CZĘŚĆ 1: AUTOMATYZCJA PRZETWÓRSTWA I PAKOWANIA ŻYWNOŚCI
W produkcji i przetwórstwie mięsa w ostatnich latach w zakresie automatyzacji nastąpił znaczny postęp. Złożyło się na to kilka czynników. Właściciele zakładów mięsnych tym chętniej inwestują w automatykę, im większe są koszty pracy. Skłania ich do tego również brak wykwalifikowanych pracowników oraz chętnych do pracy z tym specyficznym surowcem.
Oprócz tego ograniczając udział ludzi w produkcji mięsa, łatwiej jest przestrzegać norm jakości i standardów higienicznych. Dzięki automatyzacji łatwiej jest także spełnić wymogi konsumentów, którzy oczekują wyrobów w postaci, w której ich przygotowanie do spożycia nie zajmie im wiele czasu, na przykład bez kości i/albo skóry, podzielonych na porcje, pokrojonych na plasterki.
CZYM CIĄĆ MIĘSO?
W zakładach produkcji i przetwórstwa mięsa na kolejnych etapach obróbki tego surowca używane są różnego typu specjalistyczne maszyny. Jednym z procesów, który najczęściej się automatyzuje, jest cięcie mięsa i krojenie go na plasterki.
W tym celu używa się "zwykłych" ostrzy i maszyn tnących strumieniem wody pod dużym ciśnieniem (bez ścierniwa). Te drugie, oprócz mięsa, w przemyśle spożywczym tną także wiele innych grup produktów, w tym warzywa, ciasta, słodycze i mrożonki. Popularność w cięciu żywności maszyny tnące strumieniem wody zawdzięczają swoim licznym zaletom.
Cięcie wodą jest uważane za najwydajniejszą metodę porcjowania mięsa (i żywności w ogóle) na skalę przemysłową, m.in. dzięki temu, że nie jest konieczne czyszczenie / odkażanie ani ostrzenie narzędzia tnącego. Uznaje się je również za najhigieniczniejsze.
ZALETY CIĘCIA WODĄ
Wynika to stąd, że do cięcia używana jest czysta woda, zaś brak ostrzy zapobiega namnażaniu się bakterii oraz ich przenoszeniu się z mięsa na narzędzia tnące, a następnie z ostrzy na kolejne produkty, bez konieczności zapobiegania temu przez stosowanie dezynfekujących środków chemicznych.
Ważną zaletą cięcia strumieniem wody jest także jego mały wpływ na jakość mięsa. Krawędzie plastrów nie są poszarpane ani zabrudzone. Ponadto się nie nagrzewają ani nie są ściskane, co wydłuża czas ich przechowywania.
Dzięki bardzo wąskiej szczelinie po cięciu straty surowca są mniejsze. Możliwe jest również wykonanie bardzo precyzyjnych cięć. To w połączeniu z możliwością cięcia we wszystkich kierunkach zapewnia dużą elastyczność porcjowania i łatwość przestrojenia linii krojenia w przypadku zmiany surowca.
|
DLACZEGO WARTO ZAUTOMATYZOWAĆ TRYBOWANIE?
Cięcie mięsa i jego krojenie na plasterki to zadania, które zautomatyzować można stosunkowo łatwo. Wynika to przede wszystkim stąd, że na tym etapie obróbce poddawane są porcje, które są mniej więcej jednakowe pod względem rozmiarów i kształtów.
Przed podzieleniem na kawałki z mięsa należy usunąć kości. To zadanie jest trochę trudniejsze, bowiem kolejne egzemplarze zwierząt mogą się pomiędzy sobą różnić rozmiarami i/albo szczegółami anatomicznymi.
Z kilku powodów warto jednak na tym etapie wyręczyć pracowników, którzy oddzielają mięso od kości przy użyciu noży lub nożyc, specjalistyczną maszyną. Ręczne trybowanie (usuwanie kości) jest bowiem dość trudną i żmudną czynnością, wymaga zatem dużej wprawy oraz koncentracji. Jeśli osoba wykonująca to zadanie nie ma odpowiednich umiejętności, a wyszkolenie się w tej czynności nie jest łatwe, w związku z czym trudno jest znaleźć chętnych i później utrzymać pracowników na tym stanowisku, albo jest zmęczona, na przykład pod koniec dnia pracy, pracuje wolniej i/albo wykonuje tę operację niedokładnie.
