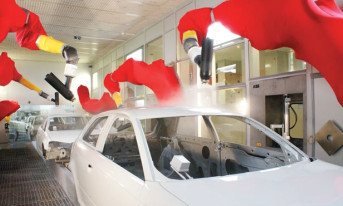

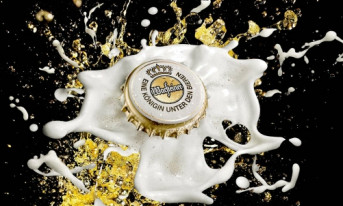
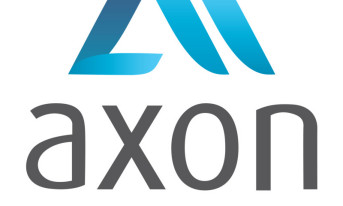
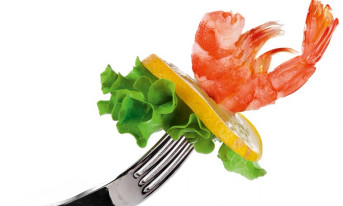
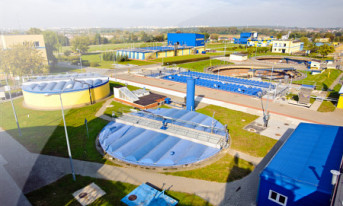
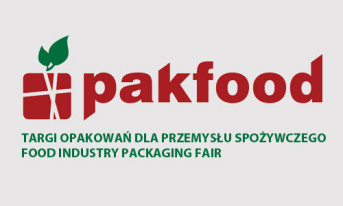
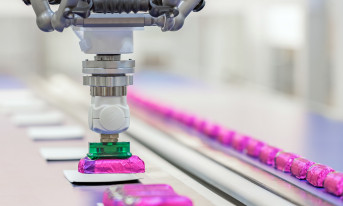
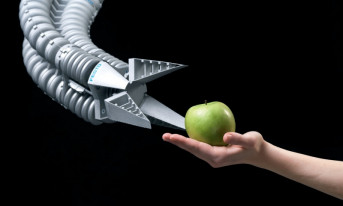
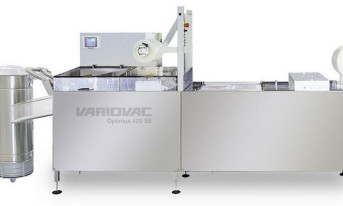
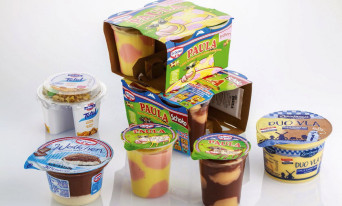
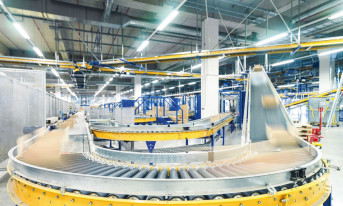
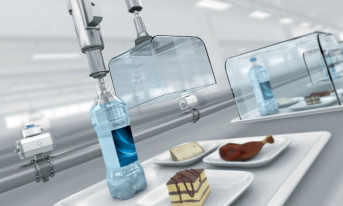
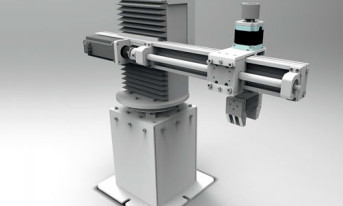


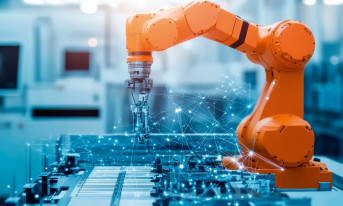
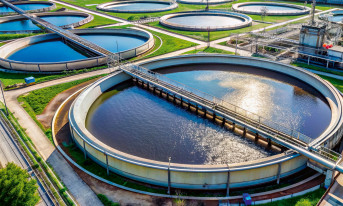
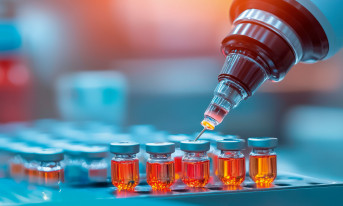
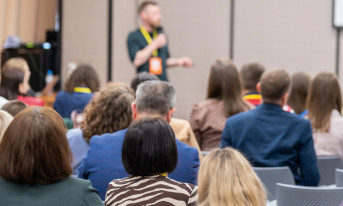
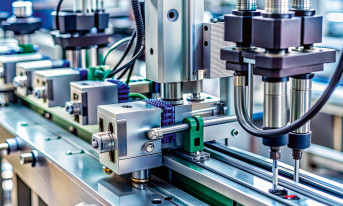