CZĘŚĆ 1: ZAUTOMATYZOWANE TŁOCZENIE BLACH
Produkcja samochodów jest procesem wieloetapowym. Rozpoczyna się od uformowania z metalu elementów karoserii. Części takie, jak drzwi, błotniki, dach i pokrywy: silnika i bagażnika, są ważnymi elementami pojazdu, które mają wpływ na jego wygląd, wagę oraz bezpieczeństwo pasażerów. Wykonuje się je w procesie tłoczenia - jest to najpopularniejsza technika produkcji części w przemyśle motoryzacyjnym.
TECHNOLOGIA TŁOCZENIA
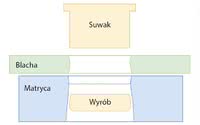
Rys. 1. Główne części prasy to suwak i matryca
Do zalet tłoczenia, w porównaniu z innymi metodami produkcji, zalicza się: dużą wydajność, mały koszt i możliwość uzyskania kształtów o różnym stopniu skomplikowania, od prostych po złożone.
Tłoczenie to metoda obróbki plastycznej, w której na materiał (metal, niemetal) wywierany jest nacisk tak silny, że powoduje on jego nieodwracalne odkształcenie się, nie niszcząc go przy tym. Realizuje się to za pomocą pary elementów tworzących prasę: ruchomego suwaka (stempla), który dociska materiał do nieruchomej matrycy.
Tłoczenie umożliwia łączenie materiałów, ich cięcie oraz nadawanie im określonych kształtów. Uzyskuje się to m.in. przez: ich zaginanie, skręcanie, zaprasowywanie, zawijanie ich brzegów, dziurkowanie, wybijanie, przetłaczanie, zgniatanie albo wyciskanie.
Na rysunku 1 przedstawiono przykład zestawu suwak - matryca prasy, która służy do wybijania. Jak widać, przekrój otworu w matrycy w początkowym odcinku biegnie prosto, natomiast dalej się rozszerza.
Taka konstrukcja zapobiega blokowaniu się w matrycy wybijanych elementów, co groziłoby awarią prasy. Prosty odcinek powinien mieć długość 3 mm w przypadku blach o grubości poniżej tej wartości. Dla pozostałych najlepiej, jeżeli jest on równy grubości pojedynczego arkusza.
KLASYFIKACJA PRAS
Wyróżnić można trzy typy pras wykorzystywanych do tłoczenia metalowych części: mechaniczne, hydrauliczne i serwomechaniczne. W przypadku pierwszych stempel jest wprawiany w ruch przez silnik za pośrednictwem sprzęgła oraz koła zamachowego.
W prasach hydraulicznych energia do elementu wykonawczego jest przekazywana przez czynnik hydrauliczny. Z kolei w urządzeniach trzeciego typu serwomechanizm zastępuje najważniejsze podzespoły pras mechanicznych (silnik, koło zamachowe, sprzęgło, hamulec).
Prasy mechaniczne na tle pozostałych wyróżnia największa szybkość działania, szczególnie jeżeli nie jest wymagane wykonanie zbyt głębokich wgłębień, jak w przypadku elementów tłoczonych z metalowych taśm, które są rozwijane ze szpuli.
Do tej grupy zalicza się m.in. części karoserii i obudów urządzeń gospodarstwa domowego. Inne ważne zalety pras mechanicznych to: duża dokładność i powtarzalność, stosunkowo niski koszt początkowy, łatwość uruchomienia oraz obsługi.
JAKA PRASA BĘDZIE NAJLEPSZA?
Prasy hydrauliczne nie działają tak szybko, jak prasy mechaniczne. Warto się jednak zdecydować na ten typ maszyn w przypadku, gdy wymagane jest wykonanie głębokich wgłębień, o złożonych kształtach, na przykład zaokrąglonych na dnie.
Dlatego w prasach hydraulicznych przeważnie wytłaczane są m.in. zbiorniki i cylindry. Generalnie jednak ten rodzaj maszyn pod względem dokładności oraz powtarzalności ustępuje zarówno prasom mechanicznym, jak i serwomechanicznym.
Jeżeli chodzi o te ostatnie, to zasadniczo, w porównaniu z prasami mechanicznymi, zapewniają lepszą jakość obróbki, większą wydajność pracy i dłuższą żywotność elementu wykonawczego. Cechuje je również większa precyzja, możliwość głębszego tłoczenia oraz większa elastyczność, pozwalająca na dopasowanie cyklu pracy do konkretnego zastosowania. Są jednak droższe.
Ważnym elementem wszystkich typów pras jest wyposażenie dodatkowe. Przykładem są czujniki.