Opakowania ze szkła - zalety i zastosowania
Szkło nie przepuszcza nic z zewnątrz, ani gazów, ani cieczy, które mogłyby przyspieszyć psucie się żywności. Stanowi też barierę dla bakterii. Dla konsumentów ważna jest oprócz tego możliwość samodzielnego sprawdzenia tego, jaki produkt oraz w jakiej ilości znajduje się w środku. Wadą opakowań szklanych jest kruchość. Są ponadto ciężkie. Ze szkła wykonywane są głównie butelki oraz słoiki. W pojemniki te pakowane są produkty żywnościowe różnego typu, na przykład napoje, sosy, dżemy, owoce oraz warzywa w zalewach, dania gotowe (pulpety, gołąbki), przyprawy oraz posiłki dla niemowląt. Trudności w kontroli jakości RTG żywności w szkle Kontrola jakości żywności zapakowanej w szkło przez prześwietlenie opakowania promieniami X nie jest łatwym zadaniem. Główną przyczyną jest to, że zanieczyszczające ją ciała obce to przeważnie okruchy szkła, nie różnią się więc gęstością od opakowania. Drugi ważny powód to kształt butelek oraz słoików, trudno jest bowiem wykryć zanieczyszczenia, które gromadzą się na dnie, ściankach albo w szyjce. Ponadto opakowania szklane, z powodu specyfiki ich procesu produkcyjnego, różnią się. Często te wyprodukowane w jednej serii, choć ważą tyle samo i mają taki sam kształt, różnią się grubością ścianek bocznych i/lub denka. Inspekcję utrudniają również defekty szkła, na przykład cząstki substancji dodawanych w procesie produkcyjnym, które nie rozpuściły się w masie szklanej, pęcherze powietrza oraz zanieczyszczenia ze stłuczki szklanej pochodzącej z recyklingu. Okrągłe pojemniki łatwiej zbadać Kontrola jakości opakowań szklanych jest trudniejsza, gdy pochodzą one od różnych producentów. Nawet jeśli bowiem wyglądają podobnie, mogą się między sobą różnić pod względem gęstości i składu chemicznego. Podobnie, im bardziej skomplikowany jest ich kształt, tym trudniej jest skutecznie zbadać ich jakość. Najłatwiej ocenić jakość pojemników okrągłych, które nie mają ostrych krawędzi odznaczających się na radiogramie. W ich przypadku nie ma też znaczenia sposób ustawienia. Trudności może zaś sprawić poprawna interpretacja radiogramu sekcji nakrętki słoika, która składa się z metalowej pokrywki i szklanego gwintu. Lepkość to ważna właściwość produktu Nie bez znaczenia jest specyfika produktu, m.in. jego lepkość. Od niej bowiem zależy to, gdzie w pojemniku będą się gromadzić zanieczyszczenia. Na przykład w przypadku produktów o półstałej konsystencji ciała obce podczas napełniania słoika uniosą się w górę. Dlatego skontrolować powinno się całe opakowanie, a nie tylko jego dno. W przypadku cieczy rzadkich bardziej prawdopodobne jest, że to właśnie tam się one zgromadzą. W związku z tym inspekcja powinna być skoncentrowana właśnie na dolnej sekcji butelki. |
MASZYNY DO TRYBOWANIA
To drugie objawia się tym, że pozostawia na kościach zbyt wiele mięsa, co oznacza straty, albo w mięsie, które oddzieliła od kości, pozostawia kostki, ich odłamki lub chrząstki. Ma to negatywny wpływ na jakość wyrobu końcowego. Nie można również zapomnieć o chorobie, zespole cieśni nadgarstka, która dotyka osoby przez wiele lat pracujące na takim stanowisku.
W zależności od gatunku mięsa zautomatyzowane maszyny do usuwania kości działają różnie. Na przykład te do filetowania najpierw odnajdują środek ryby, a potem wycinają kręgosłup, rozcinając ją na dwie części. Środek ryby lokalizuje się, umieszczając ją pomiędzy prowadnicami mierzącymi jej szerokość albo wykorzystując inne czujniki.
Z kolei w maszynach do trybowania drobiu na przykład podudzia ustawia się na membranie, przez którą kość jest przepychana. Powoduje to oddzielenie się od niej mięsa. Staw skokowy odcina piła.
ROBOTY W PRODUKCJI I PRZETWÓRSTWIE MIĘSA
Roboty w produkcji i przetwórstwie żywności znajdują zastosowanie na różnych etapach jej obróbki. Na przykład w przemyśle mięsnym w oparciu o nie organizowane są stanowiska do rozbioru tusz zwierzęcych. Ramię robota jest wówczas wyposażone w narzędzie tnące, którym rozcina tuszę albo chwytak, którym ją podnosi i naprowadza na piłę. Robot taki jest przeważnie sterowany wizyjnie.
Na podstawie obrazów, które rejestrują kamery systemu wizyjnego, tworzony jest komputerowy model tuszy. Jest on następnie poddawany analizie w specjalistycznym oprogramowaniu. Jej wynikiem są linie cięcia zoptymalizowane pod kątem szczegółów anatomicznych danego egzemplarza tuszy.
Poza tym, że zrobotyzowanie rozbioru tusz zwiększa wydajność tej operacji, poprawia również bezpieczeństwo pracowników rzeźni, których robot zastępuje w bezpośrednim kontakcie z piłą.
Innym przykładem jest wykorzystanie robota do usuwania tłuszczu z wnętrza tuszy.
