Kompletowanie serwonapędów – jak wybrać silnik?
Przed wybraniem silnika należy zapoznać się z wymaganiami aplikacji. Ważną kwestią jest m.in. dobranie właściwego stosunku bezwładności (inercji) obciążenia do bezwładności silnika. Przyjmuje się, że optymalna proporcja to 10:1 lub mniej, czyli że bezwładność silnika powinna stanowić co najmniej 1/10 bezwładności obciążenia. W praktyce spotyka się napędy, w których proporcji ta wynosi 5:1, 2:1 lub 1:1, a nawet mniej. Im mniejszy jest ten stosunek, tym wydajność silnika jest większa. Im dokładniej dopasowane są inercja obciążenia i bezwładność silnika, tym szybsza, płynniejsza i dokładniejsza jest także kontrola położenia tego pierwszego.
Jeśli natomiast nie są to kwestie najważniejsze, bezwładność silnika może stanowić nawet 1/100 bezwładności obciążenia. Nierzadkie są także proporcje większe niż 100:1. Generalnie jednak im ten stosunek jest większy, tym trudniejsze jest strojenie układu regulacji. Zbyt mała wartość tego współczynnika może się natomiast wiązać z koniecznością użycia dużego, ciężkiego, a przez to przeważnie też droższego silnika. Zatem wybór optymalnej wartości stosunku bezwładności obciążenia do inercji silnika wymaga uwzględniania specyfiki aplikacji.
Mając do wyboru kilka silników, które zapewniają odpowiedni stosunek inercji, przed podjęciem ostatecznej decyzji sprawdzić trzeba, czy dany model zapewni również wystarczającą prędkość i odpowiedni moment obrotowy. W tym celu przeanalizować należy charakterystykę silnika, która określa wzajemną zależność obydwu tych wielkości. Informacje odczytane z tego wykresu trzeba odnieść do wymogów aplikacji, które mogą być opisane na przykład krzywymi profilów ruchu: prędkości oraz momentu obrotowego w funkcji czasu. Często spotykany jest profil trapezowy.
Silniki w serwonapędachPopularne typy silników w systemach sterowania ruchem to: skokowe, szczotkowe i bezszczotkowe prądu stałego (najpopularniejsze) oraz asynchroniczne prądu przemiennego. Pierwsze mogą pracować z pełnym momentem w stanie spoczynku, a zarazem charakteryzuje je przystępny rozmiar i waga. Niestety im większa prędkość, tym ich moment napędowy jest mniejszy. Maksymalna prędkość sięga kilku tysięcy obr./min przy bardzo małym momencie obrotowym, moc tego typu silników wynosi natomiast do kilkuset watów. Do ich wad zalicza się również wytwarzanie hałasu oraz wibracje. Niepożądane są szczególnie te ostatnie, wpływające na żywotność mechanicznych komponentów systemu. Żeby ograniczyć drgania, stosuje się specjalne techniki sterowania i korzysta z amortyzatorów. Środki te jednak nie rozwiązują problemu drgań całkowicie. ![]() Szczotkowe silniki prądu stałego sprawdzają się w szerokim zakresie aplikacji, od pozycjonowania po regulację prędkości i momentu obrotowego. Dostępne są w wersjach o mocach rzędu kilku kW i prędkościach przekraczających kilka tysięcy obr./min. Pracują równo i cicho. Słabym punktem tego typu silników są szczotki, które z czasem zużywają się, przez co muszą być okresowo wymieniane. Ich pracy towarzyszy też zjawisko powstawania łuku elektrycznego. Wadą szczotkowych silników DC jest także mały moment obrotowy w stosunku do ich wymiarów oraz wagi. Do najważniejszych zalet silników bezszczotkowych DC zalicza się: równą i cichą pracę i to, że nie wymagają mechanicznej komutacji. Ich maksymalna prędkość przekracza kilkadziesiąt tysięcy obr./min. Wytwarzają duży moment obrotowy, a przy tym ich wymiary i waga są akceptowalne w większości zastosowań. Niestety są droższe, ponieważ w celu uzyskania większego momentu obrotowego elementy ich konstrukcji są wykonane z magnesów ziem rzadkich (na przykład neodymowych lub samaro-kobaltowych). Ponadto, ponieważ komutacja silników tego typu jest realizowana elektronicznie, wymagają bardziej skomplikowanych i droższych wzmacniaczy. Z kolei dzięki prostej konstrukcji zaletą silników asynchronicznych jest długa żywotność i stosunkowo niski koszt. Rzadko są one stosowane w pozycjonowaniu, natomiast coraz częściej w aplikacjach z regulowaną prędkością i momentem obrotowym. |
Profil ruchu a charakterystyka silnika
W jego przypadku moment obrotowy na początku ma największą wartość, która jest wymagana, aby pokonać tarcie i wprawić w ruch nieruchome do tej pory obciążenie. Po osiągnięciu przez nie docelowej prędkości moment powinien być utrzymywany na określonym poziomie, potrzebnym do pokonania tarcia i podtrzymania wymaganej szybkości. By zatrzymać obciążenie, wytwarzany jest moment hamujący. Nie musi on już być tak duży, jak moment wytwarzany przy rozpędzaniu, gdyż w zatrzymaniu obciążenia pomaga tarcie. Na podstawie profilu ruchu wyznaczyć można dwie wielkości kluczowe przy wyborze odpowiedniego silnika: maksymalny oraz średni moment obrotowy.