Projektowanie tłoczonych częściW zakresie projektowania przestrzega się wielu zasad, w tym m.in. tych opisanych poniżej.
|
WYPOSAŻENIE DODATKOWE PRAS - CZUJNIKI
Jedną z częstszych przyczyn przestojów pras i różnej jakości tłoczonych wyrobów jest uszkodzenie matrycy, o co nietrudno z powodu szybkości, z jaką stempel w nią uderza. Typowo wynosi ona od kilkudziesięciu uderzeń na minutę w produkcji części karoserii samochodów, do ponad tysiąca uderzeń na minutę w przypadku mniejszych elementów. Aby matryca się nie zniszczyła podczas tłoczenia, części prasy ani arkusz metalu nie powinny się przesuwać względem ustalonej pozycji.
Dlatego prasę wyposażą się w różnego typu czujniki oraz enkodery. Potrzebny jest także sterownik, który właściwie zinterpretuje sygnały z tych sensorów i wygeneruje odpowiednie sygnały sterujące.
W pierwszej kolejności trzeba zdecydować, jaki typ czujników i gdzie należy zamontować. Sensory mogą być m.in. używane do sprawdzania, czy prasa została załadowana, czy usunięto z niej gotowy wyrób, a krzywki znajdują się we właściwej pozycji. Najczęściej instaluje się czujniki kontaktowe i bezkontaktowe, na przykład indukcyjne zbliżeniowe i fotoelektryczne. Pierwsze są tanie, ale mają krótszą żywotność niż drugie, które są z kolei droższe.
PODAWANIE I SMAROWANIE
Na szybkość i wydajność procesu tłoczenia ma też wpływ sposób, w jaki do prasy doprowadzany jest materiał poddawany obróbce. W przypadku części karoserii wytłaczanych z arkuszy blach o bardzo dużych rozmiarach przez prasy o nacisku kilkuset ton i większym, płaty te są przeważnie przenoszone, a następnie układane na matrycy ręcznie, nawet przez kilka osób obsługujących maszynę.
Części o mniejszych gabarytach wytłacza się z kolei z arkuszy blach pobieranych samoczynnie przez prasę albo metalowych taśm, które rozwijane są ze szpul i doprowadzane do maszyny za pośrednictwem podajnika. W drugim przypadku taśma po odwinięciu jest przeciskana między rolkami. Ma to na celu spłaszczenie zafalowań powstałych podczas jej nawijania na szpulę.
Opór, jaki stawia metalowy arkusz naciskowi wywieranemu przez suwak prasy, powoduje tarcie. Aby je zmniejszyć, konieczne jest użycie smaru. Dzięki niemu żywotność suwaka jest dłuższa, a jakość wyrobu lepsza. W tym celu stosuje się środki różnego rodzaju, od lekkich olei mineralnych, po związki o dużej lepkości, na bazie oleju, rozpuszczalne w wodzie lub syntetyczne. Nanosi się je ręcznie albo prasa smaruje blachy samoczynnie.
Na koniec tej części warto dodać, że odpowiednio dobrany sprzęt i jego właściwa eksploatacja to tylko połowa sukcesu. Czy wytłoczone części będą wytrzymałe, spełnią swoje zadanie, zaś ich produkcja będzie opłacalna, czasowo i kosztowo, zależy także od ich projektu. Temat ten opisujemy w ramce.
CZĘŚĆ 2: ROBOTY W PRODUKCJI SAMOCHODÓW
Oprócz maszyn zautomatyzowanych w produkcji samochodów używa się również robotów przemysłowych. Wykonują one zadania w sposób powtarzalny, nie męczą się, nic nie może odwrócić ich uwagi. Jeśli są wyposażone w czujniki, na przykład laserowe albo są sterowane wizyjnie, mogą się dostosowywać do zmian właściwości, na przykład różnic w wymiarach kolejnych detali.
Dzięki temu wyroby, które produkują, charakteryzuje lepsza jakość i jednolitość wykonania. Oprócz tego nie upuszczą ich, nie popełnią błędu ani nie będą nimi operować w sposób, który mógłby je uszkodzić. Ogranicza to straty materiałów i gotowych wyrobów, które są skutkiem błędów ludzkich.
|
ZALETY ROBOTÓW
Fakt, że roboty się nie męczą, wpływa nie tylko na jakość wyrobu, ale i na wydajność produkcji. Dzięki temu, że pod koniec zmiany ich efektywność nie maleje, jak w przypadku pracowników, i nie potrzebują przerw, można utrzymać jednakowe tempo pracy. Ułatwia to planowanie produkcji i zarządzanie stanem magazynów.