Aby zminimalizować prawdopodobieństwo skażenia żywności, nie wystarczy tylko dbać o jakość surowców, czystość w zakładzie i przestrzegać standardów higieny wśród pracowników. Źródłem niebezpiecznych zarazków może też się bowiem stać sam sprzęt produkcyjny. Aby temu zapobiec, musi on być właściwie zaprojektowany i wykonany. Powierzchnie gładkie i pochylone Zapewnić trzeba możliwość jego skutecznego czyszczenia. Musi on być skonstruowany w taki sposób, aby łatwo było go rozmontować, jeśli wymaga tego jego umycie. Nie powinien też wchłaniać bakterii, umożliwiać im przeżycia ani namnażania się, na nim ani na produkcie. W tym celu m.in. powierzchnie wygładza się i unika się wszelkich zagłębień, w których bakterie mogłyby się rozwijać i/albo przetrwać proces czyszczenia. Im więcej płaskich, wypukłych oraz pochylonych powierzchni, które ułatwią spływanie płynów, oraz zaokrąglonych rogów, tym dla higieny produkcji lepiej. Preferowane są konstrukcje jednolite Zamiast pustych w środku, preferowane są wypełnione elementy konstrukcyjne. Wszelkie tabliczki, wsporniki, zaślepki, najlepiej gdy są na trwale przymocowane do podłoża, a nie tylko przykręcone do niego śrubami. Zamiast łączenia różnych elementów, lepsze będą konstrukcje monolityczne, na przykład odlewy. Materiały, z jakich budowany jest sprzęt produkcyjny, powinny być nie tylko nietoksyczne dla produktu, ale i odporne na środki chemiczne, które będą używane do ich mycia i sposób, w jaki będzie ono wykonywane. Powinny być m.in. łatwo zmywalne, odporne na korozję i wytrzymałe mechanicznie. Nie mogą za to sprzyjać namnażaniu się mikroorganizmów. Tkaniny wchłaniają wilgoć Jeżeli chodzi o odporność na korozję, to pierwszym materiałem spełniającym ten wymóg, który przychodzi na myśl, jest stal nierdzewna. Sprzętu do produkcji i inspekcji żywności nie zaleca się wyposażać w elementy malowane, gdyż powłoki farby mogą z czasem pękać i się kruszyć, na przykład podczas ich szorowania. W przenośnikach nie powinno się korzystać z taśm wykonanych z materiałów, ponieważ tkaniny łatwo wchłaniają wilgoć. Materiały konstrukcyjne powinny być również chemicznie obojętne. Inaczej mogą stać się źródłem zanieczyszczeń, będących wynikiem ich reakcji z różnymi substancjami, z żywności i tymi myjącymi. |
ZAUTOMATYZOWANE USUWANIE TŁUSZCZU
W tym celu robota wyposaża się w końcówkę ssącą. Tusze wjeżdżają na stanowisko zawieszone na hakach i na krótką chwilę zatrzymują się przed zautomatyzowanym ramieniem.
Czujniki wykrywają obecność tuszy we właściwym miejscu. Wówczas robot przez rozcięcie w płacie mięsa wprowadza ssak. Po usunięciu tłuszczu tusza transportowana jest na kolejne stanowisko.
Dzięki zwolnieniu pracowników rzeźni z wykonywania tego żmudnego zadania poprawia się wydajność rozbioru mięsa. Ponadto tłuszcz jest usuwany dokładniej.
Roboty są też wykorzystywane na liniach paczkowania mięsa. W obrębie tych stanowisk ich sterowniki korzystają z informacji z systemów wizyjnych oraz ważących, które wbudowano w przenośnik. Na tej podstawie robot na daną tackę układa te kawałki mięsa, których łączna waga mieści się w zadanym przedziale.
ZALETY ROBOTÓW
Oprócz tego, że roboty przemysłowe zwiększają wydajność operacji, w wykonywaniu której zastępują ludzi, oraz poprawiają bezpieczeństwo pracowników, którzy wcześniej obsługiwali niebezpieczne maszyny, mają także inne zalety. Charakteryzują je m.in. niezmienna precyzja i powtarzalność nieosiągalne dla człowieka. Dzięki temu jednostajne, męczące zadania wykonują przez cały czas z jednakową starannością.
W przeciwieństwie do ludzi roboty pracują 24 godziny na dobę i nie potrzebują aż tak częstych przerw, zwolnień ani urlopu. Odpowiednio konserwowane mogą działać przez nawet kilkanaście lat, w czasie których duży koszt ich zakupu zwraca się zazwyczaj z nawiązką.
Oprócz tego maszyny te bez problemu podnoszą duże ciężary i mogą pracować w warunkach nieprzyjemnych dla ludzi. Takie występują na przykład na liniach rozbioru mięsa lub wyrabiania ciast, gdzie panuje duże zapylenie.
Aby jednak te zalety rzeczywiście odczuć, stanowisko zrobotyzowane trzeba odpowiednio zorganizować. Jednym z podstawowych kryteriów wyboru robota jest specyfika zadania, które będzie on wykonywał.
JAKI ROBOT BĘDZIE NAJLEPSZY?
Jeżeli chodzi na przykład o pakowanie, to w przemyśle spożywczym, chociaż nie tylko, wyróżnić można dwa jego zasadnicze etapy. Pierwszy z nich polega na nałożeniu opakowania bezpośrednio na produkt. Przykładami takich czynności są: zawinięcie batonu lub cukierka w folię, zafoliowanie mięsa na tacce i włożenie czekoladek do pudełka.
