Jak się produkuje butelki pet?
Tytułowe opakowania wytwarza się z preform. Te zaś są produkowane w maszynach wtryskowych z tworzywa sztucznego w formie granulatu. W pierwszym kroku jest ono rozgrzewane do wysokiej temperatury, zazwyczaj rzędu kilkuset stopni Celsjusza. Powoduje to jego upłynnienie. Masa w takiej postaci jest wtryskiwana do formy, która nadaje jej wymagany kształt.
Proces produkcji butelek plastikowych w maszynach rozdmuchowych składa się z dwóch etapów. Najpierw preformy, które są automatycznie pobierane z zasobnika wbudowanego w rozdmuchiwarkę, są rozgrzewane w jej wewnętrznym piecu do wysokiej temperatury, rzędu kilkudziesięciu stopni Celsjusza. Następnie umieszcza się je w formie, która ma im nadać pożądany kształt. W kolejnym kroku następuje rozdmuch rozmiękczonej preformy powietrzem pod ciśnieniem. Wówczas zwiększa ona rozmiar, wypełniając formę. Dzięki temu, że zaraz potem zostaje schłodzona strumieniem zimnego powietrza kształt, który przyjęła, utrwala się.
![]() Liczba gniazd: 3, odległość między butelkami: 130 mm, maks. średnica szyjki: 42 mm, maks. wysokość butelki: 350 mm, min. pojemność butelki: 50 ml, maks. pojemność butelki: 300 ml, wydajność sztuk/ h: 4500, maks. ciśnienie rozdmuchu: 40 barów, technologia heat set do produkcji opakowań o podwyższonej temperaturze rozlewu, szyjki gwintów: standardowe i specjalne. ![]() Automatyczne płuczki butelek szklanych. System wtrysku jednorazowego. Płukanie wnętrza nowych butelek, bez zwilżania na zewnątrz. Filtrowanie wody. Wydajność: SA800 – 800 butelek/h, SA1500 – 1500 butelek/h. ![]() Dokładność dozowania: ± 0,25%, wydajność: 1200–4000 szt./h, typ transportera: płytkowy, powierzchnia transportera: tworzywo sztuczne, szerokość transportera: 60–160 mm, liczba nalewaków: 2–10 szt., typ nalewaków: wewnętrzne, zakres dozowania: 25 ml–5000 ml. ![]() Rodzaje opakowań: poduszki powietrzne, worki: z dnem, z fałdami, w kształcie czworościanu, łańcuchowe, zipper, z zaciskiem, z wstawką typu header, opcje zgrzewu: podwójny (produkty płynne), dziurkacz (okrąg, eurodziurka, rączka), poczwórny, profil niestandardowy, system informacji diagnostycznych, pneumatycznie regulowane pasy transportowe, automatyczne rozwarcie szczęki, gdy produkt jest uwięziony, obsługa zadrukowanych folii, detektor końca folii. ![]() Model CP180L: maks. udźwig: 160 kg, maks. zasięg: 3255 mm, liczba stopni swobody: 4, powtarzalność: ± 0,5 mm, zakres ruchu: JT1 ± 160°, JT2 +95° ~ –46°, JT3: +15° ~ –110°, JT4 ± 360°, prędkości: JT1 140°/s, JT2 125°/s, JT3 130°/s, JT4 400°/s. ![]() Robot z kontrolerem RC90 – 4 osie. Udźwig: 3 kg, zasięg: 400 mm (horyzontalny), 150 mm (wertykalny), długości ramion: J1 225 mm, J2 175 mm, orientacja: J4 +/- 360°, powtarzalność: J1, J2 ±0,01 mm, J3 ±0,01 mm, J4 ±0,01°, maks. zakres pracy: J1 ±132°, J2 ±141°, J3 150 mm, J4 ±360°, maks. szybkość na osiach: J1, J2 6000 mm/s, J3 1100 mm/s, J4 2600°/s, moment bezwładności nom./maks.: 0,005 / 0,05 kgm², typ montażu: podłogowy. ![]() igus Rynek od kilku lat napędzany jest przede wszystkim sytuacją na rynku pracy. Kiedy zestawimy brak pracowników z rosnącym popytem na produkcję, okazuje się, że automatyzacja staje się jedynym rozwiązaniem, by dotrzymać kroku konkurencji i rozwijać firmę. Jednocześnie pojawiają się kolejne, ekonomiczne rozwiązania – zarówno sprzętowe, takie jak szybkie i niedrogie roboty delta, łatwe w modyfikacji roboty kartezjańskie czy coraz popularniejsze coboty, jak i software’owe – np. zintegrowane sterowanie z interfejsem graficznym igus Robot Control, więc czas zwrotu z inwestycji skraca się. Wszystko to składa się na rozwój branży. Szczególny wzrost widzimy w przemyśle spożywczym – np. wśród producentów ciastek, gdzie stosunkowo nieduże zakłady zaczynają automatyzować pakowanie, by móc przekierować kilku pracowników do innych zadań. |
