Przegląd typów pakowarek
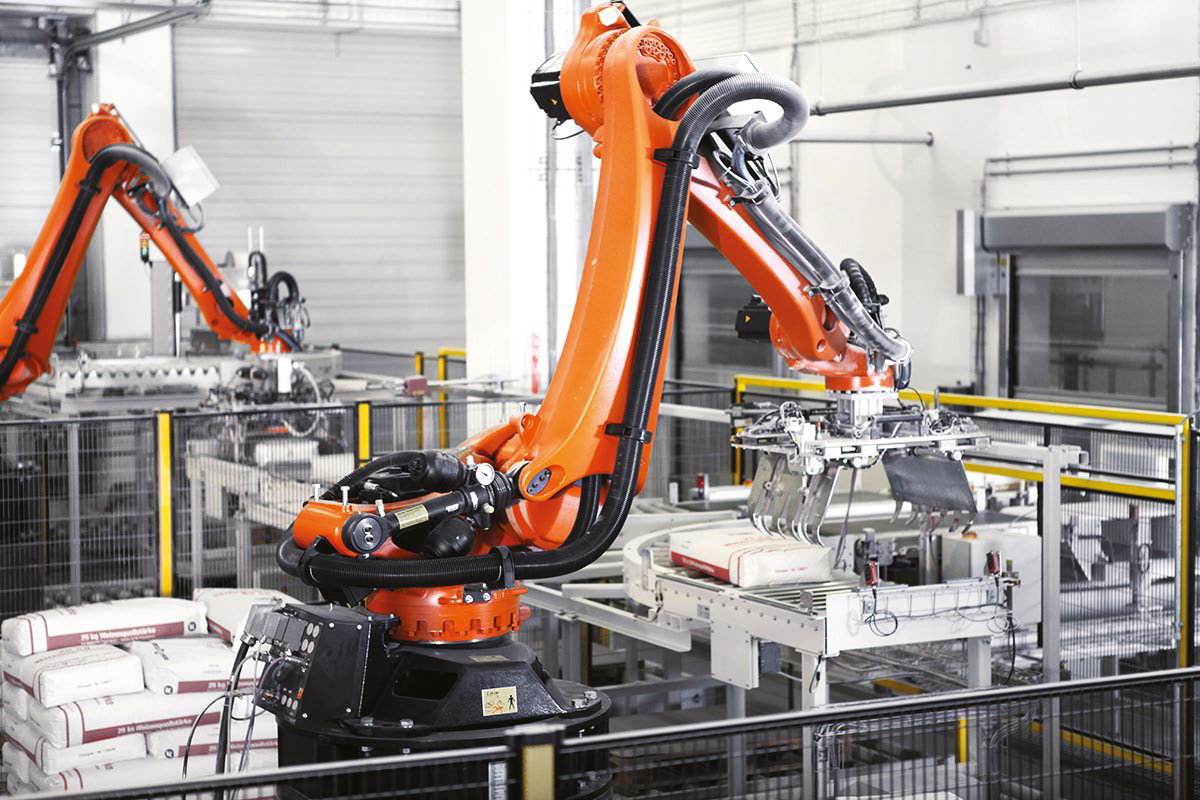
Nalewarki pakują produkty w postaci płynnej. W przypadku pozostałych korzysta się z pakowarek. Zasada ich działania jest następująca – formują rękaw z elastycznego materiału (folii lub papieru), który wypełniają produktem, a następnie zamykają przez zgrzewanie brzegów. Wyróżnić można kilka typów takich maszyn. Dwie głównie podkategorie to: działające w poziomie lub w pionie. Drugie zajmują zwykle mniej miejsca, dzięki czemu można dostępną przestrzeń wykorzystać efektywniej.
Podgrupą pakowarek są maszyny tnące materiał na paski. To pozwala na jednoczesną produkcję wielu opakowań. Są one zazwyczaj długie i cienkie. Pakuje się w nie typowo produkty płynne i sproszkowane. Zaletą takich opakowań jest kompaktowość, natomiast tego typu maszyn – duża wydajność. Kolejną podgrupę stanowią maszyny pakujące saszetki. Folia jest w tym przypadku rozcinana na pół. Obie połowy nakłada się na siebie. Potem formuje się w nich saszetki. Po napełnieniu są one zamykane ze wszystkich stron i wycinane z arkusza. Popularne są także pakowarki, które nie formują opakowań, lecz są załadowywane gotowymi, które otwierają, napełniają i zamykają.
