Na wstępie warto jest odpowiedzieć na pytanie, czym właściwie jest cyfrowa fabryka (Digital Factory, Smart Factory). Według jednej z obowiązujących definicji jest to zakład, który dzięki wdrożonym w nim rozwiązaniom technologicznym, które na wielu poziomach i w różnym stopniu ze sobą współpracują, stanowi elastyczny system mogący w znaczącym zakresie autonomicznie optymalizować swoje funkcjonowanie i samodzielnie zarządzać procesami produkcyjnymi, dostosowując się w ten sposób do zmieniających się warunków i wymagań. DANE NAPĘDZAJĄ SMART FACTORY Innymi słowy cyfrowa fabryka stanowi wysoce zdigitalizowane i skomunikowane środowisko, w którym maszyny, i inne wyposażenie są w stanie usprawniać procesy poprzez automatyzację i samooptymalizację. Dotyczy to zarówno zadań produkcyjnych, jak i innych dziedzin, takich jak planowanie, logistyka łańcucha dostaw, a nawet rozwój nowych produktów. Jest to możliwe przede wszystkim dzięki temu, że zintegrowane wyposażenie cyfrowych fabryk wymienia się danymi. Można nawet zaryzykować stwierdzenie, że to one są największą siłą napędową inteligentnych zakładów produkcyjnych – bez dostępu do informacji nie ma w ogóle mowy o osiągnięciu stawianych im celów. Dlatego nieodzownym elementem smart fabryk są rozwiązania, które umożliwiają rejestrowanie oraz zbieranie danych o przebiegu produkcji oraz stanie maszyn i wyposażenia. OD IIOT DO AI W tym zakresie wykorzystuje się smart czujniki oraz Przemysłowy Internet Rzeczy (Industrial Internet of Things, IIoT). Same dane oczywiście nie wystarczą. Żeby były użyteczne, powinny jeszcze zostać właściwie zinterpretowane. Informacje, które są generowane w cyfrowych fabrykach, są pod wieloma względami specyficzne. Oprócz ogromnych ilości, w jakich są dostarczane, dużej szybkości napływu, która może także dodatkowo podlegać okresowym wahaniom i dużej oczekiwanej szybkości ich przetwarzania, charakteryzuje je również różnorodność źródeł i formatów. Dlatego, w zależności od stopnia zdigitalizowania procesów produkcyjnych w danym zakładzie, nierzadko można je zaliczyć do kategorii Big Data. W związku z tym ich analiza wymaga specjalnych rozwiązań wykraczających poza tradycyjne metody. Trzeba zatem sięgnąć po takie technologie, jak sztuczna inteligencja (Artificial Intelligence, AI) czy chmura obliczeniowa (Cloud Computing). |
CZYM SĄ SMART SENSORS?
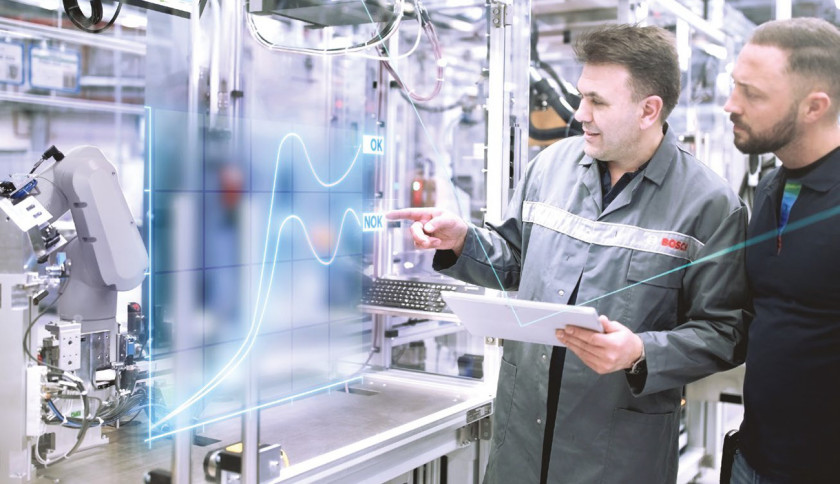
Czujniki od zawsze były nieodłącznymi elementami linii produkcyjnych. "Zwykłe" czujniki w erze Przemysłu 4.0 okazują się jednak nie wystarczać – dlatego w cyfrowych fabrykach upowszechniają się wersje smart. Stanowią one zintegrowane jednostki zawierające element pomiarowy, blok wstępnego przetwarzania wyników pomiarów oraz nadajnik wysyłający odczyty do jednostki nadrzędnej. W inteligentne czujniki wyposażane są nowe urządzenia, które dzięki temu są fabrycznie przygotowane do podłączenia do sieci Internetu Rzeczy. Starsze natomiast są wyposażane w specjalne moduły pomiarowo-komunikacyjne.
Dostępność mocy obliczeniowej do przeprowadzania obliczeń na zmierzonych danych lokalnie, w czujniku oraz możliwość ich zdalnego odczytu dzięki modułowi komunikacyjnemu to niejedyne cechy smart sensorów. Dzięki postępowi w zakresie miniaturyzacji, możliwej przede wszystkim dzięki technologii MEMS, smart czujniki stały się alternatywą dla tradycyjnych sensorów tam, gdzie montaż tych drugich, ze względu na ich rozmiary, byłby niemożliwy. Warto także dodać, że bez postępów w zakresie technologii MEMS koncepcja Internetu Rzeczy, a w tym IIoT, nie byłaby możliwa do zrealizowania ze względu na koszty.
5G w smart fabryce firmy RittalW 2019 roku firma Rittal uruchomiła produkcję w zakładzie przemysłowym w niemieckim Haiger. W fabryce produkowane są nowe serie obudów sterowniczych i małogabarytowych. W zakładzie, którego budowa kosztowała 250 milionów euro, wdrożono szereg rozwiązań z dziedziny Przemysłu 4.0. Park maszynowy w Haiger w znacznym stopniu samodzielnie się konfiguruje, w zależności od wytwarzanych przedmiotów lub podzespołów. Maszyny i systemy transportu komunikują się ze sobą oraz z systemami nadrzędnymi. Transport wewnętrzny, pakowanie, oznakowanie, dalszy transport do dystrybucji są całkowicie zautomatyzowane. ![]() Kolejną nowością w niemieckim zakładzie firmy Rittal ma być prywatna sieć komórkowa 5G, która ma zostać uruchomiona jeszcze w tym roku. Ma ona znacznie przyspieszyć i uprościć przepływ danych oraz być pomocna przy wdrażaniu analiz, które pozwolą przewidzieć i wskazać konieczność wykonania ewentualnych napraw i konserwacji urządzeń produkcyjnych oraz umożliwią optymalizację procesów produkcyjnych. |