Roboty przemysłowe poprawiają też bezpieczeństwo pracowników, zastępując ich w zadaniach niebezpiecznych. Niektóre z zagrożeń są oczywiste, jak na przykład: zranienie przez odpryski lub uszkodzenie wzroku przez błyski światła towarzyszące spawaniu części samochodowych i zatrucie szkodliwymi substancjami chemicznymi używanymi w procesie ich lakierowania. Innych nie odczuwa się natychmiast, jak na przykład zmian w kręgosłupie wywołanych wykonywaniem powtarzalnych ruchów albo podnoszeniem ciężkich przedmiotów.
Zaletą robotów przemysłowych jest dość łatwe i szybkie przestawienie ich na inne zadanie - często wystarczy je przeprogramować i zmienić końcówkę roboczą. Dzięki temu są bardziej uniwersalne niż zautomatyzowane maszyny o ograniczonej funkcjonalności. Zapewnia to dużą oszczędność w razie zmiany profilu produkcji.
Branża motoryzacyjna wkracza w erę Industry 4.0Nie tylko automatyzacja produkcji ułatwia sprostanie wyzwaniom, przed którymi stają producenci z branży samochodowej. W erze Przemysłu 4.0 pomaga w tym też jej cyfryzacja i nowe technologie. Te ostatnie to m.in.: wytwarzanie addytywne (druk 3D), rzeczywistość wirtualna oraz rozszerzona, roboty współpracujące, sztuczna inteligencja, Przemysłowy Internet Rzeczy i chmura obliczeniowa. Niektórzy producenci nie tylko korzystają z nich wybiórczo, ale i zaczynają projektować w oparciu o nie całe zakłady. Przykładem jest Faurecia. Cyfrowa fabryka Faurecii
Przykładem są samouczące się autonomiczne, inteligentne pojazdy AIV (Autonomous Intelligent Vehicles) i roboty współpracujące. Pierwsze są wykorzystywane do transportu komponentów na linie montażowe, zaś roboty współpracujące znalazły zastosowanie w produkcji. Oprócz tego wszystkie maszyny połączono w sieć za pomocą światłowodów o łącznej długości 2 kilometrów. Pracownikom stworzono w pełni cyfrowe środowisko pracy, wyposażając ich w urządzenia mobilne i prawie całkowicie "rezygnując z papieru". Szacuje się, że codziennie wszystkie nowoczesne rozwiązania wdrożone w tym zakładzie generują około terabajta informacji. Aby były użyteczne, w ich analizie korzysta się ze specjalnych rozwiązań z dziedziny eksploracji danych (data mining). |
PRZEGLĄD ZADAŃ
Roboty przemysłowe mają w przemyśle motoryzacyjnym szeroki zakres zastosowań. Są one używane m.in. w spawaniu części samochodowych. Roboty o dużym udźwigu i długim zakresie roboczym spawają części karoserii, natomiast mniejsze maszyny są używane do przymocowywania różnego typu zacisków. W tym zastosowaniu przydatna jest zdolność robotów do precyzyjnego i powtarzalnego podążania po zaprogramowanych, nawet bardzo skomplikowanych ścieżkach.
Roboty malarskie
Ostatnia z cech jest również ważna w następnym etapie produkcji samochodów, jakim jest lakierowanie. W malarni roboty przemysłowe są wykorzystywane do nanoszenia kolejnych warstw, którymi pokrywa się części karoserii, czyli: podkładu antykorozyjnego, właściwego koloru i lakieru bezbarwnego.
Roboty pracujące w malarni muszą być przystosowane do działania w takim pomieszczeniu. W tym celu w ich konstrukcji stosuje się specjalne rozwiązania, jak: materiały umożliwiające pracę w strefach zagrożonych wybuchem (ze względu na łatwopalność farb, lakierów, ich oparów), sensory do pomiaru parametrów malowania montowane na ramieniu robota, manipulatory, które pozwalają na regulację ustawienia pistoletu do natrysku w szerokim zakresie, przewody prowadzone wewnątrz ramienia i kiści (niekrępujące ruchów robota), materiały, które łatwo dają się oczyścić z zaschniętej farby i/lub specjalne pokrowce.
Montaż i cięcie
Poza malowaniem roboty nakładają różnego rodzaju uszczelnienia oraz kleje na części przed ich zmontowaniem. Montaż to następny przykład zadania, w którym chętnie ludzi wyręcza się tymi maszynami. Systemy wizyjne oraz czujniki siły to te elementy ich wyposażenia, dzięki którym sprawdzają się one na tym etapie produkcji.
Przykładowe czynności, które wykonują, to: wkręcanie śrub, montaż szyb oraz kół. Szybkie roboty typu delta, które montuje się na suficie, są również używane do składania mniejszych podzespołów samochodów, na przykład pomp i silników.