W drugim etapie pojedyncze wyroby pakuje się do zbiorczego pojemnika mieszczącego zazwyczaj dużo sztuk. Na przykład batony i bombonierki przekładane są do kartonowego pudełka, natomiast butelki do skrzynek. Opakowania zbiorcze, które mają ułatwić transport i ochronić produkt przed zniszczeniem, układa się na paletach.
W drugim etapie pakowania są zatem wykonywane przede wszystkim operacje pick and place oraz paletyzacji. W tej drugiej najlepiej sprawdzają się, przede wszystkim ze względu na ich szybkość, roboty przegubowe. Jeżeli z kolei chodzi o operację typu pick and place, warto rozważyć zakup maszyn typu delta ("pająków").
|
ZALETY ROBOTÓW DELTA
Zaletą robotów tego rodzaju jest montaż na suficie stanowiska. Zapewnia to obszerną i drożną przestrzeń roboczą. Ponadto są one szybkie, a wydajność ich wszystkich osi jest jednakowa, w przeciwieństwie do wielu innych konfiguracji robotów przemysłowych.
Mają one niestety mały udźwig, nieprzekraczający kilku kilogramów. Dla porównania roboty SCARA podnoszą ciężary o masie nawet kilkudziesięciu kilogramów. Ponadto ich przestrzeń robocza jest ograniczona w płaszczyźnie pionowej zasięgiem ramion. Roboty typu delta nie są również przystosowane do manipulowania obiektami w tym kierunku.
Równie ważny jak wybór typu robota, jest dobór odpowiednich chwytaków. Ich konstrukcja powinna być dostosowana do specyfiki produktu, którym będą manipulować.
PRZEGLĄD ZASTOSOWAŃ CHWYTAKÓW
Przykładowo do podnoszenia warstw produktów (słoików, pudełek) zalecane są chwytaki podciśnieniowe powierzchniowe, natomiast do przenoszenia jednocześnie wielu butelek - kielichowe. Chwytaki widłowe sprawdzają się w podnoszeniu worków.
Do chwytania wyrobów delikatnych, jak plastry sera albo mięsa, służą chwytaki specjalne, na przykład z końcówką w kształcie grzebieniowatych szczypiec. Z kolei kawałki ciasta można na przykład podnosić chwytakami, których końcówką roboczą są cienkie pręty.
Istotną kwestią jest także sposób organizacji zrobotyzowanego stanowiska pakowania. W tym zakresie można wyróżnić kilka najczęściej spotykanych konfiguracji. W jednej z nich produkty, na przykład pojemniki z jogurtem, są transportowane ciągiem na przenośniku ustawionym prostopadle do zrobotyzowanej linii ich pakowania do zbiorczych pudełek. Na odcinku o szerokości tej drugiej może się zmieścić określona liczba pudełek, na przykład pięć sztuk.
ORGANIZACJA STANOWISKA ZROBOTYZOWANEGO
Po zapełnieniu nimi tego odcinka przenośnik jest zatrzymywany. Specjalne prowadnice wyrównują wówczas pojemniki, przesuwając ich cały rząd na linię ich pakowania do kartonów. Wtedy robot podnosi jednocześnie pięć jogurtów, lub nawet kilka rzędów po pięć sztuk, i przekłada je do zbiorczego opakowania.
Konfiguracja ta ma dwie bardzo ważne zalety. Równoczesne pakowanie po kilka sztuk produktów znacząco poprawia wydajność produkcji. Oprócz tego robot nie musi być sterowany wizyjnie, bowiem wyroby na jego stanowisko docierają już odpowiednio ustawione i wyrównane.
W drugiej konfiguracji na jednym z przenośników transportowane są nieuporządkowane, pod względem rozmieszczenia i orientacji, produkty, na przykład świeżo upieczone ciastka albo właśnie wyprodukowane batony. Nad tym taśmociągiem biegnie drugi. Robot przekłada na niego wyroby, obracając je tak, żeby możliwe było ich zapakowanie, na przykład zafoliowanie. Jest on zwykle sterowany wizyjnie.
MASZYNY PAKUJĄCE - NALEWARKI
Jeżeli natomiast chodzi o pierwszy etap pakowania, który polega na nałożeniu opakowania bezpośrednio na wyrób albo umieszczeniu produktu w pojemniku, na przykład rozlaniu wody mineralnej do butelek albo soku do kartonów, wtedy też korzysta się z maszyn specjalistycznych. Ich przykładami są nalewarki.
Maszyny te są centralnym punktem linii pakowania napojów. Rodzaj napełniarki powinien być dobierany pod kątem specyfiki rozlewanego płynu, głównie jego lepkości. Wśród producentów piwa, win oraz soków popularne są nalewarki ciśnieniowo-przelewowe. Sprawdzają się one w dozowaniu przede wszystkim płynów o małej lepkości. Ich zaletą jest również duża szybkość napełniania.
Ten rodzaj nalewarki nie nadaje się natomiast do dozowania gęstych płynów, na przykład miodu. W ich przypadku lepiej użyć napełniarki tłokowej.
