Nawigacja laserowa w AGV
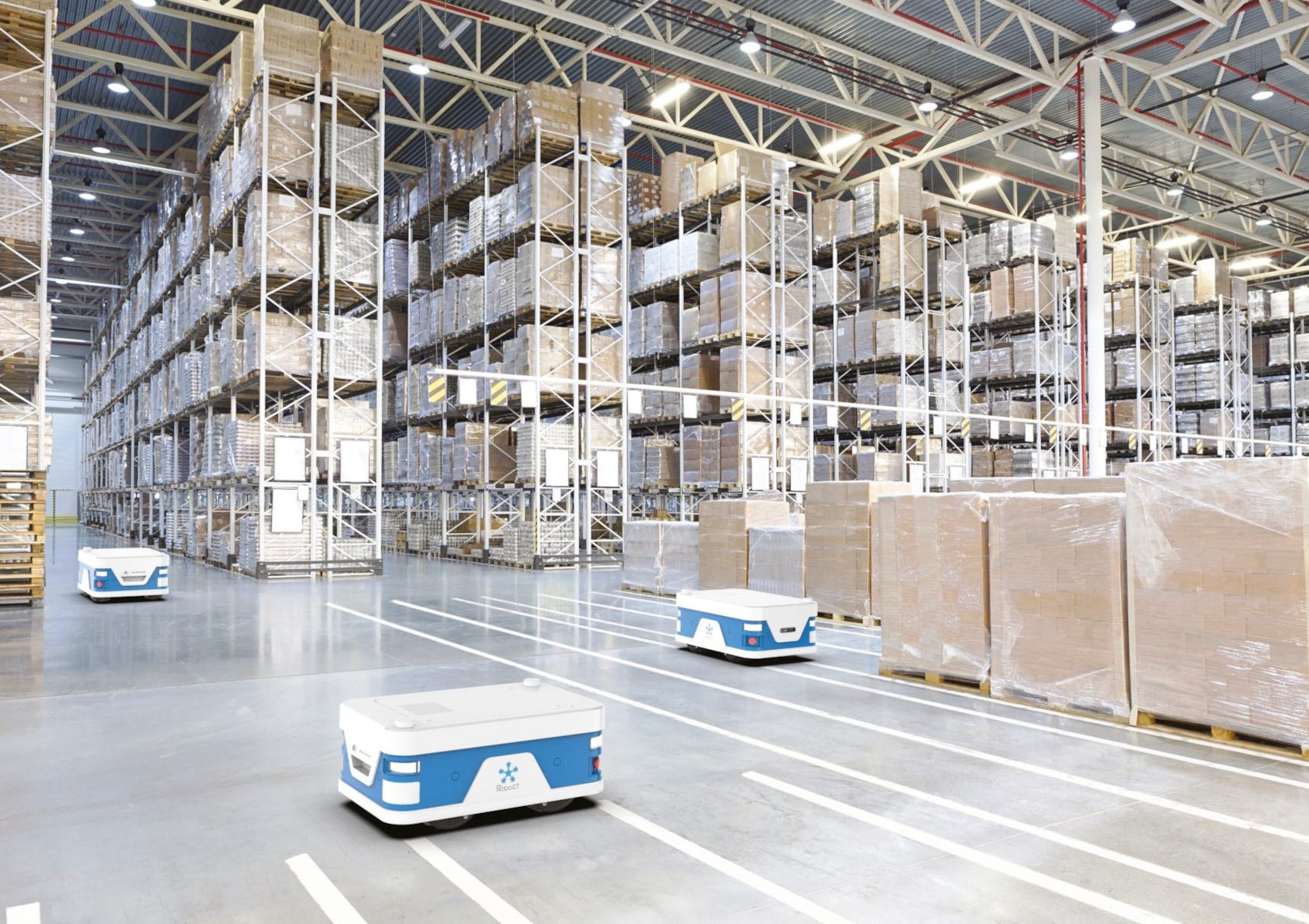
W celu wyznaczenia na terenie obiektu tras, po których wózek samojezdny będzie się poruszał, należy rozmieścić znaczniki rozpoznawane przez AGV. Różnią się one w zależności od metody nawigacji. Najpopularniejsze to: z pętlą indukcyjną, z pętlą magnetyczną i laserowa.
W ostatniej wózek jest wyposażony w montowany na maszcie skaner laserowy, zaś znaczniki (reflektory) są mocowane na ścianach. Laser emituje dookólnie ciągłą wiązkę modulowanego światła. Promieniowanie odbija się od reflektorów, które znajdują się w obszarze roboczym AGV.