Kontrola przykładanej siły, sterowanie wizyjne i podążanie zaprogramowaną ścieżką przydają się również w realizacji zadań cięcia i przycinania. Przykładowe zastosowania to: cięcie tkanin na podsufitki oraz gratowanie. Roboty są ponadto używane do załadowywania i rozładowywania urządzeń, na przykład maszyn tłoczących.
Wszystkie powyższe czynności wymagają "nauczenia" robota tego, jak ma je wykonywać, tak jak nowego pracownika należy przeszkolić w zakresie jego obowiązków. Specyfikę tego zadania przedstawiamy dalej na przykładzie spawania.
Spawanie i programowanie robotów
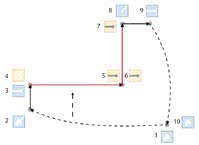
Rys. 2. Przykład ścieżki ruchu robota spawalniczego
Robota trzeba zaprogramować - wyróżnia się tutaj dwie podstawowe metody: online i offline. Pierwsza polega na programowaniu robota na jego stanowisku pracy przez nauczenie go właściwej kolejności ruchów. Zadanie to należy do operatora. Za pomocą panelu sterującego albo joysticka porusza on ramieniem robota. Układ sterujący robota zapisuje współrzędne kolejnych punktów wyznaczających tory poszczególnych przemieszczeń lub współrzędne pozycji docelowej, jeśli sposób jej osiągnięcia nie jest istotny. Do wad tej metody zalicza się: długie programowanie, wymóg dostępności robota, czyli jego wyłączenie z realizacji innych zadań produkcyjnych, i konieczność zaangażowania doświadczonego operatora.
Na rysunku 2 przedstawiono przykład ścieżki ruchu. Pierwszy punkt oznacza pozycję wyjściową. W tym położeniu ramię robota znajduje się w bezpiecznej odległości od stołu. W pozycji numer dwa przysuwa się ono trochę bliżej arkuszy, które zostaną połączone, ale wciąż na tyle daleko, aby mieć pewność, że nie uderzy ono w nie. Położenie numer trzy jest pierwszym punktem właściwej ścieżki spawania. W kroku numer 4 włączana jest spawarka.
Oba segmenty ścieżki są liniami prostymi. W kroku numer 8 spawarka jest wyłączana. Przejście z pozycji numer 8 na pozycję 9 pozwala na wycofanie ramienia robota na bezpieczną odległość od połączonych blach. Następnie wraca ono do położenia wyjściowego.
|
PROGRAMOWANIE OFFLINE. STEROWANIE ADAPTACYJNE
Programowanie offline odbywa się poza stanowiskiem roboczym robota, w specjalnym programie symulacyjnym, w którym trajektorie wyznacza się na podstawie modeli cyfrowych przedmiotów spawania i modeli kinematycznych robotów. Zaletą tej metody jest możliwość przetestowania programu przez wizualizację procesu w komputerze.
Ponadto wielokrotnie modyfikować można wcześniejsze programy. W komputerze łatwiej jest też przedstawić bardziej skomplikowane ruchy, korzystając z różnych funkcji danego oprogramowania. Co prawda koszt zakupu takiej aplikacji jest wysoki, jest to jednak wydatek jednorazowy. Zwykle zwraca się on dość szybko, gdyż robot w trakcie prac nad programem nie musi być wyłączony z dotychczasowych zadań.
Aby robot dostosowywał się do zmiennych warunków, kontroler tej maszyny powinien stosownie modyfikować parametry ruchu ramienia spawającego. Realizuje się to przez sterowanie adaptacyjne na podstawie informacji z czujników, w jakie wyposaża się robota. Ich zadaniem jest m.in.: detekcja krawędzi złącza, śledzenie jego przebiegu, żeby odpowiednio do niego zmieniało się położenie płomienia palnika oraz pomiar szerokości złącza w celu wykrycia wszelkich nieregularności i nieciągłości krawędzi.
Do znalezienia początku złącza lub krawędzi arkusza używane są głównie czujniki dotykowe i zbliżeniowe. Sensor dotykowy realizuje się, doprowadzając napięcie na przykład do dyszy, którą dostarczany jest gaz osłonowy, drutu spawalniczego lub dodatkowego próbnika. Kiedy końcówka tego elementu dotknie blachy, zwarcie jest wykrywane przez sterownik robota. Czujniki zbliżeniowe to zwykle sensory indukcyjne. Do śledzenia przebiegu i wyznaczania wymiarów złącza używane są natomiast głównie systemy wizyjne i skanery laserowe.