Jeżeli napój jest gazowany, linię butelkowania należy wyposażyć w nalewarkę przeciwciśnieniową. Maszyna ta przed napełnieniem butelki usuwa z niej powietrze. Dzięki temu w czasie butelkowania nie zmienia się stopień nagazowania napoju.
KRZYWA V
Ważnym parametrem maszyn specjalistycznych, takich jak nalewarki, jest ich wydajność wyrażana przeważnie liczbą butelek napełnianych w ciągu minuty (bottles per minute, BPM). Powinna ona nie tylko spełniać obecne wymagania, ale i gwarantować "zapas", który pozwoli na rozwój produkcji w przyszłości.
Parametr ten wpływa również na dobór pozostałych maszyn linii pakowania. Aby uzyskać jak największą wydajność, projektując linie pakowania, nie tylko zresztą w branży spożywczej, stosuje się bowiem zasadę krzywej V.
Według niej jedna z maszyn, która ma kluczowe znaczenie dla przebiegu procesu produkcyjnego, jest uznawana za centralny punkt linii pakowania. W przypadku linii butelkowania jest to zwykle nalewarka. Im dalej od tej maszyny, w obu kierunkach, tym urządzenia są wydajniejsze.
Jeżeli na przykład nalewarka pracuje z wydajnością 100 BPM, odpowiednio większą wydajność powinna mieć płukarka pustych butelek, na przykład 120 BPM. Robot, który wypakowuje puste butelki, musi z kolei pracować jeszcze szybciej.
WSPÓŁZALEŻNOŚĆ WYDAJNOŚCI
Jego wydajność może wynosić na przykład 140 BPM. Jeżeli natomiast chodzi o liczbę kartonów z pustymi butelkami, które należy rozładować w ciągu minuty, to 150 sztuk tych opakowań będzie wartością wystarczającą.
Analogicznie w drugą stronę, przykładowa wydajność etykieciarki to 110 BPM, robota, który pakuje pełne butelki do kartonów - 120 BPM, natomiast tego, który ustawia na paletach kartony z napojami - 150 BPM. Dzięki temu nigdy nie powinno zabraknąć butelek do napełniania, na przykład w razie chwilowego zatrzymania robota wypakowującego puste opakowania.
Z drugiej strony zawsze powinno być dość wolnego miejsca na przenośniku (w strefie buforowej), aby nie doszło do stłoczenia się napełnionych butelek w oczekiwaniu na ich przełożenie do zbiorczego kartonu. Wdrażając koncepcję krzywej V, można zatem maksymalnie efektywnie wykorzystać najważniejszą maszynę na linii pakowania, która z reguły jest również tą najdroższą.
JAK WAŻNA JEST HIGIENA?
Przestrzeganie standardów higieny w produkcji i przetwórstwie żywności jest priorytetem. Jeśli instytucja nadzorująca jakość żywności i przebieg jej produkcji potwierdzi ich niedotrzymanie, producentom grożą dotkliwe konsekwencje. Poza tym, że cierpi na tym ich reputacja, mogą się spodziewać wysokich kar, na przykład zakazu wprowadzania ich wyrobów do sprzedaży i/albo zamknięcia zakładu.
Przemysł mięsny jest przykładem branży, w której przepisy są szczególnie zaostrzone. Nic w tym dziwnego, bowiem surowce przetwarzane w zakładach w tym sektorze mogą być źródłem różnych groźnych dla zdrowia i życia ludzi mikroorganizmów.
Przykładem są bakterie. Zwierzęta, które trafiają do zakładów mięsnych mogą być nosicielami m.in. bakterii salmonelli, listerii i e. coli.
Bakterie oraz inne mikroorganizmy, których źródłem jest żywność, w trakcie jej przetwarzania mogą zanieczyszczać sprzęt używany do jej produkcji i pakowania. Aby zminimalizować groźbę skażenia kolejnej partii wyrobu w wyniku kontaktu surowca z zanieczyszczonymi maszynami, trzeba je myć, a potem sterylizować.
CIP I SIP
Czynności te wykonuje się różnymi metodami, ręcznie i w sposób zautomatyzowany. Przykładem jest mycie ciśnieniowe, mechaniczne (szczotkami) oraz metodami CIP (Cleaning in Place) i SIP (Sterilization in Place).
Mycie i sterylizacja na miejscu polegają na spłukiwaniu wnętrza wyposażenia linii produkcyjnych w przerwach pomiędzy kolejnymi jej uruchomieniami, bez konieczności rozmontowywania jej elementów albo wprowadzania do ich wnętrza urządzeń czyszczących, albo wchodzenia do nich (dotyczy to dużych zbiorników, na przykład mieszalników). W systemach CIP i SIP realizuje się to, wymuszając przepływ środków myjących i odkażających przez te urządzenia i obiekty, i ich powrót do głównego zasobnika.
ZALETY CIP I SIP
Mycie i sterylizacja na miejscu mają wiele zalet, w tym: szybkość, gdyż nie trzeba demontować, a potem składać wyposażenia linii produkcyjnej, dokładne czyszczenie miejsc trudno dostępnych i lepszą kontrolę zużycia wody i chemikaliów. Za metodami CIP i SIP przemawiają też: mniejszy koszt i rzadszy kontakt personelu z substancjami niebezpiecznymi.