Trendy w branży opakowaniowej a oczekiwania względem maszyn![]() Od maszyn pakujących użytkownicy oczekują przede wszystkim spełnienia wymaganej wydajności pakowania oraz łatwości ich przestawiania na inny model opakowania. Ten drugi warunek jest tym łatwiejszy do spełnienia, im bardziej modułową konstrukcję ma pakowarka. W praktyce oznacza to, że składa się ona z komponentów, które można zestawić ze sobą w różnych konfiguracjach, zmieniając funkcjonalność albo parametry pracy maszyny stosownie do bieżących potrzeb produkcji albo w zależności od dostępnych warunków przestrzennych. W najbliższej przyszłości producenci będą również musieli przystosować swoje maszyny do nowych materiałów opakowań. Chodzi głównie o te biodegradowalne, nadające się do odzysku albo pochodzące z recyklingu. Wzrost ich popularności będzie wynikiem rosnącej świadomości ekologicznej konsumentów, za którą, aby utrzymać się na rynku, muszą też podążać producenci. Popularyzować się będą także energooszczędne metody produkcji. Przykładem jest zgrzewanie ultradźwiękowe, jako alternatywa dla technik tradycyjnych, wymagających podgrzewania. W przypadku tej techniki bowiem ciepło jest generowane w złączu na skutek tarcia wywołanego wibracjami wzbudzonymi ultradźwiękami. Ponadto, w związku z tym, że coraz popularniejsze są produkty spożywcze bez konserwantów, których termin ważności siłą rzeczy jest przez to krótszy, rosnąć będzie popyt na maszyny do pakowania próżniowego. Ponadto użytkownicy oczekują sprawnego zautomatyzowanego systemu kontroli wszystkich procesów zachodzących w maszynie, a w przypadku awarii lub wstrzymania pracy, szybkiej i kompleksowej informacji o przyczynach problemów, tak żeby do minimum skrócić czas spowodowanych nimi przestojów. Wraz z rozwojem Internetu Rzeczy rosną też oczekiwania w zakresie zdalnego prewencyjnego monitoringu stanu pakowarek, dzięki któremu będzie można zapobiec nieplanowanym przerwom w ich działaniu. |
Główne komponenty pakowarek pionowych
Najważniejsze elementy pakowarek pionowych to: rolka z nawiniętym materiałem opakowania, układ prowadnic, którymi jest on rozwijany i prowadzony do kołnierza formującego torebkę, wsyp, którym podawany jest opakowywany produkt oraz zgrzewarka. Ostatnia łączy brzegi opakowania. Torebki wytworzone w pionowych pakowarkach typowo mają trzy szwy: biegnący wzdłuż, który powstał przez złączenie, zazwyczaj na zakładkę, brzegów folii, dolny, który zamyka spód torby oraz górny, uszczelniający ją od góry.
Tytułowe maszyny sprawdzają się w szerokiej gamie produktów. Wykorzystuje się je do pakowania artykułów spożywczych litych, jak ciastka, przez sypkie, jak zmielona kawa, mleko w proszku, po przykładowo ziarna, granulaty i półpłynnych, jak porcjowany ketchup, majonez. Pakowarki pionowe cieszą się dużą popularnością. To wynika głównie stąd, że są to uniwersalne maszyny, które można łatwo przestawić na produkcję zgrzewanych torebek różnego typu – ta sama maszyna na przykład bez problemu może pakować chipsy w nieprzezroczyste i z obu stron zadrukowane torebki oraz ciastka w opakowania z przezroczystym wierzchem. Poza tym pakowanie jest tanie i szybkie.