Case study 1Automatyzacja pomiarów usprawnia produkcję felg
Ze względu na wysokie wymagania odnośnie do jakości wykonania felg i dokładności ich wymiarów przedsiębiorca miał trudności ze spełnieniem oczekiwań odbiorców jednocześnie w tym zakresie i ilościowego zaspokojenia ich potrzeb. Jak się okazało, przyczyną tego stanu rzeczy było to, że proces produkcyjny wielokrotnie był przerywany w celu wykonania ręcznych pomiarów wymiarów felg, dokonania na ich podstawie odpowiednich obliczeń i w oparciu o nie dobrania i wprowadzenia nastaw maszyn. Takie podejście nie tylko wydłużało czas produkcji, ale nietrudno było o błąd w pomiarach, czy w obliczeniach. Aby rozwiązać tę niekorzystną sytuację, zdecydowano się zrezygnować z pomiarów ręcznych na rzecz sondy pomiarowej. Automatycznie kontroluje ona kluczowe wymiary felg w trakcie ich obróbki, a wyniki pomiarów drogą radiową przesyła do obrabiarki CNC. Na tej podstawie w maszynie automatycznie dostosowywane są jej nastawy. Dzięki temu usprawnieniu udało się: zredukować obciążenie pracowników, w pełni wykorzystać dostępną wydajność parku maszynowego, skrócić czas produkcji jednej felgi o połowę, ograniczyć straty materiałów i poprawić tolerancję wykonania felg. |
CZĘŚĆ 3: TRANSPORT, STEROWANIE, KONTROLA JAKOŚCI
W trzeciej części omawiamy inne ważne etapy produkcji samochodów, które są automatyzowane - takimi są transport (intralogistyka) oraz kontrola jakości.
Transport materiałów i wyrobów w obrębie zakładu jest to jedno z kluczowych zadań, od którego zależy wydajność, płynność i szybkość produkcji, nie tylko zresztą w branży samochodowej, ale w przemyśle w ogóle. W jego automatyzacji zwykle korzysta się z dwóch rozwiązań: przenośników i AGV (Automated Guided Vehicle), czyli bezzałogowych samojezdnych pojazdów wyposażonych w napęd elektryczny i zasilanych z akumulatorów.
PRZENOŚNIKI PODWIESZANE
Przenośniki podwieszane są popularnym środkiem transportu w przemyśle motoryzacyjnym. Dostępne są różne modele takich urządzeń. Najpopularniejsze są dwie konstrukcje: te, w których przenoszone obiekty są zawieszane bezpośrednio na rolkach ruchomego łańcucha pociągowego i przenośniki z wózkami przesuwanymi po oddzielnym torze za pomocą elementów popychających, które są z kolei przymocowane do ruchomego łańcucha pociągowego (typ power & free).
Przenośniki podwieszane są dostępne w wersjach o różnym udźwigu, od kilkudziesięciu kilogramów do nawet kilku ton. Dzięki temu w branży motoryzacyjnej znajdują zastosowanie w transporcie mniejszych i lżejszych podzespołów, takich o średnich rozmiarach i wadze, jak na przykład wytłoczonych części karoserii, które przewożą pomiędzy blacharnią a stanowiskiem robota spawalniczego, jak również większych i cięższych obiektów. Przykładem tych ostatnich są zespawane szkielety samochodów transportowane do lakierni.
Case study 2Automatyczna linia transportu szkła hartowanego
Hartowanie szkła Przykładem procesu produkcyjnego, w przypadku którego ma to szczególne znaczenie, jest produkcja szkła hartowanego, z którego wykonywane są szyby samochodowe. Poszczególne etapy jego obróbki, dla zapewnienia jego największej wytrzymałości powinny być zsynchronizowane, zaś nagromadzenie się szyb na jednym stanowisku może skutkować nawet ich potłuczeniem. Linia produkcyjna szkła hartowanego składa się z kilku stanowisk, w tym: pieca, w którym jest ono poddawane obróbce termicznej polegającej na jego podgrzaniu do temperatury sięgającej +700°C, stanowiska jego szybkiego schłodzenia oraz stanowiska szlifowania, na którym zostają wygładzone jego krawędzie.
Linia transportowa W pewnym zakładzie w ramach modernizacji linii transportu szkła hartowanego wyposażono ją w: sterowniki PLC, napędy AC i oprogramowanie HMI działające na IPC. Napędy przenośników łączących poszczególne stanowiska są zsynchronizowane z taśmociągiem wyjściowym pieca. W razie zmiany profilu produkcji albo specyfiki produktu sterowniki PLC zostają przeprogramowane stosownie do potrzeb. Zapewniona jest też ciągła diagnostyka napędów, dzięki czemu ogranicza się przestoje w produkcji. |
CECHY SYSTEMU PODWIESZANEGO
Przenośniki podwieszane mają wiele zalet. Na przykład w przypadku stanowisk malowania czy lakierowania dzięki nim aplikacja tych powłok jest łatwiejsza, uzyskuje się bowiem dostęp do malowanego obiektu ze wszystkich stron. Transport napowietrzny ułatwia też jego suszenie. Przenośniki podwieszane ułatwiają również organizację przestrzenną zakładu i pozwalają na oszczędność miejsca. Wynika to stąd, że nie blokują dróg komunikacyjnych.
