Jak dobrać stopień ochrony obudowy?
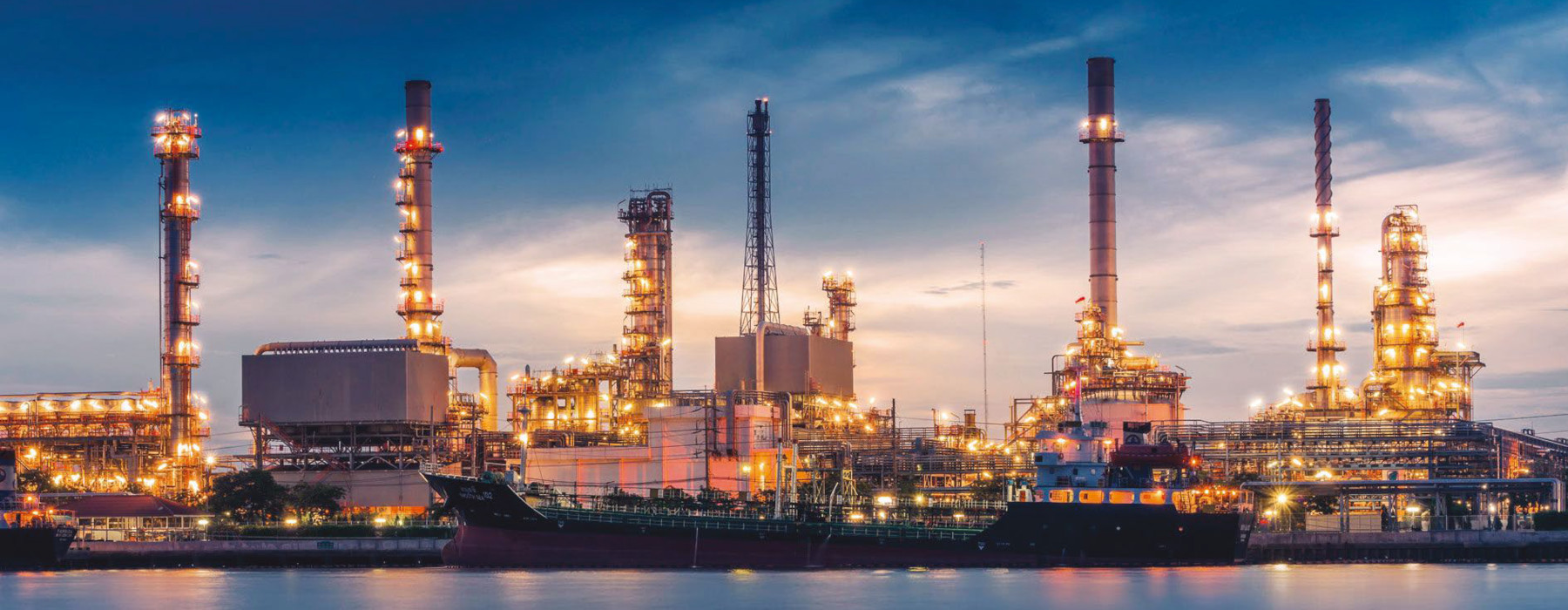
Wymagany w danym zastosowaniu stopień ochrony, jaki zapewniać powinna obudowa, zależy od warunków, w jakich będzie ona użytkowana. Przykładem branży, w której na szczelność osłon wyposażenia linii produkcyjnych trzeba położyć szczególny nacisk, jest przemysł spożywczy. Szczególnej uwagi wymagają maszyny pakujące. W produkcji oraz przetwórstwie żywności urządzenia te są narażone na pracę w otoczeniu zakurzonym, mokrym i przy występowaniu zarówno pyłów, jak i płynów, z którymi ich podzespoły mogą wejść w kontakt. Silne pylenie występuje zwłaszcza w pakowaniu takich produktów, jak przekąski (czipsy, ciastka) i w postaci sypkiej (kawa, mąka czy cukier). Wprawienie ich w ruch podczas przesypywania do opakowań sprawia, że w powietrzu unoszą się ich cząstki. Choć częścią linii pakowania są urządzenia do usuwania pyłów, drobin produktów nie można całkiem wyeliminować. Dlatego liczyć się trzeba z tym, że mogą się przedostawać do niewłaściwie uszczelnionych osłon. By temu zapobiec, maszyny pakujące produkty sypkie powinny być chronione obudowami ze stopniem ochrony co najmniej IP5x lub IP6x. Stopień zabezpieczenia przed wnikaniem wilgoci w tym zastosowaniu aż tak wysoki być nie musi.