Z kolei na charakterystyce momentu obrotowego silnika w funkcji jego prędkości wyróżnia się dwa obszary pracy: ciągłej oraz chwilowej. Z wykresu tego można oprócz tego odczytać kilka ważnych wielkości. Jedna z nich to znamionowy moment obrotowy. Jest to największy moment, jaki silnik wytwarza w sposób ciągły, przy prędkości znamionowej, ograniczony stopniem nagrzewania się silnika. Prędkość znamionowa natomiast to największa szybkość, przy której możliwy jest do uzyskania znamionowy moment obrotowy. Silnik może się co prawda obracać z prędkością większą niż znamionowa, jednak im szybsze obroty, tym mniejszy moment obrotowy wytwarza.
Jak nie przewymiarować silnika?
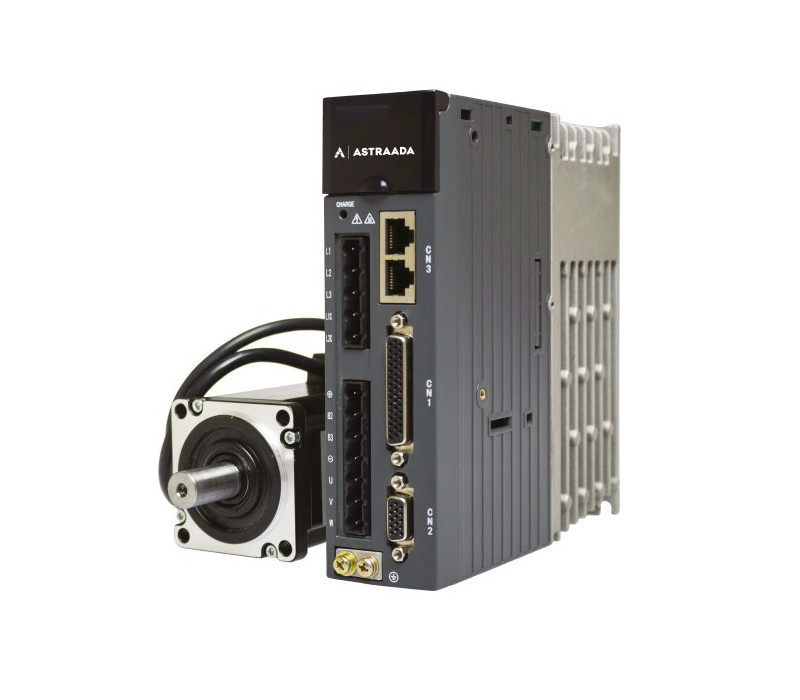
Jeśli wymagana kombinacja momentu obrotowego i prędkości wypada w obszarze pracy ciągłej silnika, oznacza to, że zapewnia on obydwie te wielkości przez cały czas pracy. Nie trzeba się zarazem obawiać, że może się wówczas przegrzewać. Jeżeli natomiast wymagana kombinacja momentu obrotowego i prędkości wypada w drugim obszarze pracy silnika, może je zapewnić jedynie przez określony czas. Po jego upływie zacznie się przegrzewać. Taki stan przeważnie aktywuje jego zabezpieczenia. Nie oznacza to jednak, że z tego modelu powinno się od razu zrezygnować. Jeżeli bowiem moment ten jest potrzebny tylko przez krótki czas, na przykład w czasie rozpędzania albo hamowania maszyny, taki silnik również może się w konkretnym zastosowaniu sprawdzić.
Podsumowując, jeżeli średni moment obrotowy wymagany w danym zastosowaniu wypada w obszarze pracy ciągłej, silnik został dobrany poprawnie. Jeśli z kolei maksymalny potrzebny moment obrotowy wypadnie w tym zakresie pracy, silnik z dużym prawdopodobieństwem przewymiarowano. Lepiej, jeśli maksymalny moment obrotowy jest osiągany chwilowo.