Projektując system transportu podwieszanego, należy jednak pamiętać, że jeżeli jego konstrukcja będzie połączona z elementami konstrukcji budynku, trzeba sprawdzić, czy dana hala produkcyjna została zaprojektowana w taki sposób, że będzie w stanie wytrzymać takie dodatkowe obciążenie.
NAWIGACJA WÓZKÓW SAMOJEZDNYCH
Ze względu na elastyczność zastosowań AGV stanowią szybko popularyzującą się grupę urządzeń w fabrykach motoryzacyjnych. Wózki samojezdne wymagają nawigacji i zarządzanie ruchem. Wyróżnić można wiele sposobów nawigowania AGV. Przykładem są metody: pętli indukcyjnej, pętli magnetycznej, optyczna, laserowa, ultradźwiękowa i w oparciu o system GPS.
W przypadku użycia pętli indukcyjnej pod podłogą umieszcza się kabel. Przepływ prądu elektrycznego wytwarza dookoła niego pole magnetyczne, którego natężenie mierzy układ odbiorczy w AGV. Sterownik koryguje kierunek, w jakim pojazd się przemieszcza, tak by wartość ta była jak największa. Metoda ta jest niezawodna i dokładna, lecz położenie przewodu pod podłogą może być kosztowne. Trudna jest również późniejsza modyfikacja trasy.
Alternatywą jest metoda pętli magnetycznej, w której wykorzystuje się namagnesowaną taśmę naklejaną na podłodze. Jej zalety to: prosta i niedroga instalacja oraz łatwa modyfikacja ścieżki. Niestety, taśma magnetyczna nie jest trwała ani odporna na uszkodzenia. Wykorzystuje się też skanery laserowe, które montuje się na dachu kabiny wózka. Skanując pomieszczenie, wykrywają znaczniki zamocowane na ścianach. Metoda ta jest dokładna, a trasę można łatwo zmienić. Znaczniki muszą być jednak umieszczone na jednakowej wysokości i cały czas znajdować się w zasięgu skanera.
Jak się produkuje opony?
Transport opon Niektóre z zagrożeń, np. te związane z ostrymi zakończeniami elementów transportujących, są wspólne dla opon zielonych i tych już po wulkanizacji. Dlatego trzeba sprawdzić przenośnik pod kątem występowania w nim nieosłoniętych śrub, kantów i ostrych połączeń pomiędzy jego segmentami. W przypadku obu typów opon występuje też bardzo duże tarcie, dlatego trudno przemieszczają się po przenośniku, wzdłuż i w poprzek taśmociągu. Jeśli chodzi o same opony surowe, to przede wszystkim nie powinny się ze sobą stykać. Ponadto ze względu na charakterystyczny "spodkowaty" kształt mogą się przewracać na pochyłościach (lepiej nie przekraczać 30° nachylenia / wzniesienia ) i się zapadać. Dlatego trzeba odpowiednio dobrać wysokość, na której umieszcza się czujnik na przykład zliczający opony tak, aby wykrywał ich obecność niezależnie od tego, czy się zapadły, czy nie. Trzeba pamiętać, że nieruchome przenośniki rolkowe mogą pozostawić na ich powierzchni wcięcia. Aby z kolei uniknąć jej ścierania się w przypadku, gdy opony podczas transportu przesuwają się z jednego przenośnika na drugi, trzeba dopilnować, żeby taśmy obu tych urządzeń poruszały się z jednakową prędkością. Jeżeli chodzi o gotowe opony, to są większe, mają wyższą temperaturę, a typowa prędkość ich przenoszenia wynosi 30÷60 metrów na minutę. Mogą się też ze sobą stykać. Opony najczęściej są transportowane za pomocą przenośników: z modułowymi pasami z tworzyw sztucznych, które charakteryzuje wytrzymałość i łatwość konserwacji, z pasami z tkanin, które z kolei są tańsze od modułowych, rolkowych i grawitacyjnych. |
ZARZĄDZANIE RUCHEM AGV
Aby system bazujący na AGV działał, a między wózkami nie dochodziło do kolizji, konieczne jest sterowanie ruchem tych pojazdów. Można to zrealizować centralnie - wówczas główny system zbiera informacje o położeniu poszczególnych wózków i nadzoruje ich ruch. W przypadku decentralizacji pojazdy komunikują się bezpośrednio między sobą - gdy określony wjeżdża do danej strefy, wysyła informację o tym do pozostałych, które zatrzymują się na jej obrzeżach do czasu uzyskania potwierdzenia, że jest pusta.