Czas powrotu wiązki odbitej jest mierzony w skanerze, co pozwala wyznaczyć odległość wózek–znacznik. Do dalszych obliczeń potrzebny jest dystans od trzech reflektorów. Wówczas metodą triangulacji można wyznaczyć współrzędne pojazdu. Algorytmy zaimplementowane w kontrolerach wózków w obliczeniach biorą pod uwagę również inne zmienne, m.in. prędkość jazdy. Pozwala to wyznaczyć pozycję wózka AGV z dużą precyzją. Jest ona stale korygowana z częstością, w zależności od modelu, nawet kilkudziesięciu razy na sekundę.
Dokładność metody laserowej jest uwarunkowana sposobem montażu znaczników – powinny być umieszczone na jednakowej wysokości oraz cały czas znajdować się w zasięgu skanera. Wyróżnia się dwa ich typy: płaskie i cylindryczne. Pierwsze cechuje prostota konstrukcji i niższa cena. Są ponadto łatwe do zamocowania – można je na przykład przykleić. Montaż cylindrycznych jest natomiast trudniejszy, gdyż trzeba obliczyć zakładowai, zwykle przykręcając je do ściany, zachować stały punkt środkowy.
Nawigacja laserowa jest zalecana, gdy wymagana jest duża dokładność pozycjonowania. Jest to również najefektywniejsza metoda w przypadku rozległych obiektów i tras o skomplikowanym rozkładzie.
W metodzie z pętlą indukcyjną z kolei pod podłogą umieszcza się kabel. Na skutek przepływu prądu elektrycznego dookoła przewodu wytwarzane jest pole magnetyczne. Wózek, który jest wyposażony w układ odbiorczy, mierzy jego natężenie. Sterownik dostosowuje kierunek, w którym AGV się przemieszcza, tak żeby wartość ta była jak największa.
W drugiej z wymienionych technik wykorzystuje się z kolei namagnesowaną taśmę naklejoną na podłogę. W tabeli 1 przedstawiamy zestawienie zalet i wad tych najpopularniejszych metod nawigacji wózków samojezdnych.
Błażej Maćkowski
Turck
Cyfryzacja i rozwój handlu elektronicznego są motywacją do stosowania nowatorskich technologii w logistyce wewnętrznej. W pełni zautomatyzowane systemy zarządzania transportem dostarczają materiały do miejsca docelowego w sposób autonomiczny i wydajny – niezależnie od tego, czy są używane w zastosowaniach związanych z produkcją, kompletacją czy wysyłką. Umożliwiają to moduły sieciowe o IP67 z serii TBEN i TBPN ze zdecentralizowaną logiką sterowania. Przenosząc wymaganą inteligencję bezpośrednio do środowiska systemu przenośników, zapewniają ulepszenia, takie jak znaczne skrócenie czasu uruchamiania nowych zakładów.
Przemysł 4.0 spowodował trend w inwestowanie w nowe technologie. Aby park maszynowy mógł zachować swoją efektywność, stosuje się różne algorytmy optymalizujące procesy konserwacji. Jednym z nich jest predykcyjne utrzymanie ruchu, które w większości wypadków jest także najtrafniejszym rozwiązaniem. Główną rolę w podejściu predykcyjnym grają czujniki. Na podstawie informacji przez nie dostarczanych można podjąć decyzję, kiedy należy przeprowadzić prace serwisowe. System kontroli wibracji i temperatury firmy Turck oferuje możliwość monitorowania pracy krytycznych napędów. Jego sercem jest czujnik QM42 montowany na monitorowanym urządzeniu. Na podstawie dostarczanych przez niego informacji można ocenić m.in: luzy i złe wyważenie, uszkodzenia i nieprawidłowości w łożyskach tocznych czy też niewyosiowania – np. w układnicach magazynowych.