Aby te zalety były rzeczywiście odczuwalne, sprzęt produkcyjny powinien być odpowiednio zaprojektowany i wykonany. W ramce przedstawiamy najważniejsze wytyczne w tym zakresie.
CZĘŚĆ 2: ZAPEWNIANIE JAKOŚCI W PRODUKCJI SPOŻYWCZEJ
Mimo starań, ani ręczne, ani zautomatyzowane trybowanie nie daje gwarancji, że w mięsie nie pozostaną drobiny kości. W żywności w ogóle mogą też występować inne zanieczyszczenia, na przykład opiłki metalowe, okruchy szklane lub kawałki tworzyw sztucznych, które odłamały się przykładowo od opakowań lub części maszyn. Dlatego kontrola jakości w zakładach produkcji i przetwórstwa żywności jest etapem obowiązkowym. Aby była dokładna, ale zarazem szybka, automatyzuje się ją.
JAK ROZPOZNAĆ CIAŁA OBCE NA OBRAZIE RTG?
Jedną z metod kontroli jakości popularną w przemyśle spożywczym jest inspekcja rentgenowska. Obiekty, które są poddawane badaniu, prześwietla się promieniowaniem RTG. Ma ono specyficzną właściwość - może przenikać przez materiały nieprzezroczyste dla światła widzialnego. Stopień tej przepuszczalności zależy od gęstości danego materiału. Im jest ona większa, tym mniej promieni przez niego przenika.
Pozwala to rozpoznać na obrazie RTG produktu elementy o innej gęstości, na przykład zanieczyszczenia. W tym celu określa się wartość progową absorpcji promieniowania X. Po jej przekroczeniu uznaje się, że dany szczegół na radiogramie jest ciałem obcym.
SKUTECZNA INSPEKCJA RENTGENOWSKA
Na czułość detekcji zanieczyszczeń przez prześwietlenie produktu promieniami X wpływa wiele czynników. Jednym z nich jest to, w jakim stopniu obiekt poddawany inspekcji różni się od ciał obcych, które mogą w nim potencjalnie występować, pod względem gęstości.
Jeżeli chodzi o produkty spożywcze, to większość z nich w dużym stopniu jest złożona z wody, na przykład banany w 74%, mięso chude w 75%, a truskawki aż w 91%. W związku z tym ich gęstość ma wartość zbliżoną do masy właściwiej wody, czyli 1 g/cm³. Na przykład gęstość mięsa, która jest wypadkową różnej gęstości jego poszczególnych składników tkankowych, czyli tkanki mięśniowej, tłuszczowej, kości, ścięgien i skóry, wynosi od 1,051 do 1,071 g/cm³.
Jeśli zatem system inspekcji został tak zaprogramowany, aby za ciała obce uznawał te pochłaniające promieniowanie rentgenowskie silniej niż produkt, w przypadku żywności bezbłędnie rozpoznane zostaną m.in. złoto, ołów, miedź, stal nierdzewna, stal zwykła oraz żelazo. Gęstość tych metali mieści się bowiem w przedziale od około 7 do ponad 19 g/cm³.
CO SYSTEM INSPEKCJI MOŻE PRZEOCZYĆ?
Istnieje wysokie prawdopodobieństwo, że wykryte zostaną drobiny aluminium, szklane okruchy i kamienie, o gęstości w zakresie od 2 do 3 g/cm³. Możliwe jest również wykrycie kości i tworzyw sztucznych, takich jak PTFE i PVC. Ich gęstość wynosi od 1,5 do nieco ponad 2 g/cm³.
Trudno jest natomiast odróżnić od żywności ciała obce m.in. z tworzyw acetalowych (delrin) oraz poliwęglanów (lexan), z których wykonywane są na przykład części maszyn, i z nylonu, gdyż ich gęstość wynosi od 1 do poniżej 1,5 g/cm³. Jeżeli system inspekcji nie reaguje na drobiny, które absorbują promienie X słabiej niż produkt, nie wykryje także wiórek z drewna, insektów ani włosów. Gęstość takich zanieczyszczeń jest bowiem mniejsza niż 1 g/cm³.
Ciała obce na podstawie przekroczenia progowej wartości absorpcji promieniowania rentgenowskiego tym trudniej jest też wykryć, im obiekt inspekcji jest mniej jednorodny. Przykładem takiego produktu są pestki albo orzechy w opakowaniu z tworzywa sztucznego.
JAK WAŻNE JEST USTAWIENIE PRODUKTU?
Warto również pamiętać o tym, że im grubszy jest obiekt badania, tym wymagana jest większa moc promieniowania rentgenowskiego. Wtedy jednak zmniejsza się kontrast radiogramu, a przez to też czułość detekcji. Dlatego sposób ustawienia produktu poddawanego inspekcji względem źródła i detektora promieni X nie jest bez znaczenia.
Najlepiej, jeżeli leży on na dłuższym boku, wówczas bowiem promieniowanie RTG prześwietla go wzdłuż tego krótszego. Dzięki temu może ono mieć mniejszą moc, niż gdyby leżał on w pozycji odwrotnej.