Mateusz Amroziński
FANUC Polska Pakowanie oraz paletyzacja produktów to procesy obecne w niemal każdej branży przemysłu. Cechują się coraz wyższą wydajnością, co eliminuje pracę ręczną. Z uwagi na to, że są to również procesy wymagające dokładności i zachowania wysokiego stopnia powtarzalności doskonale nadają się do robotyzacji. W ostatnich latach rośnie zapotrzebowanie na roboty wyspecjalizowane w realizacji tego typu zadań. Świadczą o tym m.in. statystyki IFR, obrazujące dostawy nowych robotów do fabryk, m.in. w Polsce. Operacje handlingowe, a w tym pakowanie, pick&place i paletyzacja, tworzą drugi po procesach montażu/demontażu obszar produkcji, gdzie najczęściej sięga się po roboty przemysłowe. Wzrost zainteresowania robotyzacją w ostatnich latach był napędzany koniecznością poszukiwania możliwości redukcji kosztów, zwiększenia elastyczności i skrócenia cykli produkcyjnych (pakowanie/ paletyzacja to procesy, bezpośrednio przekładające się na terminy i bezpieczeństwo dostaw produktów), a także konieczność realizowania planów produkcyjnych w obliczu nasilającego się niedoboru kadr. |
Michał SkorekStäubli Głównym aspektem napędzającym rynek w ostatnich latach jest niewątpliwie wciąż rosnący koszt utrzymania pracownika oraz do czasu pandemii problem ze znalezieniem wykwalifikowanej kadry. Dodatkowym aspektem jest również rosnąca dostępność maszyn i urządzeń tego typu, co pozytywnie wpływa na konkurencyjność cen a dokładnie ich obniżenie. |
Tomasz Szewczyk
Sitaniec W ostatnich latach w naszym kraju możemy zaobserwować duże zainteresowanie automatyzacją i robotyzacją w niemal wszystkich gałęziach przemysłu. Dzieje się tak głównie dzięki malejącemu bezrobociu oraz wzrostowi kosztów pracy. Największe ożywienie można zaobserwować w branżach tradycyjnie zatrudniających najwięcej pracowników: spożywczej, kosmetycznej, chemicznej. |
Piotr Kasiuk
Yaskawa Polska Ostatnimi czasy przemysł bardzo dynamicznie się rozwinął, wskutek czego dorósł do decyzji o wykorzystaniu maszyn w celu pakowania produktów. Kadra staje się obecnie coraz bardziej wykwalifikowana, pracownicy niechętnie pracują przy rutynowych i nużących czynnościach. Tutaj z pomocą przychodzą roboty przemysłowe oraz maszyny wykorzystywane w pakowaniu. Są to w zależności od procesu proste urządzenia wykonujące układanie, przenoszenie detali z miejsca na miejsce, ale także zaawansowane technologicznie maszyny wykorzystujące czujniki wizyjne 2D lub 3D do automatycznej detekcji rozmiarów pakowanego produktu, selekcji oraz decyzji. Najczęściej takie rozwiązania stosowane są w branży logistycznej i spożywczej. Tam, gdzie łańcuch dostaw pracuje najczęściej w myśl zasad Just in Time, każda sekunda opóźnienia wiąże się z katastrofalnymi skutkami. Zautomatyzowany i zrobotyzowany proces jest prostszy do kontroli i łatwiejszy w przewidywaniu, oczywiście jeśli założymy, że maszyny są poprawnie eksploatowane i serwisowane. |
Płukanie
Bez względu na to, czy opakowanie zostało wyprodukowane na miejscu, na przykład w rozlewni, czy zostało dostarczone przez zewnętrznego producenta, przed napełnieniem trzeba je umyć. Dzięki temu zapobiega się zanieczyszczeniu produktu zarazkami i drobinami, które osadzają się w opakowaniach podczas produkcji, transportowania, czy magazynowania. Jest to niepożądane ze względów sanitarnych, jak i wizerunkowych. Widoczne zabrudzenia, jak również te, które zmieniałyby wygląd, smak, zapach napoju, na przykład odbarwiając albo rozcieńczając go, zniechęcają bowiem do zakupu i wpływają negatywnie na reputację producenta.