Jeżeli nie korzysta się z systemu zarządzania ruchem, wózki samojezdne chroni się przed kolizjami, montując w nich czujniki. W razie wykrycia przez nie przeszkody, AGV jest od razu zatrzymywany. Pozwala to na pracę wózków w większym zagęszczeniu, aczkolwiek w przypadku, gdy ścieżki ruchu są gęste i skomplikowane, może całkiem sparaliżować ich pracę.
APLIKACJE PRZENOŚNIKÓW I WÓZKÓW SAMOJEZDNYCH
Zadania, jakie realizują wózki samojezdne oraz przenośniki, można generalnie podzielić na cztery grupy. Do pierwszej zalicza się dowóz materiałów produkcyjnych z miejsca ich odbioru do magazynu, a do drugiej ich transport z miejsca przechowywania do hali produkcyjnej.
W takim zastosowaniu sprawdzają się na przykład holownicze AGV, równocześnie ciągnące wiele przyczep. Jest to efektywniejsze rozwiązanie niż przewóz ładunku każdej z nich oddzielnym wózkiem.
W transporcie wewnątrz hali produkcyjnej korzysta się również z wózków pojedynczego załadunku w postaci platformy, na której umieszcza się ładunek. Wyróżnia je kompaktowa konstrukcja, duża ładowność oraz zwrotność.
Do trzeciej grupy zadań zalicza się transport wyrobów pośrednich, na przykład części karoserii, pomiędzy różnymi stanowiskami, na przykład z prasy tłoczącej na stanowisko spawania, a stamtąd do malarni. Wówczas korzysta się z przenośników naziemnych i podwieszanych. Do ostatniej kategorii należy transport gotowych pojazdów, na przykład na platformach o odpowiednio dużym udźwigu.
Wybór środka transportu i warunków, w jakich przebiega, zależy od specyfiki przewożonego wyrobu. Wyjaśniamy to w ramce na przykładzie opon.
Przyszłość jest pełna wyzwań
Według Capital IQ przez ostatnich pięć lat średni coroczny TSR w branży samochodowej wyniósł zaledwie 5,5%. Dla porównania, inwestując w tym samym czasie w spółki z S&P 500, można było uzyskać TSR o wartości blisko 15%. Drugim wskaźnikiem jest ROIC (Return On Invested Capital). W 2016 roku w przypadku największych przedsiębiorstw w przemyśle samochodowym wyniósł on zaledwie 4%. Branża ta nie jest zatem tak atrakcyjna dla inwestorów, jak wiele innych. Produkcja będzie drożeć Tymczasem jej potrzeby wraz z upowszechnianiem się samochodów podłączonych do Internetu, multimedialnych, a w przyszłości autonomicznych, będą rosnąć. Szacuje się, że koszt budowy aut nowej generacji, które będą naszpikowane elektroniką, czujnikami, z zainstalowanym specjalnym oprogramowaniem i nowoczesnymi systemami napędowymi może być nawet o 20% większy niż obecnie. Sam udział elektroniki w całkowitej wartości samochodu w ciągu dwóch lat zwiększy się do 20%. Dla porównania w 2015 roku wynosił on 13%. Dobrze ilustruje to przykład wyposażenia wnętrza samochodu, które dotychczas wnosiło mniej więcej stały wkład w całkowity koszt jego produkcji. W przyszłości to tam właśnie będzie instalowanych najwięcej urządzeń, które poprawią bezpieczeństwo oraz komfort jazdy, zapewnią dostęp do Internetu oraz rozrywkę. Przykłady to: ekrany dotykowe oraz wyświetlacze HUD (Head-Up Displays), prezentujące informacje na specjalnej szybie bez zasłaniania widoku. W przypadku samochodów autonomicznych zmieni się również sposób organizacji przestrzeni wewnątrz auta. Na przykład przednie siedzenia zostaną odwrócone przodem do tylnych. Mogą również zostać obrócone w kierunku szyb, które pełnić będą funkcję ekranów. Jak producenci będą sobie radzić? Najlepiej w nowej rzeczywistości odnajdą się zatem ci producenci aut, którzy będą potrafili jak najefektywniej wykorzystać ograniczone zasoby kapitałowe. Ułatwi to m.in. łączenie sił przez zawieranie transakcji fuzji czy przejęć. Korzystna może się również okazać standaryzacja w zakresie pewnych komponentów, na przykład elementów systemu napędowego. Nie są one dla większości klientów tym wyróżnikiem, który ma wpływ na decyzję o wyborze konkretnego modelu samochodu, natomiast producenci mogą sporo zaoszczędzić, łącząc siły w zakresie R&D czy zakupu materiałów. Opłacać może się też korzystanie z usług firm zewnętrznych w zakresie nowej funkcjonalności aut, na przykład oprogramowania dla pojazdów autonomicznych. Zamiast angażować siły i środki w jej rozwój, taniej będzie skorzystać z oferty przedsiębiorstw wyspecjalizowanych w danej dziedzinie. |
KONTROLA JAKOŚCI I POMIARY
Linie produkcyjne w przemyśle motoryzacyjnym stanowią nagromadzenie różnego typu sensorów. Ich podstawowym zastosowaniem jest sterowanie maszynami zautomatyzowanymi oraz robotami przemysłowymi. Ważną ich aplikacją jest również monitorowanie jakości. Można podać wiele przykładów dla obu tych zastosowań.