Produkt powinien leżeć na dłuższym boku w przypadku, gdy źródło promieniowania znajduje się nad nim, na przykład nad przenośnikiem, którym jest on transportowany, zaś jego detektor pod nim. Warto przy tym dodać, że im większe, a dokładnie szersze lub głębsze obiekty są w tej konfiguracji badane, tym odległość pomiędzy źródłem a detektorem promieni X powinna być większa.
KRZYŻOWANIE PROMIENI
Jeżeli z kolei produkty są wyższe niż szersze, źródło i detektor promieniowania powinny się znajdować po przeciwnych stronach taśmociągu, ustawione prostopadle do kierunku, w którym przesuwa się przenośnik. W przypadku pewnych grup produktów warto rozważyć użycie dwóch źródeł i dwóch detektorów, których promienie, przecinając obiekt poddawany inspekcji, będą się krzyżować.
Takie ustawienie jest zalecane zwłaszcza w kontroli jakości opakowań ze szkła, w których mogą występować szklane ciała obce oraz produktów ciekłych, rzadkich, w których zanieczyszczenia gromadzą się na dnie i gęstych, jak dżem, w których zbierają się one pod zakrętką. Trudniej też wówczas przeoczyć zanieczyszczenia na ich ściankach.
W ramce charakteryzujemy wyzwania towarzyszące kontroli jakości produktów spożywczych za pomocą promieni X w zależności od rodzaju opakowania. Przedstawiamy je na przykładzie pojemników wykonanych ze szkła.
Wizyjna kontrola jakości w przemyśle spożywczym - Inspekcja etykiet na okrągłych opakowaniachWizyjna kontrola jakości etykiet opisujących zawartość opakowań o wypukłych ściankach jest znacznie trudniejsza niż nalepek, które naklejono na płaskich powierzchniach. Składają się na to dwa najważniejsze powody. Trudności w kontroli jakości okrągłych opakowań Po pierwsze obraz, jaki rejestruje kamera w przypadku etykiety, którą naklejono na zaokrąglonej powierzchni, jest naturalnie zniekształcony. Po drugie w przypadku okrągłych pojemników nigdy nie można mieć pewności, w zasięgu której z kamer znajdzie się etykieta bądź ta jej część, której zgodność ze wzorcem należy zweryfikować. Inspekcja wielokamerowa Aby rozwiązać powyższe problemy, systemy wizyjne sprawdzające poprawność rozmieszczenia i treści etykiet tworzy się z wielu kamer, które rejestrują obrazy okrągłych opakowań ze wszystkich stron. Ustawia się je w różnych odległościach i pod różnymi kątami względem obiektu inspekcji. Obrazy przez nie zarejestrowane poddaje się następnie specjalnej obróbce, przetwarzając je do postaci, w której wykrycie nieprawidłowości na etykietach jest znacznie łatwiejsze. Kalibracja, spłaszczanie obrazu Aby w oprogramowaniu systemu wizyjnego można było spłaszczyć obraz wypukłej powierzchni, wcześniej trzeba go skalibrować. W tym celu próbne opakowanie jest owijane papierem, na którym została naniesiona siatka znaczników, na przykład kropek. Kamera rejestruje obraz pojemnika, zaś operator określa wymiary siatki. Następnie wybiera on jeden ze znaczników i wskazuje znaczniki, które z nim sąsiadują, jeden od góry oraz jeden z boku. Na tej podstawie oprogramowanie systemu wizyjnego wylicza, w jakim stopniu trzeba "wykrzywić" zarejestrowany obraz, żeby go spłaszczyć. Zniekształcenia Jeżeli inspekcji poddawane są opakowania o jednakowych rozmiarach oraz kształcie, kalibrację wykonywaną w ten sposób wystarczy przeprowadzić tylko raz. W przeciwnym wypadku powinno się ją powtórzyć dla każdego wariantu opakowania. Warto też wspomnieć o istotnym ograniczeniu tej metody spłaszczania zakrzywionych obrazów. Pomimo dość dobrej jakości obrazu wynikowego, liczyć się niestety trzeba ze zniekształceniami, które zwykle występują na jego krawędziach. Jeżeli znajdują się tam jakieś ważne informacje, których czytelność trzeba sprawdzić, warto mieć to na uwadze. Pola widzenia kamer muszą się zazębiać Jeśli z kolei chodzi o brak pewności co do tego, w oku której kamery znajdzie się etykieta bądź jej fragment, który wymaga inspekcji, rozwiązuje się to na kilka sposobów. Jeden z nich polega na złączeniu wielu obrazów opakowania w jeden. Zazwyczaj realizuje się to, wykorzystując cztery kamery, które ustawia się względem siebie pod kątem 90o w taki sposób, aby ich pola widzenia nieco na siebie nachodziły na krawędziach. W ten sposób kompensuje się zniekształcenia, które mogą w tych miejscach występować po spłaszczeniu każdego z obrazów częściowych. O łączeniu kilku obrazów w jeden piszemy w kolejnej ramce. |
KONTROLA JAKOŚCI ETYKIET
Na to, jak konsument oceni wyrób, poza jakością samego produktu składa się również sposób jego oznakowania. Bez względu na to, czy ma ono formę nalepki, folii z nadrukowanymi informacjami, którą owija się opakowanie, czy nadruku na nim, z punktu widzenia klientów najważniejsze jest, aby etykieta była czytelna.