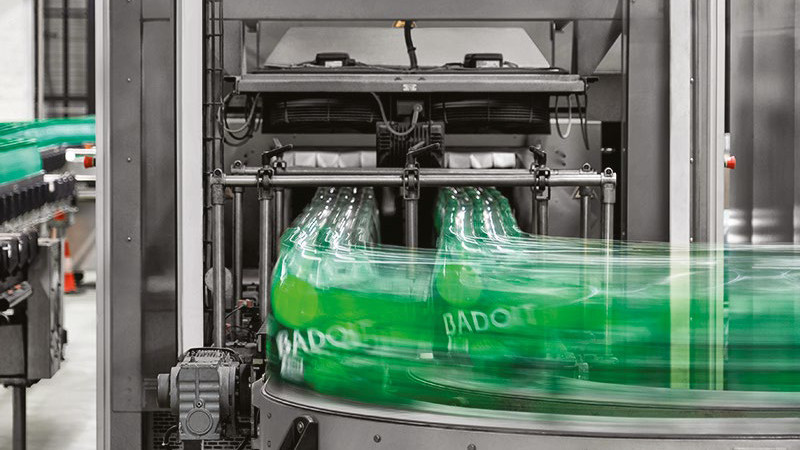
W tym celu linie pakowania uzupełnia się o płuczki. Stosuje się w nich różne czynniki czyszczące, zwykle albo w formie gazowej, albo w postaci płynnej. Ostatnim jest często woda. Czasami dodaje się do niej środki myjące i odkażające. Gazowe medium to zazwyczaj powietrze. Przedmuchiwanie nim generuje mniej odpadów – pozbyć się trzeba tylko zanieczyszczeń usuniętych z opakowania. W przypadku użycia płynnego czynnika myjącego również należy go zagospodarować, na przykład oczyszczając przed ponownym użyciem w płuczkach z jego zamkniętym obiegiem. Oprócz tego powietrze, wydmuchując zabrudzenia, nie pozostawia śladów.
W zakresie konstrukcji popularne są maszyny z chwytakiem podnoszącym opakowanie i odwracającym je do góry dnem. Jego wnętrze jest wtedy przedmuchiwane albo opłukiwane. Alternatywą są maszyny z dyszą, która bez odwracania opakowania zostaje wprowadzona do jego wnętrza. Jest ona rozmiarem dopasowana do otworu wlotowego, dzięki czemu go uszczelnia. Za jej pośrednictwem do środka butelki jest wprowadzane medium czyszczące.
Napełnianie
Po przedmuchaniu bądź opłukaniu opakowania są przekazywane dalej, do napełniarki. Rodzaj tej maszyny zależy od specyfiki produktu i tego, jaki efekt końcowy jest pożądany. W tym ostatnim chodzi o to, czy opakowania powinny być napełnione do jednakowego poziomu, czy taką samą ilością produktu, co jak się okazuje, nie jest ze sobą tożsame.
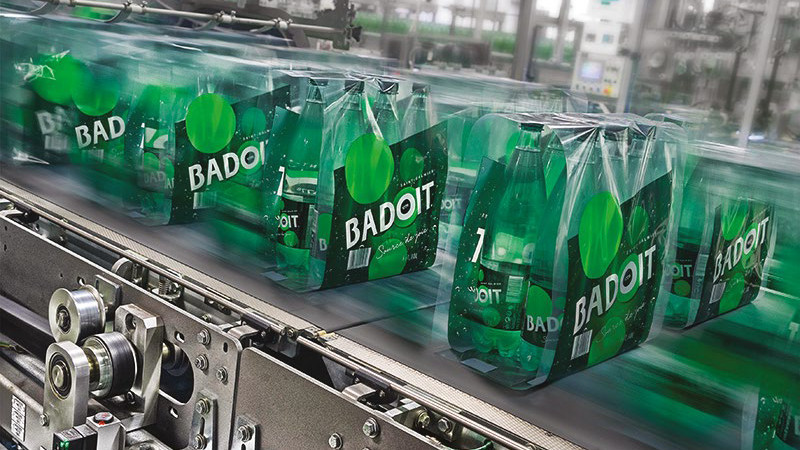
Ze względu bowiem na tolerancję wymiarów i niedoskonałości wykonania nie jest możliwe uzyskanie jednakowych poziomów napełnienia opakowań pomimo identycznej ilości ich zawartości. To przez konsumentów bywa odbierane jako oszustwo. Dlatego, jeżeli towar sprzedawany jest w przezroczystych opakowaniach, producenci częściej decydują się na skorzystanie z maszyn napełniających do jednakowego poziomu.
Do tych zaliczane są nalewarki przelewowe. Są one wyposażone w dyszę, którą płyn wpływa do butelki, a gdy przekroczy zadany poziom, jego nadmiar jest zwracany do zbiornika. W napełnianiu objętościowym korzysta się z nalewarek grawitacyjnych. Produkt jest w nich przechowywany w zbiorniku nad dyszami, a do jego rozlewania do butelek wykorzystywana jest siła grawitacji.
Wybierając nalewarkę, pod uwagę trzeba też wziąć lepkość produktu. W rozlewaniu tych o małej lepkości sprawdzają się nalewarki ciśnieniowo-przelewowe. Nie nadają się one natomiast do dozowaniu gęstych płynów, jak miód. W takim przypadku lepiej użyć napełniarki tłokowej.