Automatyzacja procesów logistycznych trwa już od kilkunastu lat, ale rok 2020 i początek pandemii COVID-19 spowodował gwałtowne przyśpieszanie. Jako dostawcy automatyki przygotowywaliśmy się do tego momentu wcześniej. Dział R&D firmy Turck rozwijał rodzinę modułów I/O o stopniu ochrony IP67, które idealnie wpisują się do zbierania sygnałów z przenośników transportu wewnętrznego, sorterów i innych systemów dystrybucyjnych. Zauważyliśmy też trend w mniejsze inwestycje z szybką stopą zwrot takich jak Pick to Light, Call for Parts. |
Autonomiczność AMR
Autonomiczność robotom mobilnym zapewnia połączenie najnowszych rozwiązań z zakresu technik pomiarowych, obliczeniowych i analitycznych. Czujniki, w które zwykle wyposaża się AMR, to: skanery laserowe 2D (LiDAR), kamery 3D, żyroskopy, akcelerometry, enkodery, które są montowane w kołach, sensory temperatury, magnetometry, czujniki środowiskowe. Każdy wykorzystywany jest w jednej albo w większej liczbie zadań. Na przykład skaner laserowy jest najczęściej używany do mapowania terenu, nawigacji (lokalizacji i omijania przeszkód) oraz wykrywania obiektów, na przykład stacji dokujących. Kamery 3D są natomiast przeważnie wykorzystywane do nawigacji (unikania przeszkód).
Lokalizacja w AMR
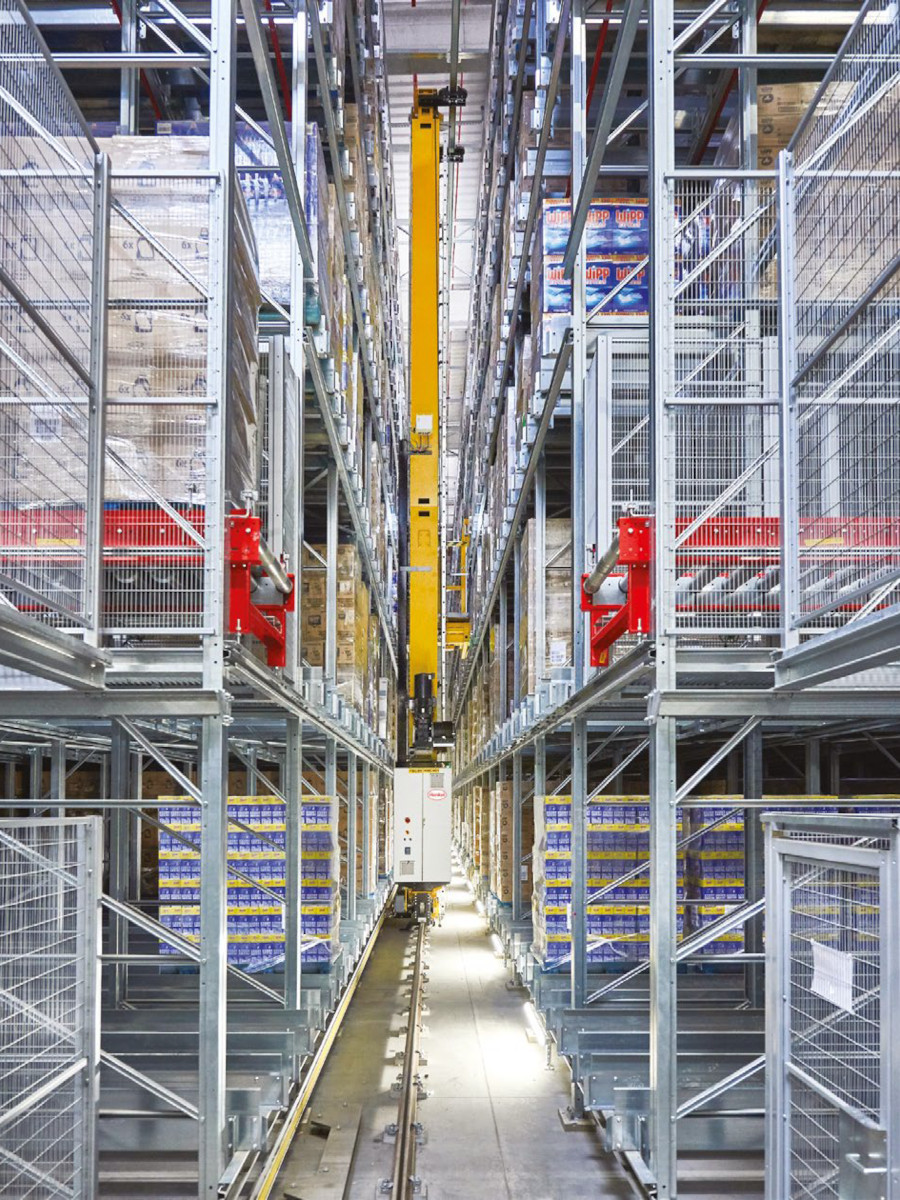
W autonomicznych robotach mobilnych implementuje się różne techniki orientacji w przestrzeni. Przykład to odometria, która pozwala oszacować zmianę położenia AMR w czasie względem miejsca startu. Ponieważ za każdym razem jest to pozycja jedynie przybliżona, błędy w jej określaniu, spowodowane m.in. poślizgiem kół i ich ścieraniem się postępującym w miarę użytkowania, z czasem się kumulują. Aby ten efekt ograniczyć, implementuje się algorytm filtru Kalmana, korygujący odczyty w oparciu o obserwację zaszumionych i obarczonych innymi niedokładnościami wyników pomiarów, głównie z żyroskopów oraz enkoderów. Odometria jest w AMR wykorzystywana jako jedyne źródło danych o położeniu wtedy, kiedy niemożliwe jest jego wyznaczanie za pomocą skanera laserowego.