Nie bez znaczenie jest też jednak jej ogólny wygląd. Dlatego etykiety ocenia się pod względem nie tylko czytelności, ale również sprawdza się, czy są naklejone w odpowiednim miejscu, nie "do góry nogami", czy nie są naderwane, pomarszczone, miejscami starte albo zabrudzone. W tym celu wykorzystywane są najczęściej systemy wizyjne. Ocena jakości etykiet z różnych powodów może być utrudniona, na przykład ze względu na umiejszczenie nalepki, jej materiał, kolor itp. Problemem może się okazać również kształt opakowania.
Wizyjna kontrola jakości w przemyśle spożywczym - Inspekcja etykiet na okrągłych opakowaniach![]() Rys. 1. Modyfikacja techniki złączania obrazów a) polega na ich częściowym nakładaniu na siebie b) Kalibracja Aby obraz wynikowy uzyskany przez złączenie wielu obrazów cząstkowych był dobrej jakości, trzeba spełnić kilka warunków. Ważne jest na przykład odpowiednie ustawienie i skalibrowanie kamer systemu wizyjnego, tak by ich pola widzenia odpowiednio na siebie nachodziły. Kalibracja jest procesem złożonym (wieloetapowym), który należy powtarzać każdorazowo, gdy zmieniają się rozmiary opakowania. Trzeba się także liczyć z tym, że jeśli produkty z jednej serii będą się bardzo różnić wielkością pola widzenia kamer, mimo kalibracji, nie będą się odpowiednio zazębiać. Wtedy krawędzie obrazów cząstkowych będą rozmazane, przez co poprawne etykiety zostaną uznane za wybrakowane. Ograniczenia metody złączania obrazów Jakość obrazu wynikowego pogarsza się pod wpływem wibracji, które przenoszą się na kamery na przykład z taśmociągu albo uderzeń w nie, o co na liniach produkcyjnych, na których panuje duży ruch, nietrudno. Ponadto mimo rosnącej mocy obliczeniowej współczesnych procesorów, metoda złączania obrazów częściowych nie jest szybka, co wpływa na całkowity czas inspekcji. Kolejny problem stwarza sytuacja, w której punkt odniesienia, identyfikujący pierwszy obraz, wypada w miejscu, które znajduje się w zasięgu dwóch kamer. Błędna interpretacja kodów kreskowych Podobnie, jeżeli na linii złączania obrazów występuje ważny szczegół etykiety, może on nie zostać rozpoznany. Chociaż zazębianie się pól widzenia kamer stosuje się właśnie po to, aby ten niekorzystny efekt zredukować, nie da się go całkowicie wyeliminować. W rezultacie linie złączania mogą na przykład spowodować, że kod kreskowy będzie nieczytelny albo zostanie zmieniony. W obu przypadkach, pomimo poprawnego oznaczenia, etykieta zostanie uznana za wybrakowaną. Alternatywa Złączanie obrazów można również zrealizować, wykorzystując więcej, niż cztery kamery oraz nie łącząc rejestrowanych przez nie obrazów cząstkowych "na styk", lecz je na siebie nakładać. Ma to wiele zalet, m.in. pola widzenia kamer zazębiają się na dłuższym odcinku. Dzięki temu drobne szczegóły, na przykład fragmenty kodu kreskowego, nie zostaną utracone. Kalibracja systemu wizyjnego jest łatwiejsza, a zmiany rozmiarów produktów z tej samej serii nie mają już takiego znaczenia. Oprócz tego, wbrew pozorom, mimo większej liczby obrazów, ich przetwarzanie w tej metodzie w mniejszym stopniu obciąża procesor. |
INSPEKCJA WIZYJNA ETYKIET
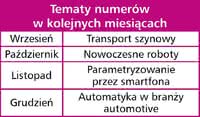
Tematy numerów w kolejnych miesiącach
Przykładowo wizyjna kontrola jakości etykiet opisujących zawartość opakowań o wypukłych ściankach jest znacznie trudniejsza niż nalepek, które naklejono na płaskich powierzchniach. Przede wszystkim obraz, który rejestruje kamera w przypadku nalepki, którą przyklejono na zaokrąglonej powierzchni, jest naturalnie zniekształcony. Oprócz tego w przypadku okrągłych pojemników nigdy nie wiadomo, w oku której kamery znajdzie się naklejka, której poprawność trzeba poddać weryfikacji.
Aby rozwiązać powyższe problemy, systemy wizyjne sprawdzające poprawność rozmieszczenia i treści etykiet tworzy się z wielu kamer, które rejestrują obrazy okrągłych opakowań ze wszystkich stron. Obrazy te następnie się spłaszcza, a potem łączy ze sobą. Technikę tę przybliżamy w ramce.
Monika Jaworowska