Przykładowo na stanowisku wytłaczania części karoserii montuje się optyczne czujniki grubości, które kontrolują, czy do prasy nie są jednocześnie ładowane po dwa arkusze. Na wcześniejszym etapie sensory tego typu znajdują zastosowanie w operacji rozcinania na arkusze taśmy metalowej, którą rozwija się ze szpul. W tym przypadku wykrywają one znaczniki na taśmie, a informacja o tym jest przesyłana do sterownika piły. Jeszcze wcześniej w miejscu, gdzie szpule są rozwijane, mierzy się ich grubość. Dzięki temu można regulować szybkość ich rozwijania, tak żeby zapewnić stałe dostawy materiału do prasy.
INSPEKCJA SPAWANIA, CZUJNIKI W LAKIERNI
Z kolei systemy wizyjne znajdują zastosowanie nie tylko w detekcji obecności danej części na danym stanowisku, ale i w rozpoznawaniu, jaki jest to element na podstawie jego dodatkowych cech, takich jak otwory czy nacięcia. Czujniki laserowe z kolei są wykorzystywane do pomiaru kształtu spawu, jego wysokości i szerokości oraz kąta, pod jakim zostały połączone zespawane części.
Kurtyny świetlne natomiast na przykład w malarni umożliwiają ustalenie położenia nadwozia transportowanego na przenośniku. Na podstawie tej informacji robot malujący przemieszcza się w odpowiednie miejsce. Następnie systemy wizyjne sprawdzają jakość powłoki malarskiej i ogólnie monitorują nadwozie pod kątem uszkodzeń i niedoróbek. Poprawność jego montażu sprawdza się również za pomocą czujników laserowych mierzących odległości.
Z kolei w montażu siedzeń wykorzystuje się podnośniki, które unoszą siedziska na wysokość odpowiednią do ich podniesienia przez robota. Jest ona kontrolowana za pomocą enkodera współpracującego ze sterownikiem windy.
|
MONTAŻ SZYB, WYKORZYSTANIE RFID
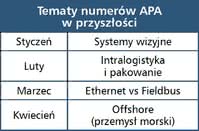
Tematy numerów APA w przyszłości
Czujniki optyczne sprawdzają też to, czy chwytak robota odpowiednio podniósł szybę. Następnie po tym, jak robot przeniesie ją w pobliże okna, sensory odległości kontrolują odległość, na jaką się do niego zbliżył.
Przed zamontowaniem sprawdzić trzeba również samą szybę. Na tym etapie systemy wizyjne i czujniki optyczne wykrywają m.in. to, czy szyba ma przewód grzejny i czy została pokryta powłoką ochronną przed promieniami UV.
Natomiast na stanowisku wkręcania śrub mocujących koła system wizyjny wykrywa otwory. Na tej podstawie kontroler robota pozycjonuje jego ramię wyposażone we wkrętak.
Na wielu stanowiskach montowane są również czytniki tagów RFID. Znaczniki takie ułatwiają identyfikację podzespołów, kontrolowanie ich przepływu, jak również poprawności ich montażu. Sprawdza się w ten sposób na przykład, czy na stanowisko montażu szyb i kół dotarły te właściwe dla danego modelu aut. Wcześniej, w lakierni trzeba się też upewnić, czy wybrano właściwy kolor do pomalowania danego nadwozia.
Monika Jaworowska
Fotografia tytułowa (od lewej):
1) Produkcja taśmowa samochodów Ford T (lata 20. zeszłego wieku)
2) Fiat Auto Poland Bielsko-Biała - ostatnie momenty produkcji Fiata 126p (wrzesień 2000)
3) Zrobotyzowana z wykorzystaniem robotów Kuka linia produkcyjna firmy Audi
4) Produkcja modelu Tesla S w fabryce Tesla Factory we Fremont (USA)