LiDAR jest z kolei używany w lokalizowaniu przez dopasowanie skanu do mapy obiektu, po którym porusza się autonomiczny robot mobilny. W jego wyniku szacunkowe, niepasujące współrzędne zostają odrzucone. Te zaś, które z określoną dokładnością pasują, podlegają uśrednieniu w ramach implementacji algorytmu filtru cząsteczkowego. W przypadku, gdy dopasowanie się nie powiedzie, AMR zgłasza problem z ustaleniem własnego położenia. Taka sytuacja zachodzi na przykład, gdy w otoczeniu, w którym przemieszcza się robot, nie występuje wystarczająca liczba punktów charakterystycznych, umożliwiających przeprowadzenie porównania. Przykładem jest rozległa otwarta przestrzeń.
W mapowaniu w AMR wykorzystuje się SLAM (Simultaneous Localization and Mapping), metodę polegającą na dopasowywaniu skanów laserowych podczas przemieszczania się robota. Ponieważ w tym zakresie stosowane są różne algorytmy, przed wyborem modelu robota trzeba się upewnić, że ten konkretny sprawdzi się w danych warunkach.
Jaki jest potencjał RTLS?RTLS (Real Time Location System) to systemy lokalizacji i identyfikacji czasu rzeczywistego. Ich najważniejszym komponentem są czujniki, które zwykle charakteryzują małe rozmiary oraz mały pobór energii umożliwiający ich długotrwałe zasilanie bateryjne. Są to na przykład tagi RFID, a coraz częściej również w technologii transmisji szerokopasmowej Ultra-Wideband (UWB). Te sensory są mocowane do obiektów, które mają być śledzone. Sygnał przez nie emitowany jest odbierany przez czujniki rozmieszczone na obszarze, który podlega nadzorowi systemu RTLS, przeważnie mocowane na stałych elementach pomieszczeń. Informacje przez nie pozyskane są analizowane w specjalnym oprogramowaniu – na przykład na podstawie kąta padania lub czasu propagacji sygnału wyznaczane jest położenie oznakowanego obiektu. Systemy RTLS umożliwiają namierzanie i monitorowanie przepływu produktów i półproduktów na wszystkich etapach produkcji, obróbki, magazynowania i często także częściowo dystrybucji. Są one przeważnie zintegrowane z systemami WMS i ERP. To jednak nie jedyne zastosowanie technologii RTLS – w logistyce oraz przemyśle ma ona znacznie większy potencjał, m.in w zakresie poprawy bezpieczeństwa. Tę systemy lokalizacji i identyfikacji czasu rzeczywistego są w stanie zapewnić na kilka sposobów. Mogą przykładowo zapobiegać kolizjom między pracownikami a maszynami lub pojazdami, jak wózki widłowe czy AGV/AMR, ostrzegając personel o prawdopodobieństwie zderzenia na podstawie informacji o jego aktualnym położeniu i informować o wkroczeniu w strefę niebezpieczną, na przykład w zasięgu ostrego narzędzia włączonego urządzenia. Za ich pośrednictwem można także przeprowadzić zdalny przegląd osobistego wyposażenia pracownika, sprawdzając, czy ma on na sobie cały wymagany na danym stanowisku sprzęt ochronny (buty robocze, kask). RTLS zapewniają bezpieczeństwo również w sytuacjach awaryjnych. Jeżeli na przykład zbierają i poddają analizie dane z czujników monitorujących parametry życiowe pracowników, mogą wykryć potrzebę pomocy medycznej lub ewakuacji. Pozwalają też sprawdzić, którzy pracownicy są już w bezpiecznym miejscu, a którzy jeszcze pozostają w strefie zagrożenia. |