Kontrola jakości etykietZwieńczeniem procesu pakowania jest oznakowanie opakowania. W tym zakresie stosuje się różne rozwiązania. Przykładowo wymagane informacje, niezmienne dla wszystkich produktów danego typu, na przykład o składzie, umieszcza się na opakowaniu jeszcze przed jego uformowaniem, na przykład zadrukowując folię, z której potem w pakowarkach wytwarzane są zgrzewane torebki. W takim przypadku przeważnie trzeba dodrukować na nich informacje unikalne dla danej serii, jak przykładowo jej numer, datę produkcji i datę przydatności do spożycia / datę ważności. Innym stosowanym podejściem jest naklejanie etykiet na opakowania. Przeważnie wykonuje się je z samoprzylepnego papieru, na który informacje się nadrukowuje. Etykieciarki w związku z tym zwykle można zintegrować z drukarkami. Ponadto implementuje się w nich szereg funkcji z zakresu kontroli jakości. Ta ostatnia jest koniecznością, ponieważ błędy w oznakowaniu w najlepszym razie mogą wpłynąć na opinię o produkcie, a w najgorszym zagrozić zdrowiu konsumentów. Dlatego jest to jedna z częstszych przyczyn wycofywania produktów ze sprzedaży. Im zatem wcześniej błędnie oznakowane produkty zostaną wykryte, tym bezpiecznej dla konsumentów i taniej dla producenta. W związku z tym sprawdzana powinna być przede wszystkim poprawność i zgodność treści etykiety ze wzorcem. Musi być też ona czytelna dla ludzi, jak i dla maszyn – to ostatnie dotyczy przykładowo kodów kreskowych. Na wstępie sprawdza się typowo także opakowania pod kątem obecności na nich etykiety w wyznaczonym miejscu. Kontroluje się również stan etykiety, co ma na celu wyeliminowanie tych uszkodzonych. Ważna jest też jej prawidłowa orientacja. |
Czujniki w pakowarkach pionowych
Pakowarki pionowe to typowo maszyny w pełni zautomatyzowane albo półautomatyczne. W obu przypadkach skupiają liczne komponenty oraz systemy automatyki i pomiarów. Jeśli chodzi o te ostatnie, wyróżnić można kilka sekcji, w których czujniki są niezbędne. Przykład to sensory ultradźwiękowe. Wykorzystuje się je jako czujniki odległości w bezkontaktowym pomiarze średnicy beli materiału opakowania, na przykład folii, nawiniętego na rolkę, z której jest on stopniowo odwijany, gdy formowane są kolejne opakowania. Kiedy promień belki jest znany, sterownik maszyny oblicza, ile jeszcze folii zostało, a gdy jest jej już zbyt mało, sygnalizuje to operatorowi, który wówczas powinien uzupełnić podajnik.
Czujniki ultradźwiękowe są także używane w pomiarach ustawienia napinacza folii, który reguluje stopień naciągnięcia jej wstęgi. Na ich podstawie sterownik maszyny decyduje, czy należy zwolnić, czy raczej powinno się przyspieszyć obroty rolki, która odwija folię.
Kolejny przykład to sensory wykrywające znaczniki umieszczane na materiale, w odstępach równych długości poszczególnych torebek. Odczytując je, sterownik maszyny w odpowiednim momencie wysyła sygnały wyzwalające do obcinarki odcinającej kawałki materiału i zgrzewarki, która łączy jego brzegi. W tym zastosowaniu wykorzystuje się czujniki optyczne. Wymaga się, by były w stanie rozpoznać znaczniki na tle innych oznaczeń nadrukowanych na folii nawet, gdy nie występuje między nimi duży kontrast, a powierzchnia jest silnie odblaskowa. Na etapie kalibracji ustawienia czujnika i układu oświetlenia są tak dobierane, aby temu sprostać.
Synchronizacja w pakowarkach pionowych
Kluczowe znaczenie dla jakości i wydajności pakowania w tego typu maszynach ma synchronizacja zadań formowania opakowania i jego napełniania. W tym celu część pakowarki odpowiedzialna za uwalnianie / dozowanie produktu powinna we właściwym momencie odebrać sygnał wyzwalający lub odwrotnie – kiedy napełni opakowanie, powinna taki sygnał wysłać do części pakowarki, która formuje kolejne. Przeważnie stosuje się pierwsze podejście, synchronizując dozownik z pakowarką. Specyfika produktu może w tym przypadku wymagać, aby sygnał wyzwalający był wysyłany nieco wcześniej lub nieco później względem momentu, kiedy opakowanie zostało uformowane. Zależy to od szybkości spadania produktu. Jeżeli bowiem spada on zbyt szybko, może zostać zgrzany razem ze szwem dolnym. W takim przypadku sygnał wyzwalania wymaga opóźnienia. Właściwy moment ustala się zwykle, dostrajając pakowarkę metodą prób i błędów. Gdy dodatkowo zgrzewane opakowania są wkładane do pudełek, nadrzędną funkcję w obrębie linii pakowania, która składa się wtedy z pakowarki pionowej oraz automatu składającego, wypełniającego oraz zaklejającego kartony, pełni zazwyczaj ten ostatni.