Odwrotnie jest w przypadku maszyn do obróbki i pakowania na przykład wyrobów mięsnych i nabiału – linie produkcyjne tego typu produktów to zdecydowanie środowiska mokre, których wyposażenie narażone jest na kontakt z wodą, środkami czyszczącymi i płynami z samych wyrobów. Dlatego jego obudowy powinny być zabezpieczane przed ich wnikaniem – w tym zastosowaniu minimalny zalecany stopień ochrony to IPx5 do IPx8. Pyły zwykle nie stanowią problemu, zatem stopień zabezpieczenia przed nimi nie musi być wysoki. Jeżeli natomiast otoczenie maszyny pakującej jest zarówno zakurzone, jak i wymaga zmywania, odpowiedni stopień ochrony to co najmniej IP55 do IP68.
Jak chronić czujniki w układach hydraulicznych?Układy hydrauliczne są częścią maszyn pracujących w trudnych warunkach m.in. w tartakach, odlewniach, hutach, ciężkim sprzęcie mobilnym. Ich newralgicznym elementem są sterowniki oraz czujniki pracujące w pętli sprzężenia zwrotnego. Aby zapewnić bezproblemowe działanie układów hydraulicznych trzeba dobrać te komponenty z uwzględnieniem warunków, w jakich będą pracować. W tym zastosowaniu wykorzystywane są sensory położenia. Dostarczają one informacji o tym, czy tłoczysko jest do końca wysunięte, czy całkowicie wsunięte albo mierzą położenie tłoka w sposób ciągły. Pierwsze to zwykle czujniki Halla. Czujniki skoku drugiego typu to z kolei na przykład: LVDT (transformatorowe przetworniki przemieszczeń liniowych), sensory magnetostrykcyjny i enkodery optyczne. Dla każdego typu czujnika problem stanowi wysoka temperatura. O taką nietrudno, na przykład w przemyśle stalowym w pobliżu pieców, urządzeń do odlewania i linii do walcowania na gorąco. Żeby zabezpieczyć sensor przed tym czynnikiem, uwzględnić trzeba przeważnie wszystkie możliwe sposoby przekazywania ciepła, czyli przewodzenie, konwekcję, promieniowanie. By zmniejszyć ilość ciepła przewodzonego, czujnik trzeba umieść możliwie jak najdalej od jego źródła albo na drodze przepływu ciepła wstawić barierę (izolator termiczny). Aby zmniejszyć wpływ konwekcji i promieniowania, sensory umieszcza się w osłonach. Sam czujnik powinien być też przystosowany do pracy w przewidywanym w danym zastosowaniu przedziale temperatur. Uwagi wymaga oprócz tego okablowanie – warto rozważyć wykorzystanie kabli w osłonach na przykład z PTFE, odpornych na temperatury do +200°C. Zastanowić się trzeba także nad ich podłączeniem. Na przykład można łączyć krótki kabel od czujnika, bezpośrednio narażony na działanie temperatury, z dłuższym kablem sterownika. Dzięki temu, jeśli ten pierwszy się uszkodzi tylko on będzie wymagał wymiany, w przeciwieństwie do sytuacji, w której należałoby wymienić jeden długi kabel przez jego uszkodzenie przy samym czujniku. Dostępne są też cylindry hydrauliczne chłodzone wodą, obniżającą temperaturę sensorów. Skrajnie niskie temperatury też są problemem – takich, poniżej –40°C można się spodziewać w branży wydobycia ropy i gazu w rejonach arktycznych. W tych warunkach tworzywa sztuczne w uszczelkach, izolacjach kabli, osłonach stają się kruche. Zmieniają się też parametry podzespołów elektronicznych. Rozwiązaniem jest zastąpienie „zwykłych” specjalnymi niskotemperaturowymi tworzywami sztucznymi, zastosowanie układu podgrzewania albo przełączanie elektroniki na zasilanie ciągłe poniżej określonej temperatury, dzięki czemu ciepło w niej wydzielane będzie ją ogrzewać. Czujniki w siłownikach hydraulicznych zabezpiecza się też przed uszkodzeniem w wyniku uderzenia. W tym celu stosuje się osłony – wadą tego rozwiązania jest to, że może się zdarzyć, że zdjęta w czasie serwisowania osłona nie zostanie nałożona z powrotem. Alternatywą są czujniki kompaktowe wbudowane w siłownik. Jeżeli chodzi o ochronę przed wnikaniem płynów i pyłów, w tym zastosowaniu wybiera się zwykle sensory w obudowie ze stopniem ochrony IP68, IP69K, a nawet hermetycznie spawane. Ważne jest, by kod obudowy był taki sam, jak kabla – często błędnie na przykład czujnik w obudowie z IP69K zostaje podłączony za pomocą standardowego kabla IP65. Kabel należy też zabezpieczyć dodatkowo przed przerwaniem i przetarciem. Przed korozją chronią obudowy ze stali nierdzewnej 303 i 304, a w środowisku ze słoną wodą albo mgłą solną ze stali 316L. Na wypadek uszkodzenia sensorów pomimo zastosowanych ochronnych rozwiązań konstrukcyjnych warto się też zastanowić nad wykorzystaniem czujników nadmiarowych. |